Solid State Electrolytes for Lithium Ion Batteries
Solid-state electrolytes represent a critical advancement in battery technology, offering ionic conductivities approaching 10⁻³ S/cm at room temperature while eliminating the safety risks inherent to liquid electrolytes. Current implementations face challenges with interfacial resistance, mechanical stress during cycling, and maintaining consistent ion transport across grain boundaries.
The fundamental challenge lies in developing materials that combine high ionic conductivity with the mechanical properties needed to maintain stable interfaces during repeated charge-discharge cycles.
This page brings together solutions from recent research—including composite polymer-ceramic architectures, protective interface layers for dendrite suppression, reinforced polymer matrices, and novel manufacturing approaches for reduced interfacial resistance. These and other approaches focus on practical implementations that can scale to commercial battery production while maintaining the safety advantages of solid-state systems.
1. Phosphorus-Sulfur Iodide Solid Electrolyte Doped with W and Mo for Enhanced Ionic Conductivity
HENGDIAN GROUP DMEGC MAGNETICS CO LTD, 2025
Doped phosphorus-sulfur iodide solid electrolyte for lithium-ion batteries with improved ionic conductivity for facilitating lithium ion transport. The doped electrolyte expands the ion transport channel by doping W and/or Mo elements with larger ionic radius. This increases the quantity of transport channels between cages, facilitating lithium ion transport. The doped electrolyte has an ionic conductivity of more than or equal to 1.0×10−3 S/cm and a wide electrochemical stability window. The doping improves the solid electrolyte's performance compared to undoped Li6PS5I.
2. Improve the Internal and Interface Stability of Sulfide‐Based Composite Electrolytes Through High Concentration Electrolyte and Continuous Li<sup>+</sup> Conductive Frameworks
jie zhang, chengshuai bao, jun jin - Wiley, 2025
Abstract Composite electrolytes have received widespread attention due to their potential simultaneously integrate the advantages of different types electrolytes. However, composite based on sulfides and polymers electrolyte still face issues such as instability toward lithium metal, low ion transference number, between sulfides. Based this, a continuous conductive Li 5.4 PS 4.4 Cl 1.6 (LPSC) framework with polytetrafluoroethylene (PTFE) is prepared binder (LPSC@PTFE) gel containing high concentration salt. The fills pores in LPSC@PTFE membrane protects interface sulfide metal. In addition, highconcentration exhibit better stability compared lowconcentration electrolytes, whether for metal or improvement has been demonstrated through analysis insitu electrochemical impedance spectroscopy (EIS) combined relaxation time distribution (DRT), well characterization by Xray photoelectron (XPS) Raman spectroscopy. mechanism behind performance enhancement theoretical calculations simulations also speculated on. optimized an window 4.98 V, increased number 0.74, critical current de... Read More
3. Crafting the Organic–Inorganic Interface with a Bridging Architecture for Solid‐State Li‐O<sub>2</sub> Batteries
minghui li, kecheng pan, dulin huang - Wiley, 2025
Abstract Solidstate lithiumoxygen batteries (SSLOBs) are offering unparalleled safety and exceptional electrochemical performance. Despite their promise, composite solid electrolytes (CSEs) fabricated through mechanical hybridization consistently manifest pronounced ceramic particle aggregation. In this study, a thin flexible CSE is developed by integrating Li 10 GeP 2 S 12 (LGPS) with poly(vinylidene fluoridecohexafluoropropylene) (PVDFHFP) implementing silane coupling agents to form bridging framework across the organicinorganic heterojunction interfaces. The engineered exhibited remarkable roomtemperature ionic conductivity reaching 1.05 4 cm 1 , superior stability within an expanded voltage window extending 4.9 V versus Li/Li + . Furthermore, lithium symmetrical cells revealed uniform deposition/dissolution behavior over 3000 h. Integration of thinfilm into SSLOBs yielded devices achieving specific discharge capacities 12874 mAh g coupled longterm operational throughout 120 cycles. enhanced interfacial adhesion forces observed between heterogen... Read More
