Hybrid Thermal Management Systems for EV Batteries
Electric vehicle battery packs generate substantial heat during operation, with cell temperatures routinely reaching 40-45°C during rapid charging and high-power discharge events. Managing these thermal loads while maintaining temperature uniformity across thousands of cells presents a significant engineering challenge, particularly as pack sizes increase to support longer driving ranges.
The fundamental challenge lies in balancing the competing demands of rapid heat extraction, temperature uniformity, and system complexity in battery thermal management systems.
This page brings together solutions from recent research—including composite phase change materials integrated with liquid cooling, distributed microchannel heat exchangers, and multi-modal thermal management architectures combining passive and active cooling. These and other approaches focus on maintaining optimal cell temperatures while minimizing energy consumption and system complexity.
1. Thermal Energy Storage with Nano-PCM for Optimizing Performance of Solar-Assisted Hybrid Electric Vehicles
t mohankumar, m chiranjivi, 2025
The transition toward sustainable mobility necessitates intelligent thermal energy management strategies, especially in solar-assisted hybrid electric vehicles (HEVs) where fluctuating solar input and dynamic operational loads challenge system efficiency. This chapter presents a comprehensive framework integrating algorithmic intelligence social pedagogy to optimize storage (TES) using nano-enhanced phase change materials (Nano-PCMs). application of advanced computational techniquessuch as genetic algorithms, reinforcement learning, optimization modelsenables precise control real-time adaptation TES performance under variable environmental conditions. synergistic incorporation Nano-PCMs significantly enhances the conductivity density systems, supporting efficient heat absorption release during vehicular operation. integration pedagogical perspectives ensures user-centric design societal alignment, enhancing both functional reliability public acceptance. also explores adaptive regulation strategies based on irradiance variability, predictive modeling for battery temperature cont... Read More
2. Novel hybrid vehicle battery cooling system: Integrating Peltier-based heat sinks for control of thermal management
h n sharma, gaurav saxena, ravindra randa - SAGE Publishing, 2025
This study presents an experimental investigation of a novel hybrid battery thermal management system (BTMS) that integrates solenoid-actuated Peltier-based heat sink with CuO/ethylene glycol (EG) nanofluid coolant loop. The delivers on-demand cooling through time-controlled thermoelectric operation, enhancing temperature regulation during surges. Experiments were conducted CuO nanoparticle concentrations ranging from 0.5% to 2.0% (vol.) and flow rates 1 5 LPM, at inlet 50C ambient 26C. Performance metrics such as drop, transfer rate, overall coefficient analyzed. Results showed maximum enhancement 40.63% (tube-side) 38.64% (air-side) CuO. Compared conventional liquid system, the setup demonstrated 7.01% higher rate improved variation control (up 28.53%). Life Cycle Cost (LCC) analysis demonstrates 25%30% reduction in long-term costs 36% life extension, supporting systems economic viability. scalable, energy-efficient BTMS offers promising solution for advanced electric vehicles requiring high-precision control.
3. Vehicle Refrigerant System with Compressor-Driven Heat Boost via Initial Recirculation and Subsequent Heat Transfer
RIVIAN IP HOLDINGS LLC, 2025
Using a compressor in a vehicle's refrigerant system to provide heat boost for cabin and battery heating without supplemental heaters when ambient temperatures are low. The compressor initially recirculates refrigerant to increase pressure, then switches to circulating refrigerant to transfer heat to cabin and battery systems. This allows heating from compressor work conversion when ambient temperatures are low.
4. Vehicle Heat Pump System with Single Chiller and Selective Valve for Adaptive Coolant Loop Configuration
KIA CORP, HYUNDAI MOTOR CO, 2025
Heat pump system for vehicles that improves efficiency, simplifies design, and enhances battery performance. The system uses a single chiller to adjust battery temperature and recycle waste heat from components. A valve selectively connects cooling circuits for components and interior. This allows optimizing battery cooling while recycling electrical component waste heat to interior. The valve forms multiple coolant loops based on vehicle mode.
