Innovations in EV Battery Management Systems
Modern electric vehicle battery packs operate under demanding conditions, managing charge/discharge cycles of up to 800V while maintaining cell temperatures within a 15-45°C window. These systems must coordinate thousands of individual cells, process real-time sensor data, and respond to rapid changes in power demand—all while ensuring safety across the pack's 8-10 year service life.
The fundamental challenge lies in balancing system performance and longevity against the competing demands of thermal management, charge optimization, and safety monitoring.
This page brings together solutions from recent research—including adaptive thermal management systems, intelligent charge coordination algorithms, liquid detection mechanisms, and predictive diagnostic routines. These and other approaches demonstrate how modern battery management systems can maximize vehicle range and battery life while maintaining robust safety margins.
1. Hybrid Converter Design Based on Boost and Push Pull Topologies
hamza yapici, remzi inan - Recep Tayyip Erdogan Üniversitesi Fen ve Mühendislik Bilimleri Dergisi, 2025
This paper introduces a hybrid converter topology based on boost and push-pull configurations for electric vehicle (EV) charging applications. In the proposed structure, an RCD snubber circuit is used to reduce thermal losses in power electronic devices peak voltages individual components. Thus, by reducing switching components, efficiency of structure increased. The aims voltage stress components transformation ratio transformer converter. addition, another aim provide improved continuous rectified output current, thus extending system's life Moreover, tested conduction mode (CCM) compared with similar existing designs. To verify mathematical analysis, 500 W designed using estimation simulation environment. analysis yielded direct current. As result significant reduction stresses elements occurred topology. turns ratio, are reduced.
2. Explainable AI for Battery Degradation Prediction in EVs: Toward Transparent Energy Forecasting
olivia chen, jerry reid, alan meier - Asia Pacific College, 2025
The rapid growth of electric vehicles (EVs) has intensified the demand for accurate and interpretable battery health prediction systems. While machine learning models have demonstrated high accuracy in forecasting degradation, their black-box nature poses challenges real-world deployment safety-critical applications. This paper proposes an explainable artificial intelligence (XAI) framework degradation prediction, aiming to provide transparent reliable insights into energy storage dynamics EVs. study integrates data-driven such as Gradient Boosting Machines (GBMs) Long Short-Term Memory (LSTM) networks with post hoc explainability tools, including SHapley Additive exPlanations (SHAP) Local Interpretable Model-agnostic Explanations (LIME). Experimental evaluations on EV datasets show that proposed achieves strong predictive performance while offering outputs regarding feature influence dynamics. These findings suggest XAI-enabled can bridge gap between power trust, contributing smarter management systems sustainable transportation.
3. Fuzzy Control and Rule-Based Control for Energy Management in Hybrid Vehicles
jose efren barbosa galarza, jose efren barbosa costales, pedro alejandro vejarano jara - AutanaBooks, 2025
This paper presents the design and simulation of fuzzy control rule-based for energy management in a parallel mild hybrid electric vehicle. The system must minimize fuel consumption while ensuring load maintenance component limitations. Equivalent is used to evaluate performance, which penalizes battery's use electrical but does not reward storage battery. presented model was tested two different driving cycles, Europe: NEDC USA: FTP-75 with an efficiency 17.6% 18.3% respectively. However, this result could be improved more in-depth testing error estimation, as well advanced simulations. In addition, rules can added proposed model, giving approach scalable functionality.
