Monitoring EV Battery Temperature Using Thermal Imaging
Electric vehicle battery packs operate with cell temperatures ranging from -20°C to 60°C, while thermal events can spike locally to over 150°C within seconds. Traditional contact sensors, spaced 5-10cm apart in modern packs, can miss critical temperature gradients and provide delayed detection of thermal anomalies across the thousands of cells in a typical EV battery system.
The core challenge lies in achieving comprehensive thermal monitoring of densely packed cells without compromising the battery's energy density or adding significant complexity to the pack assembly.
This page brings together solutions from recent research—including infrared matrix sensors with deflection optics, distributed IR sensor meshes, and non-contact temperature mapping systems. These and other approaches focus on early detection of thermal events while maintaining practical implementation in high-volume EV manufacturing.
TABLE OF CONTENTS
1. Infrared Sensor Arrays and Meshes Embedded in Battery Packs
Thermal management in electric vehicle battery systems presents unique challenges due to the high thermal sensitivity of lithium-based chemistries. While traditional battery management systems employ discrete temperature sensors at select locations, they fundamentally lack the spatial resolution needed to detect localized hot spots or evolving thermal anomalies at the individual cell level.
An innovative infrared field evolution monitoring system addresses this limitation through a distributed array of infrared thermal imaging cameras arranged in a dot-matrix configuration along the internal walls of the battery compartment. This configuration enables real-time, high-resolution thermal field mapping of each battery cell, significantly advancing the granularity and responsiveness of thermal monitoring.
The system's architecture centers on a rectangular grid imaging net that divides the battery compartment into defined detection zones, enhancing spatial fidelity of temperature measurements. Battery cells mount using a beam-and-hanger configuration that ensures consistent alignment while minimizing obstructions to the infrared sensors. The imaging system works in concert with an integrated thermal regulation mechanism comprising electric heating wires and heat dissipation modules that dynamically adjust cell temperatures based on real-time data. A central control unit interfaces with a cloud platform via GPRS, enabling remote diagnostics and adaptive control strategies.
This intelligent thermal monitoring architecture supports predictive maintenance and operational safety across both individual vehicles and fleets. The fine-grained thermal monitoring capability detects cell-level abnormalities early, substantially reducing thermal runaway risks. The non-contact nature of infrared sensing ensures monitoring without operational interference, while cloud-based analytics integration enables data-driven thermal management strategies that adapt to varying usage patterns and environmental conditions.
A complementary approach focuses on compact, embedded thermal sensors for real-time monitoring. This system utilizes a thermistor-based temperature monitoring unit housed in a mounting slot above the battery, with the thermistor protruding slightly to maintain direct thermal contact with the battery surface. This cost-effective solution includes a tamper-detection mechanism that triggers alerts via a 4G communication module if the unit is removed or tampered with. While offering less spatial detail than infrared imaging systems, this approach provides essential safety monitoring when infrastructure or cost constraints limit the deployment of complex sensing arrays.
2. Hybrid Systems Combining Infrared Imaging with Traditional Sensors
The limitations of traditional battery management systems become evident in their reliance on discrete temperature sensors placed at limited points throughout the battery pack. This approach creates significant blind spots, as only a subset of cells undergoes direct measurement while the thermal state of remaining cells must be inferred or remains unmonitored entirely.
A hybrid temperature detection architecture addresses this fundamental limitation by integrating infrared thermal imaging with real-time sensor data from selected reference cells. The infrared system captures comprehensive thermal images of the battery pack, while actual sensor readings from reference cells serve as calibration points. A computing module correlates this combined data to estimate the temperature of each individual cell with high accuracy. This hybrid approach eliminates traditional monitoring blind spots, enhances early fault detection capabilities, and supports modular scalability across various pack configurations.
Battery failure modes such as high internal resistance, pole overheating, or casing leakage often escape detection by conventional ambient or pole temperature probes. An integrated battery temperature monitoring system tackles these challenges by combining a centralized server architecture with distributed sensing components that include infrared cameras and local temperature detection devices. By utilizing non-contact infrared imaging alongside direct sensor data, the system simultaneously monitors multiple thermal zones including battery poles, casing surfaces, and environmental conditions. The architecture aggregates data in real time via a power monitoring server and high-frequency switching power supply, ensuring uninterrupted operation and early anomaly detection across large-scale battery arrays.