5. Battery Module with Integrated Heat Sink Featuring Parallel Refrigerant Flow Paths for Direct Cell Cooling
LG ENERGY SOLUTION LTD, 2025
Battery module with improved cooling performance for applications like electric vehicles. The module has a heat sink integrated into the lower frame to directly cool the battery cells. The heat sink has a flow path for refrigerant. The flow path has longer parallel paths between the cells versus perpendicular paths. This configuration allows direct cooling of the cells with better cooling efficiency compared to indirect cooling through a separate heat sink. The integrated heat sink also improves space utilization compared to a separate heat sink.
6. Thermal Management System with Integrated Glycol and Refrigeration Loops and Configurable Valve Network for Electrified Vehicles
FORD GLOBAL TECHNOLOGIES LLC, 2025
A thermal management system for electrified vehicles that efficiently manages heating and cooling of the battery and cabin using a combination of a glycol system and a refrigeration system. The system has valves to connect and isolate loops for the battery, power electronics, radiator, and cabin heating. By separating components of similar operating temperatures and allowing heat transfer between them, it reduces energy consumption and hardware compared to a single system. The glycol system actively heats the cabin, while the refrigerant system actively chills the battery and power electronics. Valve configurations allow optimization under different vehicle conditions.
7. Multi-Objective Optimization of a Hybrid Battery Thermal Management System Using Response Surface Methodology
k kumar, jahar sarkar, subha mondal - Institute of Physics, 2025
Abstract Multi-objective optimization is vital for a hybrid cylindrical Li-ion battery thermal management system to balance multiple competing goals. However, this has not been explored ternary nanofluid-cooled microchannel-integrated foam-enhanced phase change material packs. Some key design parameters and objectives were also neglected in previous optimizations. Hence, the high-fidelity numerical model developed multi-objective of (coolant inlet temperature, mass flow rate, microchannel spacing metal foam porosity). Response surface methodology employed explore balanced compromise solutions conflicting objectives, including minimization maximum temperature difference, uniformity entropy generation. The results reveal that are most influential factors managing temperature. Higher porosity enhances uniformity. Optimizing crucial reducing irreversibility. Optimized 300.875 K, rate 0.2075 g/s, 6.75 mm, 60% yield 308.95 difference 3.1655 0.4173 K generation 3.98 W/K. findings highlight importance strategically optimizing achieve optimal performance, reduced generation, improved cooling ... Read More
8. Optimization of Battery Thermal Management for Real Vehicles via Driving Condition Prediction Using Neural Networks
haozhe zhang, jiashun zhang, tao song - Multidisciplinary Digital Publishing Institute, 2025
In the context of global energy transition, thermal management electric vehicle batteries faces severe challenges due to temperature rise and consumption under dynamic operating conditions. Traditional strategies rely on real-time feedback suffer from response lag efficiency imbalance. this study, we propose a neural network-based synergistic optimization method for driving conditions prediction management, which collects multi-scenario real-vehicle data (358 60-s condition segments) by naturalistic collection method, extracts four typical (congestion, highway, urban, suburbia) combining with K-means clustering, constructs BP (backpropagation network) model (20 neurons in input layer 60 output layer) predict speed next s. Based results, coupled PID control mechanism dynamically adjusts coolant flow rate (maximum reduction 17.6%), reduces maximum battery 3.8 C, difference 0.3 standard deviation fluctuation at ambient temperatures 25~40 C is 0.2 AMESim simulation experimental validation. The results show that strategy significantly improves safety system economy complex working pro... Read More
9. Integrated Thermal Management System with Independent Component Control and Shared Coolant Loop for Fuel Cell Vehicles
HYUNDAI MOTOR CO, KIA CORP, 2025
Integrated thermal management system for a fuel cell vehicle that improves overall energy efficiency by allowing independent thermal management of components like the fuel cell, battery, electric parts, and indoor air conditioning, and integrating the cooling/heating circuits. It uses a common coolant loop for fuel cell cooling, a separate battery chiller, an air conditioning refrigerant loop, and a shared chiller. This allows optimal cooling/heating for each component while leveraging shared resources.