4. 3D Porous Single‐Ion Conductive Polymer Electrolyte Integrated with Ether Polymer Networks for High‐Performance Lithium‐Metal Batteries
tapabrata dam, asif javid, eunsan jo - Wiley, 2025
The integration of polymerbased electrolytes into nextgeneration lithiummetal batteries (LMBs) offers significant potential for enhancing energy density and safety. However, their development is impeded by challenges such as low ionic conductivity at room temperature, anion polarization effects, a lithiumion transference number. This investigation aims to address the limitations combining singleion conductive polymer (SICP) ether network (EPN) electrolytes. interwoven structure SICP EPN ensures uniform distribution, facilitating efficient delocalized transport. Utilizing sulfonated poly(vinylidene fluoridecohexafluoropropylene)based with enhances conductivity, electrochemical stability, mechanical strength. optimized SICPEPN membrane exhibits an 10 4 S cm 1 , stability window exceeding 4.9 V, transport number 0.58 30 C. Li/SICPEPN/NCM811 cell demonstrates initial discharge capacity 189 mAh g Coulombic efficiency 99.7% 0.1 C C, maintaining minimal fading after 250 chargedischarge cycles 0.5 C. These findings highlight present viable econom... Read More
5. Near-Saturated Coordinated Cations in Oxyhalide Superionic Conductors Boost High-Rate All-Solid-State Batteries
long qian, shuibin tu, yue wang - American Chemical Society, 2025
Amorphous oxyhalide solid electrolytes (SEs) have garnered significant attention due to their excellent cathodic stability and favorable mechanical properties. However, the correlations between structural characteristics in amorphous phase Li+ transport behavior remain underexplored, limiting further promotion of ionic conductivities these SEs. Herein, we establish a correlation cationic coordination saturation SEs transport. Based on this correlation, near-saturated coordinated cation (NSCC)-incorporated Li1.5Zr0.5M0.5Cl5.0O0.5 (M = Nb or Ta, denoted as Nb- Ta-LZCO) are developed with abundant vacancy concentrations weakened Li-Cl interaction, thereby significantly enhancing As result, Nb-LZCO Ta-LZCO achieve impressive 2.33 3.88 mS cm-1, respectively, at 25 C. All-solid-state lithium batteries assembled representative LiNi0.8Mn0.1Co0.1O2 cathode demonstrate superior rate performance long-term cycling stability, delivering high specific capacity 120.0 mAh g-1 10.0 C (1 195 mA g-1) an outstanding retention 84.85% after 2000 cycles. This work establishes generalizable strategy for d... Read More
6. La<sub>2</sub>O<sub>3</sub>‐Reinforced Polymer Electrolyte with Enhanced Interfacial Lithium‐Ion Conductivity for High Stability Lithium Metal Batteries
xueping liu, xiangyu dai, qiaolu lin - Wiley, 2025
Abstract Solidstate polymer electrolytes (SPEs) are attracted significant attention for their potential to enhance safety and energy density in storage systems. However, two major challenges persist, namely low ionic conductivity interface instability. A composite electrolyte with superior stability is developed using PVDFHFP/PAN as the matrix La 2 O 3 fillers. atoms on surface of fillers act adsorption sites bind TFSI , promoting lithium salt dissociation increasing concentration free ions. Simultaneously, enable anchoring N, Ndimethylformamide (DMF) mitigate side reactions between DMF metal. Consequently, achieves a high transference number (0.64) optimal (0.31 mS cm 1 ). Besides, LiFePO 4 ||Li cell excellent capacity retention 90.92% after 300 cycles at 0.5C under ambient conditions. It also exhibits almost 100% 50 (0.2C) across temperature range RT 10 C. Similarly, when coupled LiNi 0.8 Co 0.1 Mn cathode, batteries demonstrate stable cycling (capacity > 83% over 180 cycles, 0.5C, 25C). This work offers promising approach advancing construction highperfo... Read More
