Tesla's Innovations in EV Battery Recycling
Tesla's battery recycling efforts face a significant technical challenge: processing thousands of tons of end-of-life EV batteries containing valuable but intimately mixed materials. Current cells contain approximately 8kg of lithium, 35kg of nickel, and 7kg of cobalt per vehicle, with these materials bound in complex chemical structures that resist simple mechanical separation.
The core challenge lies in developing recycling processes that can recover high-purity battery materials while minimizing energy consumption, chemical waste streams, and processing costs.
This page brings together solutions from recent research—including closed-loop electrolysis systems, selective leaching processes, and pyrometallurgical techniques with optimized slag chemistry. These and other approaches demonstrate how Tesla is working to create economically viable recycling pathways that can scale with growing EV battery waste volumes.
1. Process for Solid-State Recovery of Electrode Materials from Spent Lithium-Ion Batteries Using Sequential Reduction and Carbonylation
TESLA INC, 2024
Recovering valuable materials from spent lithium-ion batteries without generating large amounts of liquid effluent. The process involves discharging the batteries in water, separating the electrode materials, reducing them, carbonylating to isolate nickel, then decomposing to isolate cobalt. Lithium is further extracted from the residue. This allows recycling of the battery cathode materials into new batteries without the environmental impacts of acid leaching and solvent extraction.
2. Effluent-Free Process for Carbonylation-Based Recovery of Metals from Spent Lithium-Ion Battery Cathodes
TESLA INC, 2023
Effluent-free recycling of spent lithium-ion battery cathode materials to recover valuable elements like nickel, cobalt, and lithium for reuse in new batteries. The recycling process involves reducing the active material mixture, carbonylating it, and then decomposing the carbonylated material to separate out the metal products. This allows pure metal recovery without generating liquid waste. The reduced mixture is carbonylated with CO gas at low temperature and pressure, followed by decomposition to separate out the nickel and cobalt metals. The remaining carbonylation material is further decomposed to separate the lithium. The process avoids generating effluent compared to acid leaching methods.
3. Battery Scrap Processing with Sequential Selective Leaching and Metal Recovery Techniques
REDWOOD MAT INC, REDWOOD MATERIALS INC, 2024
Recovering valuable metals from battery manufacturing scrap materials and generating products important to battery manufacturing and recycling through a variety of processes including mechanical separation, acid leaching, precipitation, electrolysis, oxidation, precipitation, etc. The methods aim to recover battery metals like lithium, nickel, cobalt, and aluminum from battery scrap with improved byproducts and minimal waste streams compared to conventional methods. The approaches involve selective leaching of lithium from the battery scrap using sulfuric acid and peroxide to recover lithium, nickel, and cobalt into solution. The lithium is then separated from the other metals for recovery as lithium sulfate. This allows efficient and selective recovery of lithium, nickel, and cobalt from the battery scrap with minimized waste streams compared to conventional methods.
4. Electrolysis Cell System for Direct Splitting of Sodium and Lithium Sulfate Waste Streams with Membrane Separation
REDWOOD MATERIALS INC, 2024
Electrochemically splitting battery waste streams like sodium sulfate (Na2SO4) and lithium sulfate (Li2SO4) to produce sodium hydroxide (NaOH), lithium hydroxide (LiOH), and sulfuric acid (H2SO4) using closed-loop recycling. The waste streams are fed directly to electrolysis cells with membranes to split the cations and anions without purification. This allows converting battery waste to usable chemicals while avoiding downstream processing steps.
5. Lithium Concentration from Metallurgical Fumes via Slag Formation and Fume Condensation
UMICORE, 2024
Process for concentrating lithium from metallurgical fumes generated during recycling of lithium-ion batteries and other lithium-containing scraps. The process involves melting the scraps with fluxing agents like calcium chloride in a furnace to form a slag. Lithium concentrates in the fumes as lithium chloride (LiCl) as the slag solidifies. The fumes are then condensed and the concentrated lithium chloride can be recovered for further processing. This allows efficient lithium recycling from various sources without relying solely on hydrometallurgical methods.
