Techniques for EV Battery Crash Safety
In electric vehicle crashes, battery packs face complex mechanical and thermal risks. Impact forces can reach 50g during collisions, while cell punctures or deformation can trigger thermal events exceeding 800°C. Current data shows that protecting these high-voltage systems requires managing both immediate structural damage and potential cascading failures.
The fundamental challenge lies in designing protection systems that can absorb extreme impact forces while maintaining thermal stability and electrical isolation—all without compromising the vehicle's weight and range targets.
This page brings together solutions from recent research—including smart disconnection systems, reinforced chassis designs, gas venting mechanisms, and strategic component placement. These and other approaches demonstrate how manufacturers are evolving battery protection strategies to meet increasingly stringent safety standards while maintaining practical vehicle designs.
TABLE OF CONTENTS
1. Vehicle-Level Crash Structures and Load-Path Architectures
A robust perimeter around the traction battery begins at the body-in-white. Front-end crash analysis on dedicated electric platforms shows that the pack is often contacted not by the external barrier but by the vehicle’s own sub-frame as it drives rearwards. To redirect that internal threat, the continuous side-sill/rear-member/lower-bar cage establishes an uninterrupted ring that links both longitudinal sills to the front side members, extends rear lower members, and stitches them together with a transverse lower bar. Impact loads are steered around the pack rather than through it, so the body can shed massive sill stiffeners and still arrest lateral intrusion and frontal push-back. Lighter structure, preserved cabin width, and a lower probability of cell breach all flow from the same geometric move.
Rear impacts introduce a second failure mode: the heavy pack can shear its own screw fasteners and translate forward. The three-dimensional form-fit interface counters that risk with matching projections and recesses moulded into the chassis beam and the battery flange. Once the flanges nest, inertia is converted into the vehicle’s longitudinal load paths instead of into bolt shear. Because several projection-recess pairs share the work, engineers can trim fastener count and packaging depth while guaranteeing positional integrity of the high-voltage assembly.
Side-impact energy must be managed inside a narrow deformation corridor between sill and pack. The modular three-stage crash cross member splits the lateral beam into a stiff core placed inside the battery housing and two sacrificial elements mounted outboard. When struck, the outer element crushes first, the housing-integrated section second, and the opposite side last. Sequential absorption avoids driving peak loads into cell walls. Because the sacrificial pieces bolt on separately, collision repair can proceed without lowering the pack.
Holistic rear architectures complete the loop. A dual-function impact reducer/air duct sandwiches the battery between longitudinal frames while channelling cooling air through internal passages, so thermal performance is maintained even as rear-end loads are blunted. Complementing that idea, interlocking inner and outer crash bodies ensure that the outer shell cannot diverge or twist away from the inner frame; the inner body “catches” the outer one during deformation and keeps impact vectors aligned with well-defined paths.
These vehicle-level measures act in the first 10–20 ms of a collision. They buy time, but they do not yet isolate voltage or prevent downstream heat propagation. The next layer of defence therefore focuses on electrical separation that happens even faster.
2. Millisecond-Scale Electrical Isolation and Controlled De-Energization
High-voltage isolation must occur before damaged conductors can arc. Instead of relying on a single service disconnect, the distributed smart connection sheet replaces selected bus bars with film-sized conductors that each contain a weakened foil trace and a mini gas-generator punch. When the battery-management system detects a crash, over-charge, or thermal anomaly, multiple sheets are severed simultaneously. The pack is sliced into numerous sub-60 V segments, and because the sheet is no thicker than the original bar, no extra enclosure volume is consumed.
Where pyrotechnics are undesirable, purely mechanical release is available. Passively self-retracting dovetail contacts bias adjacent module terminals apart with internal springs. Under normal assembly the contacts snap together along a transverse axis. Crash-induced shear unlocks the dovetail so both limbs retract, opening the circuit without sensors, wires, or explosives. Elastomer seals keep moisture out and copper coatings prevent welding, turning the connector itself into a fail-safe fuse.
