Hyundai's Innovation in EV Battery Management Systems
Modern electric vehicle battery packs operate across voltage ranges from 12V auxiliary systems to 800V traction systems, with cell temperatures fluctuating between -20°C and 60°C during normal operation. Hyundai's battery management systems must maintain safe operation across these ranges while optimizing charging efficiency, thermal management, and power delivery to vehicle systems.
The core engineering challenge lies in balancing the competing demands of battery longevity, charging speed, and system reliability while managing multiple voltage domains and thermal conditions.
This page brings together solutions from recent research—including multi-voltage domain management architectures, predictive thermal control systems, sensor redundancy implementations, and integrated cooling control strategies. These and other approaches demonstrate how Hyundai addresses battery management challenges in production vehicles while maintaining safety and reliability.
1. Battery Pack System with Relays, Converter, and Energy Storage Device for Voltage Regulation and Charge Balancing
HYUNDAI MOTOR CO, KIA CORP, 2024
A system for a battery pack in an electric vehicle to improve reliability and efficiency by preventing voltage spikes and balancing charge levels between high-voltage and low-voltage battery modules. It uses relays, a converter, and an energy storage device. The relays connect the high-voltage and low-voltage modules to the motor and low-voltage electronics. The converter converts voltage between the modules. The energy storage device connects to the converter output. This prevents insulation breakdown when relays close, balances charge levels, and allows operation during converter failures. A battery management system controls the relays based on vehicle state.
2. Fuel Cell Power Control System with High Side Voltage Regulation and Reverse Voltage Protection
HYUNDAI MOTOR CO, KIA CORP, 2024
A fuel cell power control system that maintains the voltage of the high side of a DC/DC converter feeding a load unit within a safe range. The system uses a controller to monitor the voltages of the high side, load unit, and battery. If the high side voltage gets too high, the controller reduces power input to the load unit or increases output from the load unit to lower the high side voltage. This prevents excessive voltages that could damage the DC/DC converter. The controller also monitors for reversed voltage conditions and bypasses the DC/DC converter to prevent damage.
3. Coolant Circulation System with Integrated Heat Exchanger and Valve-Controlled Flow for Electric Vehicle Battery Temperature Management
HYUNDAI MOTOR CO, KIA CORP, 2024
Coolant circulation system for electric vehicles to improve battery charging efficiency by managing battery temperatures. It connects to the vehicle's battery and an external heat exchanger. Coolant from the battery circulates through an internal heating core. Refrigerant circulates through an external cooling core. Valves control flow between the battery, heating core, cooling core, and heat exchanger. A controller adjusts valves based on battery temperature requirements. This allows heating/cooling the battery coolant based on environment conditions during charging.
4. Power Flow Management System with State-Dependent Control of Fuel Cell-Battery Interface During Startup
HYUNDAI MOBIS CO LTD, 2024
Managing power flow between a fuel cell system and the vehicle's battery during startup to prevent unnecessary power movement. The power conversion device, which converts high voltage from the fuel cell to low voltage for the battery, and the cooling device are controlled based on the low voltage battery's state of charge. This prevents overcharging or undercharging the low voltage battery during startup. The fuel cell can still be started without the low voltage battery being charged. The cooling device is driven first to ensure the converter is cooled before charging.
5. Electric Vehicle Charging System with Dual Battery Selective Charging and Switching Configuration
HYUNDAI MOTOR CO, KIA MOTORS CORP, 2024
Charging system for electric vehicles with dual batteries that allows selective charging of each battery based on the external charger capacity. The system has three switching elements: one between the two batteries, and one for each battery to connect/disconnect from external charger. A controller identifies charger capacity and switches to charge either battery individually, both simultaneously, or both as a single battery. This allows optimized charging based on charger capability instead of boosting one battery inside the vehicle.