4. Battery Monitoring System (BMS) Using Arduino UNO
banoth srinu - Indospace Publications, 2025
Abstract - A Battery Monitoring System (BMS) is an electronic setup designed to track essential parameters of rechargeable batteries, such as voltage, current, and State-of-Charge (SoC). By preventing overcharging over-discharging, systems help extend the lifespan reliability batteries. However, commercially available BMoS solutions are often costly unsuitable for budget-friendly embedded systems. Given widespread use Arduino Uno its affordability, open-source platform, user-friendly programming environment, this study aims develop a using microcontroller. The proposed system includes voltage current sensors, board, liquid crystal display (LCD) real-time monitoring. To achieve this, set out three primary objectives. First, it was necessary mathematically establish relationship between sensors' input output values. These mathematical expressions were then validated by observing sensor outputs under varying load conditions connecting disconnecting monitoring corresponding readings. Following complete prototype assembled integrating sensors LCD with Uno. tested 11.1 V Lithium-ion ba... Read More
5. An Enhanced Cascaded Deep Learning Framework for Multi-Cell Voltage Forecasting and State of Charge Estimation in Electric Vehicle Batteries Using LSTM Networks
supavee pourbunthidkul, narawit pahaisuk, popphon laon - Multidisciplinary Digital Publishing Institute, 2025
Enhanced Battery Management Systems (BMS) are essential for improving operational efficacy and safety within Electric Vehicles (EVs), especially in tropical climates where traditional systems encounter considerable performance constraints. This research introduces a novel two-tiered deep learning framework that utilizes two-stage Long Short-Term Memory (LSTM) precise prediction of battery voltage SoC. The first tier employs LSTM-1 forecasts individual cell voltages across full-scale 120-cell Lithium Iron Phosphate (LFP) pack using multivariate time-series data, including history, vehicle speed, current, temperature, load metrics, derived from dynamometer testing. Experiments simulate real-world urban driving, with speeds 6 km/h to 40 variations 0, 10, 20%. second uses LSTM-2 SoC estimation, designed handle temperature-dependent fluctuations high-temperature environments. cascade design allows the system capture complex temporal inter-cell dependencies, making it effective under variable-load Empirical validation demonstrates 15% improvement estimation accuracy over methods driving co... Read More
6. Research on DP-MPC control strategy based on active equalisation system of bidirectional flyback transformer
yingzhe kan, min yang, run qian, 2025
<title>Abstract</title> The inconsistency between power battery cells can seriously restrict the energy utilization efficiency of pack, accelerate aging batteries, and even significantly increase risk thermal runaway. Aiming at this inconsistency, an active equilibrium scheme combining dynamic programming (DP) model predictive control (MPC) is proposed. Firstly, topology circuit bidirectional flyback transformer with rapid equalization speed built, then a system prediction established through MPC to achieve rolling optimization. Finally, using DP solve cost function in conditional scenarios obtain global optimal current time, used predict state changes multiple sampling periods online correction balanced current. algorithm improves overall reduces loss while considering charging discharging equalizer ensure consistent convergence each individual SOC. Simulation experimental results show that strategy quickly effectively correct lithium packs under various conditions, thereby greatly improving balance pack.
7. Smart Vehicle System with Wireless Monitoring and Response Mechanism for Battery Pack Thermal Events
GM GLOBAL TECHNOLOGY OPERATIONS LLC, 2025
Smart vehicle systems for detecting and responding to severe thermal events in rechargeable battery packs. The systems employ wireless communication protocols to monitor battery temperature and surrounding environment, and automatically detect nearby vehicles or pedestrians within a defined proximity. They then assess the severity of the thermal event using data from both the battery and surrounding environment, and trigger appropriate vehicle responses such as alerts, system shutdown, or control actions to mitigate the thermal event.
8. Battery Output Limit Prevention System with SOC and Temperature-Based Thermal Management
HYUNDAI MOTOR CO, KIA CORP, 2025
Preventing output limit of a battery in a vehicle by selectively raising the battery temperature based on the state of charge (SOC) and temperature during driving and restart. A method of preventing output limit of a battery of a vehicle includes monitoring the battery SOC and temperature while driving, determining the likelihood of output limit based on a map, and selectively increasing the battery temperature if output limit is likely. This prevents output limit when the SOC decreases in cold temperatures.
9. Method for Estimating Battery States with Dual Estimators and Adaptive Nominal Value Adjustment
VOLVO TRUCK CORP, 2025
Computationally efficient and accurate method for estimating battery states of electric vehicle energy storage systems using dual estimators. The dual estimators separately estimate battery state and parameter changes around nominal values. This allows tracking fast changes while reducing computation and storage compared to estimating total changes. The nominal values are also adaptively adjusted based on operational data to account for slow timescale variations. A lower frequency third estimator estimates the nominal values using downsampled dual estimator output. This reduces computation further by not using all historical data.
