Mitigating Voltage Drop in EVs Under High-Current Discharge
Voltage drop during high-current discharge events remains a persistent challenge in modern battery systems. In extreme discharge scenarios, voltage sag can reach 0.3-0.5V per cell, with pack-level drops exceeding 15% of nominal voltage at current draws above 10C. These transient voltage depressions coincide precisely with peak power demand, creating a fundamental performance limitation in applications from electric vehicles to grid stabilization systems.
The central engineering challenge involves maintaining stable voltage delivery under high discharge rates while preserving battery lifespan, thermal stability, and practical energy density.
This page brings together solutions from recent research—including dual-battery architectures with distinct cell types, interleaved DC-DC converters with PI controllers, bidirectional switch capacitor buck-boost converters, and dynamic voltage configuration adjustment systems. These and other approaches offer practical implementations that balance the competing demands of voltage stability, thermal management, and system complexity.
1. Intermediate Circuit Device with Dynamic Voltage and Phase Configuration Adjustment for Electric Vehicles
VITESCO TECHNOLOGIES GMBH, 2022
Intermediate circuit adaptation device for electric vehicles that dynamically adjusts voltage and phase configuration to optimize system efficiency. The device monitors operating conditions and adjusts voltage and phase parameters in real-time to maximize efficiency while maintaining performance. The adaptation is based on the current operating point, including power, dynamic performance, peak current, minimum voltage, cooling power, and heating power. The device continuously monitors and adapts to optimize electrical system performance while reducing energy losses.
2. Interleaved DC-DC Converter with Dual PI Controller for Parallel Buck and Boost Mode Transition
YOUNG HWA TECH CO LTD, 2022
Interleaved DC-DC converter for electric vehicles that enables efficient power conversion during both low and high-power operating conditions. The converter uses a dual PI controller to manage soft start transitions across multiple channels, with interleaved buck and boost converters controlled in parallel. The controller dynamically switches between buck and boost modes based on load conditions and temperature, maintaining optimal power conversion efficiency and preventing reverse current during soft starts.
3. Bidirectional Switch Capacitor Buck-Boost Converter with Dual-Mode Operation and Low Switching Losses
BOARD OF TRUSTEES OF MICHIGAN STATE UNIVERSITY, 2022
Bidirectional switch capacitor buck-boost voltage converter for electric vehicles, particularly for hybrid and plug-in hybrid electric vehicles, that enables efficient high-power charging while maintaining high efficiency. The converter employs a switch capacitor circuit that can operate in both discharging and charging modes, with the capacitor storing charge during charging and discharging during discharging. The circuit is designed to handle high charging currents while maintaining low switching losses, with the capacitor serving as a buffer between the charging and discharging states.
4. DC-DC Converter with Load-Dependent Voltage and Phase Adjustment for Electric Vehicles
VITESCO TECH GMBH, 2021
Adaptive DC-DC converter for electric vehicles that dynamically adjusts voltage and phase count based on load conditions. The converter employs a control unit that continuously monitors operating point parameters like power, dynamic performance, and temperature to determine optimal voltage and phase configurations. This enables real-time optimization of the DC-DC converter's operating point while maintaining efficiency and performance.
5. DC/DC Converter System with Real-Time Voltage and Phase Configuration Adjustment
VITESCO TECHNOLOGIES GMBH, 2021
Matching DC/DC converters in electric vehicles to optimize efficiency and performance. The system adjusts the converter's voltage and phase configuration based on real-time operating conditions, enabling precise control of the DC/DC converter's output voltage and number of phases. This enables the converter to operate within its optimal operating range while maintaining maximum efficiency and performance.
6. Electric Motor Control System with Dynamic Current Ramp Adjustment for Torque Management
TRW LTD, 2021
Controlling electric motors in vehicles to optimize torque delivery while maintaining current limits. The control system adjusts the motor's current increase rate to prevent excessive current peaks during torque increases, ensuring safe operation of the battery and preventing battery drain. The system implements a ramped increase strategy that maintains current gradients below the battery's voltage limit, even at high torque demands, by dynamically adjusting the motor's current requirements based on the battery's state of charge.
7. Variable Voltage Converter with Dual Duty Cycle Switching for Electric Vehicles
FORD GLOBAL TECHNOLOGIES LLC, 2020
Variable voltage converter for electric vehicles that optimizes system performance by controlling voltage output across its operating range. The converter employs a boost mode operation mode where the converter switches operate between a low duty cycle (0-0.5) and a high duty cycle (0-1.5) to achieve optimal output voltage across the entire operating range. This allows the converter to maintain precise control over the DC bus voltage while operating in both boost and normal modes.
