Battery Coolant for EV Thermal Management
Electric vehicle battery packs generate substantial heat during charging and operation, with cell temperatures routinely reaching 45°C under high load conditions. Managing this thermal load is critical, as operating outside the optimal 20-40°C window can accelerate battery degradation and reduce pack lifetime by up to 50%.
The fundamental challenge lies in developing coolants that can efficiently transfer heat while maintaining electrical isolation properties essential for high-voltage battery systems.
This page brings together solutions from recent research—including phase change materials for enhanced thermal capacity, Fischer-Tropsch derived base oils with optimized aging properties, nanofluids with improved heat transfer characteristics, and composite cooling systems that combine multiple approaches. These and other developments focus on achieving uniform temperature distribution across battery packs while maintaining long-term stability and safety requirements.
1. Isoparaffinic Mineral Oil-Based Heat Transfer Fluid with Balanced Electrical and Thermal Properties
THE LUBRIZOL CORP, 2024
A low-cost heat transfer fluid for cooling high-power density electrical components like batteries and electronics in applications like electric vehicles and servers. The fluid has balanced electrical properties like low electrical conductivity and dielectric constant to avoid issues like shorts, arcing, and static buildup. It also has desirable thermal properties like low pour point, kinematic viscosity, and flash point. The fluid is synthesized from isoparaffinic mineral oil base stock with additives like antioxidants, dispersants, and detergents to optimize performance.
2. Refrigerant-Based Cooling Circuit with Current Limitation for Solid-State Battery Thermal Regulation
HONDA MOTOR CO., LTD., 2024
Battery cooling system for solid-state batteries in electric vehicles that prevents the battery temperature from exceeding a safe operating limit when the battery already exceeds a lower limit. The system uses a refrigerant cooling circuit between the battery and an external heat exchanger. When the battery temperature exceeds the lower limit, the battery controller limits the battery current to balance the heat generated by the battery, heat absorbed by the refrigerant, and heat exhausted by the heat exchanger. This keeps the battery temperature between the lower and upper limits. By closely controlling current and refrigerant flow, the system prevents excessive battery heating even if the battery already exceeds the lower limit.
3. Battery Module with Dual Coolant Circuits and Heat Exchanger for Individual Cell Temperature Regulation
MERCEDES BENZ GROUP AG, MERCEDES-BENZ GROUP AG, 2024
Battery module for electric vehicles that has a secondary cooling system to quickly and effectively cool individual cells with thermal runaway to prevent catastrophic failures. The module has two coolant circuits, one inside the module and another connected to an external refrigeration unit. The internal circuit has a heat exchanger that cools the cells. If a cell overheats, the internal heat exchanger is activated. If it still overheats, the external circuit is activated to bring the cell temperature down faster. This prevents thermal runaway propagation and cell damage.
4. Shared Coolant Loop with Valve-Controlled Heat Exchange for Electric Vehicle Components
GREAT WALL MOTOR COMPANY LTD, 2024
Vehicle thermal management system that allows efficient utilization of waste heat in electric vehicles. It uses a shared coolant loop with valves to enable heat exchange between components like motors, batteries, heating/cooling systems, and cabin. This allows passive cooling of components by circulating coolant through them, as well as active heating using the same loop. The shared loop allows comprehensive heat recovery versus separate loops for each component.
5. Vehicle Thermal Management System with Separate Battery Heat Exchangers and Controller
BYD CO LTD, BYD COMPANY LTD, 2024
Thermal management system for vehicles with improved efficiency and versatility compared to traditional systems. The system uses separate heat exchangers to exchange heat with the battery at different efficiencies based on battery temperature. This allows optimized heat transfer without wasting energy on unnecessary heating or cooling. A controller manages the heat exchangers. The system also includes an air conditioning loop and options for heat storage. The separate heat exchangers and controller allow more flexible and efficient battery heating/cooling compared to a single heat exchanger.
6. Electric Vehicle Battery Thermal Management System with Separate Heat Exchange Loop and Switch Valve Configuration
HUZHOU SANY WHEEL LOADER CO LTD, 2024
Battery thermal management system for electric vehicles that uses a separate heat exchange loop to prevent direct heating of the battery. The system has a circulating loop with a pump, heat exchanger, valve, and pipes filled with coolant. The loop connects to the battery for heat exchange. In standby, the loop heats the battery. When running, it cools. A switch valve connects the loop to the battery or a cooling chamber. This prevents heating components directly connected to the battery to reduce risk of battery accidents.
