Thermoelectric Cooling for EV Battery Thermal Management
Electric vehicle battery packs generate substantial thermal loads, with cells routinely experiencing temperature gradients of 5-10°C during operation and up to 30°C during fast charging sessions. These thermal conditions directly impact cell electrochemistry—accelerating degradation mechanisms when temperatures exceed 45°C and reducing power availability below 15°C. Conventional liquid cooling systems struggle to maintain uniform temperatures across large battery packs and consume significant parasitic power, particularly in extreme ambient conditions.
The fundamental challenge lies in designing thermal management systems that provide precise temperature control across varied operating conditions while minimizing energy consumption and system complexity.
This page brings together solutions from recent research—including dual-stage thermal management architectures that combine thermoelectric and liquid cooling, phase change material integration for thermal buffering, real-time temperature monitoring systems with adaptive control, and multi-layer thermal insulation structures. These and other approaches offer practical pathways to extend battery lifespan, enable faster charging rates, and improve overall energy efficiency in electric vehicle applications.
1. Battery Cooling System with Real-Time Temperature Monitoring and Control for Electric Vehicles
BOSCH GMBH ROBERT, 2025
A system for optimizing battery cooling in electric vehicles that enables rapid charging while maintaining battery health. The system employs advanced temperature monitoring and control to rapidly cool the battery during charging, eliminating the need for prolonged charging times. The system integrates with the vehicle's battery management system to monitor temperature and adjust cooling parameters in real-time. This enables rapid charging while maintaining battery health, reducing waiting times and enabling more efficient charging operations.
2. Electric Vehicle Battery Thermal Management System with Integrated Thermoelectric and Liquid Cooling Modules
VISHNU BHUVANACHANDRAN RAJESWARI, 2024
Dual-stage thermal management system for electric vehicle batteries that integrates thermoelectric cooling modules with liquid cooling to enhance thermal performance and lifespan. The system comprises a thermoelectric Peltier cooler module positioned strategically over the liquid cooling circuit, with thermal pads separating the battery pack from electrical contact. This configuration enables precise temperature control while preventing water droplet formation on the battery surface. The dual-stage approach optimizes energy efficiency and reliability by addressing the limitations of traditional single-stage cooling systems.
3. Cooling Device with Integrated Thermally Conductive Plate and Filling Layer for Energy Storage Thermal Interface
DRAEXLMAIER LISA GMBH, 2024
Cooling device for energy storage devices, particularly motor vehicles, that enables efficient thermal management through a novel thermal interface system. The cooling device comprises a thermally conductive plate and a thermally conductive filling layer that are integrated into the cooling plate structure. The filling layer fills the gap between the cooling plate and the energy storage device, providing a continuous thermal interface without requiring mechanical compression. This design enables the energy storage device to maintain thermal contact with the cooling plate while minimizing the forces required for assembly and disassembly.
4. Battery Module with Thermal Conduit and Thermoelectric Cooler for Heat Dissipation
GEORGIA TECH RES INST, 2024
Battery system for managing thermal energy in batteries, particularly for grid-connected energy storage systems. The system comprises a battery module comprising multiple battery cells, a thermal conduit connecting the cells to a thermoelectric cooler, and a thermoelectric cooler itself. The thermal conduit enables controlled thermal transfer from the battery cells to the cooler, while the thermoelectric cooler efficiently dissipates generated heat. The system achieves optimal temperature management through the thermal conduit and cooler combination, enabling long-duration operation without thermal runaway risks.
5. Energy Storage System with Unified Peltier Module and Fan-Based Temperature Control
LG ELECTRONICS INC, 2024
Energy storage system with integrated temperature management that controls both battery temperature and system-wide temperature using a single cooling system. The system employs a Peltier module and a fan to manage temperature across the battery pack, with the fan controlling the flow of coolant to the Peltier modules. The system achieves temperature stability through both cooling and heating modes, enabling precise control of both battery temperature and system-wide temperature. The integrated cooling system provides efficient heat transfer between the battery modules while maintaining system-wide temperature stability.