10. Heat Pump System with Parallel Heating and Cooling Loops for Battery Electric Vehicles
HANON SYSTEMS, 2025
Heat pump system for battery electric vehicles that provides efficient heating and cooling for the cabin and battery. The system uses a heat pump with parallel cooling and heating loops. The main refrigerant loop cools the cabin using an external heat exchanger. Parallel loops draw heat from the battery and drive train. In cooling mode, the battery and drive train loops are bypassed. In heating mode, the battery and drive train loops are active. This allows efficient heating from ambient air, battery, and drive train sources. The parallel loops reduce pressure drop compared to serially connecting all heat sources.
11. PSA-Optimized Compressor Speed Control Strategy of Electric Vehicle Thermal Management Systems
kun xia, lianglu yu, jingxia wang - Multidisciplinary Digital Publishing Institute, 2025
The thermal management system (TMS) of electric vehicles (EVs) plays a pivotal role in vehicle performance, driving range, battery lifespan, and passenger comfort. Precise control compressor speed, informed by real-time sensor data, is essential for improving TMS efficiency extending EV range. This study proposes strategy based on the PID Search Algorithm (PSA), ensuring optimal an integrated cabin TMS. A co-simulation platform combining AMESim Simulink developed validation, utilizing various sensors to monitor performance. Simulations are conducted under target temperatures 20 C 25 replicate operating conditions. optimized compared with most commonly used controllers, fuzzy strategies. results demonstrate that PSA-Optimized significantly outperforms other three For C, shows minimal temperature overshoot 0.012 COP improvements 0.06, 0.04, 0.03 strategies, respectively. further reduced 0.010 while coefficient performance (COP) increases 0.14, 0.01, 0.07 relative same benchmarks. Overall, indicate effectively utilizes data reduce overshoot, stabilize speed fluctuations, slow decay ... Read More
12. Electric Vehicle Thermal Management System with Dual Loops and Thermal Runaway Convergence Mechanism
MICROVAST INC, 2025
Electric vehicle thermal management system that improves safety and efficiency compared to traditional systems. The system has two loops for cooling/heating the battery and driving motor. A release mechanism allows converging the two loops when a battery thermal runaway occurs, with both fluids released into the battery to cool/extinguish it. During normal operation, a heat exchanger transfers heat from the driving motor to the battery loop. This uses motor waste heat to warm the battery instead of external power.
13. Topology Optimization Design of Phase Change Liquid Cooling Composite Plate
xiuwen xia, jiancheng luo, jiabao li - Multidisciplinary Digital Publishing Institute, 2025
To address the challenges of high flow resistance and poor temperature uniformity in conventional PCMliquid cooling hybrid heat exchangerswhich significantly impair performance lifespan electronic devicesa topology optimization approach was adopted. A dual-objective function, aimed at minimizing average pressure drop, introduced to reconstruct channel layout PCM filling region. two-dimensional transient thermo-fluid model coupling solidliquid phase-change process with coolant transfer established, alongside development an experimental platform. comprehensive comparison performed against a liquid plate straight channels. The results showed that topology-optimized exhibited drop 15.80 Pa pumping power 1.19 104 W, representing reductions 38.28% 38.02%, respectively. solidification time shortened by 6 min. Under these conditions, convective coefficient (hw) evaluation criterion (j/f) optimized reached 1319.06 W/(m2K) 0.56, which corresponded increases 60.71% 47.5%, configuration improved overall performance. As inlet velocity increased from 0.05 m/s 0.2 m/s, hw 38.65%... Read More
14. Energy-Efficient Battery Thermal Management in Electric Vehicles Using Artificial-Neural-Network-Based Model Predictive Control
kanghyun nam, changsun ahn - Multidisciplinary Digital Publishing Institute, 2025
This study presents a Model Predictive Control (MPC) strategy for the Battery Thermal Management System (BTMS) in electric vehicles (EVs) to optimize energy efficiency while maintaining battery temperature within optimal range. Due complexity of BTMS dynamics, high-fidelity model was developed using MATLAB/Simscape(2021a), and an artificial neural network (ANN)-based designed achieve high accuracy with reduced computational load. To mitigate oscillatory control inputs observed conventional MPC, infinity-horizon MPC framework introduced, incorporating value function that accounts system behavior beyond prediction horizon. The proposed controller evaluated simulation environment against rule-based under varying ambient temperatures. Results demonstrated significant savings, including 78.9% reduction low-temperature conditions, 36% moderate temperatures, 27.8% high-temperature environments. Additionally, effectively stabilized actuator operation, improving longevity. These findings highlight potential ANN-assisted enhancing performance minimizing consumption EVs.
