Gas Venting Techniques in EV Battery During Thermal Runaway
When lithium-ion battery cells experience thermal runaway, they can release gases at temperatures exceeding 600°C, with pressure buildups reaching 200 kPa and gas generation rates of up to 3L per ampere-hour of cell capacity. These conditions create cascading risks in battery packs, where a single cell failure can trigger chain reactions through thermal and chemical pathways.
The engineering challenge lies in designing venting systems that can rapidly channel and cool these high-temperature gases while preventing flame propagation between cells—all within the tight spatial constraints of modern battery packs.
This page brings together solutions from recent research—including active cooling airflow systems, thermally-activated pressure relief devices, isolation baffles for gas management, and mist-based fire suppression approaches. These and other approaches focus on preventing cascade failures while maintaining pack integrity during thermal events.
TABLE OF CONTENTS
1. Routine Pressure-Equalization Breathers and Check Valves
The first line of defence in any enclosure is its ability to “breathe” during altitude or temperature swings without ingesting water or dust. A simple yet robust solution is the breathable membrane–flange valve architecture. A hydrophobic membrane covers a through-hole while a slotted cap shields it from stone impacts and under-body splash. Because the mid-body flange separates the sealing zone from the test interface, technicians can pressurise the pack for leak checks without removing the valve. Compared with legacy screw-in vents, the package is smaller, more vibration-tolerant and faster to service.
For applications where both vacuum and over-pressure are expected, the bidirectional spring-loaded relief assembly mounts two independent valve elements on opposite sides of a partition plate. Each element opens only when its own differential is exceeded, while a semipermeable barrier diffuses humidity outward. Engineers can therefore tune opening thresholds simply by swapping springs, maintaining IP ratings in rain or splash environments.
Some packs consolidate daily breathing and emergency blow-off in a single cartridge. The dual-membrane ventilation cap carries a central disk for low-rate, bidirectional equalisation and an outer annulus that tears under major over-pressure. The stiff rim guards both membranes from assembly torque and road debris, letting designers shed weight by deleting a separate burst disk.
Finally, packs that must block post-event back-draft can add an active barrier. The one-way explosion-proof exhaust channel threads into the wall like a standard service plug but contains a piston that snaps shut the instant internal pressure falls. A waterproof film over the external ports protects against spray, yet the check piston prevents oxygen from re-entering after the first vent, sharply reducing the chance of secondary combustion.
2. Early-Detection Sensors and Staged Relief Hardware
Breathers cope with routine pressure swings, but once a cell starts to vent electrolyte, rapid escalation is possible. Designers therefore pair early detection with staged relief. A representative example is the directional dual-mode vent housing, which combines a selective membrane that “breathes” small volumes with a calibrated burst panel that fractures only when a threshold is crossed. The membrane blocks moisture ingress during normal cycling, while the burst path guides the high-energy jet toward a safe outlet.
When pressure rise is gradual at first but can spike two orders of magnitude during full runaway, multi-step devices give tighter control than a single fuse. The functionally staged vent architecture embeds a porous plug, an umbrella valve and a melt-to-open panel directly in the wall. Flow coefficient increases at each step, so small leaks are vented quietly while extreme events still get millisecond-scale discharge capacity. A parallel concept, the stepped explosion-proof valve, stacks three burst membranes in one body; the first two handle equalisation, and the third ruptures only for runaway-level over-pressure.
Consistent cracking pressure depends on fracture control. The two-step fracture-controlled vent notch introduces a deep primary groove overlapped by a shallow secondary groove. By eliminating intersecting stress risers, the disk bursts within a narrow statistical band, so engineers can match vent ratings to known cell vent profiles.
Some cells couple temperature and pressure triggers. In the pressure- and temperature-coupled vent case, a lower-melting insert guarantees a second, larger aperture even if an initial pressure vent drops the internal gauge value. The two-signal approach keeps the cell from re-sealing as decomposition reactions continue.
Collectively, these staged devices bridge the gap between low-rate degassing and full runaway, buying time for higher layers of mitigation to engage.
3. Passive Ducting, Manifolds and Thermal-Conditioning Paths
Once a valve opens, gas must be routed so that it neither heats adjacent modules nor reaches occupants. Increasingly, architects embed low-impedance channels directly into the structural frame. A pack can be partitioned into sealed mini-compartments, each feeding a side-manifold isolation rail. Thin mica dividers abut existing cross-members, turning the rail into a continuous exhaust plenum with minimal mass gain. Because gases are swept laterally rather than across neighbouring modules, array-to-array heat load drops sharply.
Aerospace programs, where every gram matters, often route several housings to one pipe. Each interface carries a differential-burst check valve. The membrane’s interior side has less unsupported area than the exterior, so it ruptures at lower internal pressure yet resists any back-flow from the common duct. A downstream relief valve holds shut until the pipe itself sees a preset threshold. One-way networking therefore satisfies DO-311A one-battery-out rules without duplicating heavy plumbing.
