Lithium Ion Battery Venting Design for EV Safety
Electric vehicle battery thermal events pose significant engineering challenges, with cell temperatures potentially exceeding 150°C and pressure buildups reaching critical levels within milliseconds. During thermal runaway, a single 100Ah cell can release up to 2L of hot gases containing fluoride compounds, creating risks to both vehicle components and occupants.
The fundamental challenge lies in rapidly detecting and controlling gas releases while simultaneously preventing thermal propagation between cells and protecting sensitive electronic components from exposure to high-temperature, corrosive gases.
This page brings together solutions from recent research—including specialized vent shields for component protection, thermally-activated compartment ventilation systems, gas flow path engineering, and syntactic foam barriers for cell isolation. These and other approaches focus on implementing practical safety measures that can be integrated into existing EV battery architectures while meeting space and weight constraints.
TABLE OF CONTENTS
1. Gas Flow Path Engineering and Manifolds for Directed Venting
The integrity of electric vehicle battery systems depends critically on managing gas generation during thermal events. Traditional venting methods like burst discs and single-use membranes provide immediate pressure relief but lack reversibility and diagnostic capabilities.
Recent innovations have addressed these limitations through more sophisticated approaches. A reversibly operable venting device utilizes a magnetically constrained piston that lifts when internal pressure exceeds predetermined thresholds, creating a gas flow path. The magnetic coupling automatically reseals the system once pressure normalizes, enabling multiple venting cycles without component replacement while providing valuable post-event diagnostic data.
The management of gas after venting presents additional challenges. Direct expulsion of hot gases into ambient air creates significant fire risks. To mitigate this hazard, engineers have developed a venting channel formed by a cover element integrated into battery housings. This design guides gases through curved, laterally offset paths that extend both distance and time before environmental exposure. The channel incorporates ramparts that induce turbulence and enhance heat transfer to adjacent cooling surfaces, while a burst membrane at the entry point maintains system sealing during normal operation.
Structural integration of venting mechanisms has advanced through vented cell holder systems that incorporate gas management directly into the mechanical architecture of battery packs. These multi-tray configurations channel gases from failing cells through dedicated internal passages to centralized pressure-relief valves. This approach simultaneously provides mechanical cell support while creating isolated gas flow paths that direct hot gases away from adjacent components, enhancing both thermal safety and serviceability.
Further refinements include guided venting architectures that extend gas flow paths from cell chambers through dedicated passages into cooling plate-coupled guiding channels. By forcing gases to traverse longer routes before system exit, these designs significantly enhance heat dissipation while directing exhaust away from passengers and sensitive components. This approach is particularly valuable for underfloor vehicle installations where spatial constraints and proximity to the passenger compartment create additional safety considerations.
2. Thermally or Pressure-Activated Venting Devices and Valves
The reliable detection and management of gas discharge events in battery systems requires specialized venting devices that respond to specific thermal and pressure conditions. Current approaches range from passive mechanical systems to sophisticated sensor-integrated solutions.
Thermal fuses integrated within gas guide paths offer a passive yet effective monitoring solution. Traditional detection methods often rely on expensive sensors that remain inactive until failure occurs, and frequently misinterpret fuse activation as simple disconnection. An integrated gas-triggered thermal fuse mechanism addresses these limitations by positioning thermal fuses in dedicated sub-paths of gas guide channels. This configuration allows fuses to detect elevated temperatures without direct exposure to high-pressure gas, enabling passive event-driven monitoring without compromising system integrity. The design incorporates redundant, non-temperature-sensitive power lines to maintain detection circuit functionality even during thermal events.
Pressure-activated valves in laminated battery housings present unique engineering challenges, requiring precise balance between secure sealing and reliable venting. A precision-controlled venting mechanism embedded directly into the joined edge portion of battery housings achieves this balance through tightly controlled helium leakage rates and ultra-smooth contact surfaces (≤1 µm). This precise engineering ensures predictable valve behavior, releasing gas only under specific pressure conditions while maintaining environmental sealing during normal operation. The design's reliance on defined tolerances rather than complex components supports high-volume manufacturing requirements.
For managing extreme thermal runaway conditions, more comprehensive systems combine multiple technologies. A thermodynamic buffering architecture integrates lithium-ion battery packs with metal-air battery packs to create thermal sinks for hot gas discharge. This system uses pressure and temperature sensors to control a series of valves that dynamically manage gas flow paths, directing hot gases through metal-air cells for cooling before environmental release. This approach not only delays gas discharge and reduces gas temperature but significantly lowers ignition risk upon contact with atmospheric oxygen, enhancing both occupant and first responder safety.
