EV Battery Metal Extraction and Recovery Processes
End-of-life electric vehicle batteries present a significant materials recovery challenge, with global volumes expected to exceed 2 million metric tons annually by 2030. These packs contain valuable materials including nickel, cobalt, and lithium in complex material matrices, with recovery rates currently averaging below 50% for most elements.
The fundamental challenge lies in developing recycling processes that can efficiently separate and recover multiple valuable elements while managing the varied chemistries and form factors of incoming battery waste streams.
This page brings together solutions from recent research—including selective leaching techniques for high-nickel cathodes, multi-stage separation processes for mixed chemistry batteries, water-based recovery methods, and thermal treatment approaches for lithium extraction. These and other approaches focus on improving recovery rates while reducing processing complexity and environmental impact.
1. Lithium-Ion Battery Material Recycling Process with Selective Precipitation and Chromatographic Separation
FORTUM OYJ, 2025
Recycling lithium-ion battery materials like nickel, cobalt, manganese and lithium from spent batteries in a sustainable way with reduced wastewater generation and lower CO2 footprint compared to existing methods. The process involves selectively precipitating and removing impurities like manganese, fluoride and phosphorous using lithium compounds like persulfate and hydroxide. This allows avoiding additional pH adjustments and reducing waste generation. The purified lithium solution is then further processed using chromatographic separation and concentration steps to recover high-purity lithium chemicals for battery production.
2. Apparatus for Separation and Extraction of Metals from Lithium Battery Cathode Materials Using Sequential Crushing, Magnetic Separation, and Chemical Processes
NATIONAL ENGINEERING RESEARCH CENTER OF ADVANCED ENERGY STORAGE MATERIALS CO LTD, 2025
Recycling lithium battery materials using a specialized apparatus that separates and extracts valuable metals from cathode materials. The process involves crushing, magnetic separation, winnowing, acid leaching, extraction, back-extraction, and saponification steps to recover elements like lithium, nickel, cobalt, manganese, and iron. It allows efficient recycling of metals from lithium batteries while minimizing waste and environmental impact.
3. Addressing Inherent Challenges to Chemical Relithiation of Cycled End‐of‐Life Cathode Materials
cyrus kibichi kirwa, evelyna wang, seoungbum son - Wiley, 2025
Abstract Recycling endoflife (EOL) lithiumion batteries (LIBs) is important to retain valuable resources from critical materials present in EOL battery waste. Direct recycling methods offer an opportunity recover intact cathode with minimal reprocessing. An step of the direct process relithiation which used restore lithium content materials. However, little has been done study how preprocessing steps such as washing or binder removal may affect process. Here, evolution fluorine byproducts left over during a lowtemperature chemical redox mediator tracked. A facile presented solution for mediating adverse effects surface contamination on performance. The structure, content, and electrochemical performance relithiated NMC 622 material that underwent prerelithiation remove shown match pristine 622. In this work, it showed part promising low energy method can be applied inherent impurities if proper processing are implemented.
4. Global Supply of Secondary Lithium from Lithium-Ion Battery Recycling
carolin kresse, britta bookhagen, l andrade - Multidisciplinary Digital Publishing Institute, 2025
The recycling of lithium-ion batteries is picking up rather slowly, although recent rapid growth in consumption and increasing prevalence battery electric vehicles have increased the quantity recoverable material from past years production. Yet, diversity different product types i.e., chemistries life spans complicates recovery raw materials. At present, large-scale industrial employs (1) pyrometallurgy, with downstream hydrometallurgy for refined metals/salts; (2) hydrometallurgy, requiring upstream mechanical shredding cells and/or modules. Regulatory requirements, especially Europe, high industry concentration along value chain drive efforts forward. present study aims to quantify potential contribution 2nd lithium production on a global European scale 2050. overall output any given year depends interactions between several factors, including production, lifetime distributions, rates, all which are uncertain. simplest way propagate input uncertainties final results use Monte Carlo-type simulations. Calculations were done separately EVs portable batteries. supply sum contributions ... Read More
5. Optimized Ammonia Leaching and Energy-Efficient Stripping for Lithium and Cobalt Recovery from Spent LiCoO2 Cathodes
aisulu batkal, kaster kamunur, lyazzat mussapyrova - Multidisciplinary Digital Publishing Institute, 2025
This study investigates the optimization of an ammonia-based leaching process for recovery lithium and cobalt from spent LiCoO2 cathodes, coupled with energy-efficient ammonia stripping approach. Kinetic analysis revealed that both extraction follow pseudo-first-order kinetics, activation energies 76.54 kJ/mol 97.22 kJ/mol, respectively, indicating a chemically controlled process. Optimal conditions were established at 6 M NH3, 1.5 (NH4)2CO3, liquid-to-solid ratio 10:1, 70 C 5 h, achieving 82.5% 96.1% recovery. The was optimized energy efficiency, operations 9598 providing best balance between rapid NH3 removal consumption. At 98 C, demand reduced to ~282 sevenfold improvement over lower temperature operations. A stepwise separation strategy developed, involving selective precipitation pH 10.710.8, followed by precipitate 8.89.0. integrated approach offers promising alternative conventional acid-based recycling methods, combining high metal improved efficiency reagent recyclability.