7. Soft‐Hard Synergistic Solid All‐Polymer Electrolyte Inspired by Musculoskeletal Structure for High‐Temperature Lithium Metal Batteries
guorui zhu, qin zhang, yingying zhang - Wiley, 2025
Abstract Robust structures are essential for extending the application of shapeless soft polymer electrolytes and maintaining selfsupporting solidstate allpolymer (SPEs) at elevated temperatures. Common strategies introducing additional separators or crosslinking can significantly increase manufacturing complexity SPEs, thus limiting their commercialization. Herein, inspired by musculoskeletal structure, a softhard synergy enhanced SPE (named PPHSPE) is successfully designed manufactured simple onestep in situ microphase separation strategy hightemperature lithiummetal batteries. In bicontinuous PPHSPE, soft polyphosphazene liquid electrolyte (PPZLPE) phase provides excellent electrochemical properties, interfacial compatibility, stable Li 3 N/Li PO 4 rich hybrid interfaces. PVDFHFP crystals skillfully used to build 3D continuous, highstrength (0.32 0.02 MPa 90 C), thermotolerant hard skeleton. synergy two phases, Li//Li cell maintain continuous electrodeposition over 4500 h plating/stripping process 0.25 mA cm 2 mAh... Read More
8. Enhancement of Li+ Transport Through Intermediate Phase in High-Content Inorganic Composite Quasi-Solid-State Electrolytes
haoyang yuan, wenjun lin, changhao tian - Springer Science+Business Media, 2025
Abstract Quasi-solid-state electrolytes, which integrate the safety characteristics of inorganic materials, flexibility polymers, and high ionic conductivity liquid represent a transitional solution for high-energy-density lithium batteries. However, mechanisms by fillers enhance multiphase interfacial conduction remain inadequately understood. In this work, we synthesized composite quasi-solid-state electrolytes with content to investigate phenomena achieve enhanced electrode interface stability. Li 1.3 Al 0.3 Ti 1.7 (PO 4 ) 3 particles, through surface anion anchoring, improve + transference numbers facilitate partial dissociation solvated structures, resulting in superior ion transport kinetics that an 0.51 mS cm 1 at room temperature. The mass fraction components additionally promotes formation more stable layers, enabling lithium-symmetric cells operate without short-circuiting 6000 h 0.1 mA 2 . Furthermore, system demonstrates exceptional stability 5 V-class metal full cells, maintaining 80.5% capacity retention over 200 cycles 0.5C. These findings guide role interfaces d... Read More
9. Argyrodite-Structured Solid Electrolyte with Li1-bCub7-zPS6-zM3z Composition
SAMSUNG SDI CO LTD, 2025
A solid electrolyte material for lithium batteries with improved stability against lithium metal anodes and higher ionic conductivity compared to traditional solid electrolytes. The solid electrolyte is based on a compound with a specific chemical formula (Li1-bCub)7-zPS6-zM3z. The compound has an argyrodite-type crystal structure. It is prepared by mixing lithium, group 2/11, phosphorus, and group 17 compounds, then heat treating in an inert atmosphere. The solid electrolyte can be used in all-solid-state batteries to replace flammable liquid electrolytes.
10. Sulfide Solid Electrolyte with Specific X-ray Diffraction Peaks for Enhanced Lithium-Ion Conductivity
MITSUI MINING & SMELTING CO LTD, 2025
A sulfide solid electrolyte for solid-state batteries with improved lithium-ion conductivity. The sulfide solid electrolyte has specific X-ray diffraction peaks at 20-24° (peak A) and 24-26° (peak B) when analyzed using CuKα1 radiation. This sulfide solid electrolyte can be used in solid-state batteries to replace conventional liquid electrolytes. The sulfide electrolyte enables high ionic conductivity without the need for coating the active material particles. It provides a practical, low-cost alternative to expensive coatings like lithium niobate, lithium titanate, etc. The sulfide electrolyte reduces the resistance between the electrode materials, improving battery performance.