3. Gas Shields, Baffles, and Deflectors for Component Protection
Protecting adjacent components from the effects of high-temperature gas ejection during thermal runaway requires specialized structural elements that shield, redirect, and cool these emissions. The effectiveness of these protective systems depends on their integration with both thermal management and structural elements of the battery assembly.
A venting channel with integrated cooling pathways represents a comprehensive approach to component protection. This structure directs gas away from battery cells while actively dissipating heat through cooling channels that surround the vent path. The cooling fluid circulates without mixing with exhaust gases, maintaining thermal uniformity throughout the system. Constructed from extruded aluminum profiles with sealed end plates, this design balances manufacturing simplicity with enhanced safety and maintenance efficiency.
Component-level protection can be achieved through a gas channel combined with an isolating sheet positioned above battery cell terminals. The isolating sheet contains strategically placed rupture zones that open selectively when cells experience overpressure, directing gas into a shared venting duct while maintaining electrical isolation of unaffected cells. This architecture prevents gas propagation between modules while functioning as a structural support element, reducing overall component complexity. Hollow beam structures along the gas path extend the discharge route, promoting temperature and pressure reduction before final gas ejection.
For rapid gas evacuation during thermal events, a gas venting unit with a rupture-activated plate cover provides a passive yet effective solution. The plate cover seals the gas inlet during normal operation but ruptures at predefined pressure thresholds, channeling gases through designated outlets. This mechanism eliminates dependence on sensors or electronics, offering a scalable and fail-safe approach for high-capacity battery packs.
Alignment between cell-level venting mechanisms and thermal management components further enhances protection through a battery cell with a pressure relief mechanism aligned to a relief area in the thermal management component. This configuration ensures directional emission ejection through predefined paths, using limiters and deformation gaps to minimize risk to adjacent structures. The dual-function design combines thermal regulation with emission control in a compact, scalable package suitable for multi-cell configurations.
4. Gas Cooling and Quenching Systems
The extreme temperatures of gases released during thermal runaway events (often exceeding 600°C) necessitate specialized cooling and quenching systems to reduce thermal hazards. These systems employ various mechanisms to absorb heat energy and reduce gas temperatures before environmental release.
Repurposing existing battery components for thermal management represents an innovative approach to this challenge. A metal-air battery pack system utilizes these cells as both energy storage devices and thermal sinks during gas release events. When sensors detect a thermal event, valves redirect hot gases through metal-air cells, where the substantial thermal mass absorbs excess heat before environmental release. This dual-functionality maximizes component utility while minimizing the risk of gas ignition outside the battery enclosure.
Vehicle structural elements can also contribute to thermal management through a gas duct system integrated between the traction battery and the vehicle's longitudinal sills. This approach channels gas emissions away from critical components and passenger areas using sealed battery modules and pressure-sensitive bursting elements that activate only when necessary. Heat-resistant deflection plates guide gas flow and shield adjacent components, effectively embedding the quenching system within the existing chassis structure without compromising vehicle integrity or space utilization.
The gas flow path itself can be engineered for cooling through a venting channel formed by a cover element mounted outside the battery housing. This design creates a non-linear path that forces gases to travel laterally before reaching exit points, extending residence time and enhancing heat transfer to channel walls. A rampart within the channel induces turbulence that further facilitates cooling, while an adjacent cooling plate enhances thermal dissipation. This passive cooling approach requires no active control mechanisms yet significantly reduces ignition risk at exit points.
Compact isolation and quenching can be achieved through a sealed airbag-based safety valve containing flame-retardant, heat-absorbing materials. This valve separates internal battery gases from external oxygen during venting events, with its multi-layered structure absorbing heat while preventing oxygen ingress that could trigger secondary ignition. Integrated pressure sensors enable precise activation under critical conditions, maintaining battery integrity while providing both thermal and chemical isolation.
5. Cell Isolation Using Thermal Barriers and Insulating Materials
Preventing thermal propagation between cells represents a critical safety requirement for EV battery systems. Advanced thermal barriers and insulating materials create protective boundaries that contain thermal events and prevent system-wide failures.
Pouch-type lithium-ion cells present particular challenges due to their flexible aluminum-polymer laminate housing, which can allow harmful gas leakage during thermal events. A frame-based cell isolation architecture addresses this through vertically stacked frames containing upper and lower cooling plates that form independent cooling flow paths. The physical separation between battery compartments and cooling ducts is reinforced by interlocking features such as convex portions and grooves that dynamically tighten under internal gas pressure, creating self-sealing barriers that prevent gas intrusion into cooling systems.
