BYD's Strategies for Recycling EV Batteries
BYD's battery recycling operations process thousands of end-of-life power packs annually, with each pack containing valuable materials including lithium, iron, phosphate, and graphene. Current recycling methods achieve material recovery rates of 80-95%, but face technical barriers in separating complex compounds while maintaining the purity levels required for battery-grade materials.
The core challenge lies in developing scalable processes that can efficiently separate and purify materials while keeping recovery costs below the market price of virgin materials.
This page brings together solutions from recent research—including acid-peroxide leaching for high-purity graphene recovery, selective lithium extraction from LFP cathodes, pole core component reuse, and echelon-based battery sorting systems. These and other approaches focus on maximizing material recovery while meeting battery-grade purity requirements for closed-loop recycling.
1. Method for Disassembling and Repurposing Components from Defective Battery Pole Cores
BYD CO LTD, BYD COMPANY LTD, 2024
A recycling method for defective battery pole cores that involves disassembling and repurposing components from failed cores instead of scrapping the entire core. The method involves collecting the failed cores, expanding the pole pieces, cutting them into smaller pieces, and sorting the pieces to extract usable ones. This allows recovering and reusing pole pieces with defects like partial material loss or thickness variations. The expanded and cut pieces are then used in new battery cells. This recycles the core components instead of throwing them away, improving efficiency and reducing environmental impact compared to scrapping the entire core.
2. Lithium Recovery Process from Lithium Tert-Amylate Waste via Aqueous Dissolution and Impurity Removal
Jiangxi Ganfeng Lithium Co., Ltd., JIANGXI GANFENG LITHIUM CO LTD, 2023
A method to recover lithium from lithium tert-amylate waste material and prepare battery-grade lithium carbonate. The method involves dissolving the lithium tert-amylate waste in water, separating the insoluble tert-amyl alcohol, neutralizing the lithium hydroxide with hydrochloric acid, removing impurities, and adsorbing organics to obtain a low impurity lithium chloride solution suitable for preparing battery-grade lithium carbonate.
3. Graphene Recovery from Waste Lithium-Ion Batteries via Acid-Peroxide Leaching Process
HUIZHOU BYD BATTERY CO LTD, 2023
Recycling graphene from waste lithium-ion batteries using a simple and efficient acid-peroxide leaching process to improve the quality of the recovered graphene. The recycling method involves treating the recycled graphite from the batteries with a mixed solution of acid and hydrogen peroxide. This selectively leaches impurities and weakly oxidizes the graphite, improving purity, interlayer spacing, and delamination yield. The leached graphite is then washed and dried to obtain high-quality graphene with good conductivity and reduced defects compared to direct graphene extraction from batteries.
4. Two-Step Leaching Process for Selective Recovery of Lithium, Iron, and Phosphorus from Waste Lithium Iron Phosphate Batteries
BYD Company Limited, Shenzhen BYD Lithium Battery Co., Ltd., BYD COMPANY LTD, 2022
Method for recovering lithium, iron, and phosphorus from waste lithium iron phosphate (LFP) batteries with high selectivity, yield, and purity. The method involves a two-step leaching process to separate and regenerate the main components from the LFP waste. In step 1, lithium is selectively leached from the waste using a mixed solution of hydrochloric acid (HCl) and hydrogen peroxide (H2O2) at room temperature. This leach solution contains high lithium concentration (5-8 g/L) with low impurities (iron < 30 ppm, phosphorus < 100 ppm). In step 2, iron and phosphorus are separately leached from the LFP waste using an ammonium sulfate (NH42SO4) solution at elevated temperature (
5. Core-Shell Regeneration of Lithium Iron Phosphate Electrode via Acid-Mediated Carbon and Lithium Removal
Huizhou BYD Industrial Co., Ltd., HUIZHOU BYD INDUSTRIAL CO LTD, 2022
Regenerating lithium iron phosphate (LiFePO4) positive electrode material from waste lithium iron phosphate (LiFePO4) or lithium iron phosphate battery anode recycling. The regeneration involves dissolving away the carbon coating and surface lithium-depleted regions of the waste material using weak acid. The remaining core is then used as a seed for growing new LiFePO4 shell layers around it. This core-shell structure improves conductivity, charge/discharge capacity, and cycle life compared to the original waste material.
6. System and Method for Echelon-Based Battery Sorting Using Thickness and AC Resistance Detection
BYD CO LTD, BYD COMPANY LTD, SHENZHEN BYD LITHIUM BATTERY CO LTD, 2021
Method and system for sorting retired batteries by echelon utilization to improve efficiency and widen environmental applicability compared to traditional indoor sorting methods. The method involves detecting thickness and AC resistance of retired batteries, calculating capacity using a pre-obtained formula, and determining if the battery is qualified. This allows portable handheld tools to sort batteries outdoors without requiring specialized equipment. It avoids testing batteries with unqualified appearance, reduces tests, and improves sorting speed. The system includes a portable thickness and resistance detector connected to a data processing device that calculates capacity using a pre-obtained formula.
