Cost Reduction in EV Battery Manufacturing
Electric vehicle battery production costs currently range from $130-150/kWh at pack level, with materials accounting for 65-80% of total costs. Despite significant cost reductions over the past decade, further optimization is needed to reach price parity with internal combustion vehicles across all segments. Manufacturing complexity and material expenses remain key barriers.
The fundamental challenge lies in reducing production costs while maintaining or improving energy density, safety, and longevity—factors that often work against cost reduction efforts.
This page brings together solutions from recent research—including modular frame designs that reduce assembly complexity, innovative busbar configurations that minimize connection points, composite materials that eliminate traditional joining methods, and streamlined cell-to-pack architectures. These and other approaches focus on practical manufacturing optimizations while maintaining critical performance and safety requirements.
1. Circular Economy Process for Producing Battery Materials from Recycled Industrial Byproducts
Hangzhou Changkai Energy Technology Co., Ltd., HANGZHOU CHANGKAI ENERGY TECHNOLOGY CO LTD, 2023
Circular economy process for producing battery materials using recycled waste from other production processes to reduce costs and environmental impact. The process involves recycling byproducts like ferrous sulfate, waste sulfuric acid, and wastewater from titanium dioxide, chemical fertilizer, and battery production. It also uses waste steam from power plants and condensate water. The recycled materials are used to make lithium iron phosphate and lithium titanate batteries. The process aims to minimize waste, energy consumption, and pollution while maximizing resource utilization.
2. Cylindrical Battery with Riveted Pole for Direct Cell Connection and Enhanced Thermal Management
Microvast Power Systems Co., Ltd., Microvast, Inc., 2023
Battery design that improves thermal management, ease of assembly, and reduces cost while improving energy density in cylindrical cells. The battery uses a riveted pole that penetrates the cover plate to connect to the cell. The riveted pole allows cell connection without separate terminals, enabling flexible cell polarity arrangement during assembly. It also improves heat dissipation compared to traditional tabs. The riveted pole reduces complexity, parts count, and cost while increasing energy density.
3. Modular Frame Design for Adjustable Battery Cell Accommodation in Vehicle Battery Packs
LG Energy Solution, Ltd., 2023
Battery module design for vehicle battery packs that can reduce manufacturing cost by using modular frames that can adjust in size to fit different numbers of battery cells. The modular frames can be lengthened or shortened to accommodate varying cell counts by coupling together.
4. Battery Cell Connector with Integrated Carrier, Weld Openings, and Flexible Film Conductor
TE Connectivity Germany GmbH, 2023
A connector for connecting battery cells in a battery pack of an electric vehicle that reduces cost and complexity compared to prior solutions. The connector has a carrier with weld openings, a cover over the openings, a contact in the carrier, a flexible film connector along an edge of the carrier, and a film conductor in the carrier that contacts the contact and film connector. The cells are connected by welding through the carrier openings.
5. Electric Vehicle Battery with Plastic Foam Encapsulation Formed In-Situ
VOLTABOX, 2023
An electric vehicle battery that is lightweight, compact, and efficient, while being easy and cost-effective to manufacture and assemble. The battery includes a plastic foam housing that is formed around the battery cells to encapsulate and protect them. This foam housing replaces traditional metal housings and eliminates the need for separate cell holders. The foam is foamed directly onto the cells and then cured in place.
6. Lithium Iron Phosphate Cathode Material Synthesis from Industrial Iron Mud via Oxidation Roasting and Acid-Soluble Filtration
HUBEI LIBAO NEW MATERIAL TECH DEVELOPMENT CO LTD, HUBEI LIBAO NEW MATERIAL TECHNOLOGY DEVELOPMENT CO LTD, 2023
Preparing lithium iron phosphate cathode material for lithium-ion batteries using industrial waste iron mud as a low-cost alternative to anhydrous iron phosphate. The method involves purifying and reacting the iron mud to make iron red, then reacting it with phosphorus, lithium, and carbon sources to produce lithium iron phosphate. The steps include oxidation roasting, acid-soluble filtration, pH adjustment, filtration, drying, and lithium iron phosphate preparation.