7. Power Battery Liquid Cooling System with Dual-Module Heat Dissipation and Temperature-Responsive Switching
CHINA AVIATION LITHIUM BATTERY CO LTD, 2024
Power battery liquid cooling system for electric vehicles that uses a two-stage cooling approach to improve cooling efficiency in low temperature environments. The system has two heat dissipation modules, one with a compressor for high temperature operation and another with a radiator for low temperature operation. A temperature sensor detects the ambient temperature and controls which module to use. This allows the system to switch between the compressor for high temp and radiator for low temp cooling based on ambient conditions. The radiator module avoids compressor efficiency loss in cold temperatures.
8. Thermal Management System with Series-Connected Refrigeration, Heating, and Battery Heat Exchanger and Switchable Circuit Valves
BYD CO LTD, BYD COMPANY LTD, 2024
Thermal management system for electric vehicles that allows efficient heating and cooling of the battery pack in all ambient temperature conditions. The system uses a series connection of a refrigeration component, heating component, and battery heat exchanger in the battery circuit. This allows cooling the battery during high temperatures and heating during low temperatures. The system also has an electric drive circuit with heat exchanger and radiator. Valves can switch connection between the battery and drive circuits. This enables efficient heating/cooling of both circuits.
9. Dual-Circuit Battery Thermal Management System with Directional Flow Switching and Bypass Loop
Guangzhou Automobile Group Co., Ltd., GUANGZHOU AUTOMOBILE GROUP CO LTD, 2024
Battery thermal management system for electric vehicles that improves temperature uniformity inside the battery pack. The system uses two cooling loops, one bypassing some components like heaters and radiators, to circulate coolant. A valve switches between loops. The bypass loop has lower pressure drop. Periodically switching flow direction in both loops further reduces temperature gradients.
10. Battery Cooling Composition with Low Thermal Conductivity and Thermal Runaway Protection
TOTAL MARKETING SERVICES, 2024
Cooling composition for batteries in electric vehicles that combines improved cooling with protection against thermal runaway. The composition has a thermal conductivity less than or equal to 125 mW/m·K at 30°C. It contains base oils, antioxidants, and optional additives like anti-corrosion agents. The composition circulates in cooling loops around battery cells to extract heat. By having lower thermal conductivity, it prevents excessive heating that can lead to thermal runaway. The lower conductivity also improves cooling performance compared to conventional oils. The composition can be used in devices like cooling circuits and storage tanks to cool batteries in electric vehicles.
11. Battery Thermal Management System with Closed-Loop Refrigerant Cycle and Heat Recovery for Electric Vehicles
KOREA AUTOMOTIVE TECH INSTITUTE, KOREA AUTOMOTIVE TECHNOLOGY INSTITUTE, 2024
Battery thermal management system for electric vehicles that improves battery module output efficiency by using a closed-loop refrigerant cycle with heat recovery and regeneration. The system has a thermal management unit, cycle unit, heating unit, cooling unit, sensing unit, and control unit. The cycle unit circulates a first heat exchange medium to the battery module. The heating unit transfers refrigerant from the compressor to heat the battery. The cooling unit transfers refrigerant from the evaporator to cool the battery. The control unit selectively opens/closes the heating and cooling units based on battery temperature. This allows regenerating heat from the cooling unit to heat the battery instead of wasting it. The refrigerant cycle also allows separate cooling/heating paths to share pipes for simplicity.
12. Battery Pack with Integrated Phase Change Material and Liquid Cooling System Featuring Temperature-Controlled Rotor Pump
CHINA UNIV OF MINING & TECHNOLOGY, CHINA UNIVERSITY OF MINING & TECHNOLOGY, 2023
Battery thermal management system that uses phase change materials (PCMs) inside the battery pack along with a liquid cooling system. The PCMs absorb and release heat during charging/discharging. A rotor pump circulates coolant through the PCMs and liquid cooling channels. An electronic controller monitors battery temperatures and activates the pump when needed. This provides optimal heat dissipation using both PCMs and liquid cooling based on battery temperatures. The PCMs improve uniformity and prevent overheating, while the liquid cooling provides backup when PCMs melt.