6. Energy Storage System with Multi-Stage Cooling Using Peltier Elements, Heat Sinks, and Water Blocks
LG ELECTRONICS INC, 2024
Energy storage system with integrated temperature management for battery packs. The system employs a multi-stage cooling system that utilizes a network of Peltier elements, heat sinks, and water blocks to maintain optimal battery temperatures. The system includes a pump, coolant circulation path, and heat exchanger, with temperature sensors monitoring the coolant temperature. The system can operate in multiple modes, including preheating and cooling modes, and features a bypass system to manage heat dissipation. The system integrates with the power converter and battery management system to optimize energy storage and conversion performance.
7. Battery Pack Cooling System with Thermoelectric Device-Integrated Coolant Loop for Enhanced Thermal Management
Ford Global Technologies, Inc., FORD GLOBAL TECHNOLOGIES LLC, 2022
Battery thermal management system for electric vehicles that uses thermoelectric devices to enhance cooling of the battery pack during high temperature events like fast charging. The system has a coolant loop with a thermoelectric device that can be activated to cool the battery pack further when needed. The device has a junction between hot and cold sides. Current through the junction cools the cold side exposed to the coolant loop, enhancing battery pack cooling. The hot side is cooled by airflow. This provides additional cooling during high heat events like fast charging.
8. Battery Pack with Thermoelectric and Phase Change Material-Based Thermal Management System
重庆大学, CHONGQING UNIVERSITY, 2022
Battery pack and thermal management method using Peltier effect and phase change materials for enhanced cooling and thermal management. The method employs a thermoelectric refrigerator and heat pipe cooling system to achieve efficient temperature regulation. The system comprises a battery module, a thermoelectric refrigerator, and a heat pipe cooling device. The thermoelectric refrigerator maintains a temperature close to the battery's operating temperature, while the heat pipe cooling device absorbs and releases heat through phase change materials. This phase change material-based cooling mechanism enables precise temperature control and efficient heat transfer, particularly in high-temperature environments.
9. Battery Module with Uniform Thermal Management via Novel Thermal Interface Material Design
HUNAN DIANJIANGJUN NEW ENERGY RESOURCES CO LTD, 2021
A constant-temperature high-power battery module that maintains optimal performance across a wide operating temperature range. The module incorporates a novel thermal management system that enables consistent cell temperature across all cells, regardless of ambient temperature variations. This is achieved through a unique thermal interface material (TIM) design that distributes heat evenly throughout the module, while maintaining cell temperature stability. The module's thermal management system ensures optimal performance in both high-temperature environments and low-temperature environments, enabling reliable operation across a broad temperature range.
10. Battery Thermal Management System with Integrated Thermoelectric and Liquid Cooling Mechanisms
Jiangsu University, JIANGSU UNIVERSITY, JIANGSU JIAHE THERMAL SYSTEM RADIATOR CO LTD, 2021
Battery thermal management device for electric vehicles that combines thermoelectric cooling with liquid cooling to address temperature extremes. The device employs thermoelectric cooling to rapidly cool the battery in high-temperature environments, while liquid cooling provides additional cooling through a temperature gradient. This dual-cooling approach enables both rapid battery temperature regulation and efficient cooling in low-temperature environments.
11. Integrated Cooling Circuit for Electric Vehicle Battery Temperature Regulation During High-Power Charging Cycles
VOLKSWAGEN AG, 2020
Temperature management system for electric vehicle batteries that enables controlled charging operation during high-power charging cycles. The system comprises a dedicated cooling circuit integrated into the vehicle's temperature management system, which operates in conjunction with the vehicle's internal cooling system during high-power charging. The cooling circuit provides enhanced cooling capacity during charging cycles, particularly when external charging sources are used. The system enables precise temperature management of the battery during charging operations, including both high-power charging and low-temperature charging phases.