7. Battery Module with Slit-Integrated Bus Bar Frame for Electrode Lead Engagement
LG ENERGY SOLUTION, LTD., 2023
Battery module with minimized resistance and cost by reducing the use of bus bars to connect electrode leads. The battery module has a cell stack, a bus bar frame with slits for the electrode leads, and a bus bar. The electrode leads pass through the slits and engage each other on the bus bar instead of being individually connected. The engaged leads are welded to the bus bar. This reduces the number of bus bar plates needed and shortens the current path between adjacent electrode leads.
8. Battery Module with Friction-Welded Composite Busbars and Integrated Bonding Layer
A.F.W. Co., Ltd., 2023
Battery module for electric vehicles that reduces weight and cost compared to conventional modules. It uses friction welding to join the busbars rather than welding or bolting. The battery module has a case, battery cells inside, sensing busbars that connect the cells, and power busbars connected to the sensing busbars. The sensing and power busbars are made of a layered composite material with an aluminum outer layer and a copper inner layer that friction weld together to form a bonding layer, eliminating the need for separate welds, bolts, or connectors.
9. Method for Synthesizing Lithium Iron Phosphate Cathode Material from Iron Scale via Hydrothermal Complexation and Reduction
HUAWEI METAL MINERAL RESOURCE EFFICIENT RECYCLING UTILIZATION NATIONAL ENGINEERING RES CENTER CO LTD, HUAWEI METAL MINERAL RESOURCE EFFICIENT RECYCLING UTILIZATION NATIONAL ENGINEERING RESEARCH CENTER CO LTD, SINOSTEEL MAANSHAN GENERAL INSTITUTE OF MINING RES CO LTD, 2022
Preparing lithium iron phosphate, a cathode material for lithium batteries, using iron scale as raw material. The method involves converting iron scale into high-purity ferrous oxalate through hydrothermal complexation leaching and reduction. Then, the ferrous oxalate is used as the main raw material to prepare lithium iron phosphate. This allows utilizing iron mill waste as a high-value lithium battery component instead of low-value applications. It reduces solid waste disposal costs and provides a low-cost, high-purity iron source for lithium batteries.
10. Iron Phosphate Synthesis via Dilute Phosphoric Acid and Pig Iron Reaction
YIBIN TIANYUAN GROUP CO LTD, YIBIN TIANYUAN HAIFENG HETAI CO LTD, 2022
Low-cost production of iron phosphate for lithium-ion battery cathodes using a clean process that avoids byproducts and reduces costs compared to traditional methods. The process involves reacting dilute phosphoric acid and finely ground pig iron to form iron phosphate. This is done at a specific acid concentration, iron fineness, reaction temperature, and pH conditions to optimize the reaction. The iron phosphate is then filtered, washed, and dried. The clean process eliminates byproducts and reduces costs compared to traditional methods like ammonia or pure iron routes.
11. Dry Processing Method for Lithium Iron Phosphate Cathode Recovery from Waste Batteries
HUBEI RT ADVANCED MAT CO LTD, HUBEI RT ADVANCED MATERIALS CO LTD, 2021
A method for recovering lithium iron phosphate (LFP) cathode materials from waste LFP batteries to reduce production costs and promote circular economy. The method involves dry processing the waste LFP cathode pieces without using water. The steps are: 1) Crushing and separating the waste pieces to obtain lithium iron phosphate (LFP) electrode material and foil scraps. 2) Sintering the LFP electrode material in an inert gas at a controlled temperature and time to decompose organic matter and separate the LFP particles. 3) Mixing the sintered LFP with a dopant at an optimized ratio and calcining to form a high-performance LFP cathode material for reuse.
