Tesla's Innovations in Battery Management Systems
Tesla's battery management systems handle complex thermal and electrical interactions across thousands of cells, with individual cell temperatures ranging from -20°C to 60°C during normal operation. The system must maintain precise voltage and temperature control while managing charge rates up to 250 kW during Supercharging—all while monitoring for early indicators of cell degradation or thermal events.
The fundamental challenge lies in balancing aggressive performance targets with the need to prevent thermal runaway propagation and maintain cell longevity across widely varying operating conditions.
This page brings together solutions from recent research—including predictive thermal preconditioning for fast charging, multi-mode cooling valve architectures, controlled gas venting mechanisms, and redundant communication systems for pack monitoring. These and other approaches show how Tesla is addressing battery management challenges while maintaining high performance and safety standards.
1. Battery Pack Enclosure with Emergency Coolant Ingress and Controlled Breach Mechanism
Tesla, Inc., 2021
A system for allowing controlled cooling of electric vehicle battery packs during internal thermal events. The system provides a way to ingress coolant like water into the sealed battery enclosure during thermal runaway conditions. This allows direct contact with the affected cells to remove heat and mitigate chain reactions. A specialized fill port is used for normal coolant refilling. But in emergency situations, a perforation tool can breach the enclosure wall to allow coolant ingress through a specific hole. The tool has features to prevent unintended breaches. The hole location is also designed to minimize damage and contamination. The breach-and-fill method provides a controlled way for first responders to cool a battery pack in an urgent situation where normal coolant access is unavailable.
2. System for Monitoring and Mitigating High Voltage Electrolysis in Electric Vehicle Battery Packs
Tesla, Inc., 2020
Detecting and mitigating high voltage electrolysis within electric vehicle battery packs to prevent thermal runaway and hydrogen buildup. The system uses sensors to monitor for conditions like coolant leaks and bridged terminals that can lead to electrolysis. If electrolysis is detected, the system responds by cutting power to prevent further energy input, and actively cooling the electrolyzing area to prevent boiling and temperature rise. This prevents chain reactions and thermal runaway that can occur from electrolysis.
3. Electric Vehicle Thermal Management System with Coolant Loop Bypass Valve for Independent Flow Regulation
Tesla, Inc., 2019
Thermal management system for electric vehicles that allows continuous and optimized control of battery cooling and passenger cabin cooling. The system uses a bypass valve in the coolant loop that allows splitting the coolant flow between going through the heat exchanger and bypassing it. This allows independent regulation of the amount of coolant going through the heat exchanger versus bypassing it. By adjusting the bypass valve, the system can fine-tune the cooling of the battery pack and passenger cabin to maintain desired temperatures within preset ranges. It also provides flexibility to balance cooling demands when the compressor output of the refrigeration system cannot be increased further. The bypass valve also allows bypassing the heat exchanger entirely for very low battery pack temperatures, further optimizing cooling.
4. Underfloor Battery Pack Base Plate with Thermally Coupled Decoupling Heat Exchanger
Tesla, Inc., 2019
Integrating a heat exchanger into the base plate of an underfloor battery pack in an electric vehicle. The heat exchanger is thermally coupled to the batteries when the pack is in operation. When the pack is not in use, the heat exchanger is decoupled from the batteries. This allows optimal heat transfer from the pack to the ambient air flowing over the exposed base plate during vehicle motion. An integrated heat exchanger like this provides efficient cooling without stacking multiple heat exchangers, reducing power losses and improving performance.
5. Battery Cell Preconditioning System with Predictive Charge Type Identification and Temperature Adjustment Mechanism
TESLA, INC., 2017
Efficiently fast charging electric vehicle batteries by preconditioning the battery cells before charging to improve charging efficiency. The method involves predicting if an upcoming charge will be fast or slow, and if fast, adjusting the battery cell temperature above the standard operating temperature. This is done by identifying an impending fast charge opportunity and using that information to prepare the battery cells for the fast charge by raising their temperature above the normal operating temperature. This improves fast charging efficiency compared to trying to cool the cells during fast charging. The technique involves a charge prediction system that identifies upcoming fast or slow charges, and an environment control system that adjusts the battery cell temperature based on the prediction.
