Heat Sinks for EV Battery Cooling
Electric vehicle battery packs generate substantial heat during operation, with cell temperatures routinely reaching 40-45°C during normal discharge cycles and exceeding 60°C under high-load conditions. Traditional passive cooling systems struggle to maintain consistent temperatures across cell arrays, leading to thermal gradients that can reduce pack longevity and performance.
The fundamental challenge lies in maximizing heat dissipation through passive mechanisms while maintaining uniform temperature distribution across densely packed cell arrays.
This page brings together solutions from recent research—including microfin heat sink designs, dual-layer thermal management systems, integrated housing-based heat dissipation, and direct cell-to-sink contact architectures. These and other approaches focus on achieving optimal thermal performance without the complexity and energy demands of active cooling systems.
1. Enhancing Hybrid Train Battery Performance using Liquid-Based Battery Thermal Management with Mini Channels Cooling System
mufti reza aulia putra, bhre wangsa lenggana, muhammad nizam - Akademia Baru Publishing, 2025
Electric vehicles (EV) are advancing rapidly, with increasing demand for enhanced technological support. One of the key challenges EVs is ensuring adequate power storage, a critical parameter being battery pack's ability to support high discharge rate. Achieving rate requires proper cell design and efficient heat management within pack. During discharge, generation becomes significant, necessitating an effective cooling system. Battery Thermal Management Systems (BTMS) employed regulate temperatures, optimal performance. Among various methods, liquid-based BTMS demonstrates superior performance compared phase-change materials (PCM) air cooling. However, weight liquid coolers, due volume coolant required, can add substantial battery, impacting overall vehicle efficiency. This paper investigates potential use mini channels integrated into plates applications. The study utilizes finite element method (FEM) simulate fluid flow processes in systems operating at C-rates. findings show that this novel effectively maintains temperatures below 40C, offering promising solution current limita... Read More
2. Optimization and Key Factor Analysis of Immersion Cooling Performance for 18650 Lithium-Ion Batteries in a Serpentine Channel Based on Response Surface Methodology
zhenxing li, z fu, ruoyu huang, 2025
Efficient thermal management of lithium-ion batteries is crucial for electric vehicle safety and performance. This study investigates immersion cooling in serpentine channels 18650 batteries, aiming to identify key factors affecting maximum battery temperature (Tmax) pump power (Pw). A Box-Behnken experimental design implemented with Computational Fluid Dynamics simulations analyze responses Tmax Pw. Five variables are defined: partition length (Lp), charging/discharging rate (Crate), coolant volumetric flow (V), inlet (Tin) ambient (Tamb). Statistical significance evaluated via Analysis Variance. The results show that: Tin dominated Tmax, followed by Crate, V, Lp. Significant interactions (VTin VTamb) observed. For Pw, V V extreme significance, while Lp effects were minor. Interaction LpV was significant but secondary. After optimization minimize Tave the optimal values Lp, Tin, Tamb determined be 89.5 mm, 1.08 C, 0.51 LPM, 20 C, 25.62C respectively. corresponding optimized are: = 22.87C, 21.67C, Pw 0.279 mW. Optimal requires prioritizing control suppression regulati... Read More
3. Battery Assembly with Expandable Insertion Members and Integrated Cooling System
SK ON CO LTD, 2025
Battery assembly with integrated cooling system to mitigate thermal runaway propagation and improve safety. The assembly has expandable insertion members between cells that absorb heat when filled with fluid. Temperature and gas sensors monitor cells. If temps exceed threshold or gas detected, a pump moves fluid into the insertion members to cool adjacent cells. This prevents thermal runaway spread. The insertion members also have insulation layers to minimize heat transfer between cells.