12. Lithium Iron Phosphate Battery with Crystalline Structure of Space Group Pnma Formed by Pressure-Assisted Synthesis
Semiconductor Energy Laboratory Co., Ltd., 2021
Lithium iron phosphate battery with enhanced power output and cost-effective manufacturing. The battery uses an active material with a specific crystalline structure made by a low-cost synthesis method. The method involves mixing lithium, phosphorus, iron compounds and water, adjusting pH, and heat treating under pressure. The resulting lithium-containing complex phosphate has a flat or columnar shape and a space group Pnma.
13. Lithium Iron Phosphate Synthesis from Waste Lithium Solution via Controlled Precursor Mixing and Thermal Processing
HUNAN CHANGYUAN LICO CO LTD, JINCHI ENERGY MAT CO LTD, JINCHI ENERGY MATERIALS CO LTD, 2020
A low-cost method to prepare lithium iron phosphate (LFP) for lithium-ion batteries using waste lithium solution as the lithium source. The method involves adding the appropriate amounts of phosphoric acid and iron source to the waste lithium solution based on the lithium concentration and molar ratio, followed by mixing, grinding, drying, and heating to produce LFP. This avoids using expensive pure lithium sources and utilizes waste lithium from battery production to reduce costs.
14. Multi-Core Lithium-Ion Battery with Sealed Enclosure, Deflectable Pressure Release Domes, and Flame Arrestors
Cadenza Innovation, Inc., 2020
A multi-core lithium-ion battery with improved safety and reduced manufacturing costs. The battery has a sealed enclosure that houses multiple lithium-ion cores, along with features like deflectable pressure release domes, external fuses, and flame arrestors to prevent cascading failures and contain any failures to a single cell. The battery also uses endothermic materials and kinetic energy absorbing supports to mitigate thermal runaway and impact risks.
15. Lithium-Ion Battery with Pressure-Activated Electric Disconnects and Venting Casing
Cadenza Innovation, Inc., 2019
Lithium-ion battery design with improved safety and reduced manufacturing costs. The design uses features like pressure triggered electric disconnects and venting to prevent cascading failures and thermal runaway. The battery casing has a bottom plate that can separate from the battery components when pressure exceeds a threshold. This disconnects the battery. The casing also has a vent structure to release pressure.
16. Method for Synthesizing Lithium Battery Electrode Materials from Vanadium Extraction Waste
Northeastern University, 2018
A method for preparing lithium battery electrode materials like lithium iron phosphate and lithium titanate using vanadium extraction waste to reduce cost and environmental impact. The method involves extracting vanadium from slag to recover the valuable metal, then using the leftover waste as a precursor for lithium battery electrode materials. The steps involve leaching vanadium from slag, precipitating the vanadium, converting it to a lithium precursor, and synthesizing the lithium battery electrode material from the vanadium precursor. This utilizes the vanadium slag as a resource instead of dumping it, and reduces the need for expensive and impurity-containing lithium precursors.
17. Solvothermal Apparatus with Flash Evaporation and Solid-Liquid Separation for Solvent and Water Recycling
Jiangsu Huadong Institute of Li-Ion Battery Co., L td., Tsinghua University, 2017
A solvothermal apparatus for making lithium iron phosphate with improved resource efficiency and reduced production costs. The apparatus allows recycling of organic solvent and water from the solvothermal reaction. The recycling is done using a flash evaporation unit and a solid-liquid separation unit. The flash evaporation unit removes water from the solvent-rich waste stream. The separation unit separates the solid lithium iron phosphate from the solvent and water. The separated solvent is recycled back to the solvothermal reaction. The water and remaining solvent are recycled as washing liquid to clean the lithium iron phosphate. This reduces fresh solvent and water requirements during continuous production.
