Lithium Extraction Processes from End-of-Life EV Battery Materials
Lithium-ion battery recycling presents significant material recovery challenges, with current processes achieving lithium extraction rates between 50-80% from end-of-life batteries. The black mass from shredded batteries contains valuable lithium compounds intermixed with other metals, electrolytes, and organic materials, requiring precise separation techniques to isolate high-purity lithium suitable for battery remanufacturing.
The fundamental challenge lies in developing extraction methods that can efficiently separate lithium from complex material mixtures while maintaining the purity levels required for battery-grade materials.
This page brings together solutions from recent research—including acid leaching processes, lithium phosphate precipitation techniques, electrolyte-based recovery systems, and integrated recycling-to-cathode manufacturing methods. These and other approaches focus on maximizing lithium recovery while minimizing energy consumption and process waste.
TABLE OF CONTENTS
1. Physical Disassembly and Pre-processing Technologies
The foundation of efficient lithium recovery begins with intelligent battery design and disassembly strategies that preserve material value while minimizing processing complexity. Traditional spot-welded interconnects create significant barriers to end-of-life material recovery, requiring destructive disassembly that damages valuable components and complicates downstream processing.
The detachable magnetized ICB cover represents a paradigm shift toward design-for-recycling principles. Permanent magnets embedded in interconnect circuit board covers create secure electrical connections through magnetic clamping rather than welding. This approach enables non-destructive disassembly at end-of-life, allowing individual cell harvesting without damaging leads or current collectors. The elimination of welds reduces manufacturing complexity while dramatically simplifying recycling operations.
Once cells are accessed, electrode material recovery faces the challenge of removing tenacious PVDF binders that secure active materials to current collectors. The TEP-enabled green delamination process addresses this bottleneck by using tri-ethyl phosphate at 100-150°C to dissolve PVDF completely. This approach releases intact active materials while preserving aluminum and copper foils for reuse, eliminating HF evolution and toxic solvents associated with conventional binder removal methods.
For aged cathode materials, surface contamination with LiOH, Li₂CO₃, and LiF compounds can severely impact electrochemical performance. The multi-component conductive surface layer treatment rejuvenates these particles through sequential organic rinsing, inorganic conversion, and solid-state reactions that transform resistive surface layers into ion-conductive phases. This surface engineering approach enables direct reuse of recovered materials without full metallurgical processing.
2. Thermal Pre-treatment and Roasting Technologies
Building on physical pre-processing, thermal treatment methods offer selective lithium liberation through controlled atmosphere roasting. These approaches address the fundamental challenge of separating lithium from transition metals without extensive chemical consumption or complex downstream separations.
The mobile shredder-roaster and electrochemical flowsheet integrates on-site processing with selective lithium extraction. Spent cells undergo low-temperature carbothermic roasting under 2-4 vol% H₂, converting lithium compounds to water-soluble phases while generating magnetically responsive Ni/Co alloys. This dual transformation enables simultaneous lithium extraction through aqueous washing and transition metal upgrading via magnetic separation, eliminating the need for complex acid-base processing trains.
The dual-waste reductive roasting strategy extends this concept by substituting fossil reductants with lignin-rich agricultural waste. Cathode scrap blended with milled biomass undergoes roasting at 550-600°C, where devolving organics provide reducing gases that selectively convert lithium phases to water-soluble forms. CO₂ sparging during subsequent water leaching accelerates dissolution by stabilizing Li⁺ as carbonate/bicarbonate species, creating a process that addresses two waste streams simultaneously.
For applications requiring higher selectivity, the graphite-assisted reduction roasting route utilizes discarded graphite anodes as in-situ reductants. Blending spent cathode powder with waste graphite enables carbothermic reduction that partially de-lithiates layered oxide structures, allowing >97% lithium extraction through plain water washing while preserving transition metals in solid form. This approach transforms every battery component into a resource while eliminating external reductant requirements.
3. Hydrometallurgical Approaches: Acid-Based Systems
While thermal pre-treatment provides selective lithium liberation, hydrometallurgical processing offers precise control over dissolution chemistry and enables recovery of all valuable metals. Advanced acid-based systems have evolved beyond conventional sulfuric acid leaching to address specific challenges in mixed-chemistry battery waste processing.