Physical deformation represents another critical failure mode that traditional thermal monitoring cannot detect. A mobile real-time monitoring device integrates optical and thermal monitoring through a micro camera, infrared thermometer, and lighting system mounted on a movable rail above the battery pack. Beyond temperature measurement, this system detects physical deformations such as battery bulging—an early indicator of mechanical failure. The rail-mounted design allows the device to traverse multiple cells, capturing high-resolution visual and thermal data. Its autonomous operation, powered by a built-in rechargeable battery, enables continuous inspection without human intervention, significantly improving safety monitoring in high-density EV battery configurations.
3. Optical and Photonic Techniques for Remote Temperature Sensing
Remote temperature sensing for EV battery terminals faces a fundamental challenge: traditional embedded sensors compromise the structural and electrical integrity of the terminals. Conventional methods that integrate nitinol wires or phase-change materials reduce the terminal's cross-sectional area, increasing resistance and generating additional ohmic heating—precisely the phenomenon they aim to monitor.
A novel non-invasive optical and magnetic sensing patch applied directly to the terminal surface overcomes this limitation. With less than 10% of the terminal's thermal mass, this patch exhibits temperature-dependent optical or magnetic properties that an external circuit detects using photodetectors or eddy current-based magnetic field sensors. The system remains electrically isolated from the terminal while ensuring rapid thermal response without increasing the system time constant. This approach maintains terminal integrity while providing accurate temperature monitoring without intrusive modifications.
Wireless power transfer systems in EVs introduce additional thermal monitoring challenges, particularly foreign object detection in the charging zone. Metallic or ferromagnetic objects can absorb electromagnetic energy and heat to hazardous temperatures. An infrared-based foreign object detection system monitors thermal emissions from the critical space between power transfer coils. Rather than relying on absolute temperature values, the system analyzes time-differentiated thermal signals correlated with changes in magnetic field exposure. This approach detects small, low-emissivity objects by analyzing their dynamic thermal behavior, enhancing safety without requiring extensive sensor calibration. The flexible implementation—via hardware, software, or firmware—makes it compatible with various IR sensor configurations and EV charging environments.
For battery-level thermal monitoring, temperature-sensitive paint coupled with AI-driven imaging offers continuous, non-destructive monitoring of lithium-ion batteries. The battery casing receives a specialized paint coating that changes color in response to temperature elevations. A thermal imaging system captures these changes in real time, while a neural network analyzes the data alongside voltage and current readings to detect early signs of thermal anomalies. This system enables autonomous, predictive safety monitoring with minimal data requirements, making it suitable for integration into EVs and stationary energy storage systems where proactive thermal management is essential.
4. Thermal Imaging with Machine Learning or Predictive Analytics
Electric vehicle battery systems exhibit particular sensitivity to thermal fluctuations that can trigger performance degradation or catastrophic failures. Traditional monitoring approaches using contact-based sensors or RF-based techniques suffer from invasive installation requirements and environmental interference susceptibility.
The non-contact thermal imaging system with predictive maintenance introduces a vision-based approach using thermal cameras to continuously monitor battery cell temperatures without physical integration. The system's core innovation lies in its artificial neural network (ANN) that performs real-time thermal pattern recognition, enabling proactive detection of anomalies that precede failure events. Thermal images undergo preprocessing via MATLAB to enhance feature extraction before the trained ANN classifies deviations from normal thermal behavior. These classifications benchmark against safe operating temperature ranges for charging, discharging, and optimal performance. When anomalies appear, the system sends alerts via an ESP32 microcontroller and triggers alarms through an Arduino interface.
This ANN-driven approach eliminates physical contact requirements while introducing sophisticated predictive maintenance capabilities. The ANN-based defect classification and alert mechanism facilitates early intervention, substantially reducing battery damage risks and enhancing vehicle safety. The system operates autonomously, executing scheduled inspections based on configurable parameters, allowing continuous battery health assessment without human oversight. Unlike RF-based solutions, it maintains resilience against environmental factors such as moisture or electromagnetic interference. The machine learning core can undergo retraining and adaptation to different battery chemistries and configurations, creating a scalable and adaptable monitoring solution applicable across various EV platforms.
While not centered on machine learning, a complementary thermal management system integrates real-time temperature monitoring with automatic fire suppression. The automatic fire extinguishing module responds rapidly to abnormal thermal conditions, providing drivers additional evacuation time during emergencies. This solution enhances thermal efficiency by combining air-cooled and liquid-cooled heat dissipation units into a unified architecture that extends component lifespan and improves overall safety in EV applications.
5. Temperature Monitoring with Mobile or Mechanically Scanning Imaging Systems
Static thermal sensors fundamentally limit detection capabilities for localized heating events in battery packs. Mobile or mechanically scanning thermal imaging systems overcome these limitations through dynamic, non-contact temperature monitoring approaches.