Air-cooled electric vehicles that recirculate cabin air need a different safeguard. The switching wall outlet duct flips orientation when onboard sensors detect runaway: during normal driving, it returns cooled air to the cabin, but on trigger it blocks the return and vents the plume overboard, optionally with a booster fan to overcome line losses. Packs that favour purely passive hardware can repurpose a cross-member as a cross-member passageway with one-way vents. Reed or flap valves stay sealed against splash in normal service, then open under local over-pressure and dump gas into the beam’s hollow core.
When the priority shifts from isolation to moderation, duct geometry itself becomes the tool. In electric aircraft, batteries connect to a vent conduit with internal cooling fins that absorbs heat as the plume travels through the fuselage. Immersion-cooled packs face a different challenge: keeping coolant clean. A submerged vent manifold captures gases directly above each cell and tunnels them out of the fluid bath, preserving dielectric integrity so normal thermal loops stay operational even after a cell vents.
4. Flame Arresting, Particulate Filtering and Gas Scrubbing Inserts
Vent paths that merely route gas can still project a blow-torch if the plume ignites. Flame-quenching hardware therefore sits downstream of the passive manifolds. A space-efficient choice is the quenching chamber with tortuous baffle path. Gas first expands in a chamber, then snakes around oblique plates before reaching the spring-loaded outlet valve. Residence time and momentum change extinguish flame kernels and drop temperature.
Where packaging is tighter, teams swap chambers for porous conductors. The porous metallic temperature-reducing tunnel lines the conduit with sintered mesh that wicks heat and sieves incandescent particles. A non-metal alternative stacks resin plates with staggered perforations, forming the mis-aligned multi-plate diffuser stack. Each layer forces a direction change, throttling momentum without heavy metal meshes; hole diameters can be graded from large to small for balanced relief and cooling.
Chemistry can address hazards that temperature alone cannot. The molecular-sieve gas scrubber fills the vent path with zeolite beads that adsorb hydrocarbons and HF. Where particulate load is high, the dual-stage explosion-proof valve with built-in filter vents in two steps: the first plate relieves the surge; the second maintains flow even if debris starts to clog the passage.
If sustained heat threatens to melt the primary medium, sacrificial layers provide an escape. A rupture disk plus sacrificial porous quencher absorbs energy until it willingly breaks up, avoiding blockage. The thermo-responsive vent closure assembly holds the exit open with low-melting posts that retract a shutter when temperature nears ignition, denying oxygen while other vents upstream stay active.
5. Active or Resettable Vent Actuators
Passive inserts tame most events, but high-energy packs often demand control beyond fracture disks. The closed-loop bidirectional vent folds a pump-and-valve manifold into the housing and hands it to the BMS. Telemetry on pressure, temperature and charge lets the controller evacuate hazardous gas or back-flush inert fluid through the same port, something mechanical vents cannot match.
A simpler layout is the fan-assisted single-port exhaust. One membrane valve sits coaxially with an ECU-driven blower. Pressure-rate sensing decides when both open, lowering the membrane’s crack pressure and protecting thin aluminium walls from sudden impulse loads.
Resettable hardware decreases service cost. The reversible magnetic piston vent replaces expendable disks with a magnet-latched piston. Dual position sensors report stroke; an electromagnet lifts the piston under fault, then reseats it when conditions normalise, keeping the pack in service after benign excursions.
To reach sub-10 kPa actuation levels that springs cannot, designers add stored energy. The pyrotechnic diaphragm puncture carries a low-energy explosive charge that ignites electronically once a programmable limit is exceeded. For chemistries such as LFP that seldom build pressure fast enough to stroke a valve, the pressure-booster driven valve stroke monitors displacement and momentarily drives a compressor to raise case pressure just enough for full lift. In parallel, the OR-logic CO₂ release can bypass the BMS entirely; smoke or temperature sensors fire a solenoid that floods the enclosure with inert gas, forcing ejecta out of a fast-response vent. Trigger fidelity improves further with the thermal-conductivity first-vent sensor, which registers the conductivity drop caused by the very first puff of electrolyte vapour, often hundreds of milliseconds ahead of temperature sensors.
6. Cooling-Integrated Vent Channels and Coolant Release
With routing and flame arrest in place, the next priority is reducing ejecta temperature. One compact answer is the actively cooled vent channel. A single aluminium extrusion forms both a central gas conduit and surrounding liquid passages. When a cell erupts, the circa-700 °C jet impinges on the conduit walls; heat is absorbed by the coolant loop, debris is deflected by flow-splitting ribs and the diluted plume exits a central port.