10. Dynamic Interrupt Handling Migration Across Processing Cores in System-on-Chip with Runtime Affinity and Priority Adjustment
ALTERA CORP, 2025
Migrating interrupt handling between processing cores in a system-on-chip (SoC) to improve real-time responsiveness and reduce latency. The method involves dynamically assigning interrupt affinities and priorities at runtime based on real-time conditions and workload demands. This allows interrupts to be serviced by the most appropriate core without fixed affinity constraints. The technique involves monitoring core utilization, interrupt latency, and other metrics to determine optimal affinity and priority assignments. It also supports live migration of interrupt handling between cores during execution to further optimize performance. This enables dynamic interrupt management that can adapt to changing workloads and prioritize critical real-time interrupts over less time-sensitive ones.
11. Battery Management System Utilizing Voltage-Based Observation Matrix and Principal Component Analysis for Cell Abnormality Detection
LG ENERGY SOLUTION LTD, 2025
Battery management system for detecting cell abnormalities using just the cell voltage as input. The method involves generating an observation matrix of voltage histories for each cell, recovering it using principal components, and comparing the original and recovered matrices to find abnormal cells. This reduces computation, time, and power compared to monitoring multiple parameters.
12. Thermal Management System with Zoned Temperature Control for Electric Vehicle Batteries
FORD GLOBAL TECHNOLOGIES LLC, 2025
Thermal management system for electric vehicle batteries that allows individual cooling or heating of different zones within the battery to optimize performance and lifespan. The system uses multiple distinct circuits, each associated with a cooling zone, with independent flow control valves. A controller ranks the zones by temperature and adjusts the valves to balance cooling and heating based on the hottest and coldest zones. This provides customized cooling/heating to prevent hot spots and improve overall battery temperature management.
13. Battery Management System with Demand-Responsive Charge/Discharge Cycling and Degradation Assessment
TOYOTA JIDOSHA KABUSHIKI KAISHA, 2025
Battery management system and method for optimizing battery utilization during storage. The system involves charging/discharging batteries in response to demand response signals from a power system. By cycling stored batteries this way, it allows effective utilization during storage periods rather than just sitting idle. The system also evaluates degradation of each battery based on charging/discharging data. This allows selecting batteries with the right condition for subsequent uses like reuse or rebuilding.
14. Electric Vehicle Charging Station Utilizing Highly Concentrated Photovoltaic System Combined with Lithium-Ion Batteries
kandil m kandil, haitham a alabdulali, ibrahim m kadad - European Center of Sustainable Development, 2025
Combining highly concentrated photovoltaic (HCPV) modules and battery storage systems attain high power- density than other ones using separate elements. This work aims to examine the performance of electric vehicle (EV) charging station utilizing an HCPV system integrated with lithium-ion batteries in Kuwait. is EV, storge system, AC grid as a four-component for EV at educational building located A theoretical technique developed calculate proposed efficiency. simple algorithm utilized reduction greenhouse emissions due use HCPV-EV. Energy produced from used charge four EVs, supplying energy electrical appliances feeding remaining grid. Present results reveal that represents 81% total load needed EVs about 90% required through utilization which can potentially reduce operating costs EVs. Only 10% (1218 kWh) be exported fully Also, provide 93% resulting big saving electricity bill. feed utility by 11458 kWh, additional decrease consumption costs. In all months, ratio (PR) higher 80%, indicating reliability system. Battery state (SOC) exceeds 70% most year months durability batteries.... Read More
15. Sensors Innovations for Smart Lithium-Based Batteries: Advancements, Opportunities, and Potential Challenges
jamile mohammadi moradian, amjad ali, xuehua yan - Springer Science+Business Media, 2025
Abstract Lithium-based batteries (LiBs) are integral components in operating electric vehicles to renewable energy systems and portable electronic devices, thanks their unparalleled density, minimal self-discharge rates, favorable cycle life. However, the inherent safety risks performance degradation of LiB over time impose continuous monitoring facilitated by sophisticated battery management (BMS). This review comprehensively analyzes current state sensor technologies for smart LiBs, focusing on advancements, opportunities, potential challenges. Sensors classified into two primary groups based application: optimization. Safety sensors, including temperature, pressure, strain, gas, acoustic, magnetic focus detecting conditions that could lead hazardous situations. Performance optimization such as optical-based electrochemical-based, monitor factors charge health, emphasizing operational efficiency lifespan. The also highlights importance integrating these sensors with advanced algorithms control approaches optimize charging discharge cycles. Potential advancements driven nanotechnolo... Read More