6. Method for Recycling Lithium Batteries Using Pyrolysis with Integrated Gas-Solid Separation and Metal Extraction
NATIONAL ENGINEERING RESEARCH CENTER OF ADVANCED ENERGY STORAGE MATERIALS CO LTD, 2025
A method for recycling lithium batteries that provides a more efficient, less complex, and less costly process compared to existing methods. The method involves pyrolysis, gas-solid separation, gas combustion, and flue gas treatment to recover valuable metals like lithium, nickel, cobalt, and manganese from the battery components. The pyrolysis step involves heating the batteries to break down the materials. The gas-solid separation separates the pyrolysis products into a gas stream and a solid stream. The gas is combusted and the flue gas treated to meet emissions standards. The solid stream is further processed to extract the metals.
7. Chlorination-Based Process for Metal Extraction from Pyrolyzed Lithium Battery Solids
NATIONAL ENGINEERING RESEARCH CENTER OF ADVANCED ENERGY STORAGE MATERIALS CO LTD, 2025
Recycling lithium battery materials using chlorination. The process involves pyrolyzing the batteries to convert the contents into gases and solids. The gases are burned to generate heat. The solids, including metal sheets, powders, and carbon, are chlorinated at lower temperatures to extract the metals. This chlorination step is done in an oxygen-free environment. The chlorinated gases are then treated to remove pollutants and meet emissions standards. The chlorinated solids can be further processed to separate and recover the metals. The chlorination provides a more efficient and scalable way to extract valuable metals from recycled lithium batteries compared to traditional methods.
8. Closed-Loop Recycling Method for Nickel-Cobalt-Manganese Cathode Materials Using Citric Acid Leaching
CHINA UNIVERSITY OF MINING AND TECHNOLOGY BEIJING, 2025
A closed-loop and environmentally friendly method for recycling and regenerating retired nickel-cobalt-manganese (NCM) lithium-ion battery cathode materials without using strong acids or bases. The method uses citric acid as a leaching agent to extract metals like lithium, nickel, cobalt, and manganese from retired cathodes. It leaches at suitable conditions to achieve high metal recovery. The citric acid precursors are then mixed with lithium hydroxide and calcined to regenerate a new cathode with improved electrochemical performance compared to the original cathode. The citric acid leaching avoids secondary pollution compared to strong acids/bases and allows recycling of the filtrate.
9. Wet Processing System for Metal Extraction from Mixed Lithium Battery Cathode Materials
NATIONAL ENGINEERING RESEARCH CENTER OF ADVANCED ENERGY STORAGE MATERIALS CO LTD, 2025
Recycling lithium battery metals using a wet processing method to extract valuable metals from cathode materials like lithium iron phosphate and ternary compounds without pre-separating the battery types. The process involves pyrolysis to convert the batteries to gases and solids, followed by gas cleaning and solid separation. The solids are treated with water to extract metal ions. This allows efficient separation and recovery of metals like lithium, nickel, manganese, and cobalt from the battery waste.
