V2G Integration for EV Battery Systems
Vehicle-to-grid (V2G) systems manage bidirectional power flows between electric vehicles and the power grid, with individual vehicles handling energy transfers up to 19.2 kW through Level 2 charging. At scale, even a modest fleet of 1,000 connected vehicles could provide 19 MW of flexible capacity—enough to help stabilize local grid segments during demand peaks or supply shortfalls.
The fundamental challenge lies in coordinating distributed energy flows while simultaneously preserving battery health and meeting individual vehicle owners' mobility needs.
This page brings together solutions from recent research—including adaptive state-of-charge estimation systems, intelligent load balancing algorithms, shared power electronics architectures, and selective battery management strategies. These and other approaches aim to maximize grid services while ensuring reliable vehicle operation and battery longevity.
1. An Optimal Integral Fast Terminal Synergetic Control Scheme for a Grid-to-Vehicle and Vehicle-to-Grid Battery Electric Vehicle Charger Based on the Black-Winged Kite Algorithm
ishak aris, yanis sadou, abdelbaset laib - Multidisciplinary Digital Publishing Institute, 2025
The utilization of electric vehicles (EVs) has grown significantly and continuously in recent years, encouraging the creation new implementation opportunities. battery vehicle (BEV) charging system can be effectively used during peak load periods, for voltage regulation, improvement power stability within smart grid. It provides an efficient bidirectional interface from grid discharging into These two operation modes are referred to as grid-to-vehicle (G2V) vehicle-to-grid (V2G), respectively. management flow both directions is highly complex sensitive, which requires employing a robust control scheme. In this paper, Integral Fast Terminal Synergetic Control Scheme (IFTSC) designed BEV charger through accurately tracking required current G2V V2G modes. Moreover, Black-Winged Kite Algorithm introduced select optimal gains proposed IFTS checked using Lyapunov method. Comprehensive simulations MATLAB/Simulink conducted assess safety efficacy suggested IFTSC comparison with IFTSC, integral synergetic, conventional PID controllers. Furthermore, processor-in-the-loop (PIL) co-simulation ca... Read More
2. Electric Vehicle Charge/Discharge Scheduling Device with Mixed-Integer Programming-Based Model Selection
KIA CORP, 2025
Electric vehicle charge/discharge scheduling method and device for optimizing electric vehicle battery charging and discharging to buildings using vehicle-to-building (V2B) technology. The method involves inputting data like electric vehicle battery info, building power usage, and charging station details. It then sets an appropriate scheduling model using mixed-integer linear programming (MILP) if the number of vehicles is less than stations, or mixed-integer quadratic programming (MIQP) if more vehicles. The scheduling model is optimized using an objective function and output as scheduling data to coordinate vehicle charging and discharging.
3. Battery Charging Method with Vehicle-to-Grid Discharge for Accurate State of Charge Estimation in Lithium Iron Phosphate Batteries
KIA CORP, 2025
Charging method for batteries in electric vehicles that improves accuracy of state of charge (SOC) and state of health (SOH) estimation for lithium iron phosphate (LFP) batteries without disrupting normal driving patterns. The method involves calculating the exact SOC during charging by leveraging vehicle-to-grid (V2G) functionality. When the vehicle is plugged into a charging station, it first discharges to 24% SOC to accurately determine the SOC. It then charges back to full. This allows precise SOC determination without relying solely on open circuit voltage (OCV) in the flat voltage range of LFP batteries.
4. EV Charging and Discharging Scheduling Method with Constraints on Power Flow and Demand Response Compliance
KIA CORP, 2025
Electric vehicle (EV) charging and discharging scheduling method that optimizes EV battery usage to reduce costs and generate profits by considering factors like contract for difference, smart charging, demand response, and national DR markets. The method involves setting a scheduling model with constraints like vehicle charging limits, prevention of reversed power flow, compliance with DR bid power, etc, and optimizing an objective function that balances regular charging/discharging for contract for difference, plus DR, and irregular charging/discharging for national DR.