12. Thermoelectric-Liquid Hybrid Cooling Device with Flow-Dependent Voltage Control for Battery Thermal Management
JIANGSU JIAHE THERMAL SYSTEM RADIATOR CO LTD, 2020
Thermoelectric cooling coupled liquid cooling battery thermal management device and voltage regulation strategy. The device integrates a thermoelectric cooling module with a liquid cooling module, where the thermoelectric module is connected to the battery and the thermoelectric module is cooled by the liquid cooling module. The thermoelectric module's differential voltage is controlled based on the flow of the liquid cooling module's coolant, with the thermoelectric module's temperature matching the liquid cooling module's temperature. This enables precise temperature regulation of both the battery and the cooling system.
13. Battery Module Thermal Management Component with Peltier-Integrated Heat Spreader and Finned Heat Dissipation Assembly
WEBASTO SHANGHAI LTD, 2020
Thermal management component for battery modules in electric vehicles that uses Peltier devices to cool/heat battery cells. The component has a heat spreader inside the module that contacts the cells, a fixed bottom plate against the module shell, fins fixed to the plate with a thermally conductive pad, and a Peltier device between the plate and fins. This allows active cooling/heating of the cells. The module has at least one of these assemblies symmetrically positioned between the module halves.
14. Lithium-Ion Battery Thermal Management System with Phase Change Material Heat Sink
ZHEJIANG HOZON NEW ENERGY AUTOMOBILE CO LTD, 2020
Thermal management system for lithium-ion batteries that utilizes phase change materials to regulate temperature. The system comprises a phase change material (PCM) heat sink surrounding the battery cell, with a temperature-dependent phase change phase that absorbs and stores heat during discharge and releases heat during charging. The PCM maintains a stable temperature range between 35°C and 45°C, where the battery operates optimally, thereby preventing thermal runaway and enabling reliable operation.
15. Battery Module with Phase-Change Energy Storage, Active Thermal Insulation, and Semiconductor Refrigeration for Low-Temperature Resistance
WANG JIANGUO, 2020
A low-temperature-resistant battery module that maintains optimal operating conditions for electric vehicle batteries in extreme cold environments. The module incorporates advanced thermal management solutions, including a phase-change energy storage component, active thermal insulation, and semiconductor refrigeration technology. The system enables controlled temperature operation of the battery pack, maximizing its performance and lifespan in winter conditions.
16. Integrated Cooling System with Curved Graphite Tape for Enhanced Thermal Transfer in High-Voltage Devices
DRAEXLMAIER LISA GMBH, 2019
A novel cooling system for high-voltage devices that eliminates the challenges of traditional thermal management solutions. The system integrates a heat sink with a heat source on a single component, featuring a thermally conductive graphite tape between them. The tape is designed with optimized thermal interface properties, enabling efficient heat dissipation while maintaining structural integrity. The graphite tape is arranged in a curved, over-bent configuration to provide optimal thermal transfer between the heat sink and the heat source, eliminating the need for separate thermal interfaces and enabling higher thermal performance compared to conventional busbar-based solutions.
17. Electric Vehicle Battery Temperature Management System with Advanced Thermal Architecture
HUATING POWER TECHNOLOGY CO LTD, 2019
Temperature management system for electric vehicle batteries to mitigate thermal stress. The system enables precise temperature control between the battery cell temperature and ambient temperature through advanced thermal management architecture. This approach ensures optimal battery performance while maintaining the required operating parameters for safe and efficient charging and discharging.
18. Battery Thermal Management System with Electric Heating Films and Phase Change Material Integration
BEIJING UNIVERSITY OF TECHNOLOGY, 2019
Integrated battery thermal management method for electric vehicles that provides efficient heating and cooling of battery packs in both low and high temperature environments. The method uses electric heating films attached to one side of the battery cells and spaced apart. The gaps between the films are filled with phase change materials like paraffin wax. In low temperatures, the heating films heat the batteries and the PCM absorbs excess heat. In high temperatures, the PCM releases latent heat to dissipate heat. This allows batteries to be maintained within a suitable temperature range for optimal performance and longevity.