10. Lithium-Ion Battery Recycling via Pulsed Charging for Metal Precipitation and Electrode Miniaturization
PRIME PLANET ENERGY & SOLUTIONS INC, 2025
Recycling method for lithium-ion batteries that improves efficiency and allows better extraction of valuable metals. The method involves two steps: (1) Li precipitation on the negative electrode by pulsed charging/discharging at low temperature, then (2) breaking down the positive electrode active material by charging/discharging in a low potential range. This miniaturizes the positive electrode material for easier separation and recovery of constituent metals during subsequent processing.
11. Realizing Reusability of Biomass Leachate for Closed‐Loop Recycling of Wasted NCM Cathode
xinghua guan, liang lou, houqiang shi - Wiley, 2025
Abstract The largescale production and EndofLife (EoL) of lithiumion batteries (LIBs) call for recycling with economic environmental efficiency. However, existing hydrometallurgical strategies typically consume huge amounts corrosive leachate without reusability, especially materials multiple types metallic elements. Herein, the successful realization reusability Rosa roxburghii type biomass is reported during wasted LI cathode. key to realizing relies on coprecipitation transition metal elements based coordination chemistry, which different from conventional method where alkali necessary neutralize precipitating It demonstrated that complete leaching NCM cathode at room temperature (25 C) 1 h, an activation energy E a = 70.30 kJ mol 1 . Highly efficient recovery achieved by using anhydrous oxalic acid (OA) (with efficiencies 97.21%, 98.78%, 96.55%, Ni, Co, Mn, respectively) neutralizing leachate, thus enabling reusability. structure electrochemical properties regenerated (RNCM111) are comparable those commercialized samples. This work expected provide general ... Read More
12. Method for Sequential Extraction of Metals from Lithium-Ion Batteries Using Multi-Stage Sorting, Crushing, and Separation Techniques
BLUE WHALE MATERIALS LLC, 2025
A method to extract valuable materials from used lithium-ion batteries in an efficient and environmentally friendly way. The method involves sorting, crushing, discharging, shredding, magnetic separation, and air separation steps to isolate and recover metals like lithium, cobalt, nickel, manganese, and carbon from the batteries. The steps are performed in stages to separate the battery components and extract the valuable metals. It aims to increase the extraction efficiency compared to direct smelting of whole batteries.
13. A Closed-Loop Process for Rapid and Selective Lithium Extraction and Resynthesis from Spent LiFePO4 Batteries
ruijing liu, yuxiao liu, jianjiang li - Multidisciplinary Digital Publishing Institute, 2025
The rapid growth of lithium iron phosphate (LiFePO4, LFP)-based lithium-ion batteries in energy storage raises urgent challenges for resource recovery and environmental protection. In this study, we propose a novel method selective extraction the resynthesis cathodes from spent LFP batteries, aiming to achieve an economically feasible efficient recycling process. process, leaching H2SO4-H2O2 system is employed rapidly selectively extract lithium, achieving efficiency 98.72% within just 10 min. Through exploration precipitation conditions lithium-containing solution, high-purity Li2CO3 successfully obtained. recovered FePO4 are then used resynthesize cathode materials through carbon-thermal reduction method. A preliminary economic analysis reveals that disposal cost approximately USD 2.63 per kilogram, while value regenerated reaches 4.46, highlighting advantages Furthermore, with acid-to-lithium molar ratio only 0.57-just slightly above stoichiometric 0.5-the process requires minimal acid usage, offering clear benefits. Overall, work presents green, efficient, viable strategy showcas... Read More
14. Progress, Challenges and Opportunities in Recycling Electric Vehicle Batteries: A Systematic Review Article
hamid safarzadeh, francesco di maria - Multidisciplinary Digital Publishing Institute, 2025
Objective: The rapid growth of electric vehicle (EV) adoption has led to an unprecedented increase in lithium-ion battery (LIB) demand and end-of-life waste, underscoring the urgent need for effective recycling strategies. This review evaluates current progress EV explores future prospects. Design: Review based on PRISMA 2020. Data sources: Scientific publications indexed major databases such as Scopus, Web Science, ScienceDirect were searched relevant studies published between 2020 15 April 2025. Inclusion criteria: Studies included if they English 2025, focused batteries. Eligible specifically addressed (i) methods, technologies, material recovery processes batteries; (ii) impact recycled systems power generation grid stability; (iii) assessments materials used manufacturing, including efficiency recyclability. articles meta-analyses excluded ensure inclusion only original research data. extraction: independently screened extracted by two researchers analyzed rates, environmental impact, system-level energy contributions. One researcher all A second validated accuracy data then org... Read More
15. Method for Direct Recycling of Lithium-Ion Battery Components via Sequential Heat Treatment, Material Separation, Surface Treatment, Relithiation, and Chemical Purification
LI INDUSTRIES INC, 2025
Direct recycling of lithium-ion battery waste in a scalable and efficient manner to isolate, purify, and regenerate recoverable battery components. The recycling method involves steps like heat treatment to decompose binder, separation to isolate electrode material, surface treatment to remove coatings, relithiation to replenish active material, washing to remove impurities, chemical purification, and flotation to extract metals. It yields commercial-grade cathode and anode materials for reuse.