4. Novel hybrid vehicle battery cooling system: Integrating Peltier-based heat sinks for control of thermal management
h n sharma, gaurav saxena, ravindra randa - SAGE Publishing, 2025
This study presents an experimental investigation of a novel hybrid battery thermal management system (BTMS) that integrates solenoid-actuated Peltier-based heat sink with CuO/ethylene glycol (EG) nanofluid coolant loop. The delivers on-demand cooling through time-controlled thermoelectric operation, enhancing temperature regulation during surges. Experiments were conducted CuO nanoparticle concentrations ranging from 0.5% to 2.0% (vol.) and flow rates 1 5 LPM, at inlet 50C ambient 26C. Performance metrics such as drop, transfer rate, overall coefficient analyzed. Results showed maximum enhancement 40.63% (tube-side) 38.64% (air-side) CuO. Compared conventional liquid system, the setup demonstrated 7.01% higher rate improved variation control (up 28.53%). Life Cycle Cost (LCC) analysis demonstrates 25%30% reduction in long-term costs 36% life extension, supporting systems economic viability. scalable, energy-efficient BTMS offers promising solution for advanced electric vehicles requiring high-precision control.
5. Battery Module with Integrated Heat Sink Featuring Parallel Flow Path for Direct Cell Cooling
LG ENERGY SOLUTION LTD, 2025
Battery module with improved cooling performance for applications like electric vehicles. The module has a heat sink integrated into the lower frame to directly cool the battery cells. The heat sink has a flow path for refrigerant. The flow path has longer parallel paths between the cells versus perpendicular paths. This configuration allows direct cooling of the cells with better cooling efficiency compared to indirect cooling through a separate heat sink. The integrated heat sink also improves space utilization compared to a separate heat sink.
6. Optimization of Thermoelectric Module Configuration and Cooling Performance in Thermoelectric-Based Battery Thermal Management System
senbo fu, hongmao qin - Multidisciplinary Digital Publishing Institute, 2025
A good thermal management system for batteries is the key to solving potential risks such as runaway of and ensuring that work within appropriate temperature range. To resolve conflict between cooling efficiency input power in existing battery systems based on thermoelectric cooling, this paper proposes an optimization method layout devices. Using a multi-physics coupling numerical model, study focuses analyzing impact quantity devices current temperature. The optimal arrangement structure response characteristics are investigated from four aspects: maximum temperature, difference, difference uniformity, coefficient. research results show optimized capable reducing both pack, reduces consumption by 19.8%, effectively enhancing energy system.
7. Thermal Management of EV Battery Pack: Evaluating the Cooling Strategy with Air Convection
shanaya thadani, puneet rana, anup sharma, 2025
The study presents a thorough theoretical analysis of the thermal distribution in electric vehicle battery packs under different heating loads. A finite-element heat transfer model is developed COMSOL to simulate pack with 15 cylindrical lithium-ion cells integrated liquid-cooled support plates. C-rates, which define generation during charge-discharge cycle, are included model-in real case scenarios wherein 10 Ah generates outputs about 10.5 W, 25 and 54 W at 3C, 5C, 8C charge rates, respectively. Transient simulations display how temperature profiles evolve time reach quasi-steady states by input counterbalanced dissipation through convection. It also examines air convection performance as technique for cooling, revealing that while it cheaper simpler implement, less effective than liquid cooling. Other alternatives this regard, such use graphite foam, have been investigated concerning their ability achieve higher coefficients, thus enhancing load management greater rates charge. results illuminate importance optimized systems avert runaway EV ensure safety, efficiency, longevity. w... Read More
8. Numerical and Thermal Analysis of Battery Pack
atharva yewale, abhishek sherkhane - International Journal for Multidisciplinary Research (IJFMR), 2025
Research and development in batteries has resulted a boom the production of electric vehicles. Considered environmentally friendly, these vehicles are on rise due to developments battery chemistry. But clear problem is associated with batteries: temperature. These tend get hot as more current gets extracted from them. Ongoing research made it possible decrease temperature using various methods. so many methods available only one/two select, becomes difficult choose one. Using strong method can take energy while docile one will not do its job properly. Our project based selecting for an vehicle, designing pack, calculating heat load suitable cooling validating through finite element analysis. This help understand how selected.