Where liquid loops are undesirable, residence time does the cooling. The extended guiding channel forces gases to skirt beneath an existing cooling plate, exchanging heat through a long metal detour before discharge. A side-wall cooled pressure-relief valve surrounds its discharge conduit with phase-change media or a secondary refrigerant path so even short vent pulses exit at lower temperature. To avoid pumps entirely, the ambient-air entrainment vent injects outside air through annular jets that shear and dilute the plume.
Some concepts turn the cold plate into an injector. The sacrificial coolant plate thins the wall facing the vent so the first blast ruptures it, dumping liquid directly onto ejecta and into a downstream chamber. A variant embeds a destruction-assisting substance inside a dome aligned with the vent; ignition of this material guarantees plate failure even if jet momentum is modest, ensuring coolant delivery.
7. Structural Enclosure Elements that Deform for Controlled Discharge
Even with cooling, internal pressure can deform housings. Designers therefore weave calibrated weak points into structural members. An extruded guiding-rib sidewall doubles as a reinforcement beam and a vent manifold. Multiple 5 kPa umbrella valves are machined along the perimeter, and internal ribs steer gas from each module bay toward the nearest valve. The approach distributes pressure release, avoiding bulge and violent single-point blowouts.
Another weight-saving layout casts a deep recess into the main housing and seals it with the bottom cover, forming an intermediate plenum. The recessed two-space vent path lets gas expand first in the plenum, equalising pressure before it reaches outer walls, then vents through a port located between structural fasteners. Fastener preload, therefore, remains undisturbed.
Corrosion risk can trump deformation risk. A double-layer vent cover sandwiches an air gap between two steel skins. A tapered projection on the inner plate splits the 700 °C plume; the gap cools gases so the Zn-Ni coating on the outer plate survives salt exposure.
Staged venting can even use internal electronics bays as buffers. In the dual-compartment housing with pressure-gated duct, gases first migrate into an adjacent electronics compartment, which has more volume and no live cells. A second rupture element opens only if that chamber itself exceeds a threshold, delaying external discharge just long enough to protect sensitive components.
8. Cell- and Module-Level Directional Vent Guides and Isolation Barriers
Bulk vent paths work best if the initial jet is pointed the right way. Cylindrical modules employ the paper-based one-way thermal shield. A thin, flame-resistant diaphragm sits between adjacent cans. The first pressure surge flexes it outward, creating a unidirectional valve that directs gas toward the pack wall and blocks reverse flow. Radiant and convective heat transfer to healthy neighbours drops, and crimp-seal melt-through events decline markedly.
Pouch formats need tunable openings to avoid ballooning. The wing-shaped pressure-responsive vent insert embeds a hollow channel through the laminate wall. Internal pressure lifts a seat, vents gas through the “wing” and reseals once normalised, preserving moisture barrier integrity.
Where multiple pouch cells share a compartment, the directional pouch cell cover layers two spaced unit covers to create a separation cavity. Any hot jet is steered laterally into that cavity, where mesh inserts quench sparks before exit. The design deletes discrete module cases, freeing volume for coolant channels.
Cylindrical cells gain a dual-mode safeguard from the temperature-triggered external safety valve. A thermoplastic bond holds the stack to the can. In over-charge, an internal striker disk opens first, cutting current and metering gas. In full thermal runaway, the softened resin lets the entire valve peel away, granting a large vent before the can wrinkles.
9. Pack-Level Containment Volumes and Redundant Exhaust Pathways
Even with cell-level guidance, a runaway can fill the pack with hot, flammable gas. Isolation baffles convert that gas into a manageable flow. The sensor-controlled bidirectional exhaust architecture runs a divider down the pack’s centre, creating two communicating regions. One exhaust assembly inhales ambient air; the other expels internal gases. Cross-flow strips heat and lowers concentration while keeping the enclosure sealed from splash.
Dedicated intermediate chambers add further resilience. In the dual-chamber battery box, the jet passes through a thermal-management plate into a collection chamber, then out a side-wall relief zone. The three-zone containment stack inserts an avoidance chamber for valve actuation freedom, a coolant plate for energy absorption, and a sealed collection chamber for debris capture. Designers can now place relief valves on any cell face without sacrificing density.
At module scale, frangible layers add precision. The separation plate with frangible layer and vent volume sits against the coplanar vent ends of cylindrical cells. A pressurised cell ruptures only its aligned hole; gases expand in a void below the array where mesh or phase-change inserts quench sparks. The flame-retardant rupture plate offers a lighter alternative, while the heat-sink rupture wall with self-sealing medium ejects a sealing compound that plugs the breach once pressure drops.
Electrical interconnects can play a role. Compound-filled busbar apertures trap the first jet in silicone caulk under a pad, preventing molten metal from bridging conductors. If channel capacity is the main constraint, a staggered-cell enlarged vent channel spaces cells to create extra cross-section, lowering internal pressure peaks so the case itself is not forced open.