16. Application of Lithium-ion Battery in New Energy Vehicle
qiuxin liu - EWA Publishing, 2025
With the shortage of fossil energy and global warming, traditional cars are gradually being replaced by new vehicles. The automobile industry has made great progress, in which lithium-ion battery is widely used. paper aims to discuss current status challenges application batteries field By combing analyzing relevant literature, it summarizes basic working principle, performance characteristics applications batteries, discusses detail technical bottlenecks encountered during their use vehicles, including density, charging speed, safety recycling. This proposes solutions these looks forward future development trend batteries. results indicate that although technology a broad prospect still necessary further improve its solve recycling problem order promote sustainable
17. Hybrid Pyrometallurgical-Hydrometallurgical Process for Nickel Recovery with Selective Lithium Leaching and Thermal Treatment
KOREA ZINC CO LTD, KEMCO, 2025
Nickel recovery method from complex raw materials using a hybrid pyrometallurgical-hydrometallurgical process. The method involves selectively leaching and recovering lithium from raw materials containing strong lithium bonds through thermal treatment. Then, roasting converts all the nickel-containing raw materials into a uniform phase. Leaching, neutralization, and purification processes follow to remove impurities. Finally, nickel is hydrogen reduced from the purified solution to recover nickel.
18. Method for Recycling Lithium-Ion Batteries via Aqueous Buffer-Assisted Electrode Delamination
UT-BATTELLE LLC, 2025
A simple, low-cost, and environmentally-friendly method for recycling spent lithium-ion batteries by separating and recovering valuable components like cathode materials, anode materials, and metal foils. The method involves isolating a composite electrode, combining it with an aqueous buffer solution, delaminating the electrode material from the current collector, and recovering each separated component. The aqueous solution allows efficient separation without toxic solvents, avoiding complex multi-step processes. The recovered components can be reused to make new batteries.
19. Pyrolyzed “Black Mass” Feedstocks and Their Synthetic Proxies Relevant to Li-Ion Battery Recycling
a bologna, rebecca c vincent, anna kallistova - American Chemical Society, 2025
Lithium-ion battery (LIB) recycling aims to recover valuable materials present within end-of-life electrochemical cells. Industrial processes produce "black mass" from feedstock which desirable can be recollected. Spent cells first undergo mechanical shredding and sieving, organic components are removed by thermal treatment (pyrolysis) before hydrometallurgical processing is employed the constituent elements. Black mass may contain a range of reaction products, formed at high temperature during pyrolysis, due compositionally complex inhomogeneous nature feedstock. These however, have different elemental compositions, ratios, structures, making efficient recovery difficult. Here, we three distinct, industrially sourced black samples containing Li-(Ni x Mn y Co z )-O2 (x + = 1) positive electrodes varying composition. We employ suite structural compositional characterization techniques, including synchrotron X-ray neutron powder diffraction element specific analysis (X-ray photoelectron spectroscopy, fluorescence energy dispersive inductively coupled plasma optical emission spectroscop... Read More
20. Using Recovered Lithium Iron Phosphate Battery Materials as Efficient Electrocatalysts for the Oxygen Evolution Reaction
arshdeep kaur, hongxia wang, umair gulzar - John Wiley & Sons Australia, Ltd., 2025
ABSTRACT The rapid emergence of lithiumion batteries (LIBs) to satisfy our ever increasing energy demands will result in a significant future waste problem at their end life. Lithium iron phosphate (LFP) as cathode material is now widely used LIBs with market share. It expected that there be volumes battery containing this the near future, and therefore it important develop methods for effectively repurposing LFP mitigate its impact on environment. In work we demonstrate from spent electrocatalysts oxygen evolution reaction (OER) which critical electrochemical water splitting production green hydrogen. Our study has shown recovered once immobilized onto Ni substrate reconstructs into mixed Fe/Ni oxide surface layer highly active OER. Promisingly, were cycled multiple times (up 100 cycles) showed excellent electrocatalytic performance low Tafel slope 58 mV dec 1 , overpotential values 250 310 reach 10 mA cm 2 respectively 24 h stability over 200 . This research provides potential motivation recycling companies isolate Li ion later use electrolysis technologies.