16. Assessment of Battery Electric Vehicles using the EDAS Method: A Comprehensive Evaluation of Performance and Sustainability
, 2025
The global shift toward environmentally sustainable transportation has accelerated the development and adoption of Battery Electric Vehicles (BEVs). This paper presents a comprehensive evaluation BEVs using Estimation Based on Distance from Average Solution (EDAS) method, multi-criteria decision-making (MCDM) approach that facilitates an objective systematic comparison across multiple performance parameters. assessment considers critical technical user-centric criteria, including battery capacity, driving range, top speed, acceleration (0100 km/h), charging time, overall environmental impact. Eight popular BEV modelsKia EV6, Mahindra XUV400 EV, Hyundai Kona Electric, BMW i7, Jaguar I-Pace, Mercedes-Benz EQS, Audi e-tron GT, Porsche Taycanwere analyzed EDAS method to determine their relative scores. analysis revealed Kia EV6 ranks highest, demonstrating well-balanced profile all key indicators. Conversely, recorded lowest score due trade-offs in metrics. results offer practical implications for potential consumers, manufacturers, policymakers by identifying optimal models hig... Read More
17. Intelligent Battery Management in a Hybrid Photovoltaic Using Fuzzy Logic System
joann v magsumbol, argel a bandala, alvin b culaba - Multidisciplinary Digital Publishing Institute, 2025
LiFePO4 batteries need a battery management system (BMS) to improve performance, extend their lifespan, and maintain safety by utilizing advanced monitoring, control, optimization techniques. This paper presents the design, development, implementation of an intelligent (i-BMS) that integrates real-time monitoring control batteries. The was extensively tested using multiple datasets, results show able temperature within set range, balance cell voltages, distribute energy according load prioritization. It uses fuzzy logic approach effectively manage farm requirements. Additionally, proposed method embedded three-level prioritization algorithm woven into rule allocate dynamically among essential, regular, non-essential loads.
18. A combined improved dung beetle optimization and extreme learning machine framework for precise SOC estimation
kl yao, xinyu yan, xinwei mao - Nature Portfolio, 2025
Accurate estimation of the state charge (SOC) lithium-ion batteries (LiBs) proportionally impacts efficiency battery management systems (BMS) considering dynamic and non-linear behavior LiBs. Changes in activities cathode anode materials internal resistance tend to impact capacity. When is operated at high or low temperatures under HWFET condition, capacity tends deteriorate drastically. Therefore, high-precision SOC required ensure safe stable operation. In this work, we propose a combined Improved Dung Beetle Optimization (IDBO) Extreme Learning Machine (ELM) framework for evaluate BMS. The novelty model stems from application IDBO algorithm, which incorporating Circle chaotic mapping, Golden sine strategy, Levy flight hyper-parameter optimization. This effectively resolves problems inconsistent performance instability arising randomly initialized hidden layer weights biases ELM, resulting enhanced prediction accuracy. proposed IDBO-ELM method validated context five parameters, namely, different ambient temperatures, operating conditions, materials, initial values, running time. ex... Read More
19. Expansion Force‐Based Adaptive Multistage Constant Current Fast Charging with Lithium Plating Detection for Lithium‐Ion Batteries
yudong shen, xueyuan wang, yuguang li - Wiley, 2025
Abstract The multistage constant current (MCC) charging protocol for lithiumion batteries is commonly used to balance lithium plating and time. Traditional methods depend on a predefined map without considering the feedback of subsequent selfregulation rate. To tackle this problem, an adaptive MCC method proposed, which based expansion force detect plating. By integrating experiments with simulations, results indicate that when occurs, experiences abnormal, accelerated increase. If rate reduced until ceases, decreases. Correspondingly, three thresholds, V1, V2, V3, in derivative (dF/dSOC), are identified. Utilizing these can be selfregulated. demonstrate speed increased by 50% causing irreversible proposed holds great promise integration into intelligent battery management systems, thereby enhancing performance fast charging.