5. V2G Participation in European Union: Legal and Regulatory Barriers in Spanish Electricity Markets
yusuf ercan ozercan, 2025
The European Union (EU) aims to realize the energy transition by increasing renewable production and enhancing flexibility of system. Vehicle-to-Grid (V2G) technology, which enables electric vehicles (EVs) both draw power from supply back grid, presents a particularly important opportunity contribute this goal. However, technology faces legal regulatory barriers in some EU Member States, including Spain. This article investigates contribution V2G sector coupling examines its potential participation balancing markets, with specific focus on Spanish context. Balancing markets are technically well-suited for participation, but Spain's current legislation significant barriers. While level regulations supporting integration were introduced under Clean Energy All Europeans Package, Spains delayed or incomplete transposition these rules into national law continues prevent entering electricity markets. analyzes key factors behind limitation, market design favoring large-scale centralized absence framework independent aggregators. Nevertheless, it concludes that recent ongoing legislative ... Read More
6. Bidirectional Power Transfer System Utilizing EV Battery for Initial Communication and Backup Power
FORD GLOBAL TECHNOLOGIES LLC, 2025
Bidirectional power transfer system between electric vehicles (EVs) and structures like homes that allows EVs to provide backup power during outages. The system uses the EV's own battery to power initial communications between the EV and an EVSE. This prompts the EV to start transferring power through the EVSE to the structure. The EVSE can then recharge its battery from the EV. This allows the EVSE to still operate during grid outages.
7. Vehicular Microgrid System with Machine Learning-Controlled Battery Aggregation and Discharge
VOLVO CAR CORP, 2025
Intelligent vehicular microgrids to enable vehicles to collectively provide grid support by aggregating and discharging surplus battery capacity at optimal times using machine learning. Vehicles indicate if they want to charge or discharge when docking. A cluster forms of vehicles discharging. When the cluster reaches a threshold, it requests grid access. The microgrid accumulates and discharges surplus in bulk at optimal times.
8. Vehicular Microgrid System with Aggregated Battery Discharge Control Mechanism
VOLVO CAR CORP, 2025
Intelligent vehicular microgrids to enable scaled discharging of electric vehicle batteries to the main grid. The microgrids have charging stations that accumulate excess battery charge from vehicles. A grid component determines when the main grid needs supplemental power and discharges the accumulated battery charge then. This consolidates and timed discharges versus individual vehicle schedules.
9. Networked Power Conversion Units for Electric Vehicle Coordination with Centralized Analytics
MOREL ENERGY LLC, 2025
Optimizing power and energy utilization from multiple electric vehicles at an off-grid site by networking the vehicles' power conversion units and coordinating their power and energy availability. Each conversion unit communicates its available power and energy at intervals to a central analytics process. The analytics determines the optimal utilization of the units and vehicles based on their individual limits to provide continuous power and energy to site loads.
10. Electric Vehicle Charging System with Communicative Pads and Integrated Solar Panel Interface
CHARGE FUSION TECHNOLOGIES LLC, 2025
Intelligent charging system for electric vehicles that enables efficient charging, load balancing, and power generation. It uses charging infrastructure like pads or wireless systems in parking spaces to charge electric vehicles. The charging pads can communicate with the vehicles to customize charging based on preferences and profiles. They can also coordinate charging schedules to balance load on the grid. The pads can also integrate with solar panels on vehicles to generate power when parked and feed it back into the grid. This allows optimized, flexible, and decentralized charging of electric vehicles.
11. ADVANCED ELECTRIC VEHICLE CHARGING TECHNOLOGIES: A COMPREHENSIVE REVIEW OF ACDC SYSTEMS, CONNECTOR STANDARDS, AND SMART GRID INTEGRATION VIA ISO 15118
yusuf ercan ozercan, 2025
The burgeoning adoption of electric vehicles (EVs) globally necessitates a robust and intelligentcharging infrastructure. This article provides comprehensive review current emergingEV charging technologies, focusing on the fundamental distinctions between Alternating Current(AC) Direct Current (DC) charging, diverse landscape global connector standards,and transformative role smart protocols. Particular emphasis is placed ISO15118, an international standard enabling advanced functionalities such as Plug & Charge forseamless user authentication Vehicle-to-Grid (V2G) communication for bidirectional energyflow. technical principles, benefits grid stability renewable energy integration, andpersistent implementation challenges these technologies are rigorously analyzed. reviewconcludes by outlining future trends in wireless artificial intelligence, batterytechnology, alongside critical influence policy investment, underscoring complexinterplay engineering innovation, economic viability, regulatory frameworks, consumerbehavior shaping EV charging.