9. Battery Module with Upper and Lower Frames Incorporating Heat Transfer Members and Bending Parts for Enhanced Cooling and Structural Stability
HYUNDAI MOBIS CO LTD, HYUNDAI MOTOR CO, KIA CORP, 2025
Battery module design for electric vehicles that improves cooling and stability of the battery cells. The module has upper and lower frames around the battery cells, with heat transfer members that connect to cooling channels. The frames support the cells to prevent expansion damage. The upper and lower frames have bending parts that join the side panels. The lower frame also has a flange around the cover plates. This provides a sealed, rigid structure with cooled upper and lower cell areas. The frames and heat transfer members enhance cooling by direct contact with the channels. It improves stability by supporting cell expansion and prevents internal fires spreading between modules.
10. The Effect of Cross-Sectional Shape on the Thermo-Hydraulic Performance of Microchannel Heat Sinks
yiuwing mai - EWA Publishing, 2025
Microchannel heat sinks are widely used in thermal management systems due to their compact design and efficient transfer. To further enhance performance, this study uses numerical simulations explore the transfer characteristics of rectangular, triangular, trapezoidal, circular microchannels while maintaining equal cross-sectional areas. At Re = 900, triangular microchannel demonstrates optimal performance (HTP) but weakest hydraulic with a 5.56% reduction resistance 54.45% increase pumping power compared rectangular microchannel. The exhibits worst HTP best 12.78% 32.04% power. trapezoidal similar those one. This paper provides theoretical basis for optimizing sink designs by evaluating different shapes. findings offer insights into trade-offs between efficiency helping guide future improvements applications.
11. Battery Pack with Integrated Mechanical and Electrical Fixing and Built-In Heatsink
LG ENERGY SOLUTION LTD, 2025
Battery pack design for electric vehicles that simplifies assembly, reduces costs, improves space utilization, and enables higher energy density compared to conventional packs. The pack has integrated mechanical and electrical fixing for the battery modules. The pack case has a tray to support the modules and a cover that attaches to the tray. The cover has electrical connections built into it that connect to the module terminals. This eliminates separate bolting and wiring steps for the modules inside the pack. The cover also has an integrated heatsink. This reduces parts count, simplifies assembly, improves space utilization, and allows higher module packing density compared to separate heatsinks and wiring.
12. Battery Pack with Integrated Frame-Embedded Refrigerant Piping and Fastening System
LE ENERGY SOULUTION LTD, 2025
Battery pack with improved cooling and safety by integrating the refrigerant piping and fastening into the pack frame, preventing refrigerant leakage and minimizing damage if leakage occurs. The pack has multiple battery modules stacked in a frame with a heat sink below. The pack frame encloses the modules and has a central refrigerant pipe. A dedicated bolt connects the module frame, heat sink, and pack frame. This bolt contains a secondary connection pipe that links the pack's refrigerant pipe to the heat sink. This integrated cooling and fastening design prevents refrigerant leaks from spreading if they occur.
13. Battery Array with Integrated Roll-Bonded Cold Plates Formed by Bonded Metal Sheets
FORD GLOBAL TECHNOLOGIES LLC, 2025
Battery array design for electric vehicle packs that integrates roll-bonded cold plates into the battery array itself rather than using separate external cold plates. The roll-bonded cold plates are formed by joining two metal sheets along a bonded seam. This allows the cold plates to be integrated into the battery array support structure to directly manage the thermal performance of the battery cells. It reduces cost and complexity compared to separate cold plates. The roll-bonded plates can form one or more sides of the array structure.
14. Battery Heat Management System with Spring-Loaded Contact Elements for Direct Thermal Conduction
MERCEDES-BENZ GROUP AG, 2025
Heat management for electric vehicle batteries that improves cooling without the use of heavy, expensive heat conduction compounds. The solution involves using spring-loaded contact elements between the battery cells and a heat dissipating element. The springs apply a defined force to maintain contact between the cells and the heat conduction element. This allows direct thermal conduction to transfer heat from the cells to the cooling system without needing a separate compound.