10. Venting Systems Combined with Fire Suppression and Gas Neutralisation
Suppression agents are most effective once pressure paths and cooling measures are in place. The gas-entrained hybrid water-mist nozzle mounts directly in the pack and mixes inert carrier gas with metered liquid at a Venturi outlet. The gas phase races through narrow cell gaps, displacing oxygen, while micron-scale droplets linger to quench hot surfaces. Where electrical isolation is critical, de-ionised water or treated blends keep conductivity low.
Fresh oxygen entering exhaust pipes can ignite residual vapours, so some designs inert the plume before it exits. The meandering inerting vent pipe with staged gas injection integrates a baffled conduit and suppressant cartridge at the relief port. When the valve lifts, an internal mechanism meters inert gas into the pipe. Staggered baffles promote turbulence and mixing, cooling the flow and allowing downstream capture.
High-nickel cylindrical packs need sub-second response. The sub-second N₂/CO₂ dry-ice jet suppression unit bolts to the vent manifold and uses pre-charged nitrogen to propel dry ice within 0.15 ms of trigger. Ultra-cold, inert gas fills the chamber before the 0.8 s deflagration window closes, stripping heat and starving oxygen.
Large stationary modules employ flood methods. The self-sealing water-injection valve nozzle connects to a rack water line. On detection of runaway, it floods the module; an expandable member swells on contact, automatically closing normal inlets so coolant stays around the cells. Propagation to neighbouring modules is prevented even in dense energy-storage racks.
Get Full Report
Access our comprehensive collection of 268 documents related to this technology
Identify Key Areas of Innovation in 2025
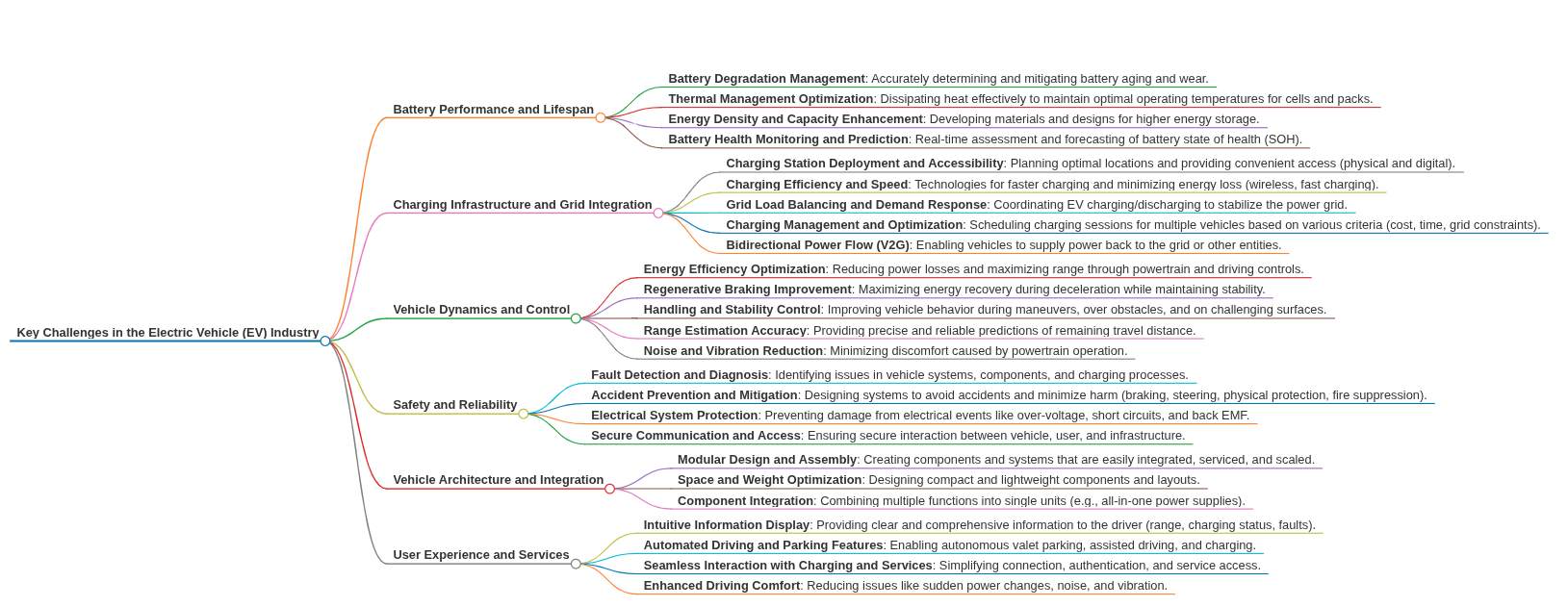