Thermal Management Systems for EV
Electric vehicle battery packs can generate heat loads exceeding 3kW during rapid charging and high-power discharge events, with cell temperatures potentially rising above 45°C. Managing this thermal load while maintaining uniform temperature distribution across thousands of cells presents a significant engineering challenge, particularly as pack sizes and charging rates continue to increase.
The fundamental challenge lies in balancing cooling system effectiveness against the parasitic energy losses, weight penalties, and packaging constraints inherent in thermal management architectures.
This page brings together solutions from recent research—including immersion cooling systems with enhanced heat transfer surfaces, phase change material composites, two-fluid heat exchangers, and predictive thermal management control strategies. These and other approaches focus on maintaining optimal cell temperatures while maximizing system efficiency and minimizing complexity.
1. Novel hybrid vehicle battery cooling system: Integrating Peltier-based heat sinks for control of thermal management
h n sharma, gaurav saxena, ravindra randa - SAGE Publishing, 2025
This study presents an experimental investigation of a novel hybrid battery thermal management system (BTMS) that integrates solenoid-actuated Peltier-based heat sink with CuO/ethylene glycol (EG) nanofluid coolant loop. The delivers on-demand cooling through time-controlled thermoelectric operation, enhancing temperature regulation during surges. Experiments were conducted CuO nanoparticle concentrations ranging from 0.5% to 2.0% (vol.) and flow rates 1 5 LPM, at inlet 50C ambient 26C. Performance metrics such as drop, transfer rate, overall coefficient analyzed. Results showed maximum enhancement 40.63% (tube-side) 38.64% (air-side) CuO. Compared conventional liquid system, the setup demonstrated 7.01% higher rate improved variation control (up 28.53%). Life Cycle Cost (LCC) analysis demonstrates 25%30% reduction in long-term costs 36% life extension, supporting systems economic viability. scalable, energy-efficient BTMS offers promising solution for advanced electric vehicles requiring high-precision control.
2. Characteristic Differences of Thermal Runaway Triggered by Overheating and Overcharging in Lithium-Ion Batteries and Multi-Dimensional Safety Protection Strategies
yao yao, lu liu, juan gu - Multidisciplinary Digital Publishing Institute, 2025
Overheating and overcharging are the core triggering conditions for thermal runaway of lithium-ion batteries. Studying behavioral differences batteries under these two is crucial safety design protection In this study, we investigated temperature, pressure, gas generation, heat generation characteristics lithium conditions. Under overheating conditions, release lattice oxygen in cathode decomposition electrolyte trigger a self-catalytic reaction, generating CO2 (54.7%) H2 (29.7%), with total 17.6 kJ accumulation rate 24.3 W, forming local high-temperature area. voltage drop, capacity attenuation 21.1% (22301762 mAh), internal resistance surge (621 m) reflect severe damage to electrode. Accompanied by oxygenation EC (CO32 + C2H4), production faster. The middle pressure was 0.601 MPa, proportion 67.4%. However, relies on synergistic effect electrochemical reactions ohmic accumulation, resulting relatively low energy accumulation.
3. Configuration study of next-generation BMS based on Wireless Sensor Network
jeongchang kim, hyotaek lee - Scientific Research Archives, 2025
This paper proposes a wireless sensor network (WSN)-based next-generation battery management system (BMS) architecture for large-scale packs in electric vehicles (EVs) and energy storage systems (ESS). Traditional wired BMS offers high reliability but suffers from complex wiring, installation costs, maintenance difficulties. study compares the characteristics of key communication technologies such as Bluetooth Low Energy (BLE), Zigbee, LoRa, Ultra-Wideband (UWB) to optimize design. Moreover, performance cost-effectiveness are compared based on existing literature simulation data analysis. Technical measures improve security environments also proposed. The findings this can serve valuable reference commercialization standardization EV ESS applications.
4. Research on DP-MPC control strategy based on active equalisation system of bidirectional flyback transformer
yingzhe kan, min yang, run qian, 2025
<title>Abstract</title> The inconsistency between power battery cells can seriously restrict the energy utilization efficiency of pack, accelerate aging batteries, and even significantly increase risk thermal runaway. Aiming at this inconsistency, an active equilibrium scheme combining dynamic programming (DP) model predictive control (MPC) is proposed. Firstly, topology circuit bidirectional flyback transformer with rapid equalization speed built, then a system prediction established through MPC to achieve rolling optimization. Finally, using DP solve cost function in conditional scenarios obtain global optimal current time, used predict state changes multiple sampling periods online correction balanced current. algorithm improves overall reduces loss while considering charging discharging equalizer ensure consistent convergence each individual SOC. Simulation experimental results show that strategy quickly effectively correct lithium packs under various conditions, thereby greatly improving balance pack.