The hydrobromic-acid leaching route exemplifies this evolution by coupling dissolution and reduction chemistry in a single operation. Aqueous HBr simultaneously solubilizes Li, Ni, Co, and critically, Mn by reducing high-valent transition metals to divalent bromides while generating elemental Br₂. The bromine formed is stripped and partially re-oxidized to bromate, which selectively precipitates MnO₂ with >90% yield without disturbing lithium retention in solution. This closed Br⁻/Br₂/BrO₃⁻ loop eliminates external reductants and provides a sequential recovery pathway that tolerates graphite and metallic debris.
Complementing this approach, the integrated impurity-management and transition-metal co-recovery scheme addresses the broader challenge of mixed-waste processing through systematic purification. Following initial H₂SO₄ + H₂O₂ leaching, the liquor undergoes sequential treatment: cementation removes Cu, lime-oxidant dosing strips fluoride as CaF₂, and controlled pH adjustment co-precipitates Al, Fe, Ti, and phosphates. The purified sulfate stream enables either high-pH co-precipitation of stoichiometrically controlled NiₓMnᵧCo₁₋ₓ₋ᵧ(OH)₂ precursors or chromatographic separation yielding individual metal hydroxides.
4. Alternative Leaching Chemistries
Recognition of the limitations inherent in strong mineral acid systems has driven development of alternative leaching chemistries that offer improved selectivity and reduced environmental impact. These approaches leverage specific chemical interactions to achieve targeted metal dissolution while minimizing reagent consumption and waste generation.
The closed-loop formic-acid leach-distill-sinter train demonstrates the potential of organic acid selectivity. Concentrated formic acid operated at 60°C selectively dissolves virtually all lithium while passivating Co, Ni, Mn, and Fe as insoluble formates. Simple atmospheric distillation recovers 99.8% of the acid for reuse while isolating solid lithium formate, which converts to Li₂CO₃ during low-temperature sintering. This minimalist approach achieves ~100% lithium recovery at 99.994% purity without oxidants or high-temperature processing.
The membrane-coupled salt-splitting electroconversion extends organic acid selectivity by enabling direct LiOH·H₂O production. Following formic acid leaching, lithium-rich formate liquor feeds a multi-chamber electro-dialytic stack where bipolar and monovalent-selective membranes drive Li⁺ into catholyte while regenerating formic acid. This configuration eliminates sodium contamination associated with conventional precipitation methods while enabling continuous processing with lower energy demand than water electrolysis.
For applications requiring minimal chemical input, the Fe₇S₈-assisted alkaline leaching process provides atmospheric pressure lithium extraction. Phase-pure Fe₇S₈ generated by calcining FeS₂ at 500-900°C accelerates alkaline leaching kinetics, enabling 99.3% lithium recovery while maintaining leachate purity levels below 0.01 ppm for Ni/Co/Mn. This approach preserves transition metal value in solid residues while eliminating autoclave requirements.
5. CO₂-Enhanced and Carbonate-Based Systems
The integration of CO₂ chemistry into lithium recovery processes represents a convergence of environmental stewardship and process efficiency. These systems leverage carbonic acid chemistry to achieve selective lithium dissolution while potentially sequestering CO₂ and avoiding aggressive chemical environments.
The two-stage, near-neutral CO₂ leach-crystallization loop addresses the challenge of lithium recovery from refractory compounds such as Li₂CO₃, Li₃PO₄, and LiF. CO₂ bubbling through aqueous cathode slurries generates carbonic acid that converts these phases to highly soluble LiHCO₃ while maintaining pH between 5.5 and 8.5. This pH range promotes aluminum precipitation as Al(OH)₃ rather than dissolution, simplifying downstream processing. Subsequent degassing or cooling regenerates battery-grade Li₂CO₃ crystals in a closed-loop system with minimal reagent consumption.
Extending this chemistry to more aggressive conditions, the super-critical CO₂ fluidized-bed system operates at 25-200°C under supercritical CO₂ pressures. Dense CO₂ phase permeation achieves 60% lithium dissolution in one hour and >90% in two hours while maintaining cobalt, nickel, and aluminum in solid residues. This approach eliminates roasting, strong acids, and aluminum-foil removal while providing a compact, continuous flowsheet with reduced energy demand and greenhouse gas footprint.
The CO₂-pressurized selective lithium leach demonstrates the applicability of this chemistry to mixed electrode powders. Modest CO₂ pressure exposure converts lithium to soluble carbonate/bicarbonate species while nickel, cobalt, and manganese remain locked in oxide lattices. This selectivity enables 93-97% lithium dissolution with clean stream separation, pushing overall Li recovery above 91% while maintaining >98% transition metal recovery in solid residues.
