EV Battery Packaging to Prevent Thermal Runaway
Thermal events in EV battery packs present significant engineering challenges, with individual cell temperatures potentially exceeding 180°C during thermal runaway. Recent data shows that without proper thermal barriers and venting mechanisms, cell-to-cell propagation can occur in less than 60 seconds, while accumulated gases can create dangerous pressure buildups within sealed battery enclosures.
The fundamental challenge lies in designing packaging systems that can both prevent thermal propagation between cells and safely manage gas venting while maintaining the pack's structural integrity and thermal efficiency during normal operation.
This page brings together solutions from recent research—including distributed heat sink architectures, intelligent venting pathways with debris mitigation, thermally-responsive partition materials, and multi-compartment isolation approaches. These and other developments focus on implementing practical safety measures that can be integrated into mass-production vehicle designs while meeting both thermal management and crash safety requirements.
1. Hybrid Thermal Management Systems Using Nano-PCM for Battery Cooling in Electric and Solar Vehicles
sanjay r kumavat, shyam sunder agrawal, 2025
The advancement of electric and solar vehicles demands efficient sustainable thermal management solutions to ensure optimal battery performance, safety, longevity. This chapter presents a comprehensive exploration hybrid systems (HTMS) employing nano-enhanced phase change materials (nano-PCMs) as next-generation strategy for effective cooling. Nano-PCMs combine the latent heat storage capability traditional PCMs with superior conductivity nanomaterials, thereby overcoming limitations conventional cooling systems. integration passive active control methods within HTMS is examined, highlighting improved temperature uniformity, accelerated dissipation, enhanced energy efficiency under varying operational conditions. Emphasis placed on material synthesis, thermophysical characterization, system-level modeling nano-PCM-based architectures tailored solar-powered vehicle platforms. role nanomaterials such graphene, carbon nanotubes, metal oxides in augmenting performance analyzed, along techno-economic considerations real-time testing data. also addresses design challenges, environmental im... Read More
2. Lithium-Ion Battery Thermal Management System with Directional UHMWPE Fabric
CILOGEAR, 2025
A passive thermal management system for lithium-ion batteries in portable electronic devices that prevents overheating and thermal runaway without active cooling or heavy components. The system uses a specially designed fabric made of ultra-high molecular weight polyethylene (UHMWPE) with directional thermal conductivity. The fabric surrounds the battery and provides a long thermal path with high conductivity in the battery's main direction of heat generation. The UHMWPE fabric absorbs and conducts the heat away from the battery as it generates it, preventing hotspots and thermal runaway. The fabric's low density and floating property make it neutrally buoyant for marine applications.
3. Coupon-Level Experimental Material Screening of Carbon Fiber-Reinforced Polymers under Thermal Runaway Conditions for eVehicle Applications
margarita etchegaray bello, ovul ozgu ozsoy, jan schoberl - Trans Tech Publications, 2025
The shift towards electric mobility needs extensive research into battery modules, particularly in relation to safety due the high energy density of Li-ion batteries. Battery casings must be able protect module from external impacts while also containing any potential danger event internal failure. This study presents a comprehensive qualitative screening thermoset and thermoplastic carbon fiber-reinforced polymers (FRP) used automotive aerospace applications under thermal runaway (TR) conditions, identify suitable materials for enclosures. test setup is an adaptation UL 2596 standard with hexagonal array seven 21700-format cells. results indicate that CF-PEEK, CF-PPS, aerospace-grade epoxy, CF-EP str (primary structural material) effectively contain TR low damage using current setup. Medium was observed CF-PC, CF-bio-based phenolic, non-structural CF-epoxy CF-PA6 failed TR. serves as initial process narrow down further in-depth analysis, emphasizing need reproducible events accurate assessment.