Get Full Report
Access our comprehensive collection of 234 documents related to this technology
Identify Key Areas of Innovation in 2025
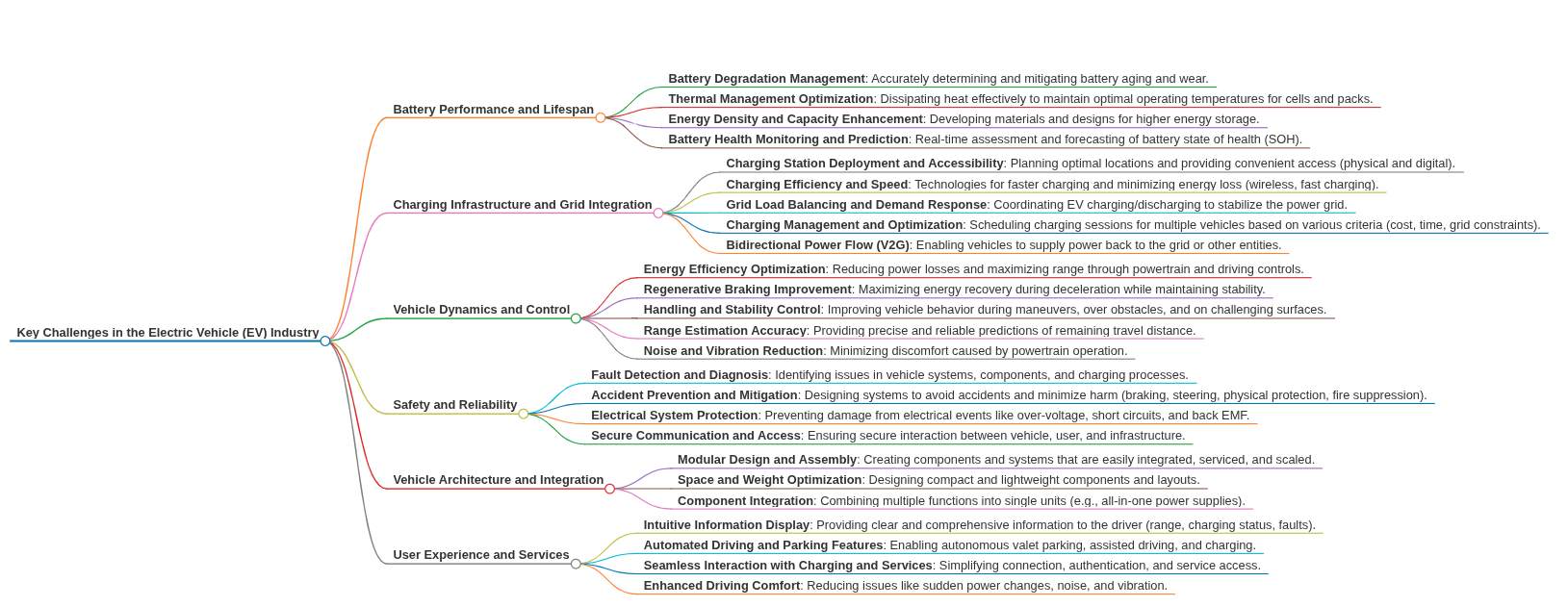