Material innovation plays a crucial role in thermal isolation, exemplified by a silicone-based syntactic foam barrier specifically engineered for battery applications. This material combines a crosslinkable silicone matrix with hollow borosilicate glass beads to provide both thermal insulation and structural support. Unlike conventional foams, it maintains resilience under compression and uniformity during curing, minimizing manufacturing defects. The addition of flame-retardant fillers enhances fire resistance, while compatibility with multi-component RTV systems enables both injection molding and pre-formed application methods.
Active protection systems complement passive barriers through a dual-function temperature control and fire suppression system that circulates cooling fluid through dedicated lines connected to individual cells. A key innovation is the integration of check valves that regulate flow direction and enable targeted fluid redirection during fire events. When thermal incidents are detected through predefined safety sections or sensor feedback, the system redirects cooling fluid specifically to affected zones, suppressing fires at their source without requiring separate extinguishing components.
6. Use of Inert Gases or Oxygen Displacement for Fire Suppression
Oxygen displacement represents one of the most effective strategies for suppressing battery fires, as thermal runaway reactions can continue even in the absence of external oxygen. Inert gas systems provide rapid intervention capabilities that complement other safety mechanisms.
A self-inflating nitrogen deployment mechanism integrates a gas-permeable nitrogen-release bag within battery enclosures to respond rapidly to thermal anomalies. Upon detection of thermal events, the system deploys nitrogen gas to cool the battery pack and displace oxygen, reducing fire risk. The controller coordinates multiple actions: activating the nitrogen bag, gradually decelerating the vehicle, shutting down the battery system, and issuing visual and audible alerts. A one-way vent tube expels internal gases while preventing external contaminant ingress, enabling autonomous fire suppression without compromising vehicle control or electrical integrity.
For lithium metal solid-state batteries, maintaining a non-flammable internal environment requires continuous gas composition management. A real-time inert atmosphere regulation system employs a closed-loop gas circulation approach with air valves, circulation fans, and a gas control unit capable of dynamic composition adjustment. The system incorporates a molecular sieve for moisture removal, copper catalyst-based oxygen scavenging, and harmful gas adsorption. During thermal events, sensors trigger simultaneous activation of deoxidation units while introducing inert gases such as ammonia and nitrogen mixed with cooled air to maintain a stable atmosphere, adapting to various battery operational states without introducing additional thermal stress.
7. Gas Detection and Monitoring Systems
Early detection of gas generation provides critical lead time for intervention before thermal runaway escalates to catastrophic failure. Advanced monitoring systems combine mechanical, electrical, and chemical sensing to provide comprehensive detection capabilities.
Precise pressure management requires highly engineered valve mechanisms integrated into battery housings. A precision surface valve mechanism maintains helium leakage rates within tightly controlled limits and features surface roughness tolerances as low as ≤1 μm. This precision ensures consistent valve actuation during high-pressure events while maintaining sealing integrity under normal conditions. The compact integration into the housing's joined edge enables reliable pressure relief without compromising structural integrity or environmental protection.
Post-event diagnostics capabilities enhance safety assessment through a reversible venting system with diagnostic capability that overcomes limitations of single-use venting devices. This system incorporates a piston assembly within a cylinder block that opens a gas flow path when internal pressure exceeds thresholds. A magnetic restrictor ensures the piston remains sealed under normal conditions and re-engages after venting, allowing system reuse. The ability to detect and differentiate between critical and non-critical pressure events enables informed decisions about continued battery service, enhancing operational efficiency and reducing maintenance downtime.
Dynamic thermal management during gas events is facilitated by a multi-actuation thermal management system that addresses uneven heat distribution in high-density battery packs. The system employs reusable air control valves capable of multiple open-close cycles to actively regulate airflow and pressure during thermal events. This controlled release of flammable gases improves heat dissipation while maintaining thermal and electrical balance during critical operational phases.
8. Integration of Venting with Cooling or Structural Components
The spatial constraints of vehicle design necessitate multifunctional components that combine venting, cooling, and structural functions. This integration enhances space utilization while improving thermal management and safety performance.
The proximity of traction batteries to structural elements like longitudinal sills creates particular challenges during thermal events. A gas deflection mechanism addresses this through heat-resistant deflection plates positioned between batteries and sills. Constructed from materials like steel, ceramic, or fiber-reinforced plastic, these plates redirect high-temperature gases through defined ducts formed between sills and batteries. Pressure-sensitive bursting elements activate only under critical conditions, ensuring predictable and controlled gas release while preventing thermal propagation to unaffected cells.