5. Optimization of Battery Thermal Management for Real Vehicles via Driving Condition Prediction Using Neural Networks
haozhe zhang, jiashun zhang, tao song - Multidisciplinary Digital Publishing Institute, 2025
In the context of global energy transition, thermal management electric vehicle batteries faces severe challenges due to temperature rise and consumption under dynamic operating conditions. Traditional strategies rely on real-time feedback suffer from response lag efficiency imbalance. this study, we propose a neural network-based synergistic optimization method for driving conditions prediction management, which collects multi-scenario real-vehicle data (358 60-s condition segments) by naturalistic collection method, extracts four typical (congestion, highway, urban, suburbia) combining with K-means clustering, constructs BP (backpropagation network) model (20 neurons in input layer 60 output layer) predict speed next s. Based results, coupled PID control mechanism dynamically adjusts coolant flow rate (maximum reduction 17.6%), reduces maximum battery 3.8 C, difference 0.3 standard deviation fluctuation at ambient temperatures 25~40 C is 0.2 AMESim simulation experimental validation. The results show that strategy significantly improves safety system economy complex working pro... Read More
6. Heat Pump System with Parallel Heating and Cooling Loops for Battery Electric Vehicles
HANON SYSTEMS, 2025
Heat pump system for battery electric vehicles that provides efficient heating and cooling for the cabin and battery. The system uses a heat pump with parallel cooling and heating loops. The main refrigerant loop cools the cabin using an external heat exchanger. Parallel loops draw heat from the battery and drive train. In cooling mode, the battery and drive train loops are bypassed. In heating mode, the battery and drive train loops are active. This allows efficient heating from ambient air, battery, and drive train sources. The parallel loops reduce pressure drop compared to serially connecting all heat sources.
7. Electric Vehicle Battery Thermal Management System with Zoned Independent Flow Control
FORD GLOBAL TECHNOLOGIES LLC, 2025
Thermal management system for electric vehicle batteries that allows individual cooling or heating of different zones within the battery to optimize performance and lifespan. The system uses multiple distinct circuits, each associated with a cooling zone, with independent flow control valves. A controller ranks the zones by temperature and adjusts the valves to balance cooling and heating based on the hottest and coldest zones. This provides customized cooling/heating to prevent hot spots and improve overall battery temperature management.
8. Battery Array with Integrated Roll-Bonded Cold Plates Formed by Bonded Metal Sheets
FORD GLOBAL TECHNOLOGIES LLC, 2025
Battery array design for electric vehicle packs that integrates roll-bonded cold plates into the battery array itself rather than using separate external cold plates. The roll-bonded cold plates are formed by joining two metal sheets along a bonded seam. This allows the cold plates to be integrated into the battery array support structure to directly manage the thermal performance of the battery cells. It reduces cost and complexity compared to separate cold plates. The roll-bonded plates can form one or more sides of the array structure.
9. Stacked Perforated Separator Plates with Interconnected Zigzag Channels for Liquid Immersion Cooling of Battery Packs
GM GLOBAL TECHNOLOGY OPERATIONS LLC, 2025
Liquid immersion cooling (LIC) system for battery packs that uses stacked perforated separator plates between cell rows to distribute coolant fluid vertically upward between the cells. The separator plates have interconnected coolant channels with angled grooves on one plate aligned with opposite angled grooves on the other plate. This zigzag channel pattern creates a pressure differential that forces coolant to flow vertically between the cells. The perforated plates with angled channels stacked between cell rows improve LIC cooling by distributing the coolant fluid over and between the cells.