6. Electrochemical and Membrane-Based Separation Technologies
The evolution toward electrochemical lithium recovery reflects growing recognition that conventional precipitation and crystallization methods often represent the bottleneck in achieving high-purity products. These advanced separation technologies offer precise control over lithium concentration and purity while enabling continuous processing and reagent recycling.
The in-cell fast-charging redox-targeting strategy transforms retired batteries into their own separation vessels. Repeated charging at 1-5 C rates under mild compression intentionally plates lithium metal at the anode/separator interface while accumulating SEI-derived salts in the same region. This approach eliminates external acids, bases, and organic solvents, with the plated layer dissolving in deionized water to yield LiOH or Li₂CO₃ at >90% recovery rates. The method preserves graphite on copper foil and leaves cathode chemistry intact for separate processing.
For applications requiring ultimate purity, the selective lithium-ion conducting membrane cell operates at ambient temperature with ceramic or composite membranes that admit only Li⁺ while blocking all other ions. This configuration drives impurity levels below 20 ppm and delivers >99.998 wt% lithium, well above thresholds required for solid-state batteries. The continuous, modular architecture enables lithium deposition onto moving foil with real-time isolation of failed cells, eliminating the high-temperature molten salt electrolysis used in conventional processing.
Complementing these electrochemical approaches, the single-step chromatographic lithium polishing process addresses the persistent challenge of transition metal and alkaline earth contamination in black-mass leachates. Weak-acid cation-exchange resins with carboxylic sites enable lithium elution within 0.8-2 bed volumes at ~1.5× concentration while retaining Ni, Co, Mn, and Al for subsequent acid stripping. This ambient-temperature operation eliminates high-temperature processing while achieving battery-grade purity through simple regeneration cycles.
7. Advanced Extraction and Purification Technologies
The integration of advanced materials and process intensification techniques has opened new possibilities for lithium recovery that combine high selectivity with reduced environmental impact. These technologies often leverage novel solvents, advanced materials, or process intensification to achieve performance levels unattainable through conventional methods.
The mesoporous SBA-15 adsorptive capture system employs surface-modified molecular sieves with tailored mesopores and functional groups displaying exceptional Li⁺ affinity. Following impurity precipitation pre-treatment, lithium-rich solutions undergo column percolation where lithium ions are selectively adsorbed and subsequently stripped with dilute HCl. The adsorbent regenerates through simple water washing, enabling continuous operation with minimal secondary waste generation.
Process intensification through vacuum and controlled atmosphere processing is demonstrated in the vacuum reduction-roasting followed by water-only leaching system. Spent cathode powder pressed with carbon reductant undergoes sequential roasting at 350-450°C and 750-950°C under deep vacuum. This staged treatment reduces lithium salts to highly soluble Li₂O/LiOH while preventing violent gas evolution. Subsequent water leaching extracts 91% of lithium without co-dissolving valuable transition metals, with negative-pressure evaporation crystallizing high-purity LiOH while minimizing CO₂ uptake.
The solvothermal in-situ reduction mechanism represents a solution-phase alternative to high-temperature processing. Cathode or anode powders dispersed in recyclable organic solvents undergo chemical reduction at solvothermal temperatures, enabling metallic particle filtration and lithium salt crystallization through simple distillation. This approach avoids 1000-1600°C furnaces while suppressing HF formation and accommodating mixed chemistries without pre-sorting.
8. Chemistry-Specific Processing: LFP-Focused Systems
The growing market penetration of lithium iron phosphate (LFP) batteries has created demand for specialized processing routes that address the unique challenges posed by high iron-phosphorus content and absence of valuable transition metals. These systems optimize economics by targeting the specific chemistry and value proposition of LFP materials.
The selective ferrous-phosphate precipitation route begins with size reduction under immersion liquid to create pumpable slurries while eliminating thermal runaway risks. Alkaline pH adjustment (8-11) followed by ferrous sulfate dosing co-precipitates Fe and P as ferrous phosphate, removing ~90% of mass while leaving lithium-enriched liquor. The precipitated ferrous phosphate provides a secondary revenue stream as fertilizer precursor, while simplified lithium purification reduces both capital and operating costs compared to conventional NMC-oriented flowsheets.