One innovative system employs a traversing mechanism mounted above the battery stack, positioning an infrared thermal imager below on a slidable rail. This configuration enables horizontal movement across the battery surface, capturing high-resolution thermal profiles in real time. The slidable infrared scanning system significantly enhances spatial coverage and resolution compared to fixed sensors, enabling early detection of thermal anomalies that could trigger thermal runaway or accelerate cell degradation.
Pre-deployment quality control represents another critical application area for mobile thermal imaging. A specialized system for lithium battery inspection integrates a motor-driven mechanical assembly with rotating shafts, pulleys, and belts to maneuver a thermal imaging sensor across battery surfaces. Housed within a structural frame with a locking mechanism for operational stability, the motorized pulley-based scanning system automates precise thermal monitoring during manufacturing. This approach addresses the fundamental limitations of single-point temperature detection, which frequently misses subtle faults or localized hot spots. The system's complete surface coverage and consistent data acquisition capabilities significantly improve defect identification before batteries enter service, enhancing both safety and manufacturing yield.
The mechanical mobility in both systems dramatically improves reliability and granularity of battery temperature monitoring. By incorporating traversing or rotational mechanics, these designs offer scalable and adaptable solutions for modern battery management systems, particularly in high-density EV battery configurations where thermal gradients can develop rapidly and unpredictably.
6. Distributed Sensor Networks with Dedicated Controllers
Conventional thermal management systems for EV batteries typically treat the pack as a homogeneous unit, resulting in inefficient cooling when dealing with localized hot spots or uneven temperature distributions. This approach fails to address the fundamental challenge of detecting and controlling temperature variations at the cellular level.
A novel distributed sensing solution integrates a flexible conductive composite film embedded with multiple temperature sensors, conformally applied over the battery surface. These distributed sensors enable real-time, point-level temperature tracking and feed data to a centralized control module that actuates an electronically controlled injector system for dynamic temperature management. The system incorporates an alarm mechanism that proactively alerts drivers when thermal thresholds approach critical levels.
The system's closed-loop architecture integrates sensing, control, and actuation within a unified framework. Unlike bulk temperature monitoring approaches, this design provides localized temperature monitoring and precise thermal regulation. The execution module dynamically adjusts placement and flow rate of thermal control agents via the injector system, ensuring uniform temperature distribution. The flexible composite film maintains sensor stability under mechanical and thermal stress, ensuring long-term reliability. This configuration mitigates thermal runaway risks while extending battery life by reducing internal resistance variations and promoting uniform cell aging.
A complementary innovation embeds thermal sensing capabilities directly within the battery enclosure, eliminating external sensor requirements. This solution features a real-time temperature monitoring mechanism integrated into a collection chamber above the battery pack. The design incorporates a heat-conducting belt and heat-absorbing plate that channel thermal energy to a centrally located sensor, ensuring accurate temperature acquisition. A data collector mounted adjacent to the sensor transmits real-time information to the vehicle's control system. The protective shell houses all components for environmental durability, while a movable mechanism allows maintenance access or dynamic adjustment.
This embedded approach achieves structural integration that enables continuous temperature tracking without altering battery layout. The modular design simplifies implementation and maintenance across various battery chemistries and configurations. The improved thermal conductivity through the heat-conducting interface ensures responsive and accurate sensing for early thermal anomaly detection. By facilitating real-time data acquisition and seamless integration with vehicle control systems, this solution enhances both safety and reliability of EV battery operations.
7. Thermal Modeling and Estimation Using Equivalent Networks or Algorithms
Electric vehicle batteries generate and dissipate heat non-uniformly during operation, creating internal temperature gradients that significantly impact safety and performance. While surface temperatures can be directly measured, internal temperatures remain inaccessible in practical applications. Traditional methods like electrochemical impedance spectroscopy prove impractical for onboard use, while empirical surface-to-core models lack the physical foundation to capture complex thermal behaviors.
An equivalent thermal network (ETN) model addresses these limitations by integrating multiple heat transfer paths and dynamically accounting for structural asymmetries within the battery. The model calibrates thermal parameters using offline testing data combined with multi-objective optimization, enabling high-fidelity estimation of internal temperatures during real-time operation. The ETN model's physically grounded design incorporates thermal interactions between battery surface and cooling plate, accurately representing non-uniform heat flow. Real-time estimations utilize a state-space representation driven by operational inputs including current, voltage, and ambient temperature. A feedback mechanism, typically a Luenberger observer, refines internal state predictions for robust performance under transient conditions.