11. Battery Module with Selective Thermal Conductive Resin Application and Through-Hole Frame Design
LG ENERGY SOLUTION LTD, 2025
Battery module design for improving cooling performance while reducing thermal conductive resin usage. The module has a stack of battery cells surrounded by a frame. The bottom of the frame has regions separated by through holes. A thermal conductive resin layer is applied to the regions without holes to transfer heat between the cells and frame. This prevents temperature variations between cells. However, using resin only in those regions avoids excess resin that can decrease cooling efficiency. The holes allow direct contact between the cells and frame in the remaining region.
12. Aluminum Oxide Membrane Regulating the Performance of <scp>PEO</scp> Based Electrolyte for High‐Performance Quasi‐Solid‐State Lithium Batteries
yidan song, xue lu wang, yefeng yao - Wiley, 2025
ABSTRACT Solid electrolyte materials have improved the safety and stability of quasisolidstate lithiumion batteries, making them highly desirable. Through mesoporous confinement regulation anodic aluminum oxide (AAO) membranes optimization lithium bis (trifluoromethanesulfonyl) imide (LiTFSI) concentration, a lowcrystallinity polyethylene (PEO) based solid membrane, 18PEO/LiTFSI160, was prepared. This shows that when molar ratio ethylene to ion (EO: Li) is 18 AAO pore size 160200 nm, membrane exhibits crystallinity as low 13%, roomtemperature ionic conductivity 9.78 10 5 S cm 1 , Li + transference number increased 0.4, an electrochemical window broadened 5.1 V. In Li/Li symmetric cell tests, interfacial impedance remained stable at 180 after 160 h cycling, with smooth interface no dendrite formation observed. Fullcell performance tests further verified effects: assembled LiFePO 4 delivered discharge capacity 142 mAh/g 0.1 C rate retained 95% its 100 cycles. The 18PEO/LiTFSI160 polymer demonstrates promising viable material for allsolidstat... Read More
13. Solid Electrolyte Comprising Zirconium-Doped Argyrodite with Enhanced Ionic Conductivity
SAMSUNG SDI CO LTD, 2025
Solid electrolyte for all solid-state batteries that improves ionic conductivity and cycle life compared to pure argyrodite electrolytes. The solid electrolyte contains a very low concentration (100-1000 ppm) of zirconium (Zr) mixed with the argyrodite compound. The Zr addition improves the ionic conductivity of the argyrodite electrolyte without degrading its stability, enabling faster charging and discharging. The Zr-doped argyrodite electrolyte can be used in all solid-state batteries with improved performance compared to pure argyrodite electrolytes.
14. Solid-State Battery Subassembly with Carbon-Based Bonding Layer for Enhanced Interfacial Adhesion
SAMSUNG ELECTRONICS CO LTD, 2025
A solid-state battery subassembly with improved interfacial adhesion between the solid electrolyte and anode for higher charging/discharging performance. The subassembly has a carbon active material layer sandwiched between the anode current collector and solid electrolyte. A bonding layer made of material similar to the carbon active material is formed between the solid electrolyte and carbon layer. This bonding layer enhances adhesion between the electrolyte and anode components compared to direct contact.
15. Imaging System with Movable Active Lens for Fluorescence Microscopy on Curved Surfaces
SEOUL NATIONAL UNIVERSITY HOSPITAL, POSTECH RESEARCH AND BUSINESS DEVELOPMENT FOUNDATION, UNIVERSITY INDUSTRY FOUNDATION YONSEI UNIVERSITY WONJU CAMPUS, 2025
An imaging system for examining cells on a curved surface like the eye conjunctiva using fluorescence microscopy. It uses a movable lens to keep the entire area in focus during image acquisition. The system has a light source, a fixed objective lens, a movable active lens, a CCD camera, and an image processing unit. The active lens dynamically adjusts focus during imaging to capture in-focus data of the curved tissue stained with moxifloxacin. This allows acquiring a single image with the entire tissue in focus, unlike traditional microscopes with shallow depth of field.