4. A Layered Swarm Optimization Method for Fitting Battery Thermal Runaway Models to Accelerating Rate Calorimetry Data
saakaar bhatnagar, andrew comerford, zelu xu - Institute of Physics, 2025
Abstract Thermal runaway in lithium-ion batteries is a critical safety concern for the battery industry due to its potential cause uncontrolled temperature rises and subsequent fires that can engulf pack surroundings. Modeling simulation offer cost-effective tools designing strategies mitigate thermal runaway. Accurately simulating chemical kinetics of runaway, commonly represented by systems Arrhenius-based Ordinary Differential Equations (ODEs), requires fitting kinetic parameters experimental calorimetry data, such as Accelerating Rate Calorimetry (ARC) measurements. Particle Swarm Optimization (PSO) offers promising approach directly data. Yet, created multiple Arrhenius ODEs, computational cost using brute-force searches entire parameter space simultaneously become prohibitive. This work introduces divide-and-conquer based on PSO fit N-equation ODE models ARC The proposed method achieves more accurate compared while maintaining low costs. analyzed two distinct datasets, resulting are further validated through simulations 3D oven tests, showing excellent agreement with data align... Read More
5. Secondary Battery with Compression and Tension Member Constraint System for Electrode Stability
ENOVIX CORP, 2025
A secondary battery with an enclosure, electrode assembly, and non-aqueous electrolyte that uses a constraint to prevent expansion and buckling of the electrode stack during cycling. The electrode assembly has opposing ends and a lateral surface. Compression members overlie the end projections, tension members overlie the lateral surface. This maintains pressure in the stacking direction exceeding the perpendicular directions. The constraint can be inside or outside the enclosure. This prevents expansion and buckling as the battery cycles and prevents short circuits.
6. Battery Module with Elastic Member and Thermally Expanding Resin for Heat Propagation Control
TOYOTA JIDOSHA KABUSHIKI KAISHA, 2025
Battery module design with improved thermal management to prevent heat propagation between cells in high temperature conditions. The module has an elastic member between adjacent cells and a thermally expandable resin composition inside the elastic member. This resin expands at 80°C or higher to restrict heat conduction between cells when they get hot. The resin has low thermal conductivity after expansion. The elastic member can have a concave/convex pattern.
7. Battery Module with Controlled Venting Mechanism and Opposing Cell and Housing Vents
DR ING H.C F PORSCHE AG, 2025
Battery module design for electric vehicles that improves safety in the event of a battery fault or accident by allowing controlled venting of gases to prevent overpressure and thermal runaway. The module has multiple vents in the housing walls and opposing cell vents. The housing vents initially close but open to allow partial venting if pressure rises. The cell vents initially close but open to vent gases directly. This prevents pressure buildup and prevents cell rupture while allowing venting to the outside. The housing vents also have covering parts between the cell and housing that allow straight path venting.
8. Research on DP-MPC control strategy based on active equalisation system of bidirectional flyback transformer
yingzhe kan, min yang, run qian, 2025
<title>Abstract</title> The inconsistency between power battery cells can seriously restrict the energy utilization efficiency of pack, accelerate aging batteries, and even significantly increase risk thermal runaway. Aiming at this inconsistency, an active equilibrium scheme combining dynamic programming (DP) model predictive control (MPC) is proposed. Firstly, topology circuit bidirectional flyback transformer with rapid equalization speed built, then a system prediction established through MPC to achieve rolling optimization. Finally, using DP solve cost function in conditional scenarios obtain global optimal current time, used predict state changes multiple sampling periods online correction balanced current. algorithm improves overall reduces loss while considering charging discharging equalizer ensure consistent convergence each individual SOC. Simulation experimental results show that strategy quickly effectively correct lithium packs under various conditions, thereby greatly improving balance pack.
9. Electrochemical Cell with Gradient Thickness Interlayer for Dendrite Detection and Mitigation
24M TECHNOLOGIES INC, 2025
Electrochemical cells with interlayers between the anode and cathode to prevent dendrite growth and mitigate safety issues like short circuiting and thermal runaway. The interlayer has a thickness that increases towards the cathode end. If a dendrite grows into the interlayer, it can be detected by monitoring the voltage potential. A battery management system can then discharge the cell and use the remaining energy to power other devices, removing cell energy to create a safe condition. The interlayer voltage can also be actively changed to stop dendrite growth or dissolve it.