6. Battery Management System with Dual-Channel Voltage Measurement for Reverse Voltage Protection
HYUNDAI MOBIS CO LTD, 2024
Battery management system and method to measure cell voltages in a battery pack while preventing damage to the voltage monitoring circuit due to reverse voltages on the busbar. The method involves using a single channel of the monitoring IC to simultaneously measure cell and busbar voltages. It also uses an additional channel to measure reverse voltage on the busbar. The cell voltage is then calculated using the normal cell voltage measurement and the reverse busbar voltage. This allows using all channels of the monitoring IC for cell voltages while still detecting reverse voltages on the busbar.
7. Battery Cooling System with Selective Radiator and Chiller Coolant Control
HYUNDAI MOTOR CO, KIA CORP, 2023
Battery cooling system control for electric vehicles that efficiently manages battery temperature. The method involves selectively using a radiator coolant or an air conditioning chiller coolant to cool the battery based on its temperature. If the battery is above a target temperature, the AC chiller is used. If below, the radiator coolant is used. This prevents unnecessary AC usage and maximizes cooling efficiency for optimal battery performance.
8. Battery Management System with Sensor Failure Temperature Estimation Using Historical Operational Data
HYUNDAI MOTOR CO, KIA MOTORS CORP, 2023
Battery management system for vehicles that estimates temperature of failed sensors using accumulated battery operation data to prevent accelerated battery deterioration. If a temperature sensor fails, the system estimates the temperature at that location based on historical differences between highest and lowest temperatures, and the behavior of other sensors. This estimated temperature is then used to manage battery charging/discharging instead of disabling it completely when a sensor fails.
9. Battery Temperature Control System with State of Charge-Dependent Optimal Charging Temperature Determination
HYUNDAI MOTOR CO, KIA CORP, 2023
Battery temperature control for electric vehicles that improves charging efficiency by determining the optimal temperature to charge the battery based on the state of charge (SOC) when charging begins. The method involves determining the charging start time based on driving patterns and environment, calculating the battery's temperature change leading up to charging, and then determining the time to start temperature control to reach the optimal charging temperature. This avoids unnecessary heating/cooling when the battery is already at the optimal temperature.
10. Integrated Battery Management System with Unified Communication Protocol for Low and High Voltage Monitoring
HYUNDAI MOBIS CO LTD, 2023
Battery management system that integrates monitoring of both low voltage and high voltage batteries using a single communication protocol. The low voltage battery is monitored by a dedicated low voltage monitoring unit. The high voltage battery is monitored using a daisy-chained array of sensing ICs connected to the low voltage monitoring unit. The low voltage unit relays the high voltage monitoring results to the central control unit. This allows both battery types to be monitored and managed using a unified communication protocol.
11. All-Solid-State Battery State of Health Estimation via In-Cell Hydrogen Sulfide Detection
HYUNDAI MOTOR CO, KIA CORP, 2023
Estimating the state of health (SOH) of an all-solid-state battery by detecting hydrogen sulfide generation in the cells and using that as a factor. The method involves placing a hydrogen sulfide sensor in the battery to measure the amount or increase rate of hydrogen sulfide generated in each cell. By comparing the hydrogen sulfide data to pre-prepared information, the SOH of the battery can be estimated accurately regardless of charge level or temperature. This improves reliability compared to traditional SOH estimation methods that rely solely on capacity degradation.
12. Battery Management Semiconductor Device with Comparator-Based Leakage Current Detection
HYUNDAI MOBIS CO LTD, 2023
Battery Management System (BMS) semiconductor device with leakage current detection that uses a simple comparator instead of an ADC to detect leakage currents in battery cells. The BMS has upper and lower sensing terminals connected to the positive and negative cell terminals, respectively. A comparator compares the balancing terminal voltage to the lower sensing terminal voltage. An ADC senses the voltage difference between upper and lower sensing terminals. A threshold is set based on the ADC value. If the comparator output exceeds the threshold, it indicates a leakage current. This allows detecting leakage currents without needing separate ADCs on each sensing terminal.