6. Automated System for Dynamic Charging Rate Adjustment of Lithium-Ion Batteries Based on Critical Parameter Monitoring
Tesla, Inc., 2017
Automated method and apparatus for low temperature fast charging of lithium-ion battery packs to enable fast charging at cold temperatures without risk of lithium plating. The method involves periodically monitoring critical parameters like cell temperature, state of charge, and current to determine if fast charging is safe. If conditions allow, fast charging is used. Otherwise, slower charging is used. This allows fast charging at low temperatures without disabling it completely. The charging rate scales dynamically based on the critical parameters.
7. Battery Cell Cap with Ejectment Structure for Controlled Gas and Debris Release During Thermal Runaway
TESLA, INC., 2017
Battery cell design to prevent cell rupture during thermal runaway by efficiently releasing hot gas and debris through the cell cap. The design involves creating a specialized ejectment structure in the cell cap that responds to specific combustion properties of the electrode materials. This structure provides an aperture to direct combustion gases and debris out of the cell in a controlled manner, reducing the likelihood of side wall perforation compared to conventional cells. The ejectment aperture is created by responding to preselected combustion properties like temperature and pressure. This allows hot gases to escape the cell through the cap rather than penetrating the side walls.
8. Modular Energy Storage System with Galvanic Isolation and Independent Power Electronics for Parallelization of Dissimilar Battery Blocks
Tesla Motors, Inc., 2017
Scalable, modular energy storage system that allows parallelization of multiple battery blocks with different cell types, ages, and voltages without requiring exact voltage matching. The system uses galvanic isolation and power electronics converters for each battery block to provide a common DC interface. This allows failure independence, scalability, and parallelization of dissimilar batteries without propagation or system-wide voltage balancing.
9. External Thermal Conditioning System with Adaptive Thermal Interface for Electric Vehicle Battery Management During Charging
Tesla Motors, Inc., 2016
External thermal conditioning system for electric vehicles that provides active cooling or heating of the vehicle's battery pack during charging to maintain optimal operating temperatures. The charging station detects the battery's thermal information and provides customized thermal conditioning through connections like fluid loops, air intakes, or contact pads. This allows external cooling during fast charging when internal systems can't keep up, or heating to bring the battery up to a required temperature. It enables more efficient and flexible charging by supplementing the onboard cooling system.
10. Series-Connected Battery Pack System with Dual-Mode Exceptional Charge Event Detection and Response Mechanism
TESLA MOTORS, INC., 2016
Detecting and responding to exceptional charge events in series-connected battery packs to prevent overcharge and overdischarge. The system uses two detection modalities: steady-state analysis of charge-dependent parameters like voltage and impedance, and transient analysis during charging and discharging to detect deviations from normal behavior. If an exceptional charge event is detected, responses like preventing further charging, increasing cooling, or service intervention are triggered to mitigate potential hazards.
11. Battery Pack Service System with External Charging and Discharging Capability
TESLA MOTORS, INC., 2016
A system and method for charging and discharging high voltage battery packs outside of the vehicle they are normally installed in. The system allows maintenance and management of battery packs when the vehicle is not operational or the pack is compromised. It uses a separate battery service unit with access to the pack's ports. The unit can charge/discharge the pack directly or simulate the vehicle environment to trigger the pack's BMS. This enables setting pack SOC levels without needing a functional vehicle. It also provides charging/discharging for storage, transport, recycling, and servicing scenarios.
12. Multi-Stage Charging Protocol for Lithium-Ion Batteries with Dynamic Voltage and Current Adjustments Based on State-of-Charge, Temperature, and Internal Resistance
TESLA MOTORS, INC., 2016
Fast charging lithium-ion batteries to reduce charging time without degrading cycle life. The charging process involves multiple stages with adjustable voltages and currents based on factors like cell state-of-charge, temperature, and internal resistance. This allows fast charging without excessive voltage or current levels that can damage the battery. The stages are: 1) initial constant current with increasing voltage, 2) intermediate stages like constant voltage, constant current, or decreasing current, 3) final constant voltage with decreasing current. The intermediate stages are selected based on resistance, SOC, and temperature to prevent overcharging or plating. The adjustable profile compensates for resistance changes and reduces degradation compared to fixed two-step CC-CV charging.