10. Secondary Battery Sheath with High-Conductivity Metal Layer for Thermal Regulation
SAMSUNG SDI CO LTD, 2025
A secondary battery with improved thermal management to prevent overheating and extend battery life. The battery has a unique sheath design with a thick metal layer making up 50-70% of the total sheath thickness. The metal layer provides high thermal conductivity to efficiently dissipate heat generated during charging and discharging. This reduces the internal battery temperature without adding bulk. The remaining sheath thickness is non-metal insulation layers.
11. Stacked Perforated Separator Plates with Interconnected Zigzag Channels for Liquid Immersion Cooling of Battery Packs
GM GLOBAL TECHNOLOGY OPERATIONS LLC, 2025
Liquid immersion cooling (LIC) system for battery packs that uses stacked perforated separator plates between cell rows to distribute coolant fluid vertically upward between the cells. The separator plates have interconnected coolant channels with angled grooves on one plate aligned with opposite angled grooves on the other plate. This zigzag channel pattern creates a pressure differential that forces coolant to flow vertically between the cells. The perforated plates with angled channels stacked between cell rows improve LIC cooling by distributing the coolant fluid over and between the cells.
12. Lithium Battery with Metallized Composite Current Collectors and High Temperature Nonconductive Materials
SOTERIA BATTERY INNOVATION GROUP INC, 2025
Lithium battery with improved safety against short circuits and fire hazards. The battery uses thin metallized surface composite current collectors, high shrinkage rate separators, and materials that become nonconductive upon exposure to high temperatures. This internal fuse mechanism prevents undesirable high temperature results from short circuits. The thin current collectors stop conducting at the point of contact of an exposed short circuit. This allows for a safe discharge pathway during short circuits that prevents rapid discharge and high temperatures. The high shrinkage rate separators prevent shrinkage that could increase short circuit area. The nonconductive materials become nonconductive at high temperatures to further prevent high temperature issues.
13. Lithium Battery with Thin Polymer-Based Current Collectors for Rapid Oxidation in High Current Events
SOTERIA BATTERY INNOVATION GROUP INC, 2025
Lithium battery design that prevents thermal runaway and fires by using thin, low-resistance current collectors that short circuit and oxidize during high current events. The collectors are made with thin polymer substrates coated in conductive materials. The collectors have thicknesses below 20 microns and resistances below 1 ohm/square. When shorted, the thin collectors oxidize or degrade quickly, stopping the current flow before separator or cell damage. This internal fuse mechanism prevents runaway heating and fires compared to thicker, stable collectors.
14. Lithium-Ion Battery Thermal Runaway Suppression Using Water Spray Cooling
eric huhn, nicole braxtan, shenen chen - Multidisciplinary Digital Publishing Institute, 2025
Despite the commercial success of lithium-ion batteries (LIBs), risk thermal runaway, which can lead to dangerous fires, has become more concerning as LIB usage increases. Research focused on understanding causes runaway and how prevent or detect it. Additionally, novel runaway-resistant materials are being researched, different methods constructing LIBs that better isolate it from propagating. However, field firefighters using hundreds thousands liters water control large emergencies, highlighting need merge research with practical observations. To study battery fire, this utilized a temperature abuse method increase investigated whether be suppressed by applying external cooling during heating. The used were pouch-type ones subjected high states charge (SOC), primed increase. A spray was then devised tested reduce temperature. Results showed that, without cooling, fire occurred every time abuse. successfully prevented runaway. This observation shows reducer is effective than suppressant, substantially improve performance public safety.
15. Battery Module with Vertical and Lateral Heat Blocking Members for Thermal Runaway Containment
SK ON CO LTD, 2025
Battery module design to prevent thermal runaway propagation between cells in a battery pack. The module has a housing, a stack of battery cells, and two heat blocking members. The cell stack and first blocking member are vertically stacked. The second blocking member is between the stack and housing. This prevents lateral heat transfer between cells. The blocking members contact to fully isolate. The design forces contact between the vertical and lateral blocking to prevent gaps. This prevents flames and gases from spreading between cells and the housing.