13. Battery Cooling System with Selective Air Conditioning Integration and Temperature-Responsive Activation
HYUNDAI MOTOR CO, KIA MOTORS CORP, 2022
Battery cooling system for electric vehicles that prevents battery degradation when parked in hot weather. The system selectively connects the vehicle's air conditioning to the battery cooling apparatus. A battery management system measures battery temperature periodically. When the battery temperature exceeds a threshold, the controller activates the air conditioning and cooling apparatus to cool the battery. This prevents battery degradation when parked in hot conditions.
14. Battery Pack Monitoring System with Data Fusion from Cell and Module Sensors
HYUNDAI MOTOR CO, KIA MOTORS CORP, THE INDUSTRY & ACADEMIC COOPERATION IN CHUNGNAM NATIONAL UNIVERSITY, 2022
A vehicle with a battery pack containing multiple battery modules, each with multiple cells. The vehicle uses a reduced number of sensors to accurately monitor the state of the cells and pack. It does this by fusing data from a cell voltage sensor and a module voltage/current sensor to estimate cell charge levels. The fused data reduces error and allows accurate charge tracking with fewer sensors compared to measuring each cell individually. The fused data is used to correct cell charge estimates based on module and pack charge levels.
15. Battery Management System with Discharge Rate Adjustment Based on Cell Voltage Deviation and Degradation
HYUNDAI MOTOR CO, KIA MOTORS CORP, 2022
Battery management system for eco-friendly vehicles that adjusts the maximum discharge rate of a battery based on cell voltage deviation and battery degradation. The system uses a map to match power limits with voltage deviations. It identifies the max and min cell voltages, calculates the deviation, looks up the limit from the map, and sets the final limit considering weight. This prevents over-discharging below safe limits as cells degrade. The limit adjustment helps prolong battery life by preventing excessive discharge as cells age and voltage balance deteriorates.
16. Battery Management System with Auxiliary Charging and Active Warming for Low-Temperature Performance in Electric Vehicles
HYUNDAI MOTOR CO, KIA MOTORS CORP, 2022
System for managing batteries in electric vehicles to maintain optimal performance at low temperatures like winter. The system involves charging an auxiliary battery when conditions permit to prevent discharging it. It also actively warms the main battery when it falls below an optimal temperature range. This prevents the main battery output drop at low temperatures while conserving charge in the auxiliary battery.
17. Battery Management System with Periodic Controller Activation for Power-Off State Monitoring
HYUNDAI MOTOR CO, KIA MOTORS CORP, 2022
A battery management system for electric vehicles that enables efficient monitoring of the battery in a power-off state to prevent issues like battery combustion. The system involves waking up some controllers periodically in the power-off state to monitor the battery. When the vehicle turns off, a controller turns off the main relay disconnecting the battery from the vehicle system. It then monitors the battery for a set time using its own power. When the time elapses, another controller wakes up and continues monitoring. This allows monitoring the battery even when the vehicle is off without continuous power consumption. It also checks if the battery charge is sufficient, other battery is available, and communication is possible before starting monitoring.
18. Battery Management System with Off-State Battery Issue Detection and Alert Mechanism
HYUNDAI MOTOR CO, KIA MOTORS CORP, 2022
Battery management system for electric vehicles that can detect and alert battery issues even when the vehicle is powered off. The system calculates battery parameters and compares them to reference values to determine if the battery is abnormal. If an issue is found, it stores an error code, displays an alert on the cluster, wakes the AVN system, notifies an external server, and prevents starting the vehicle until resolved. This allows identifying and addressing battery problems even in the no-load state when the main relay is off and the vehicle is powered down.
19. Vehicle Battery Management System with Dual State of Charge Estimation and Error Mitigation Mechanism
HYUNDAI MOTOR CO, KIA MOTORS CORP, 2022
Vehicle with improved battery management for vehicles with lithium-ion batteries to efficiently manage the battery state of charge and extend battery life. The method involves calculating an estimated SoC based on current alone, then calculating an actual SoC using a battery model with voltage and current inputs. By comparing the estimated and actual SoCs, the method determines if an error exists. If so, it activates features like generator control and engine shutoff during stopping to mitigate the error and improve battery life.