12. A New Framework of Vehicle-to-Grid Economic Evaluation: From Semi-Systematic Review of 132 Prior Studies
chengquan zhang, hiroshi kitamura, mika goto - Multidisciplinary Digital Publishing Institute, 2025
Vehicle-to-Grid (V2G) technology enables electric vehicles (EVs (Unless otherwise specified, Electric Vehicles (EVs) in this study refer to the totality of BEVs, PHEVs, and other battery-equipped that have potential participate V2G)) interact with renewable energy sources, positioning it as a key driver system decentralization. While V2G holds significant for enhancing grid stability economic efficiency, its large-scale deployment requires robust assessment. However, existing research predominantly focuses on technical feasibility, lacking comprehensive evaluations due complexity architectures. To bridge gap, we propose BSTP (Business-Stakeholders-Technology-Policy) evaluation framework VRR (Value Realization Rate) methodology, employing Semi-Systematic Co-Design Approach. This systematically characterizes evolution business models, interactions among stakeholders, influence technological policy factors, criteria feasibility Furthermore, identify Big Models, No Trials issue research, where theoretical models lack empirical validation. address challenge ensure practical applicab... Read More
13. Detachable Transmission Assembly for Bidirectional Power Conversion in Electric Vehicles
LITE-ON TECHNOLOGY CORP, 2025
A power conversion device for electric vehicles that allows utilizing the vehicle's battery to provide power for home or grid applications when the vehicle is not in use. The device has a detachable transmission assembly that connects to the vehicle's battery pack to receive the battery power. An external power converter then converts the battery power into either DC or AC form. This enables extracting power from the vehicle's battery when it's parked to provide off-grid or backup power. The converter stops when the battery charge gets low.
14. Electric Vehicle Charging System with Shared Power Electronics via Common DC Bus
General Electric Company, 2024
Rapidly charging an electric vehicle's battery using shared power electronics from nearby vehicles. The charging station has a common DC bus that connects to the vehicles. When a vehicle wants a fast charge, it can request the station to provide extra power from other vehicles' converters. The station communicates with their controllers to coordinate sharing the charging current. This allows faster charging than just using the vehicle's converter alone. It reduces component count and weight compared to dedicated chargers, as the shared converters can provide higher currents. The vehicles can also use the station's converters for normal charging when parked.
15. Transformerless Bidirectional Voltage Regulation Circuit with NMOS Transistor Loop and Inductor
ZHUHAI COSMX POWER BATTERY CO., LTD., 2024
Bidirectional voltage regulation circuit for charging and discharging batteries in vehicles without the need for transformers. The circuit uses three NMOS transistors and a control chip to convert voltages bidirectionally between a battery and a power bus. The transistors form a loop with an inductor to boost or buck the voltage as needed for charging or discharging. This allows charging a battery with a lower input voltage to full capacity, and discharging a higher voltage battery to match the bus voltage.
16. Electric Vehicle Charging System with Dynamic Load Management Using Power Controllers and Remote Scheduling
Pismo Labs Technology Limited, 2024
Distributing electricity from a limited supply to multiple electric vehicle chargers based on scheduling and ammeter measurements. The system has power controllers, relays, and ammeters at each charger. A remote server schedules charger usage, authorizes users, and sends instructions to enable/disable relays. The server calculates total current drawn from the power supply. If supply exceeds draw, it disables the main relay. The power controllers independently disable their relays. This allows dynamic charging based on availability and prevents overloading. The server can also send alerts and cancel reservations if time limits are exceeded.
17. Inductive Power Transfer Pads with Non-Uniform Turn Spacing and Core Discontinuities for Enhanced Lateral Misalignment Tolerance
Auckland Uniservices Limited, 2024
Low profile magnetic flux pads for inductive power transfer (IPT) systems that can operate over a wider range of lateral misalignments between the pads. The pads have two closely spaced coils with different turn spacing inside vs outside the coil centers. This non-uniform turn spacing alters the flux patterns to compensate for misalignment and improve power transfer over a wider range. The coils are also wound with variations in turn spacing and core discontinuities to further shape the flux. This allows optimizing the flux profiles for specific applications like electric vehicle charging.
18. Electric Vehicle Charging System with Parallel Supercapacitor Reservoirs and Voltage Conversion
Oxcion Limited, 2024
A system for efficiently delivering electrical energy to charge electric vehicles using a combination of supercapacitors, converters, and reservoirs. The system has multiple input lines to connect to power grids or renewable sources. It uses supercapacitor reservoirs connected in parallel for storing and delivering electrical energy. Converters step-up or step-down the voltage as needed. The reservoirs charge and discharge within limited voltage ranges to extend cell life. The system can also discharge into power grids during peak demand.