10. PSA-Optimized Compressor Speed Control Strategy of Electric Vehicle Thermal Management Systems
kun xia, lianglu yu, jingxia wang - Multidisciplinary Digital Publishing Institute, 2025
The thermal management system (TMS) of electric vehicles (EVs) plays a pivotal role in vehicle performance, driving range, battery lifespan, and passenger comfort. Precise control compressor speed, informed by real-time sensor data, is essential for improving TMS efficiency extending EV range. This study proposes strategy based on the PID Search Algorithm (PSA), ensuring optimal an integrated cabin TMS. A co-simulation platform combining AMESim Simulink developed validation, utilizing various sensors to monitor performance. Simulations are conducted under target temperatures 20 C 25 replicate operating conditions. optimized compared with most commonly used controllers, fuzzy strategies. results demonstrate that PSA-Optimized significantly outperforms other three For C, shows minimal temperature overshoot 0.012 COP improvements 0.06, 0.04, 0.03 strategies, respectively. further reduced 0.010 while coefficient performance (COP) increases 0.14, 0.01, 0.07 relative same benchmarks. Overall, indicate effectively utilizes data reduce overshoot, stabilize speed fluctuations, slow decay ... Read More
11. Enhancing E-Bike Efficiency with Intelligent Battery Temperature Control
tiago gandara, adriano figueiredo, jose santos - Multidisciplinary Digital Publishing Institute, 2025
This work presents an innovative approach to battery thermal management for e-bikes by addressing heat generation at its source rather than relying on conventional cooling techniques. Traditional systems rely sinks, fans, phase change materials, or fluids, which increase cost and complexity. In contrast, this study integrates embedded algorithms into the e-bikes motor controller, enabling temperature regulation through performance limitation. Two models are investigated: a reactive algorithm that reduces speed as nears critical threshold, predictive forecasts future evolution adjusts accordingly. Experimental results show successfully limited 26.7% below value but of reductions up 40%. The model, tested in two configurations, demonstrated improved performance, limiting maximum 20% while maintaining stable profiles. These findings confirm can effectively manage temperature, with model being suitable low-complexity applications offering enhanced when more computational resources available.
12. A Thermal Runaway Protection Strategy for Prismatic Lithium-Ion Battery Modules Based on Phase Change and Thermal Decomposition of Sodium Acetate Trihydrate
tianqi yang, hanwei xu, changjun xie - Multidisciplinary Digital Publishing Institute, 2025
With the rapid development of battery energy storage technology, issue thermal runaway (TR) in lithium-ion batteries has become a key challenge restricting their safe application. This study presents an innovative protection strategy that integrates liquid cooling with sodium acetate trihydrate (SAT)-based composite phase change materials (CPCM) to mitigate TR and its propagation prismatic modules. Through numerical simulation, this systematically investigates mechanism optimization pathways for The results indicate pure SAT exhibits poor latent heat performance due low conductivity. In contrast, incorporation expanded graphite (EG) significantly enhances conductivity improves overall performance. Compared traditional paraffin-expanded (PA-EG), SAT-EG, 4.8 times higher than PA-EG, demonstrates more six effectiveness delaying (TRP). When combined cooling, effect is further enhanced, will not be triggered when initial abnormal generation rate relatively low. Even if experiences TR, prevented thickness SAT-EG exceeds 12 mm. Ambient temperature influences both peak timing occurrence modu... Read More
13. Design of Dielectric Fluid Immersion Cooling System for Efficient Thermal Management of Lithium‐Ion Battery Packs
s hemavathi, d a antopaul - Wiley, 2025
ABSTRACT Heat generation during fast charging and discharging of lithiumion batteries (LIBs) remains a significant challenge, potentially leading to overheating, reduced performance, or thermal runaway. Traditional battery management systems (BTMS), such as airbased cooling indirect liquid using cold plates, often result in high gradientsboth vertically within cells horizontally across packsespecially under highcurrent discharge rates. To address these issues, this study introduces evaluates steadystate convectionbased esteroil immersion (EOIC) technique for LIBs. Numerical simulations based on the Newman, Tiedemann, Gu Kim model, aligned with multiscale multidimensional principles, were performed both single 18650 cylindrical cell 4S2P pack. Experimental validations conducted 2C 3C rates at 25C ambient temperature. The EOIC system demonstrated temperature reduction up 13C 15C pack compared natural air convection achieved 10C gradient simulation results closely matched experimental data, maximum deviation only 2C, confirming model's reliabi... Read More
14. Numerical Investigation on Positional Optimisation of Extra Air Channels for Conventional Battery Cooling Models
ferhat koca, recai ozcan - IOP Publishing, 2025