13. Lithium-Ion Cell Manufacturing with Liquid-Based Thermal System for Accelerated Reaction and Testing
Tesla Motors, Inc., 2016
Improving the manufacturing process of lithium-ion cells by using a liquid-based thermal system for accelerating chemical reactions, capacity testing, and OCV measurement during cell assembly and formation. The cells are stored in contact with circulating liquid at elevated temperatures to initiate and accelerate chemical reactions. After initial charging/discharging, open circuit voltage (OCV) testing is done at high and low temperatures. Cells are then cooled and tested again. Finally, capacity testing is performed. This sequence allows accurate detection of defects using OCV and capacity tests. The liquid thermal system provides even temperature distribution, faster reaction times, and more accurate capacity measurement.
14. Battery Pack with Charge State Detection and Remediation for Series-Connected Elements
Tesla Motors, Inc., 2016
Detecting and remediating exceptional charge states in individual battery elements of a series-connected battery pack. The technique involves monitoring charge-dependent parameters during operation to establish characterizations for each element. If a selected element's characterization shows an exceptional charge pattern during operation, it indicates an imbalance. This detects charge anomalies that voltage monitoring misses. Responses to exceptional charge events include preventing charging, increasing cooling, and limiting charging cycles.
15. Electric Vehicle Battery Disconnection System with Pyrotechnic Switch for Collision Response
Tesla Motors, Inc., 2015
A system for safely disconnecting the high voltage battery of an electric vehicle in the event of a crash. It uses a pyrotechnic switch instead of an inertial switch to decouple the battery. The pyrotechnic switch has a pre-activated state allowing normal battery operation. But upon receiving a collision signal from the airbag system, it activates to sever the battery connection. This prevents unnecessary battery decoupling for minor collisions while ensuring decoupling for severe crashes.
16. Battery Pack System with Dual-Mode Charge Event Detection and Remediation Mechanism for Series-Connected Cells
Tesla Motors, Inc., 2015
Detection and remediation of exceptional charge states in battery packs with series-connected cells. The system detects excessive overcharge or overdischarge of individual cells in a pack beyond normal limits. It uses two types of charge event detection: one for steady state charging and one for transient charging. For steady state, statistical analysis of cell parameters is used. For transient, deviations in cell impedance during discharge are monitored. If an exceptional charge event is detected, responses like preventing charging, reduced cooling, or service are taken to mitigate risks like thermal runaway.
17. Battery Pack with Fluid-Filled Conduits for Thermal Runaway Mitigation Through Temperature-Triggered Breach Mechanism
Tesla Motors, Inc., 2015
Mitigating thermal runaway in battery packs to prevent cascading cell failures and contain the thermal energy release. The system uses fluid-filled conduits around the cells that breach at lower temperatures than the cell materials. When a cell enters thermal runaway, the breach allows fluid to discharge onto the overheating cell, cooling it and nearby cells. This helps prevent propagation of thermal runaway. The fluid can be pumped or from a source, and sensors monitor pressure, temperature, and fluid level.
18. Battery Pack Thermal Event Detection via Pressure Data Anomaly Analysis with Exponential Decay Curve Fitting
Tesla Motors, Inc., 2015
Detecting thermal events like thermal runaway in battery packs using pressure data analysis. The method involves dividing pressure data into sets, detecting anomalies, fitting curves to trailing edges, and checking time constants. If an anomaly's trailing curve fits an exponential decay with a certain time constant range, it indicates a thermal event. This helps distinguish true thermal events from false positives caused by vibrations or noise. The system also checks curve goodness of fit. If a thermal event is detected, it triggers an appropriate response.