15. Solid-State Battery Module with Integrated Resonant Capacitor and Wireless Power Circuitry on a Single Substrate for Direct Thermal Management
MURATA MANUFACTURING CO LTD, 2025
Solid-state battery module for efficient temperature control using resonant wireless charging. The module has the battery, a resonant capacitor, and wireless power circuitry all mounted on one side of a substrate. This allows the capacitor to directly heat the battery using resonant charging. The capacitor is sandwiched between low thermal conductivity components to isolate and concentrate the heat. A thermally conductive path connects the capacitor to the battery. This enables efficient battery heating using wireless charging without needing a separate heating element.
16. Battery System with Dual Fluid Circuits and Adjustable Flow Valves for Thermal Management
DEERE & CO, 2025
Battery system with improved thermal management to increase efficiency, cell life, and uniformity. The system has a cell holder with a fluid circuit through the cell stack obstructed by the cells. An unobstructed fluid circuit runs alongside the stack. Valves allow controlling fluid flow to the cell stack vs. side channel. This allows separate cooling/heating of the stack vs. side channel. For example, a non-dielectric fluid can circulate around the cells during low load, while a dielectric fluid circulates inside the stack during high load. This provides flexibility in fluid selection and flow distribution for optimal thermal management.
17. Electric Motor with Enclosed Cavity and Integrated Heat-Transfer Fluid Circuit
NOVARES FRANCE, 2025
An electric motor with integrated cooling using a heat-transfer fluid to extract heat from the motor and transfer it to a heat engine or battery pack. The motor has an enclosed cavity with bearings and a bell-shaped lid covering the rear bearing. The lid has an internal chamber around the motor cavity with fluid inlet/outlet for circulating the heat-transfer fluid. This allows direct cooling of the motor without external connections. The fluid circuit connects the motor, heat engine, and batteries for efficient heat management.
18. Integrated thermal and battery management for electric vehicles: Experimental validation and simulation-based optimization of lithium-ion batteries
pujari harish kumar, gks prakash raju, mohit bajaj - SAGE Publishing, 2025
Electric vehicles (EVs) are pivotal in reducing greenhouse gas emissions and achieving sustainable transportation goals. However, lithium-ion batteries (LIBs), the primary energy source for EVs, face critical thermal management, safety, long-term efficiency challenges. This study proposes an integrated battery management system that combines a waterethylene glycol-based liquid cooling mechanism with high-conductivity copper tubing to enhance LIB performance, longevity, safety. Through COMSOL multiphysics simulations, this examines behavior under varying operational conditions. The results indicate 20% reduction temperature peaks, maintaining optimal range of 15C 35C, thus mitigating risks runaway. Experimental validation using infrared thermography imaging confirms system's efficiency, showing maximum recorded 43.48C load conditions, significantly lower than unmanaged systems. Beyond work integrates advanced strategies, including state-of-charge estimation, predictive fault diagnostics, active optimization, cell balancing. analysis further reveals proposed improves heat diss... Read More
19. Establishment of Reduced Order Models for Temperature Prediction in Electric Vehicle Charging Gun
feifei lu, bingyun jiang, shu huang - ASM International, 2025
Abstract With the rapid development of liquid cooled charging technology, thermal management gun electric vehicle has also become an urgent challenge to be solved. In this paper, accurate simulation model is developed by correcting conductivity and heat generation through integration experimental results. Subsequently, experiment designed with current, coolant inlet flow, temperature, ambient temperature as variables, from which a series results are obtained. Utilizing these training set, reduced order for predicting established. The influence multi-layer perceptron model, response surface gaussian process on prediction accuracy then compared. indicate that compared other two models, more significant advantage in fitting nonlinear average error 1.61 C. This study holds importance intelligent devices.