Abstract Currently, as the use of electric vehicles is rapidly increasing, battery pack that powers system one most important issues. Li-ion batteries are preferred type because their high energy density, fast-charging capabilities, and long life. However, heat generated by current drawn affects performance poses safety risks. Effective thermal management systems (BTMSs) required to quickly remove this from packs. For purpose, three different models were created adding extra air inlet channels points on 4 6 module, cooling efficiency was investigated. Numerical analyses performed using Ansys Fluent software package, comparisons made both among themselves with conventional model. The (Basic Model, Model A, B C) analyzed at four Reynolds numbers (104, 2x104, 3x104, 4x104) calculated according velocity duct cross sections. Based these results, Nusselt number (Nu), temperature values, friction factor, pressure drop, PEC (performance criteria) values obtained. Compared Base effective methods determined C, respectively. Adding module resulted in least a 23.86% increase Nu numbers, 40% l... Read More
15. Thermal Performance Enhancement of Lithium‐Ion Batteries Through <scp>PCM</scp>/<scp>CuO</scp> Nanoadditives and Fin Integration: A Numerical Approach
s m d shehabaz, santhosh kumar gugulothu, raju muthyala - Wiley, 2025
ABSTRACT The efficiency and effectiveness of a battery thermal management system (BTMS) primarily depend on the lesser heat capacity phase change material (PCM). To improve performance BTMS, bare batteries with different extended surfaces (straight arc) are considered to enhance dissipation heat, leading significant enhancement performance. In present study, numerical simulations carried out study impact influence CuO (10%) nano additive dispersion in PCM. Also, analyses by modifying geometries arc fins battery. Results reported that proposed improved life 61%90% compared conventional BTMS systems. Extended boost exchange surface area, batterytoPCM/CuO dissipation, form novel method for conduction during liquid fraction melting. This network expands increasing fin radial distance, enhancing At ambient temperature range 15C45C, PCM/CuO/fin substantially PCMbased 163%, 192%, 212%, respectively. These findings demonstrate possibility straight shapes PCM control. experimental results show how these designs optimize transport, improving control under varied operating si... Read More
16. Optimal Charging of Lithium‐Ion Batteries: An Electro‐Thermal Model Approach Using Maximum Possible Optimization
kamala kumari duru, praneash venkatachalam, syed ali hussain - Wiley, 2025
Abstract Electric vehicle (EV) charging has recently become one of the most pressing issues. Given growing demand for lithiumion batteries (LIBs) in electric vehicles, this study analyzes optimization methods improving existing approaches to speed up while reducing temperature rise. This work formulates a doubleobjective function battery based on an electrothermal model. The focused objective is comprised combination two different fitness functions. Optimization current made dynamically following battery's temperature. These experimental findings validate proposed strategy's effectiveness delivering optimal profile. approach demonstrably achieves wellcalibrated balance between competing performance objectives. By adopting suggested strategy, any increase can be maintained within acceptable range. constant voltage (CCCV) method takes total time 1874 s, with shift from 26 45.78 .
17. Battery Pack with Dual-Compartment Housing and Integrated Heat Sink for Thermal Isolation and Dissipation
TECHTRONIC FLOOR CARE TECH LTD, 2025
Battery pack design for electronic devices that prevents overheating and thermal runaway by using a separate heat sink to dissipate heat from the battery pack components. The battery pack has a housing with two compartments, one for the battery cells and another for the circuit board with heat generating components. The heat sink is attached to the compartment without the cells and extends into the cell compartment to contact the heat sources. This isolates the cells from direct contact with the heat sink, preventing overheating and thermal runaway. The heat sink also covers an aperture in the cell compartment to seal it off. Air vents allow airflow between the compartments to cool the heat sink.
18. Battery System with Dual-Fluid Circulation for Thermal Management
DEERE & CO, 2025
Battery system with improved thermal management for electric vehicles. The system circulates two different fluids through the battery cells and surrounding areas to optimize cooling and heating. One fluid circulates through channels at the ends of the cells while the other fluid circulates through the cell holder cavity. This allows separate control of fluid flow for thermal management based on factors like load, temperature, and cell uniformity.
19. Solid-State Battery Module with Integrated Resonant Capacitor and Wireless Power Circuitry on a Single Substrate
MURATA MANUFACTURING CO LTD, 2025
Solid-state battery module for efficient temperature control using resonant wireless charging. The module has the battery, a resonant capacitor, and wireless power circuitry all mounted on one side of a substrate. This allows the capacitor to directly heat the battery using resonant charging. The capacitor is sandwiched between low thermal conductivity components to isolate and concentrate the heat. A thermally conductive path connects the capacitor to the battery. This enables efficient battery heating using wireless charging without needing a separate heating element.