20. Battery Temperature Increase Method Using Inverter and Motor with Phase Switching in Electric Vehicles
HYUNDAI MOTOR CO, KIA MOTORS CORP, 2022
A method to rapidly increase the temperature of a battery in an electric vehicle without adding extra heaters or dedicated circuits. The method involves using the existing inverter and motor to generate alternating current (AC) and supply it to the battery while suppressing motor torque. The key steps are: 1. Selecting two phases out of the three phases for the battery. 2. Controlling the switching devices of those two phases to have complementary states (one on, one off) at a fixed frequency. 3. Turning off the switching device for the third phase. This creates an AC voltage across the battery terminals without applying DC from the inverter. By alternating phases at a high frequency, the battery quickly heats up. Torque is minimized since current flows through only two phases.
Get Full Report
Access our comprehensive collection of 25 documents related to this technology
Identify Key Areas of Innovation in 2025
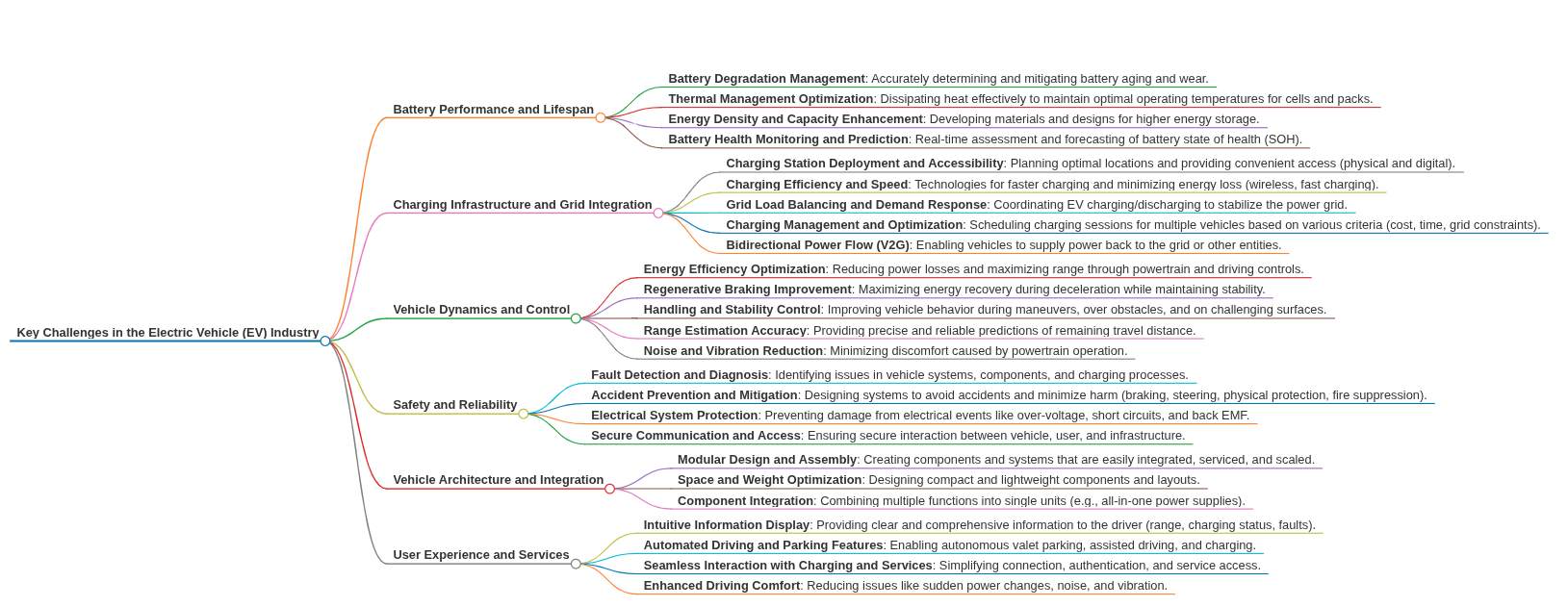