6. Lithium-Ion Battery Recycling via Smelting and Selective Leaching for Lithium-Rich Compound Production
REDWOOD MAT INC, REDWOOD MATERIALS INC, 2023
Recycling lithium-ion batteries to produce high-concentration lithium compounds that can be used to return lithium to the supply chain. The process involves smelting the batteries to oxidize and separate the lithium from other metals. The lithium-rich slag is then leached selectively to extract lithium without co-extracting other elements like aluminum. This allows clean and efficient lithium recovery compared to traditional smelting.
7. Pyrometallurgical Smelting Process with Magnesia-Lined Furnace Using MnO-Rich Slag Composition
UMICORE, 2023
Pyrometallurgical process for recycling lithium-ion batteries with reduced wear of furnace walls. The process involves smelting battery waste and slag formers in a magnesia-lined furnace at temperatures above 1400°C. The slag composition is optimized to suppress dissolution of magnesia from the refractory bricks. The slag has MnO 25-70%, Al2O3+0.5MnO<45%, SiO2>5%, Li2O>3%, (CaO+2LiO+0.4MnO)/SiO2≥2.0. This slag composition protects furnace walls during smelting compared to standard slags. The green color of the slag indicates optimal MnO content.
8. Lithium-Ion Battery Waste Recycling via Co-Precipitation of Nickel, Manganese, and Cobalt for Cathode Precursor Synthesis
UMICORE, 2023
Recycling lithium-ion battery waste to produce precursor compounds for new battery cathodes, avoiding the complex and hazardous steps of separating and purifying individual metals from spent batteries. Instead, the essential metals nickel, manganese, and cobalt are refined together in a modified recycling process. This involves crushing and shredding batteries, dissolving the metal oxides in acid, co-precipitating them with lithium, and drying the precursor compound for use in cathode production. This simplifies and improves the recycling of lithium-ion battery waste compared to traditional methods of separating and purifying individual metals.
9. Slag Composition with High Lithium and Manganese Oxide Content for Reduced Fluxing Agents and Lower Melting Point
UMICORE, 2023
Slag composition for recycling lithium-ion battery scrap with high lithium content and reduced fluxing agents compared to conventional slags. The slag has a composition that allows lower melting points and viscosities compared to traditional slags containing high levels of fluxing agents like CaO and SiO2. The composition uses high lithium content (>15%) along with manganese oxide (MnO) to reduce the need for fluxing agents. This allows lower melting points below 1700°C and viscosities below 1600°C, which facilitates alloy separation and reduces dilution of lithium in the slag. The slag also has benefits like lower cobalt content for easier reuse compared to conventional slags.
10. Copper Smelting Process Incorporating Low Cobalt Lithium-Ion Batteries with Copper Scrap
UMICORE, 2016
Recycling lithium-ion batteries with low cobalt content by smelting them alongside copper-containing scrap in a copper melting furnace. The batteries, containing copper anode foil, aluminum cathode foil, and copper, aluminum, and plastic casing, are added to the furnace charge along with other copper scrap. The high copper content in the batteries increases the yield of blister copper from the smelting process. This allows recycling of the batteries along with regular copper scrap without requiring specialized pretreatment to handle the volatile electrolyte and ignitable materials.
11. Furnace-Based Metal Recovery Process with Oxygen Injection and Freeze Lining for Electric Vehicle Battery Smelting
CAMPFORTS MIEKE, UMICORE, UMICORE NV, 2011
Recycling process for recovering metals like Ni, Co, and Cu from electric vehicle (EV) batteries. The process involves smelting the batteries in a furnace with oxygen injection to reduce the metals. The furnace has freeze lining to protect against battery explosions. The reduction agents from the batteries provide energy for the smelting process. The metals form a bullion that can be further processed. The high battery content requires freeze lining to prevent furnace wall damage.
12. Single-Furnace Melting and Smelting Process for Metal Recovery from Lithium-Ion Batteries with Controlled Slag Composition
UMICORE, UMICORE NV, 2008
Recovering valuable metals like cobalt and nickel from used lithium-ion batteries and scrap in a single furnace process that avoids the high costs and drawbacks of multi-step hydro-metallurgical and pyro-metallurgical processes. The process involves melting and smelting the battery charge in a single furnace to extract the metals. Strategic selection of slag-forming materials allows controlling the slag composition to promote separation of the metals. Adding zinc-containing materials like alkaline batteries further helps segregate the valuable metals.