8. Interleaved DC-DC Converter with Series-Connected Parallel Phase Legs and Selective Node Switching
FORD GLOBAL TECH LLC, 2019
Interleaved DC-DC converter for electric vehicles that achieves improved voltage gain through reduced current ripple and increased current capability over a wide operating range. The converter employs a configuration where two parallel phase legs with upper and lower switching devices are connected in series between a positive node and a negative node, each having an intermediate junction coupled to a battery by a respective inductance. The converter operates by selectively connecting the positive node to either the positive bus or a capacitor junction, and the negative node to the capacitor junction or the negative bus. This configuration enables the converter to provide both voltage gain and current capability across a broader voltage range compared to conventional interleaved converters.
9. Variable Voltage Control Inverter with Dynamic Duty Cycle Adjustment for Electric Vehicles
FORD GLOBAL TECH LLC, 2019
Operating a variable voltage control inverter in electric vehicles to optimize motor torque and regeneration performance. The control inverter dynamically adjusts its duty cycle based on battery voltage, enabling precise control of the inverter's output voltage. This allows the inverter to maintain optimal operating conditions for the electric motor while also providing efficient regeneration capabilities.
10. Battery Management System with Task Scheduling and Component Power State Adjustment to Mitigate Power Spikes
MICROSOFT TECHNOLOGY LICENSING LLC, 2019
Techniques to prevent battery shutdowns due to power spikes by intelligently scheduling tasks and altering component power states. The technique involves monitoring battery power availability and estimating component power usage to determine potential power spikes. By scheduling tasks and changing component power states at the spike times, it prevents voltage drops below shutdown thresholds, allowing more battery capacity to be extracted. This prevents premature device shutdowns and extends runtimes by avoiding unnecessary battery drain from spikes.
11. Variable Voltage Converter with Switch-Based Power Management and High-Voltage Capacitor Integration
FORD GLOBAL TECHNOLOGIES LLC, 2018
Variable voltage converter control for electric vehicles that enables precise control of electric machine power across different operating conditions. The converter integrates a high-voltage capacitor and a variable voltage converter with switch-based power management, allowing for dynamic adjustment of the converter's output voltage to optimize torque and efficiency across the vehicle's electric machine set.
12. DC-DC Converter with Adaptive Voltage Step Selection Based on Torque-Dependent Historical Data
FORD GLOBAL TECHNOLOGIES LLC, 2018
Controlling a DC-DC converter in electric vehicles to optimize performance and efficiency during high-power torque conditions. The converter adjusts its output voltage step values in response to the vehicle's torque requirement, dynamically selecting from a predefined set of discrete voltage levels. This adaptive approach enables the converter to maintain optimal power delivery while minimizing switching losses and NVH. The converter's voltage step selection is based on historical operating data, allowing it to adapt to changing torque conditions.
13. Electric Drive System with Dual-Mode Inverter for Dynamic Voltage Control in Electric Vehicles
BOSCH GMBH ROBERT, 2017
Electric drive system for electric vehicles that enables dynamic voltage control of the electric motor. The system employs a single inverter that can switch between two operating modes: one for low-power applications and another for high-power applications. The inverter can be configured to operate at both 400V and 600V voltages, with the 600V mode providing higher power output. This allows the system to dynamically adjust voltage levels based on the vehicle's operating conditions, enabling efficient operation across a broad power spectrum.
14. Power Module Assemblies with Reduced Stray Inductance for Enhanced Inverter Switching Performance
FORD GLOBAL TECH LLC, 2016
Power module assemblies for automotive vehicles that minimize voltage spikes and switching losses during inverter operation. The assemblies incorporate design features to reduce stray inductance effects, particularly in the power inverter region. This enables improved performance of semiconductor devices during switching events, particularly in high-power applications like power modules. The design achieves this through optimized power module architecture and component selection.
15. Hybrid and Electric Vehicle Propulsion System with Real-Time DC Bus Voltage Control via Speed-Dependent Adjustment
GEN ELECTRIC, 2016
Optimizing hybrid and electric vehicle propulsion systems through real-time voltage control of the DC bus. The system employs a controller that continuously monitors the speed of an electromechanical device and compares it to its scheduled speed. When the actual speed exceeds the scheduled speed, the controller dynamically adjusts the DC bus voltage to maintain optimal power transfer while preventing excessive voltage fluctuations. This enables precise voltage regulation across the system, particularly during transient conditions like acceleration or deceleration. The controller integrates with nonlinear models to predict system behavior and ensures optimal energy storage unit performance while maintaining fuel efficiency and vehicle performance.