15. Numerical Study on the Influence of Elliptical Ribs on the Cold‐Plate Performance of Electric Vehicle Power Batteries
shuai liu, quan xu, hekun jia - Wiley, 2025
In this article, a cold plate with elliptical ribs in the flow channel is designed. The influence of shape on maximum temperature and difference battery, as well fluid rate, explored. Additionally, effects varying number ribs, minor axis ellipse, major ellipse battery's temperature, difference, pressure loss plate, rate are analyzed. cooling performance evaluated using heat transfer coefficient. results show that dissipation better when contains under premise acceptable loss, reduced by 11.53%. containing has highest lowest cell temperature. Excessive larger higher mass which causes vortexing at end ribs. parameter greatest effect an increase 64.50%. change only 12.39% changed.
16. Advances in the Battery Thermal Management Systems of Electric Vehicles for Thermal Runaway Prevention and Suppression
le duc tai, mooyeon lee - Multidisciplinary Digital Publishing Institute, 2025
In response to the global imperative reduce greenhouse gas emissions and fossil fuel dependency, electric vehicles (EVs) have emerged as a sustainable transportation alternative, primarily utilizing lithium-ion batteries (LIBs) due their high energy density efficiency. However, LIBs are highly sensitive temperature fluctuations, significantly affecting performance, lifespan, safety. One of most critical threats safe operation is thermal runaway (TR), an uncontrollable exothermic process that can lead catastrophic failure under abusive conditions. Moreover, propagation (TRP) rapidly spread failures across battery cells, intensifying safety threats. To address these challenges, developing advanced management systems (BTMS) essential ensure optimal control suppress TR TRP within LIB modules. This review systematically evaluates cooling strategies, including indirect liquid cooling, water mist immersion phase change material (PCM) hybrid based on latest studies published between 2020 2025. The highlights mechanisms, effectiveness, practical considerations for preventing initiation suppre... Read More
17. Battery Module and Pack with Integrated Heat Sink and Interconnect Bus Bars
SK ON CO LTD, 2025
Battery module and pack design with integrated heat sink for better cooling efficiency and uniform cooling of multiple modules. The battery module has a housing that encloses the stacked battery cells and also integrates a heat sink with cooling passages. This allows direct contact between the cells and heat sink for enhanced cooling. In a pack with multiple modules, the integrated heat sink provides uniform cooling compared to separate heat sinks. The pack also has interconnect bus bars between adjacent modules to simplify wiring.
18. Battery Module Frame with Central Cooling Plate and Perpendicular Exterior Plates for Cylindrical Cell Thermal Management and Retention
LG ENERGY SOLUTION LTD, 2025
A battery module frame for compactly packaging multiple cylindrical battery cells with improved thermal management and simplified cell retention compared to prior art. The frame has a central cooling plate with manifolds and channels to circulate cooling fluid. Exterior plates extend perpendicularly from the manifolds. The channels between the plates have thermally conductive layers to transfer heat between the plates and the cells. This allows efficient cooling and retention without complex mechanisms or fasteners.
19. A Thermal Runaway Protection Strategy for Prismatic Lithium-Ion Battery Modules Based on Phase Change and Thermal Decomposition of Sodium Acetate Trihydrate
tianqi yang, hanwei xu, changjun xie - Multidisciplinary Digital Publishing Institute, 2025
With the rapid development of battery energy storage technology, issue thermal runaway (TR) in lithium-ion batteries has become a key challenge restricting their safe application. This study presents an innovative protection strategy that integrates liquid cooling with sodium acetate trihydrate (SAT)-based composite phase change materials (CPCM) to mitigate TR and its propagation prismatic modules. Through numerical simulation, this systematically investigates mechanism optimization pathways for The results indicate pure SAT exhibits poor latent heat performance due low conductivity. In contrast, incorporation expanded graphite (EG) significantly enhances conductivity improves overall performance. Compared traditional paraffin-expanded (PA-EG), SAT-EG, 4.8 times higher than PA-EG, demonstrates more six effectiveness delaying (TRP). When combined cooling, effect is further enhanced, will not be triggered when initial abnormal generation rate relatively low. Even if experiences TR, prevented thickness SAT-EG exceeds 12 mm. Ambient temperature influences both peak timing occurrence modu... Read More
20. Modular Battery Pack with Parallel-Surfaced Cells and Integrated Cooling Plates Featuring Thermally Conductive Beads
RASCO D.O.O, 2025
Energy-dense modular battery pack design with integrated cooling system for electric vehicles. The battery pack has an array of parallel-surfaced battery cells in a non-conductive shell. Thermally conductive material like beads are placed between the cells and top/bottom contacts. Cooling plates with fluid channels compress the beads and surround the cells. The plates have inlets/outlets and channels arranged to distribute heat across the pack. This provides efficient cooling for high-density, compact battery packs that can be customized for various EV applications.