Protecting electronic components from exhaust gases requires careful spatial organization within battery assemblies. A degassing space integrated into structural elements such as rocker panels or housing covers creates separation between gas paths and sensitive electronics. Partition walls made of electrically insulating materials provide both thermal and structural separation between battery cell compartments and component compartments. Additional features like rupture disks, spark guards, and pressure equalization elements enhance the system's ability to manage overpressure and prevent flame propagation while maintaining modular design flexibility.
9. Metal-Air Batteries as Heat Absorbers for Gas Routing
The dual functionality of metal-air batteries as both energy storage devices and thermal management components represents an innovative approach to battery safety. These systems leverage the substantial thermal mass of metal-air cells to absorb heat from gases generated during thermal runaway.
During thermal events, a controlled venting architecture redirects hot gases through metal-air batteries before environmental release. This path allows the metal-air cells to absorb and dissipate heat, cooling the gas discharge and reducing ignition risk. The system employs dynamic valve control mechanisms that use sensor feedback to modulate multiple valves, ensuring gas flow occurs only when specific thresholds are exceeded. Components include plenums, interconnecting ducts, pressure relief valves, and centralized controllers that orchestrate the entire operation, enhancing safety for both passengers and emergency personnel.
Vehicle structural elements can complement this approach by channeling and controlling gas release. When traction batteries are positioned between longitudinal sills, these structural elements form natural conduits for gas flow. The addition of bursting elements and deflection devices controls and redirects gas under high-pressure conditions, releasing at predefined thresholds and safely deflecting away from sensitive components and occupants. Materials such as steel or ceramic withstand extreme temperatures while directing gas flow predictably and safely, reducing the likelihood of cascading failures or secondary fires.
10. Gas Filtering and Toxic Compound Mitigation
The gases released during thermal runaway contain numerous toxic and flammable compounds that pose significant health and environmental hazards. Advanced filtering systems selectively capture or neutralize these compounds before environmental release.
A zeolite-based molecular sieve filtration system integrated within sealed battery compartments selectively captures specific gas constituents generated during thermal events. By channeling gases through multi-stage filters beginning with zeolites and optionally followed by activated carbon, the system minimizes the release of flammable and toxic compounds. The ceramic nature of zeolites ensures thermal durability under extreme conditions without requiring external power, while the modular design enables the use of different zeolite materials (ZSM-5, Silicalite, or Ru(II)/zeolite composites) to target specific gas species.
Temperature and flammability management provides an alternative approach through a passive thermal runaway safety system employing air intake and exhaust pipelines connected to each battery module. These pipelines are sealed with fusible material sheets that melt only when local temperatures exceed safe thresholds, triggering localized responses. Once activated, ambient air is drawn into affected modules via compressors, rapidly cooling hotspots and diluting flammable gases before expulsion through exhaust systems. This passive activation mechanism eliminates dependence on internal electronic sensors or actuators, enhancing robustness under high-temperature conditions.
11. Battery Housing Designs with Integrated Pressure Relief Features
Battery housing design plays a critical role in managing gas release during thermal events while maintaining structural integrity and occupant protection. Advanced housings incorporate multiple features that provide controlled pressure relief while directing gases away from sensitive areas.
An enclosure failure port engineered using thin or scored enclosure regions, low-melting-point covers, or sacrificial gaskets creates predictable failure points that activate during thermal events. These ports remain sealed under normal operating conditions but open when exposed to high temperature or pressure. The system employs thermal insulation and fire-retardant materials to buffer passenger compartments, while integrated hot gas routing channels direct energy away from critical areas without requiring sensors or electronics.
Valve-based systems offer more precise pressure management through a valve-based exhaust port system within battery pack casings. This design features valve retention plates covering elastomeric ports that remain sealed under normal conditions but open at predefined cracking pressures. Components made from meltable plastics clear flow paths once thermal thresholds are exceeded, while ducted exhaust guides channel hot gases away from vehicles to prevent ignition of nearby materials. Compartmentalization of battery packs, with dedicated venting mechanisms for each section, localizes thermal incidents while maintaining enclosure integrity.
Complementing these physical systems, predictive thermal management uses embedded sensors to detect early signs of thermal runaway and activate rapid cooling systems targeted at individual cells. By lowering temperatures before cells reach runaway thresholds, this approach reduces the likelihood of gas ejection and structural failure, minimizing the need for venting activation.
12. Gas Recirculation and Recombination Systems
Gas management in battery systems extends beyond simple venting to include recirculation and recombination technologies that minimize electrolyte loss and maintain system integrity during both normal operation and thermal events.