16. Battery Apparatus with Parallel-Connected Modules Exhibiting Distinct Voltage and Discharge Characteristics
SONY CORP, 2015
Battery apparatus for electric vehicles and devices that utilizes battery modules with different voltage and discharge characteristics to optimize performance. The battery modules are connected in parallel with distinct voltage profiles and discharge ranges, enabling the battery apparatus to achieve higher maximum voltage and longer discharge capabilities compared to conventional single-module configurations. This configuration allows the battery apparatus to maintain optimal performance across a broader operating range, particularly in applications where high voltage and long discharge are required.
17. Secondary Battery with Series-Connected Positive Electrode Assemblies and Controlled Voltage Distribution
SAMSUNG SDI CO LTD, 2015
Secondary battery with improved self-discharge and lifetime characteristics through controlled voltage distribution between positive electrodes. The battery comprises a first positive electrode assembly with a first positive electrode active material, and a second positive electrode assembly with a second positive electrode active material, connected in series. The voltage difference between the two positive electrode assemblies is controlled to maintain a discharge capacity ratio of 25% to 80% across the entire battery. This enables optimized performance across different charging and discharging conditions while maintaining battery health.
Get Full Report
Access our comprehensive collection of 17 documents related to this technology
Identify Key Areas of Innovation in 2025
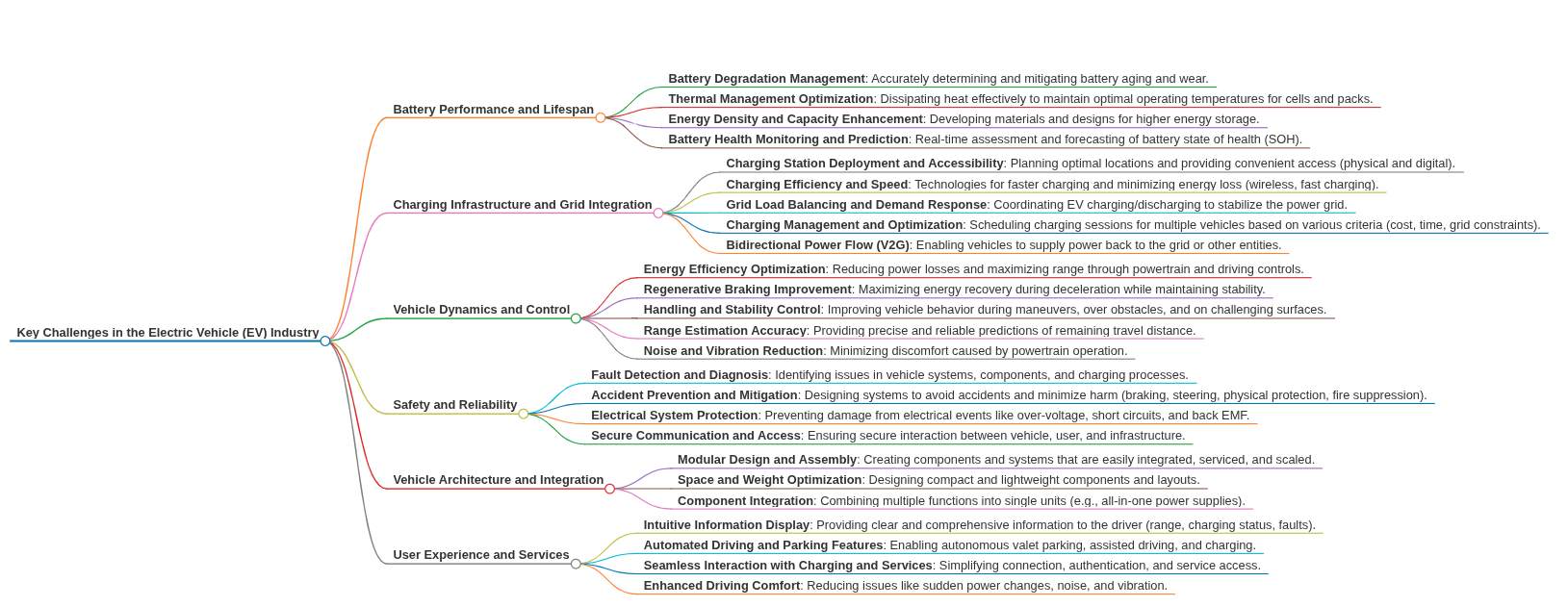