16. Integrated design of covalent organic frameworks-based solid-state electrolytes and cathode materials for constructing high-performance lithium metal batteries
weikuan guo, kexin zhu, panpan li - American Institute of Physics, 2025
Solid-state lithium metal batteries (SSLMBs) are regarded as the next-generation energy storage systems, offering enhanced safety and higher density. Polyethylene oxide-based solid-state electrolytes (SSEs) have garnered significant attention due to their advantages, including superior safety, straightforward fabrication processes, high However, low ionic conductivity has hindered commercialization of SSLMBs. In this study, we developed a modified grafting PEG onto material COF-5-6 SSE slurry, which was coated surface LiFePO4 cathode construct an integrated for The B atoms in COF-5-6-PEG serve Lewis acid sites, adsorbing anchoring anions from salts, thereby promoting dissociation salts releasing more Li+. Additionally, S O polar complex with Li+, facilitating solvation Li+ within flexible segments enabling rapid transport through interconnected channels. As result, membrane demonstrates 1.41 103 cm1 transference number 0.47, along stable polarization behavior over 400 h Li electrodes at 80 C. Moreover, Li||COF-5-6-PEG SSE||LiFePO4 cells exhibit dendrite-free surface, promi... Read More
17. Interfacial-Oxygen-Regulated Lithium-Rich Manganese-Based Cathode for High-Performance Solid-State Lithium Batteries
keke gao, fusheng yin, fanghui mi - American Chemical Society, 2025
High-capacity lithium-rich manganese-based materials Li1.20Mn0.54Ni0.13Co0.13O2 (LRMs) are potential cathodes for solid-state lithium batteries with high energy density. However, there challenges of low initial Coulomb efficiency (ICE) and interfacial degradation the cathode caused by irreversible oxygen release. Here, oxygen-deficient ceria (CeO2-x) abundant vacancies was used to scavenge excess species manipulate evolution LRM in battery. CeO2-x realizes reversible storage release anion vacancies, doping Ce3+/4+ into lattice stabilizes structure enhances Li+ transport kinetics. Therefore, cell a NASICON-type F-doped Li1.3Al0.3Ti1.7(PO3.93F0.07)3 (F-LATP) solid electrolyte shows ICE 86.74%, an outstanding rate performance 70.0 mAh g-1 at 1 C, remarkable cyclability lower capacity decay 0.27% per cycle. It is believed that this work provides valuable guidance design redox high-capacity LRMs batteries.
18. Bipolar Lithium Battery Packs with Solid Electrolyte Hybrid for Enhanced Safety and Energy Density
HONEYCOMB BATTERY CO, 2025
Bipolar lithium battery packs for high energy density applications like electric vehicles with reduced flammability and improved safety compared to conventional liquid electrolyte batteries. The packs use bipolar electrodes with solid electrolytes sandwiched between the electrode layers instead of liquid electrolytes. The electrodes have a current collector, cathode, and optionally an anode. The solid electrolyte is a hybrid of an inorganic solid electrolyte and a solid polymer electrolyte. The packs are made by stacking the bipolar electrodes with separators between them to form modules.
19. Ce/O Co‐Substitution Strategy Enhanced Stability of Sulfide Electrolyte for All‐Solid‐State Lithium Metal Batteries
m g zhao, jie zhang, lihua pu - Wiley, 2025
Abstract Sulfide solid electrolytes (SSEs) exhibit exceptional ionic conductivity and processing advantages for allsolidstate lithium metal batteries (ASSLBs), but their commercialization is constrained by ambient hydrolysisinduced H 2 S generation dendrite formation at electrolyte/anode interfaces. Herein, a Ce/O cosubstitution strategy employed to synthesize argyroditetype Li 5.4+x P 1x Ce x 4.42x O 2x Cl 1.6 (0 0.05) electrolytes. The substitution of 5+ with 4+ 2 2 in the PS 4 3 structure forms stable CeS 4 3 groups enhances structural integrity. Simultaneously, incorporation expands lattice spacing facilitates + transport. Optimized 5.42 0.98 0.02 4.36 0.04 electrolyte exhibits superior (7.13 mS cm 1 ) excellent air stability (H emission: 0.36 g after 30 min 30% RH). demonstrates an enhanced critical current density 1.3 mA 2 plating/stripping over 5000 h 0.1 . ASSLBs LiNbO @NCM622 cathodes deliver initial discharge capacity 128.19 mAh 99.49% retention 300 cycles. This work provides designing highperformance SSEs toward practical batte... Read More
20. Synthesis of Lithium Lanthanum Zirconate Solid Electrolyte via Lanthanum Zirconate Nanocrystal Precursor Transformation
ARIZONA BOARD OF REGENTS ON BEHALF OF ARIZONA STATE UNIVERSITY, 2025
Synthesizing high-performance lithium lanthanum zirconate (LLZO) solid electrolyte for lithium-ion batteries by starting with lanthanum zirconate (LZO) nanocrystals. The LLZO is formed by dispersing LZO nanocrystals in a slurry with lithium and lanthanum compounds, drying and calcining the slurry to transform the LZO nanocrystals into LLZO. This allows direct synthesis of LLZO using LZO nanocrystals as precursors instead of starting from scratch.