For still finer granularity, the cell-level disconnectable battery architecture embeds a solid-state switch and mini sensor on every cell branch. A central controller can open all switches in less than a millisecond after an abnormal pressure, temperature, or strain reading is registered. The concept scales when paired with the predictive pre-crash power isolation algorithm that classifies the imminent collision in real time and triggers isolation even before metal parts deform.
Isolation removes the series path but stored energy remains. The series-to-parallel reconfiguration with fast discharge flips contactors so every cell string becomes a parallel group, then either dumps energy through a resistor or shuttles it into an auxiliary pack. A refrigeration loop running in parallel prevents the discharge heat from reigniting damaged cells.
With voltage now segmented and discharge underway, the mechanical envelope can be asked to do more of the crash work. The narrative therefore moves from the electrical domain back to the battery enclosure itself.
3. Energy-Absorbing Battery Housings, Trays, and Underbody Shields
Traditional lightweight trays use thin peripheral beams that can collapse when squeezed. The load-bearing vapor-chamber tray lid transforms the simple cover into a two-phase heat spreader whose reinforced edges interlock with the tray walls. During a side or under-ride impact the vapor chamber behaves like a cross-member, arresting buckle while simultaneously distributing or removing heat through embedded coolant tubes and optional heaters. One multifunctional panel replaces separate steel reinforcements and gains package volume.
Side intrusion asks the structure to deform without driving loads into the cell block. Bolt-on geometry like the gap-tuned side-sill shield is positioned outboard of the battery. Calibrated cavities to both pack and sill allow the hollow two-plate shield to crush internally before feeding residual forces into the body through a secondary path. Shared attachment points reduce hardware and optional corner wraps extend coverage under the pack.
When a design goal is for the battery itself to absorb energy, the inclined front wall with cross-member comes into play. An angled crash box and a lateral brace at the pack’s leading edge intercept frontal sub-frame loads and direct them away from mounting bolts and high-voltage parts. The geometry uses simple stampings rather than complex draw dies, which helps cost.
Multiple teams are layering sacrificial or adaptive media directly inside the housing. Crush-able cooling conduits sit between cell modules and the lower enclosure, collapsing like miniature crash tubes while still circulating coolant in normal driving. Where higher-speed events are a concern, an on-demand inflatable cushion can be triggered within milliseconds, filling gaps between cells and casing so impact loads are spread over a larger area without permanent weight penalty. A passive companion, the multi-layer air-column shell, surrounds the pack with concentric sealed air pockets that double as thermal insulation and can replace heavy skid plates.
Material tailoring further refines the stiffness-absorption mix. Tailored stamp-hardened strips boost strength only along critical paths in a hot-stamped trough while leaving other zones ductile enough to fold as crash boxes. Beneath the pack, a hybrid composite-metal bottom plate sandwiches a steel core between fibre-reinforced skins so delamination, stone impact, and corrosion are all checked by matched thickness ratios. Inside the lateral frame, a curved shock-absorber insert dissipates side-impact energy, allowing ultra-high-strength wall sections to be made thinner. Finally, variable-width rocker rails flare outward only where crush zones are required, giving programmable deformation without growing the overall footprint.
A housing that resists deformation buys seconds, yet cell vent gases will still need an exit. The next layer therefore addresses high-mass-flow venting.
4. Integrated Gas Venting and Smoke Exhaust Paths
Thermal runaway can release large volumes of hot, conductive gas. If the plume is trapped, it can melt insulation and create pack-level fires. The integrated underride-protection venting channel tackles mass-flow and road-debris impact in one sheet-metal component. A metallic underride plate contacts the battery housing at two reinforced walls, leaving a deliberate gap between. During a bottom strike the plate steers loads into those walls, shielding cells. In a thermal event the same gap becomes the lead section of a gas channel that routes the plume out of the enclosure where it can cool and lose conductivity. No added vent stack or extra package is required, and the channel can be pressed or stamped to match any floorpan.
Venting controls the immediate over-pressure, but it cannot halt propagation once adjacent modules begin to heat. Passive barriers that activate only where needed therefore follow.