16. A Thermal Runaway Protection Strategy for Prismatic Lithium-Ion Battery Modules Based on Phase Change and Thermal Decomposition of Sodium Acetate Trihydrate
tianqi yang, hanwei xu, changjun xie - Multidisciplinary Digital Publishing Institute, 2025
With the rapid development of battery energy storage technology, issue thermal runaway (TR) in lithium-ion batteries has become a key challenge restricting their safe application. This study presents an innovative protection strategy that integrates liquid cooling with sodium acetate trihydrate (SAT)-based composite phase change materials (CPCM) to mitigate TR and its propagation prismatic modules. Through numerical simulation, this systematically investigates mechanism optimization pathways for The results indicate pure SAT exhibits poor latent heat performance due low conductivity. In contrast, incorporation expanded graphite (EG) significantly enhances conductivity improves overall performance. Compared traditional paraffin-expanded (PA-EG), SAT-EG, 4.8 times higher than PA-EG, demonstrates more six effectiveness delaying (TRP). When combined cooling, effect is further enhanced, will not be triggered when initial abnormal generation rate relatively low. Even if experiences TR, prevented thickness SAT-EG exceeds 12 mm. Ambient temperature influences both peak timing occurrence modu... Read More
17. Design of Dielectric Fluid Immersion Cooling System for Efficient Thermal Management of Lithium‐Ion Battery Packs
s hemavathi, d a antopaul - Wiley, 2025
ABSTRACT Heat generation during fast charging and discharging of lithiumion batteries (LIBs) remains a significant challenge, potentially leading to overheating, reduced performance, or thermal runaway. Traditional battery management systems (BTMS), such as airbased cooling indirect liquid using cold plates, often result in high gradientsboth vertically within cells horizontally across packsespecially under highcurrent discharge rates. To address these issues, this study introduces evaluates steadystate convectionbased esteroil immersion (EOIC) technique for LIBs. Numerical simulations based on the Newman, Tiedemann, Gu Kim model, aligned with multiscale multidimensional principles, were performed both single 18650 cylindrical cell 4S2P pack. Experimental validations conducted 2C 3C rates at 25C ambient temperature. The EOIC system demonstrated temperature reduction up 13C 15C pack compared natural air convection achieved 10C gradient simulation results closely matched experimental data, maximum deviation only 2C, confirming model's reliabi... Read More
18. Thermal Performance Enhancement of Lithium‐Ion Batteries Through <scp>PCM</scp>/<scp>CuO</scp> Nanoadditives and Fin Integration: A Numerical Approach
s m d shehabaz, santhosh kumar gugulothu, raju muthyala - Wiley, 2025
ABSTRACT The efficiency and effectiveness of a battery thermal management system (BTMS) primarily depend on the lesser heat capacity phase change material (PCM). To improve performance BTMS, bare batteries with different extended surfaces (straight arc) are considered to enhance dissipation heat, leading significant enhancement performance. In present study, numerical simulations carried out study impact influence CuO (10%) nano additive dispersion in PCM. Also, analyses by modifying geometries arc fins battery. Results reported that proposed improved life 61%90% compared conventional BTMS systems. Extended boost exchange surface area, batterytoPCM/CuO dissipation, form novel method for conduction during liquid fraction melting. This network expands increasing fin radial distance, enhancing At ambient temperature range 15C45C, PCM/CuO/fin substantially PCMbased 163%, 192%, 212%, respectively. These findings demonstrate possibility straight shapes PCM control. experimental results show how these designs optimize transport, improving control under varied operating si... Read More
19. Characterization of Thermal Runaway of Lithium Ternary Power Battery in Semi-Confined Space
xu hai, chenghao hou, po hu - Multidisciplinary Digital Publishing Institute, 2025
In some new energy aircraft powered by lithium-ion batteries (LIBs), the LIBs operate in semi-confined spaces. Therefore, studying thermal runaway (TR) characteristics of such spaces is significant to safety research aircraft. This paper investigated TR space using external heating, and compared it with open terms behavior temperature changes lithium ternary power The results show that process can be subdivided into seven different stages according LIBs. Compared LIB space, has an additional explosion stage. temperature, maximum 708 C, heating rate 72.3 C/s, while 552 32.1 C/s. study beneficial for subsequent provision certain theoretical guidance use environments.