Get Full Report
Access our comprehensive collection of 293 documents related to this technology
Identify Key Areas of Innovation in 2025
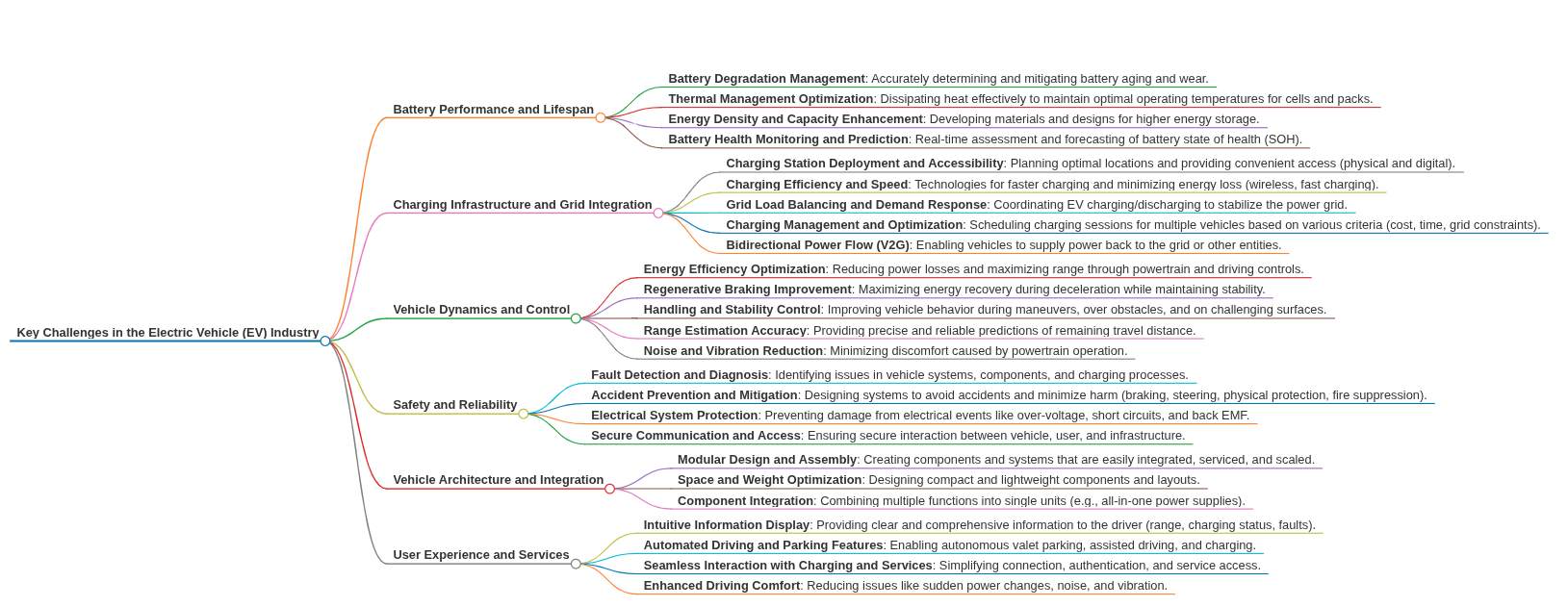