An alternative approach utilizing the two-stage HCl/NaClO₃ flowsheet achieves >99.9% lithium dissolution while generating concentrated LiCl liquor (≥15 g Li L⁻¹) that minimizes downstream precipitant demand. The residual FePO₄-rich solid undergoes controlled redissolution and re-precipitation in stoichiometric Fe:P = 1:1 ratio, followed by counter-current washing to achieve battery-grade purity. This closed-loop system reduces wastewater by ~75% and caustic consumption by 274 kg t⁻¹ LFP while delivering 94% FePO₄ recovery.
For applications requiring high-purity lithium hydroxide, the electrodialytic LiOH production scheme operates at <70°C using dilute acid leaching with stoichiometric H₂O₂ for Fe²⁺ oxidation. Bipolar-membrane electrodialysis directly generates battery-grade LiOH while recycling acids, eliminating caustic reagent addition and chlorine gas evolution associated with conventional processing.
9. Integrated Closed-Loop Systems
The ultimate goal of sustainable lithium recovery lies in closed-loop systems that integrate extraction, purification, and precursor manufacture into seamless operations. These systems eliminate intermediate processing steps while ensuring that recovered materials meet specifications for direct reuse in battery manufacturing.
The direct Li₃PO₄ co-precipitation route exemplifies this integration by combining lithium extraction with phosphate synthesis and cathode precursor manufacture. Lithium leached as Li₂SO₄ undergoes direct Li₃PO₄ precipitation, bypassing evaporation and carbonate formation. Simultaneous Fe/Mn phosphate generation or stoichiometric adjustment in the same liquor enables simple milling plus 550-750°C calcination to yield battery-grade LiMPO₄ powder. This approach eliminates expensive Li₂CO₃ intermediate production while reducing both capital and operating costs.
Complementing materials recovery, the zwitterionic SEI rejuvenation strategy extends cell life through electrolyte additives that selectively dissolve Li-bearing SEI compounds. Phosphonium- or ammonium-carboxylate zwitterions liberate trapped Li⁺ ions for re-entry into charge-discharge cycles, chemically restoring capacity without cell disassembly. This approach postpones recycling requirements while ensuring higher lithium accessibility when processing eventually occurs.
10. Digital Integration and Process Control
The scaling of lithium recovery operations requires sophisticated digital platforms that can manage complex logistics, authenticate battery condition, and optimize processing decisions across diverse feed streams. These systems address the fragmentation and information asymmetries that currently limit recycling efficiency.
The battery degradation authentication device and mark mechanism provides tamper-proof battery health documentation through cloud-linked authentication units that issue one-time QR codes or digital tokens. Buyers access server-stored degradation metrics extracted from ECU logs, eliminating subjective discounting and standardizing data sharing across chemistries. This authenticated data stream enables accurate valuation and appropriate processing route selection.
Building on authenticated data, the multi-server remanufacturing support architecture orchestrates the complete second-life supply chain from identification of suitable packs to assembly of graded modules. Integrated database systems align diagnostic data with performance targets, generate assembly plans, and convert plans into personalized take-back offers. This automation overcomes manual program fragmentation while guaranteeing traceable provenance and enabling alternative specification proposals when inventory constraints arise.
11. Future-Oriented Technologies and Complementary Innovations
The continued evolution of lithium recovery technologies reflects both advancing technical capabilities and changing economic drivers. These emerging approaches address limitations of current methods while preparing for future battery chemistries and circular economy requirements.
The spatially segregated first-ion electrolyte architecture addresses lithium inventory preservation through interface chemistry redesign. Deliberate separation of lithium-conducting active material particles from solid-electrolyte particles carrying different mobile ions (K⁺, Mg²⁺, Al³⁺) enables preferential solvent binding by non-lithium ions. This configuration frees Li⁺ for efficient desolvation and lattice insertion with reduced polarization, extending lithium inventory through decreased interfacial degradation.
Operational approaches to lithium conservation include the zero-volt shunt rejuvenation strategy that redistributes lithium through controlled deep discharge cycles. Pairing lithium-titanate anodes with aluminum current collectors and switchable low-ohmic shunts enables pack collapse to ≤0.1 V for extended periods. This benign potential range redistributes lithium uniformly through electrodes, reversing apparent irreversible losses while widening usable SOC windows.
For high-capacity silicon anodes, the iron-free Ni-Cu pre-lithiation agent addresses the lithium consumption challenge through engineered LiₓNiₐCu₁₋ₐ₋ᵦMᵦO₂ particles with tailored surface area and size ratios. Formation-stage lithium release offsets SEI growth without introducing Fe ions that compromise separator integrity, enabling sustained capacity retention over thousands of expansion-contraction cycles.