20. Core-Sheath Binder Fiber Heat Transfer Suppression Sheet for Battery Packs
IBIDEN CO LTD, 2025
Heat transfer suppression sheet for battery packs that prevents thermal runaway propagation between battery cells. The sheet has a unique core-sheath binder fiber structure and processing method to achieve both strength and heat insulation. The binder fiber has a higher melting core enclosed by a lower melting sheath. Processing involves melting the sheath while the core remains solid. This retains the core framework to prevent inorganic particle falling, while fusing the sheath to hold particles. It allows high temperature processing without particle loss. The sheet has excellent strength and heat insulation compared to wet-formed sheets.
Get Full Report
Access our comprehensive collection of 133 documents related to this technology
Identify Key Areas of Innovation in 2025
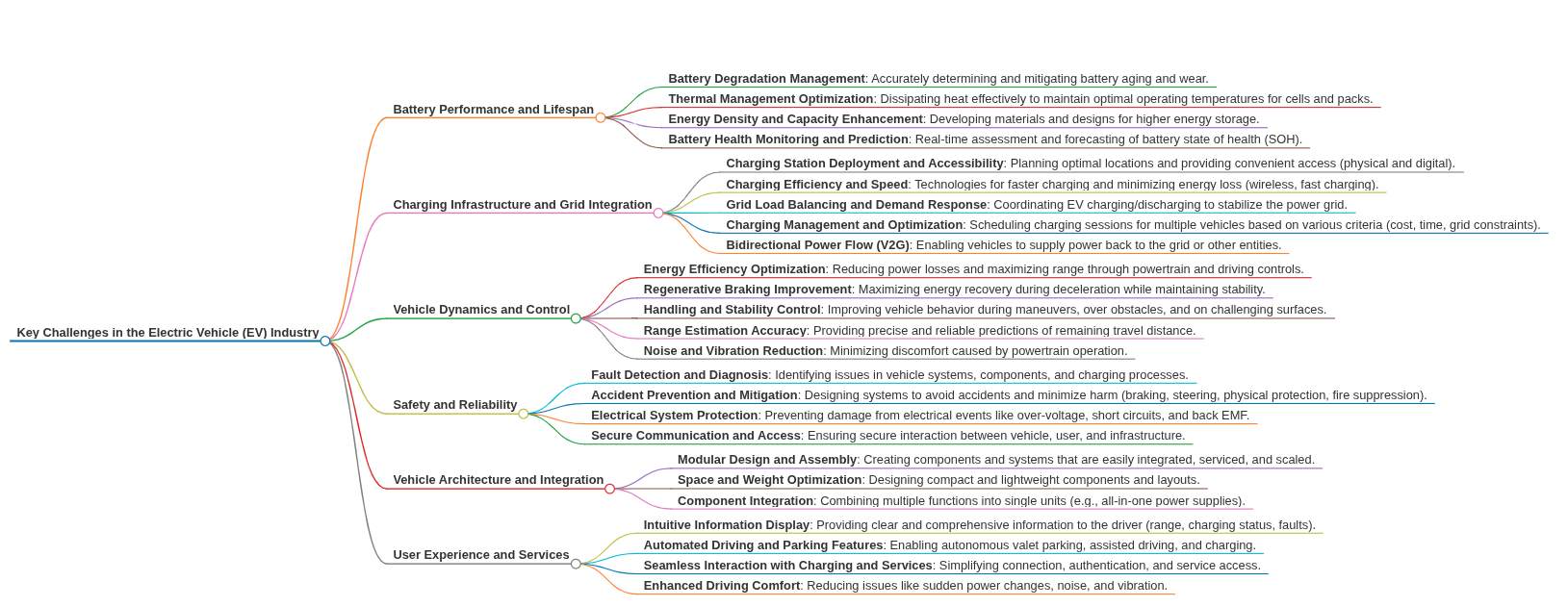