20. A Novel Method of Parameter Identification for Lithium-Ion Batteries Based on Elite Opposition-Based Learning Snake Optimization
wuke li, ying xiong, shiqi zhang - Multidisciplinary Digital Publishing Institute, 2025
This paper shows that lithium-ion battery model parameters are vital for state-of-health assessment and performance optimization. Traditional evolutionary algorithms often fail to balance global local search. To address these challenges, this study proposes the Elite Opposition-Based Learning Snake Optimization (EOLSO) algorithm, which uses an elite opposition-based learning mechanism enhance diversity a non-monotonic temperature factor exploration exploitation. The algorithm is applied parameter identification of second-order RC equivalent circuit model. EOLSO outperforms some traditional optimization methods, including Gray Wolf Optimizer (GWO), Honey Badger Algorithm (HBA), Golden Jackal (GJO), Enhanced (ESO), (SO), in both standard functions HPPC experiments. experimental results demonstrate significantly SO, achieving reductions 43.83% Sum Squares Error (SSE), 30.73% Mean Absolute (MAE), 25.05% Root Square (RMSE). These findings position as promising tool modeling state estimation. It also potential applications management systems, electric vehicle energy management, other compl... Read More
Get Full Report
Access our comprehensive collection of 472 documents related to this technology
Identify Key Areas of Innovation in 2025
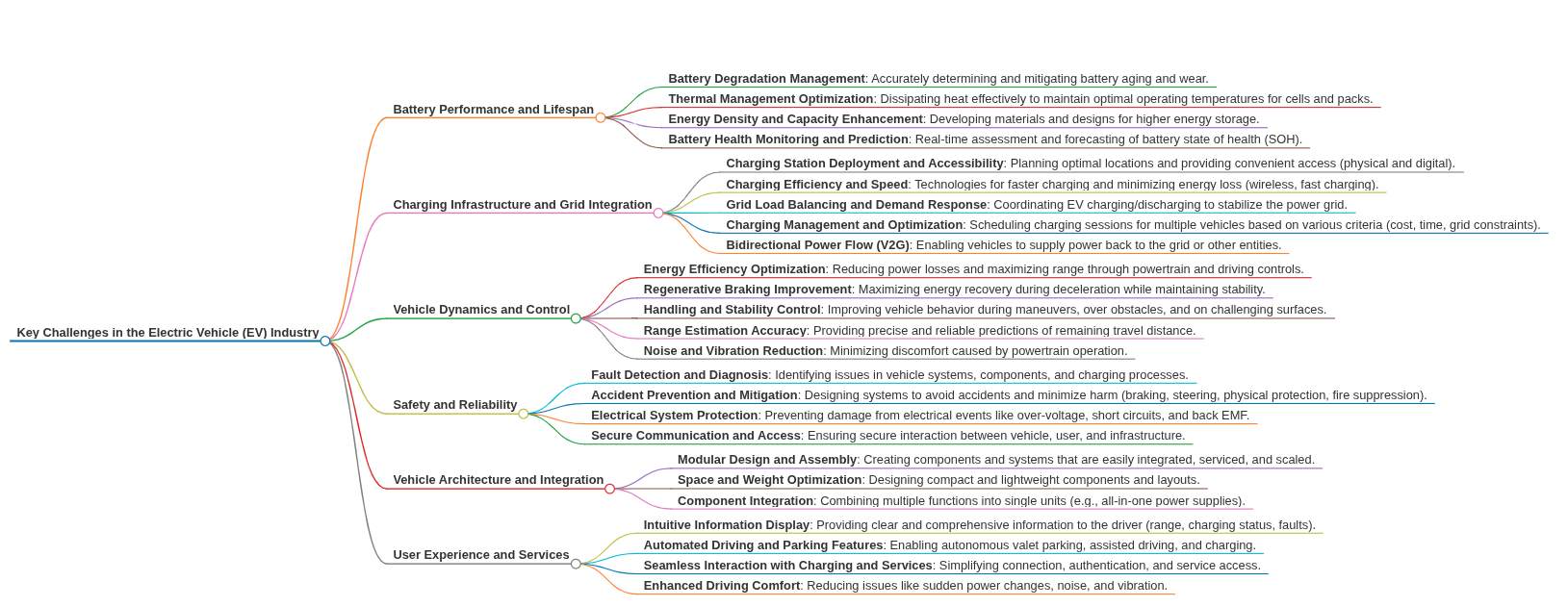