20. Numerical Improvement of Battery Thermal Management Integrating Phase Change Materials with Fin-Enhanced Liquid Cooling
bo wang, c f jiao, zhang shiheng - Multidisciplinary Digital Publishing Institute, 2025
Under high-rate charging and discharging conditions, the coupling of phase change materials (PCMs) with liquid cooling proves to be an effective approach for controlling battery pack operating temperature performance. To address inherent low thermal conductivity PCM enhance heat transfer from plates, numerical simulations were conducted investigate effects installing fins between upper lower plates on distribution. The results demonstrated that merely adding surfaces filling in inter-cell gaps had limited effectiveness reducing maximum temperatures during 4C discharge (8A current), achieving only a 1.8 K reduction peak while increasing difference over 10 K. Cooling incorporating optimized flow channel configurations fins, alternating coolant inlet/outlet arrangements, appropriate increases rate (0.5 m/s), reduced inlet (293.15 K) could maintain below 306 constraining differences approximately 5 discharge. Although increased rates enhanced efficiency, improvements became negligible beyond 0.7 m/s due limitations conductivity. Excessively found adversely affect control initial phases. ... Read More
Get Full Report
Access our comprehensive collection of 307 documents related to this technology
Identify Key Areas of Innovation in 2025
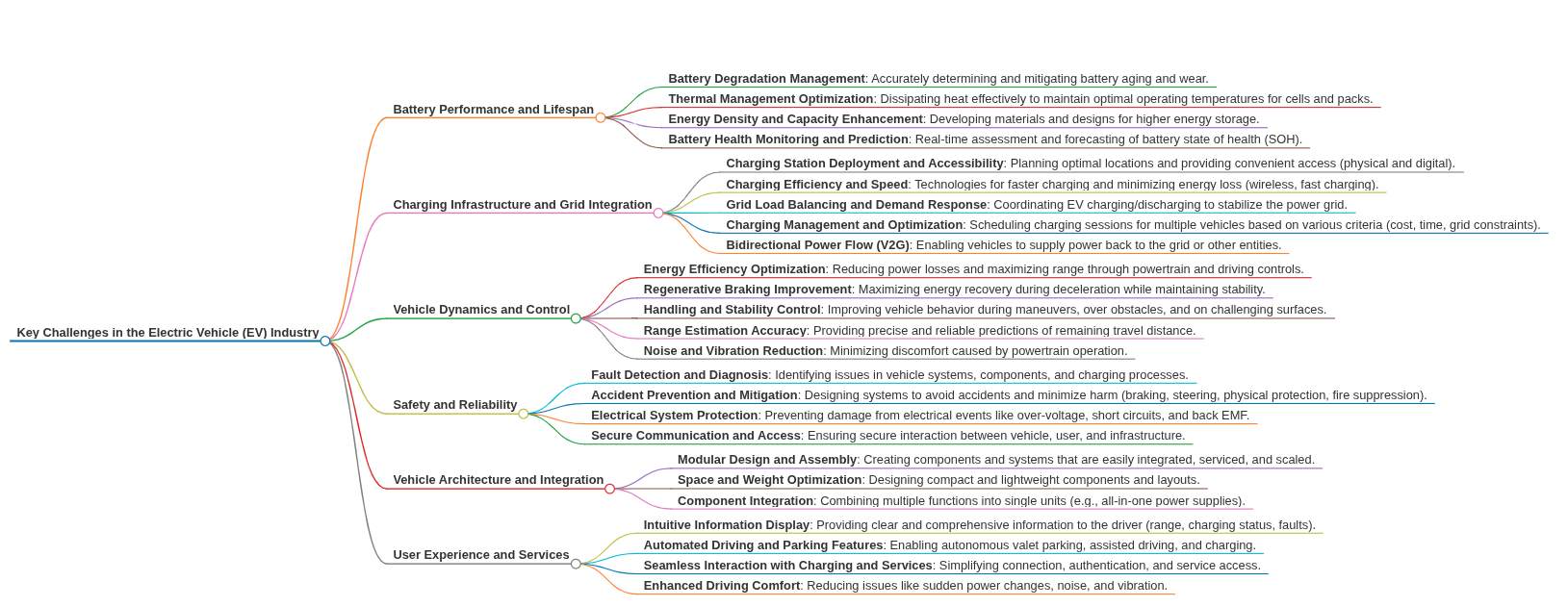