19. Battery Pack with Rigid Substrates for Force Distribution and Integrated Cooling System
Tesla Motors, Inc., 2015
Battery pack design to improve reliability, durability, and cooling for applications like electric vehicles. The pack sandwiches batteries between rigid substrates that distribute force to prevent crushing. Conductors draw power and connect parallel/series between the batteries. Holes in the substrates prevent shorting. Cooling is via air blown through the pack and interconnected cooling tubes. The pack shape closely fits space, reducing wasted area.
20. Battery Pack Monitoring System with Electrical Isolation Resistance Detection and Failure Containment Mechanism
Tesla Motors, Inc., 2015
Early detection of thermal events in batteries to prevent propagation and mitigate damage. The system monitors the electrical isolation resistance of a battery pack. If the resistance drops below a threshold, indicating cell failure, the system responds to contain the failure. The response can be a warning, reducing load, increasing cooling, or activating fire containment. The system also tracks the isolation resistance fall and recovery to distinguish between initial venting and subsequent runaway.
Get Full Report
Access our comprehensive collection of 69 documents related to this technology
Identify Key Areas of Innovation in 2025
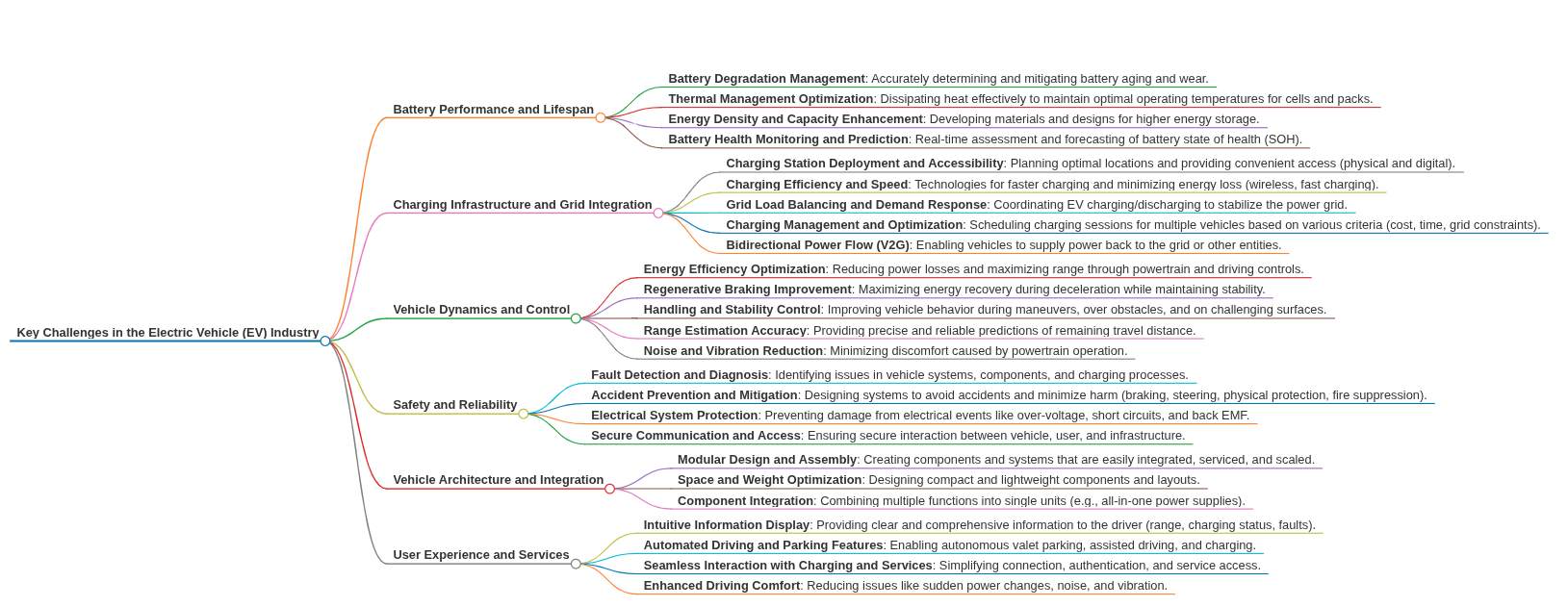