5. Passive Thermal Barriers and Propagation-Mitigating Materials
Where permanent insulation is impossible, distance can be created on demand. The telescopic expansion barrier uses slim rods placed between neighbouring modules. Temperature, voltage, flame, and gas sensors feed an intelligent control unit; when incipient runaway is detected, the rods extend, forcing modules apart and inserting an insulating air layer. Elastic water-chiller tubes weave through the supports so the cooling loop keeps operating even after geometry changes. The rods only deploy where necessary, so volume and mass penalties are modest.
If space or weight leaves no room for temporary gaps, the failing module itself can be removed. The self-ejecting module architecture treats runaway cells as their own propellant. When internal pressure or temperature meets a threshold, thermal-pressure tubes unlock an inner casing, and a combination of springs, gas boosters, wheels, and a tilting shaft pushes the module clear of the array. Conductive, convective, and radiative paths are severed in one motion, and multiple redundant triggers ensure the mechanism still works even if one actuator fails.
These passive concepts restrict heat propagation over tens of seconds, creating a window in which active systems can intervene. The focus therefore shifts to cooling, suppression, and managed energy removal.
6. Active Cooling and Fire-Suppression Control during Thermal Runaway
Standard EV logic disconnects the battery at the first sign of danger, which inadvertently de-energizes the very pumps and fans needed to remove heat. Several inventions retain power for those devices. In dual-battery emergency cooling a healthy auxiliary pack is self-tested, switched in through the power-distribution unit, and assigned to drive the coolant loop until the runaway pack stabilises. The same philosophy scales to module level in the healthy-module powered cooling path; here the battery-management system isolates the failed module but reroutes energy from a neighbouring one to the chiller circuit, bypassing the low-voltage bus. To shorten electrical paths even further, an internal switch gate inside the enclosure provides on-pack, redundant-module cooling without external piping. A different approach, the power-off override for coolant circulation, energises pumps from an auxiliary source whenever thermal disequilibrium is detected, even if the vehicle is keyed off.
Cooling sometimes needs help from quenching agents. The impact-severity-modulated liquid-nitrogen injection routes cryogen into the pack within milliseconds after a crash, employing a neural network to set valve opening and avoid both under- and over-cooling. For non-crash scenarios, two passive spray concepts exploit the runaway itself as the trigger: a conduit placed near a pre-weakened cell wall ruptures and floods the cell in the self-opening coolant pipeline, while an internal mist system delivers high-latent-heat water to offending cells in the pressure-optimised spray suppression pack. Both localise extinguishing media directly at the heat source and add negligible mass in normal operation.
Some concepts integrate cooling and energy management. The step-by-step prevention and control architecture combines early fault prediction, local coolant routing, gas extraction, and fire-extinguishing agents in one hierarchy, escalating only as needed. The dying-sacrifice high-power load strategy forces heaters, air-conditioning compressors, and even traction motors to absorb residual charge while occupants evacuate. Where external power may be unavailable, the self-powered suppression module harvests electricity from the failing cells themselves to drive coolant or inert-gas actuators, and the auxiliary discharge-and-cooling add-on bolts onto existing BMS hardware to isolate, load-dump, and chill suspect cells in a coordinated sequence.
When the fire is out and temperatures have plateaued, attention moves to the residual energy and materials locked inside the damaged pack.
7. Post-Crash Discharge and Recycling Techniques for End-of-Life Batteries
Compromised packs still hold significant energy and flammable solvent, so immediate neutralisation is essential. The grate-preheated low-oxygen detoxification heats intact packs below 400 °C in a reducing atmosphere to vaporise electrolyte without ignition, followed by a controlled crush and a secondary 400 °C to 660 °C roast that liberates cathode materials. Manual disassembly is eliminated, which accelerates roadside or depot-level stabilisation.
Once the modules are inert, high-value metals must be recovered without strong acids. A dry two-step inert-atmosphere phase-separation route heats spent NMC or NCA powders above 900 °C, splitting the lattice into Li₂O and a discrete Ni/Co-rich oxide. Water leaching then dissolves only the lithium, leaving a clean transition-metal concentrate. The absence of acid cuts reagent cost and toxic effluent.