13. Electric Vehicle Battery Thermal Management System with Dual Refrigerant Circuit Integration
SANHUA HOLDING GROUP CO., LTD., 2023
Thermal management system for electric vehicles that allows rapid cooling of the battery during high heat conditions. The system has two separate refrigerant circuits, one for the passenger compartment and one for the battery. During rapid cooling, both circuits are connected to the battery heat exchanger. This allows coolant from both circuits to absorb battery heat simultaneously, rapidly dissipating it. The separate circuits prevent overloading one circuit with battery heat.
14. Hierarchical Electric Vehicle Battery Cooling System with Multi-Level Heat Exchanger Integration
Jilin University, JILIN UNIVERSITY, 2023
Electric vehicle battery cooling system that enables efficient and adaptive cooling of batteries across a wide temperature range. It uses a hierarchical cooling strategy with three levels: air cooling for low load, indirect refrigerant cooling for medium load, and direct refrigerant cooling for high load/overheating. The system has multiple heat exchangers in the battery pack, one with a refrigerant circuit and another with a coolant circuit. The refrigerant directly contacts the battery for rapid cooling, while the coolant provides secondary cooling. This allows efficient cooling in all conditions without compromising performance or safety.
15. Thermal Management System with Encapsulated Phase Change Material-Enhanced Working Fluid for Direct Contact Cooling of Heat-Generating Components
SHELL INTERNATIONALE RES MAATSCHAPPIJ B V, SHELL INTERNATIONALE RESEARCH MAATSCHAPPIJ BV, SHELL USA INC, 2023
Thermal management system for heat-generating components like batteries in electric vehicles that uses a working fluid with encapsulated phase change materials (PCMs) to improve cooling performance. The system involves direct contact between the component and the fluid, which contains a base fluid and micro/nano-encapsulated PCMs. The encapsulated PCMs absorb and store heat as they melt, providing additional cooling capacity compared to just the base fluid. This allows more effective thermal management of the component by uniformly distributing the heat away from the component surface.
16. Integrated Thermal Management System with Combined Battery and Vehicle Cooling Utilizing Convection and Refrigerant Loops
Deere & Company, 2023
Integrated thermal management system for electric work machines like excavators that combines battery cooling with vehicle cooling in a compact and efficient manner. The system uses a battery coolant loop, a refrigerant loop, and a radiator with a fan. The battery coolant loop circulates coolant through the battery and radiator to passively cool the battery by convection. The fan forces air over the radiator for semi-passive cooling. The refrigerant loop actively cools the battery when needed by circulating refrigerant through the radiator. This integrated system allows versatile battery cooling in stationary work machines without relying solely on ambient air.
17. Thermal Management System with Fischer-Tropsch Derived Fluid for Direct Immersion of Heat-Generating Components
SHELL INT RESEARCH, SHELL INTERNATIONALE RESEARCH MAATSCHAPPIJ BV, 2023
Thermal management system for heat-generating components like batteries in electric vehicles that uses a working fluid containing a Fischer-Tropsch derived base oil, antioxidant, and antistatic additives. The components are directly immersed in the fluid to improve heat transfer. The fluid flows cyclically between components and a heat exchanger. The Fischer-Tropsch oil provides better aging properties compared to conventional fluids.
18. Variable Diameter Cooling Conduit for Adaptive Response to Battery Cell Swelling
VOLVO TRUCK CORP, 2023
Cooling system for electric battery cells that adapts to the cells swelling as they age and degrade. The cooling system has a variable diameter cooling conduit that expands or contracts in response to cell swelling. This prevents coolant flow restrictions due to cell expansion. The diameter change is proportional to the cell's swelling mechanism. By matching the cooling conduit dimension to the cell's expansion, it ensures adequate coolant flow even as the battery cells enlarge over time. This helps maintain cooling performance and prevents thermal runaway during use.
19. Battery Pack Thermal Management Structure with Inflated Aluminum Plates, Vapor Chamber Plates, and Heating Film
South China University of Technology, Guangdong New Creativity Technology Co., Ltd., SOUTH CHINA UNIVERSITY OF TECHNOLOGY, 2023
Integrated phase change cooling and heating structure for battery packs in electric vehicles. The structure uses inflated aluminum plates between the battery cells, vapor chamber plates on top, and a heating film on bottom. This allows phase change cooling with aluminum and vaporization cooling at the top, while also providing heating at the bottom using a film. A control system manages the cooling/heating fluid flow. It enables efficient thermal management of the battery pack across a wide temperature range.