13. Single-Furnace Melting and Smelting Process for Metal Recovery from Lithium-Ion Battery Waste
UMICORE, 2007
Recovering valuable metals like cobalt and nickel from lithium-ion battery waste using a single-furnace process that avoids the high investment and operational costs of multi-step hydro-metallurgical or two-furnace pyro-metallurgical processes. The single-furnace process involves melting and smelting the battery waste in a single furnace to separate the metals from other components like plastic and electrolyte. The process allows high metal recovery while avoiding explosive reactions with moisture-containing shredding steps. By choosing slag-formers to produce a slag with a high SiO2:CaO ratio, the metal-rich slag floats to the top for easy separation. Adding zinc-containing waste like alkaline batteries helps further separate the metals.
Get Full Report
Access our comprehensive collection of 13 documents related to this technology
Identify Key Areas of Innovation in 2025
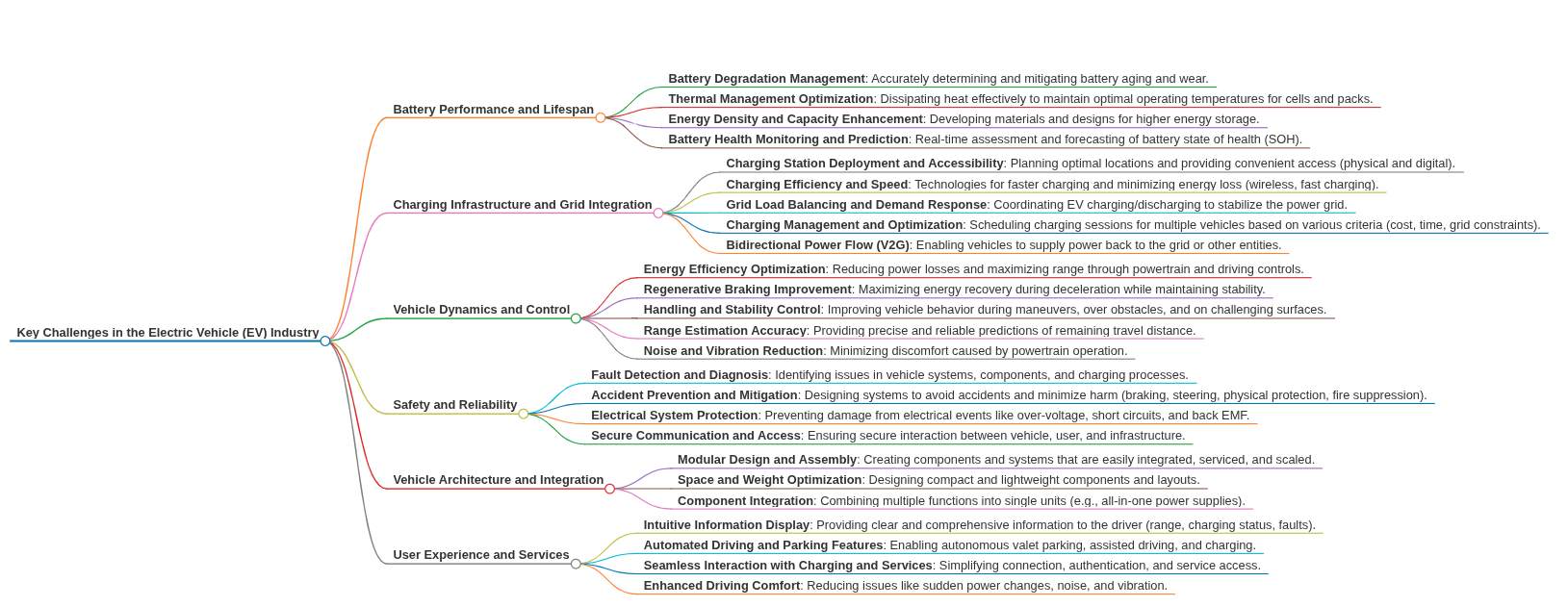