12. Complementary Resource Recovery Technologies
The integration of recycled lithium supply with primary resource development requires technologies that can efficiently process ultra-dilute streams and variable feed compositions. These complementary approaches ensure supply security while maintaining economic viability across diverse resource types.
The MCDI-sulfate hybrid concentration train addresses ultra-dilute resources through membrane capacitive de-ionization followed by insoluble compound precipitation and hydrothermal conversion. Initial 1.5-5× electro-sorption concentration enables subsequent dense Li₂SO₄ liquor generation with mild alkaline polishing to battery-grade carbonate or hydroxide. This low-voltage, moderate-temperature approach accommodates both virgin brines and recycled process liquors while minimizing thermal duty and reagent consumption.
These technological developments collectively demonstrate the evolution from simple acid leaching toward integrated, selective, and environmentally conscious lithium recovery systems. The convergence of advanced materials, process intensification, digital integration, and circular economy principles is creating new possibilities for sustainable lithium supply that can meet growing demand while minimizing environmental impact and resource waste.
Get Full Report
Access our comprehensive collection of 147 documents related to this technology
Identify Key Areas of Innovation in 2025
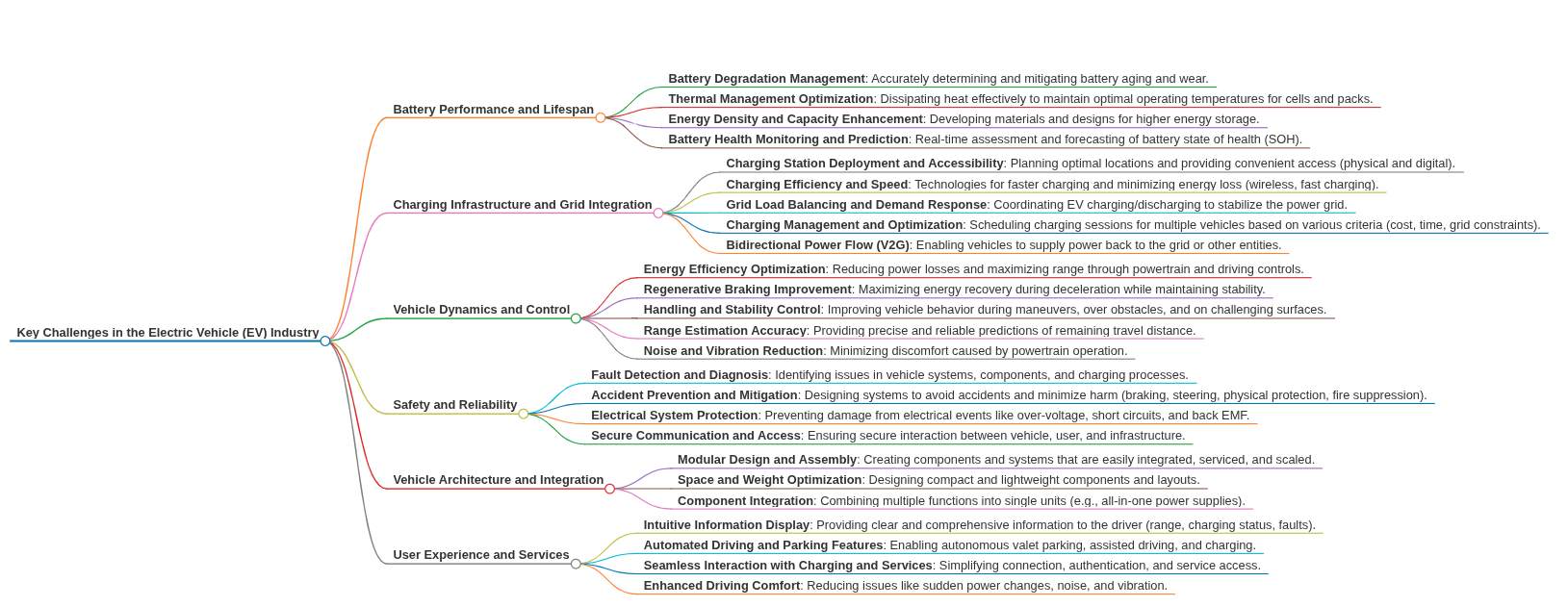