Leachates that do exist elsewhere in the flow-sheet can be refined electrically. The electro-nanofiltration silicon module applies a tunable field across nano-porous channels, steering monovalent Li⁺ through while arresting or plating multivalent Co, Ni, and Mn on the membrane. One stage replaces precipitation, solvent extraction, and crystallisation, shrinking plant footprint and raising purity.
Two persistent contaminants are then closed-looped. Shredded current-collector foil is removed by selective in-process aluminium capture, and the recovered Al is reincorporated into new electrodes so energy density is preserved. Finally, the Li₂O/NH₃ halogen scavenging loop converts corrosive super-halide complexes into benign LiCl or saleable NH₄Cl crystals, returning the expensive anhydrous solvent to service.
These chemistries close the loop on both energy and materials, completing the safety chain that began with millisecond-scale crash structures and ended with a truly circular end-of-life workflow.
Get Full Report
Access our comprehensive collection of 69 documents related to this technology
Identify Key Areas of Innovation in 2025
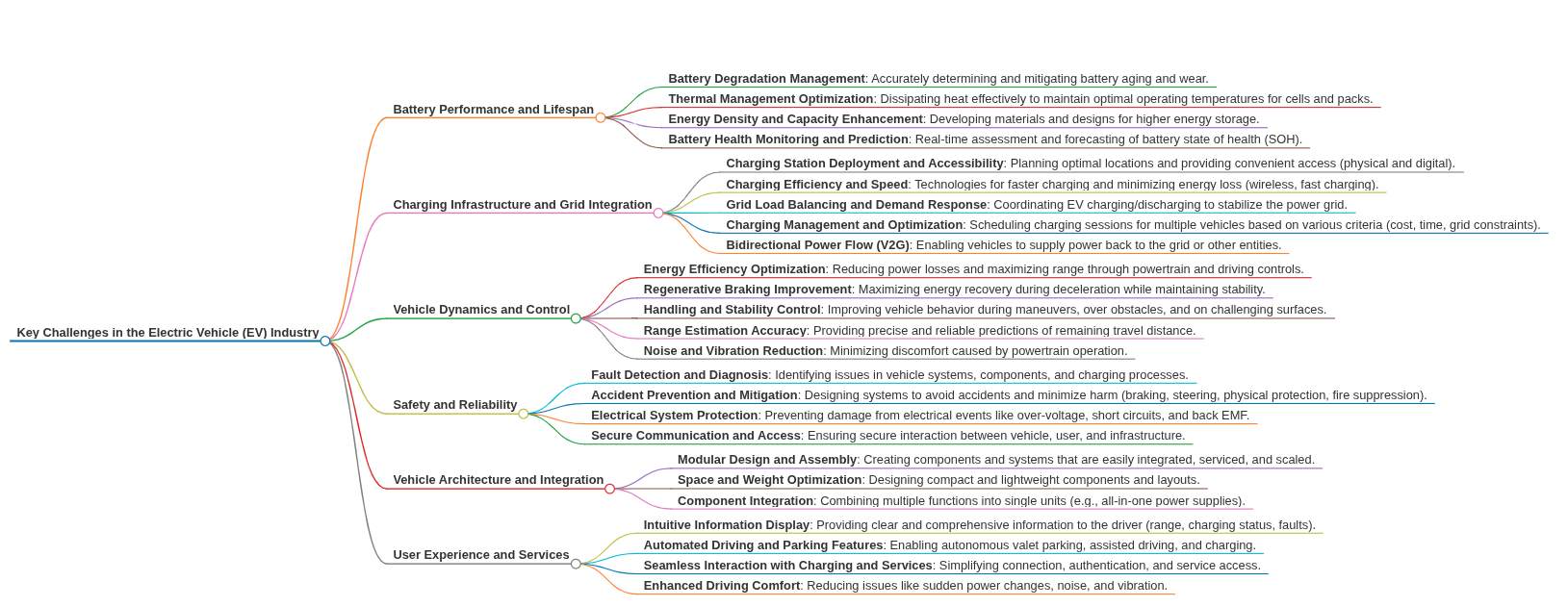