7. Process for Producing Low-Phosphate Lithium Solution via Acid Dissolution and Phosphate Precipitation
AUSTRALIAN NUCLEAR SCIENCE AND TECHNOLOGY ORGANISATION, ENIRGI KNOW-HOW PTE LTD, 2019
Converting lithium phosphate into a low-phosphate lithium solution suitable for making saleable lithium products like carbonate or hydroxide. The process involves dissolving lithium phosphate in acid, treating with a phosphate carrier hydroxide to precipitate phosphate, separating the phosphate, then treating the residual phosphate with a strong hydroxide base to convert it into phosphate carrier hydroxide. This allows recycling phosphate from the lithium solution for reuse. The lithium solution after phosphate removal has <10 mg/L phosphate suitable for further processing into marketable lithium products.
8. Lithium Recovery Method from Waste Lithium Iron Phosphate Batteries via Magnesium Salt Roasting and Acid Leaching
Jiangxi Ganfeng Lithium Co., Ltd., 2019
A method for recycling lithium from waste lithium iron phosphate batteries to extract high-purity lithium carbonate. The method involves dismantling the batteries, separating the lithium iron phosphate powder, roasting it with magnesium salts and oxygen to convert the iron, leaching with acid to extract lithium, removing impurities with bases, and precipitating lithium carbonate.
9. Method for Metal Recovery from Waste Lithium Battery Cathode Material via Calcination, Acid Leaching, Fluoride Extraction, and Precipitation
JIANGXI GANFENG LITHIUM CO LTD, 2017
A method for treating waste lithium battery cathode material to recover valuable metals like nickel, cobalt, manganese, and lithium from the waste. The method involves steps like calcination, acid leaching, fluoride extraction, and precipitation. The calcination step converts the battery cathode waste into oxide forms. The acid leaching extracts the metals. The fluoride extraction removes lithium and other metals as fluorides. The final precipitation separates the metals. This integrated process achieves high metal recovery, efficient extraction, and environment-friendly treatment.
Get Full Report
Access our comprehensive collection of 9 documents related to this technology
Identify Key Areas of Innovation in 2025
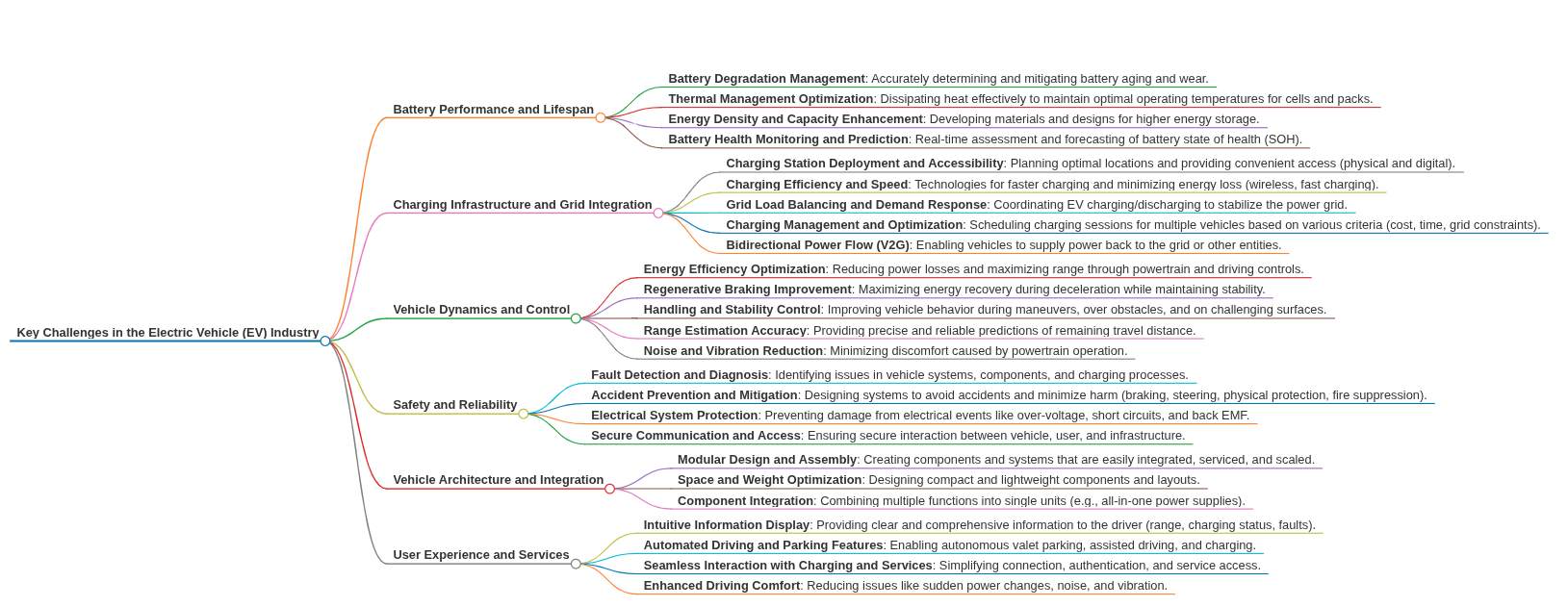