Get Full Report
Access our comprehensive collection of 150 documents related to this technology
Identify Key Areas of Innovation in 2025
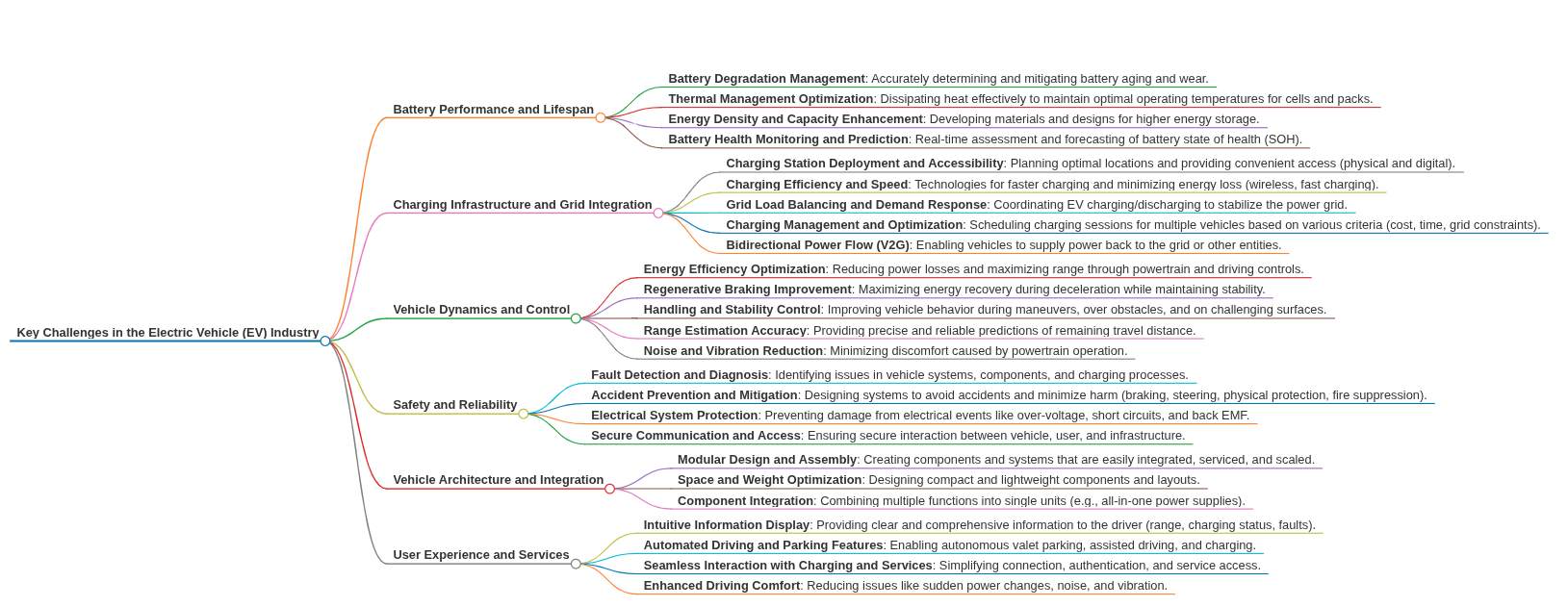