20. Thermal Management in Electronics and Battery Systems in Vehicles
ms dhyaneshwar s phapale, prof b m randhavan, prof p b dengale - Shivkrupa Publication's, 2025
The rapid evolution of electronic systems and battery technologies in vehicles necessitates advanced thermal management strategies to ensure optimal performance safety. This paper presents a comprehensive review (TMS), comparing conventional methods such as air liquid cooling with emerging techniques like phase change materials (PCMs), heat pipes, systems. While traditional offer simplicity cost- effectiveness, they often struggle limited dissipation capacity inefficiencies under high loads. In contrast, modern TMS provide enhanced regulation, faster absorption, better adaptability varying conditions. study identifies key limitations, including implementation costs system complexity, while highlighting the scope for integrating nonmaterial's smart technologies. Methodologies, tools, simulation used development are outlined. Expected outcomes include improved lifespan, energy efficiency, vehicle concludes by emphasizing critical role innovative advancing automotive technology..
Get Full Report
Access our comprehensive collection of 183 documents related to this technology
Identify Key Areas of Innovation in 2025
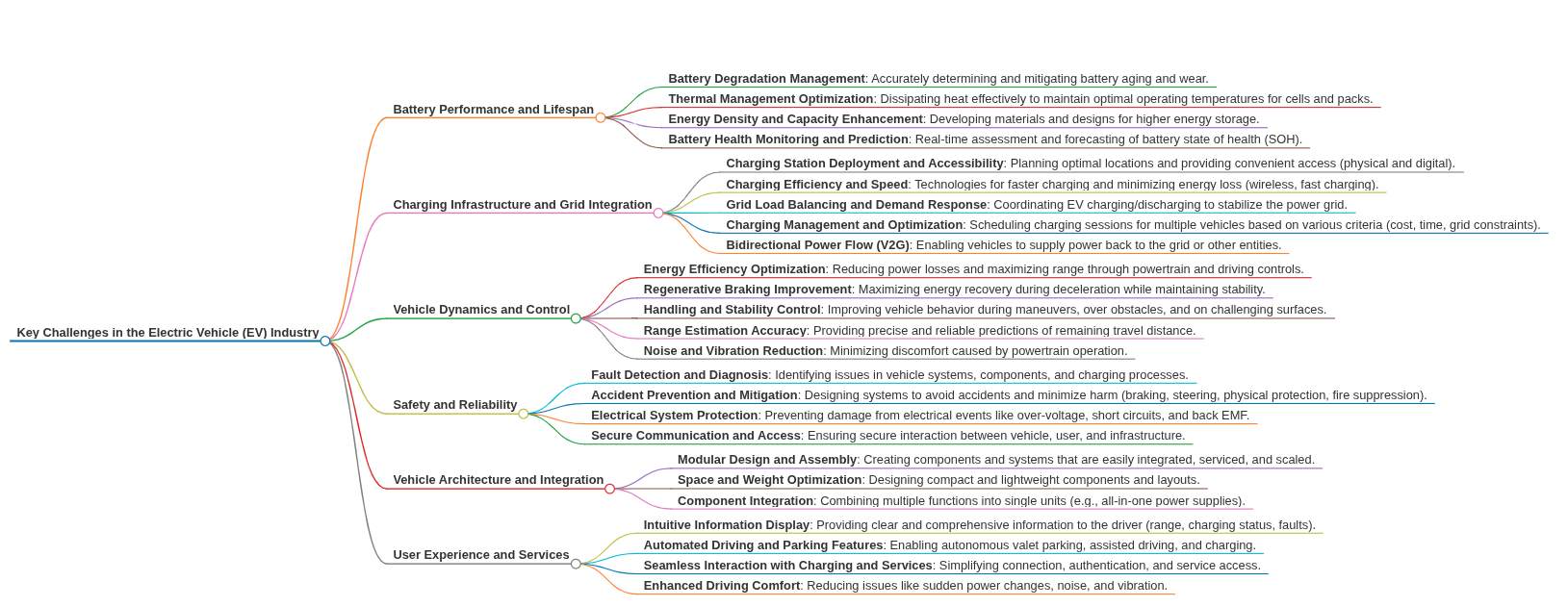