19. Thermal Management System for Power Batteries with Integrated Active Cooling and Phase Change Material Heat Storage
BEIJING HUAHOU ENERGY TECH CO LTD, 2019
Active and passive thermal management system for power batteries that improves temperature control efficiency and reliability compared to traditional methods. The system combines active cooling like fans and refrigeration with passive phase change materials (PCMs) to maintain optimal battery temperatures. The battery pack has a metal plate attached to it, with a PCM-filled heat storage plate attached to the metal plate. Fans blow air through the PCM to cool it. A refrigeration device chills the air. Metal fins increase thermal conductivity. The PCM provides stable temperature buffering. A controller manages the active cooling and fan speeds based on battery temperature.
20. Battery Module with Integrated Structural Cooling System for Power Electronics and Busbar
NIO USA INC, 2019
Battery module design for electric vehicles that integrates cooling into the module structure itself. The module comprises a cooling system that thermally cools both the power electronics and the busbar. The cooling system is integrated into the module's structural components, with the power electronics mounted to a bottom portion and the busbar positioned between the top and bottom portions. This modular approach enables efficient cooling of both critical components while maintaining a single, enclosed enclosure.
Get Full Report
Access our comprehensive collection of 48 documents related to this technology
Identify Key Areas of Innovation in 2025
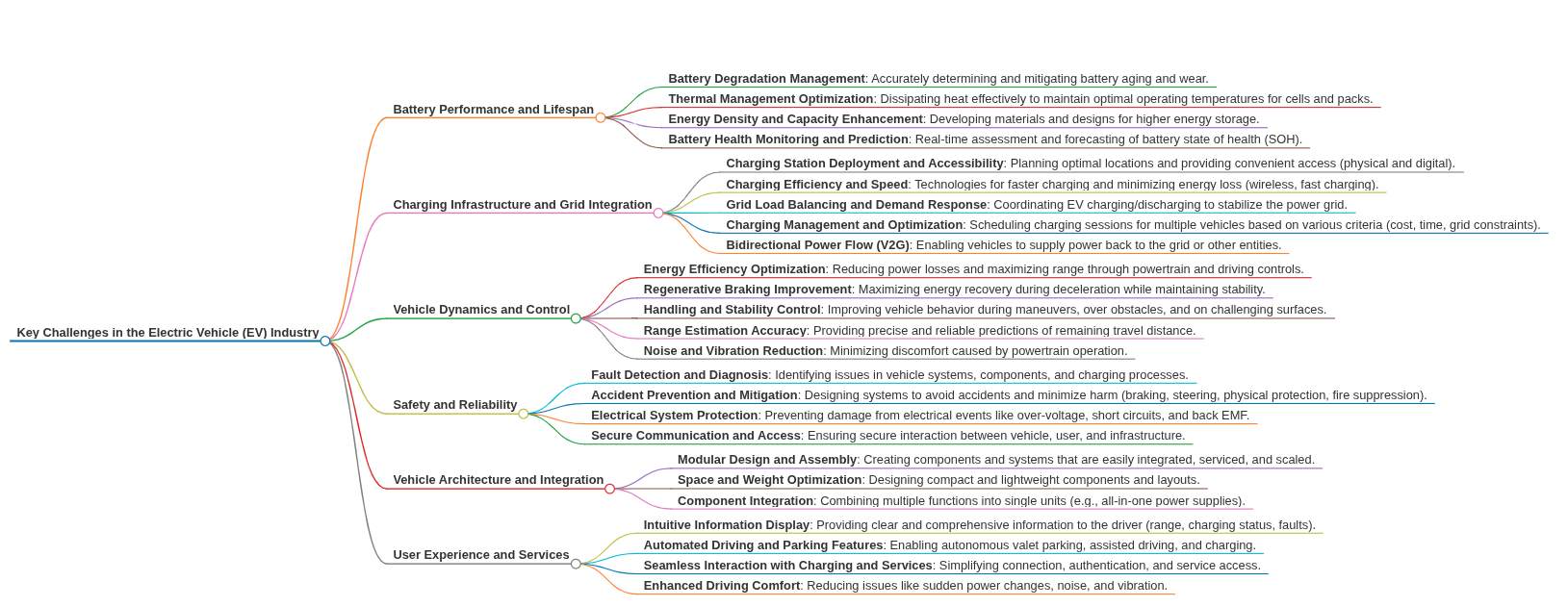