18. Closed Loop System for Solvothermal Synthesis of Lithium Iron Phosphate with Integrated Solvent and Lithium Recycling
JIANGSU HUADONG INSTITUTE OF LI-ION BATTERY CO LTD, TSINGHUA UNIVERSITY, 2016
Solvothermal synthesis of lithium iron phosphate (LFP) cathode material for lithium-ion batteries with reduced waste and cost compared to traditional methods. The process involves using a closed loop system with recycling of lithium and organic solvents from the reaction. This prevents waste generation and allows reuse of solvents instead of distillation. The closed loop includes a product preparation unit with reaction vessel, filter, and backflushing. The waste treatment unit has a flash separator and solid-liquid separator. The product unit feeds into the waste unit, with the flash separator recycling the solvents and the solid-liquid separator recycling the lithium. This reduces fresh solvent and lithium consumption compared to traditional solvothermal synthesis.
Get Full Report
Access our comprehensive collection of 18 documents related to this technology
Identify Key Areas of Innovation in 2025
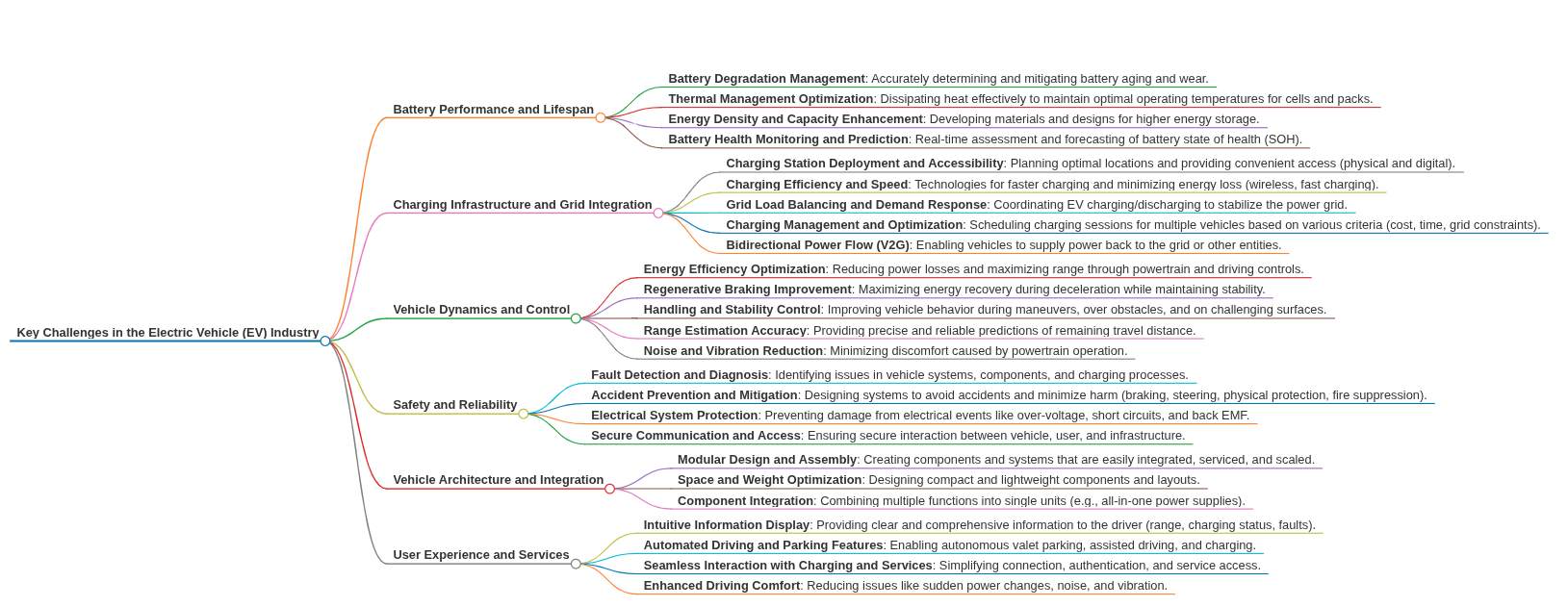