19. DC-DC Converter with Immersion and Conduction Cooling for High-Power Density Applications
DIMAAG-AI, Inc., 2024
DC-DC converters for high-power applications like cross-charging electric vehicles that have efficient cooling methods to enable compact size. The converters have features like immersion cooling of the inductor coils, conduction cooling of switching sub-modules, and convection cooling of diode sub-modules. The converter units are arranged with out-of-phase operation. The cooling is optimized with liquid-cooled inductor coils, a module cooling unit with heat exchanger and plate for sub-modules, and immersion-liquid cooled inductors in adjacent converter units. This enables high power density (2 kW/L) and 200 kW+ power levels.
20. Dynamic Charge Control System for Electric Vehicle Fleets with Real-Time Grid and Vehicle Data Integration
UATC, LLC, 2023
Dynamic charge control for electric vehicle fleets that balances energy consumption needs with grid supply/demand balance. The charge control uses real-time vehicle location, state of charge, grid signals, and service demand to determine optimized charging schedules. This helps regulate grid frequency, balance energy consumption, and enables fleet operators to manage charging to minimize grid costs. Charging structures with centralized control can further optimize fleet charging by orchestrating vehicle entry/exit based on state of charge.
Get Full Report
Access our comprehensive collection of 64 documents related to this technology
Identify Key Areas of Innovation in 2025
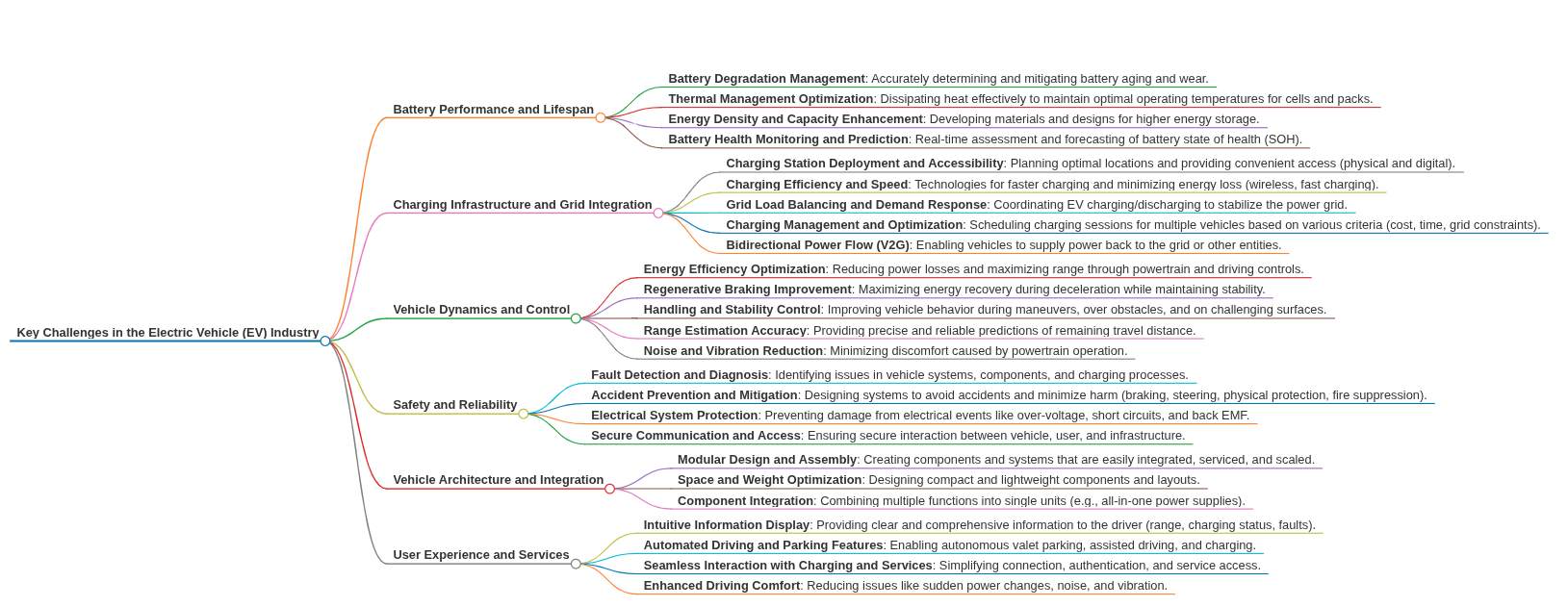