20. Electric Vehicle Thermal Management System with Configurable Valve-Controlled Heat Exchange Pathways
Kelvin New Energy Technology Co., Ltd., 2023
Vehicle thermal management system for electric vehicles that improves heat exchange efficiency compared to conventional systems. The system has a refrigeration assembly, cabin heat exchanger, motor-drive-side heat exchanger, battery heat exchanger, and radiator tank. Three-way valves, reversing valves, and solenoid valves are used to selectively connect the components in various ways based on cooling/heating needs. This allows optimized heat flow paths between components like the motor, battery, and cabin. A control method coordinates the valve positions for different operating scenarios. This enables efficient heat transfer between components like radiating motor heat, using battery heat for cabin, or selective cooling of motor/battery.
Get Full Report
Access our comprehensive collection of 106 documents related to this technology
Identify Key Areas of Innovation in 2025
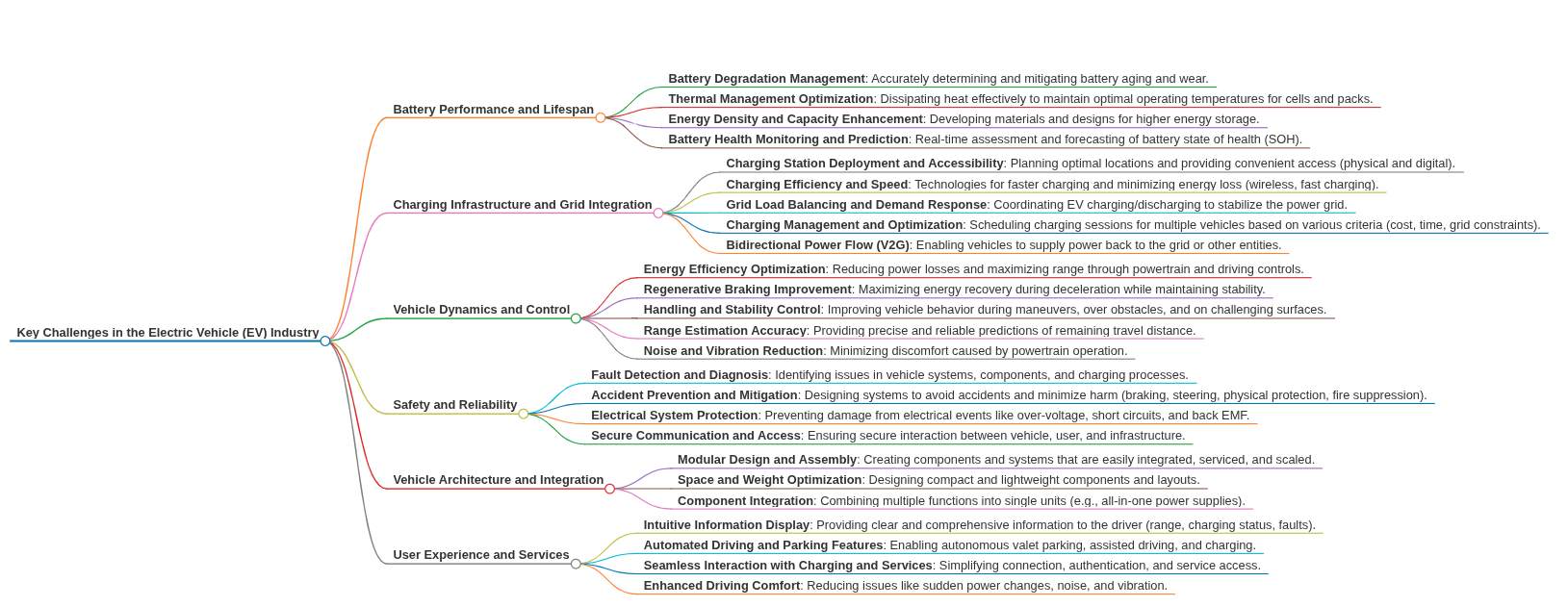