This real-time internal temperature estimation framework embeds directly in vehicle control hardware and integrates with the battery management system, facilitating predictive thermal management strategies. The approach enhances safety by enabling the BMS to initiate mitigation actions like current derating or thermal alerts based on accurate internal temperature data. The model maintains functionality even during sensor failure, improving overall system reliability.
Hybrid electric vehicles with distributed battery architectures, such as four-wheel-drive systems, present additional thermal modeling complexities. Traditional centralized BMS configurations cannot adequately address spatial variation in thermal behavior or the influence of fuel-assisted drive units. Contact-based sensors further complicate matters through delayed response times caused by thermal inertia. A multi-point infrared temperature correction method overcomes these challenges using non-contact infrared sensors to monitor temperature across multiple vehicle locations. This approach captures spatially resolved temperature data in real time, significantly reducing latency and improving thermal modeling accuracy under dynamic driving conditions.
The infrared-based solution dynamically updates the BMS thermal model using real-time data from multiple thermal zones. This enables precise control over battery charging and discharging, particularly during transient or low-speed operations when thermal gradients become most pronounced. The infrared-based multi-point temperature detection and correction system enhances battery safety and performance while supporting the scalability required for modern HEVs. Its non-invasive nature reduces sensor wear and maintenance requirements, making it practical and durable for long-term deployment in distributed thermal management architectures.
8. Integrated Cooling Control Based on Thermal Imaging Feedback
Lithium-ion batteries in electric vehicles face significant risks from thermal abuse conditions such as overcharging or internal short circuits. Traditional monitoring systems rely on fixed-point sensors and threshold-based alarms, creating inherent response delays and failing to detect localized thermal anomalies before they propagate.
The thermal imaging-based monitoring system transforms this paradigm by integrating real-time infrared image acquisition with advanced image processing techniques. By analyzing spatial distribution, size, and temporal evolution of high-temperature zones, the system detects abnormal heating patterns that precede thermal runaway. This proactive approach allows dynamic cooling system adjustment based on actual thermal behavior rather than static thresholds, dramatically enhancing thermal management responsiveness and precision.
The system extracts and analyzes thermal features using grayscale conversion and morphological operations to isolate critical heat zones. Processed thermal images undergo comparison against predefined alarm thresholds, enabling distinction between different failure modes based on heat pattern characteristics. This thermal feedback integration into the cooling control loop ensures that anomalies trigger localized cooling responses rather than system-wide performance reductions. The targeted intervention improves reliability while optimizing energy efficiency by preventing unnecessary cooling of unaffected cells.
For comprehensive surface monitoring, the thermal characteristic analysis system provides non-contact, real-time temperature distribution monitoring across lithium-ion batteries during both charging and discharging cycles. Unlike thermocouple-based methods with limited discrete data points, this system generates high-resolution temperature maps using infrared thermal imaging. These maps feed directly into a control logic module that autonomously adjusts charging and discharging parameters when anomalies appear. The real-time feedback loop initiates protective actions—such as power reduction or system shutdown—before thermal thresholds reach critical levels.
The integration of temperature visualization with automated control mechanisms advances battery safety and performance monitoring. The high-fidelity thermal data supports immediate operational decisions while contributing to long-term battery design optimization. By eliminating physical contact sensors, the system simplifies installation and reduces battery surface damage risks during integration. The real-time, full-surface thermal feedback loop forms a foundational element in intelligent cooling control strategies for next-generation EV batteries.
9. Gas and Multi-Parameter Sensing for Thermal Runaway Detection
Conventional electric vehicle battery monitoring systems primarily rely on voltage and temperature sensors, which often fail to detect early thermal runaway precursors. This fundamental limitation results in delayed response and increased thermal propagation risk.
A sophisticated multimodal sensing architecture addresses this gap by integrating voltage, temperature, hydrogen gas, and infrared sensors within each battery module. This comprehensive approach enables predictive detection by identifying abnormal gas emissions and thermal radiation patterns before critical thresholds trigger. The hierarchical monitoring framework—comprising Cell Monitoring Units, Battery Management System, and optional cloud-based control—facilitates real-time analysis and fault isolation. The system's most innovative aspect involves IR dissimilarity scoring for spatial thermal anomaly detection, enabling precise fault identification in early stages. Active relays provide immediate electrical isolation of affected modules, substantially enhancing safety by preventing thermal propagation throughout the pack.
Battery deformation represents another critical failure mode that traditional monitoring systems cannot effectively detect. A cloud-connected IoT framework addresses this limitation through multiple sensing modalities. The system incorporates grayscale imaging to monitor volumetric changes, outer wall temperature sensors for thermal analysis, and gas sensors to detect hazardous emissions. A centralized analysis server computes a safety impact coefficient based on these parameters and issues proactive alerts through an early warning module. The diverse sensor data integration enables holistic safety assessment, while cloud analytics facilitates fleet-wide monitoring and predictive maintenance. The battery volume acquisition and analysis module provides non-invasive physical deformation detection—a critical thermal runaway precursor that conventional systems miss entirely.
Internal battery faults, particularly those caused by lithium dendrite formation and internal short circuits, create localized thermal events that surface-mounted sensors cannot reliably detect. A multi-point temperature sensor array system targets this challenge by collecting distributed temperature data across battery surfaces or interiors. The system applies thermal modeling algorithms to simulate internal heat generation patterns and identify abnormal hotspots. A prediction processing unit estimates thermal runaway probability and calculates battery state of health in real time. The thermal distribution-based prediction method provides high-resolution internal anomaly visibility, enabling preemptive action before catastrophic failure occurs. This approach improves diagnostic accuracy while maintaining seamless integration with existing BMS platforms.
Get Full Report
Access our comprehensive collection of 69 documents related to this technology
Identify Key Areas of Innovation in 2025
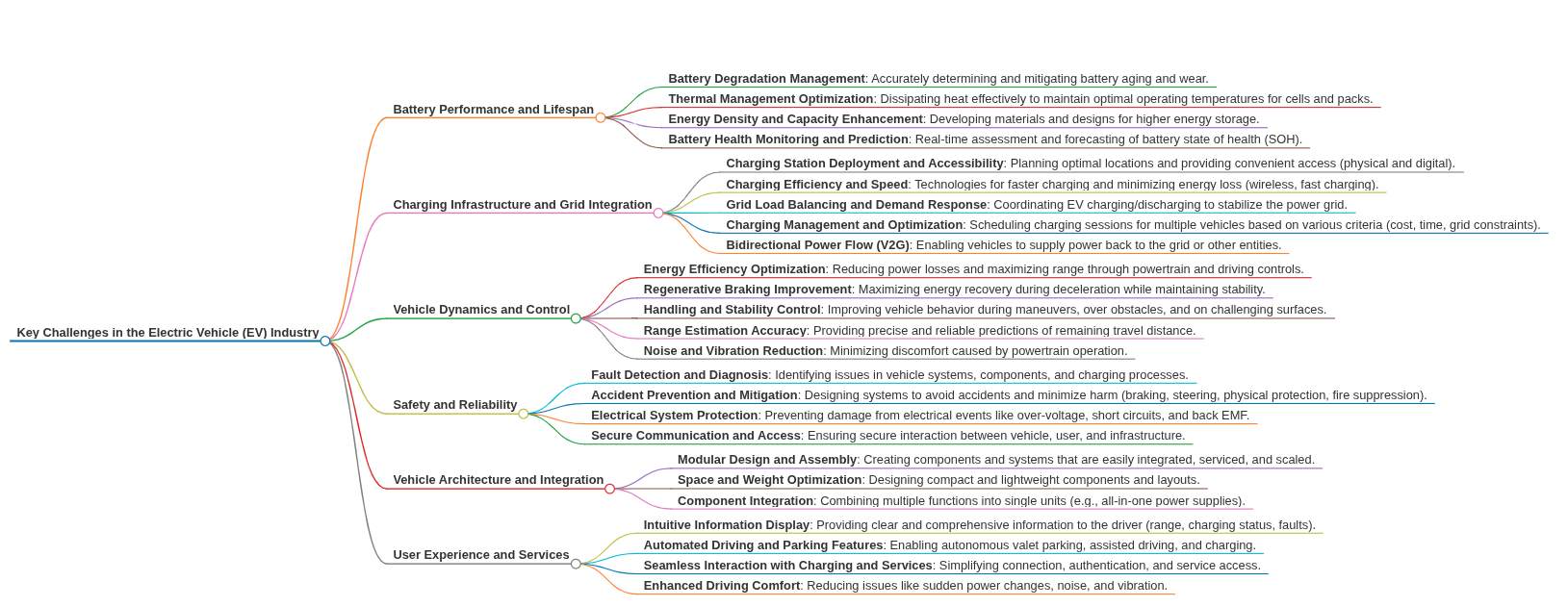