In lead-acid battery systems, electrolyte depletion due to hydrogen and oxygen venting represents a persistent challenge. A gas recirculation system architecture addresses this through gas collection units and partition plates equipped with pressure-sensitive valves that dynamically regulate gas flow between cells and collection chambers. This internal gas recirculation minimizes external venting while improving electrolyte retention and battery durability through internal water regeneration and optimized pressure management.
Altitude-induced pressure variations create additional challenges for EV batteries in mobile or aerospace applications. A pressure equalization system employs calibrated check valves to maintain uniform internal pressure across all cells regardless of ambient conditions. One valve isolates each cell from gas migration, while another links gas collection chambers to external environments, enabling controlled depressurization. This design ensures consistent gas collection conditions regardless of altitude, reducing risks of acid creep and leakage currents while maintaining structural integrity during pressure fluctuations.
For lithium-ion battery modules experiencing thermal runaway, an integrated gas management system provides controlled degassing architecture including pressure-activated vents, strategically placed gas receiving spaces, and overpressure valves that direct gas flow away from vital components. This targeted venting during fault conditions helps preserve enclosure integrity and mitigate fire hazards while supporting safer operation and integration into existing battery pack architectures.
13. Gas Detection and Selective Cooling/Venting Control
The integration of detection systems with targeted cooling and venting control enables precise, localized responses to thermal events that minimize system-wide impacts while maximizing intervention effectiveness.
Early detection and dynamic response to internal gas accumulation is achieved through a gas sensor and active fluid delivery system integrated within battery management systems. When off-gassing is detected, the system activates valves to inject thermal control fluid directly into affected battery modules, cooling cells and suppressing exothermic reactions before escalation. This real-time responsiveness combines passive (pressure-sensitive pouch seals) and active (fluid injection) mitigation strategies, enabling system-level safety actions including charge termination, module isolation, and ventilation enhancement.
Cabin protection during thermal events is provided by a smart battery case architecture that integrates gas management with real-time sensing and flow path control. Under normal conditions, the system uses interior air for battery cooling, but upon detecting thermal runaway, automatically blocks air-cooling passages to prevent cabin contamination while activating blower-driven discharge units that expel toxic gases to vehicle exteriors. This dual-path airflow design with actuator-controlled mechanisms ensures rapid venting and passenger protection through coordinated airflow redirection and gas evacuation.
Cell-level structural improvements address mechanical failure points under high-pressure gas conditions through a reinforced separator design that applies synthetic resin films to joint areas of pouch-shaped separators. These films have higher adhesion strength and softening points compared to separator materials, preventing deformation and rupture during high-voltage overcharging. By encapsulating electrodes in reinforced separators and aligning lead terminals with material mechanical axes, the design maintains electrical integrity even under extreme thermal and pressure stresses.
14. Flame Arresters and Gas Filtering Mechanisms
The final barrier between battery thermal events and environmental exposure, flame arresters and gas filtering mechanisms provide critical protection against fire propagation and toxic gas release.
Advanced gas filtration within battery enclosures is achieved through a molecular sieve-based filter system that addresses hazardous emissions including methane, ethylene, and acetylene. This multi-stage design begins with zeolite-based molecular sieves that selectively absorb specific gas molecules based on size and structure. Zeolites like ZSM-5 and Silicalite offer high selectivity for hydrocarbons while maintaining thermal robustness, with secondary filters such as activated carbon providing additional treatment before environmental venting. This approach enables controlled pressure release while minimizing health and environmental risks, particularly in enclosed environments.
Gas dilution provides an alternative approach through a forced airflow gas dilution system utilizing thermally triggered fusible materials at air inlet and exhaust joints. When localized overheating occurs, these materials melt to open pathways for forced air entry and exit. Compressors and exhausters then introduce ambient air to cool affected cells and dilute flammable gases before expulsion. This passive triggering combined with active airflow suppresses fire propagation without compromising unaffected battery modules, enhancing system reliability under extreme thermal conditions.
Intelligent control systems further enhance safety through a selective gas redirection mechanism that monitors voltage, current, temperature, and pressure across individual cells to predict thermal instability. When cells show early signs of thermal runaway, processor-controlled assemblies activate pressure relief valves and mechanically redirect high-temperature gases through dedicated pipelines away from sensitive components. This targeted intervention prevents escalation of single-cell failures into pack-wide thermal events, providing robust, adaptive safety mechanisms that localize and manage thermal incidents before they become catastrophic.
Get Full Report
Access our comprehensive collection of 151 documents related to this technology
Identify Key Areas of Innovation in 2025
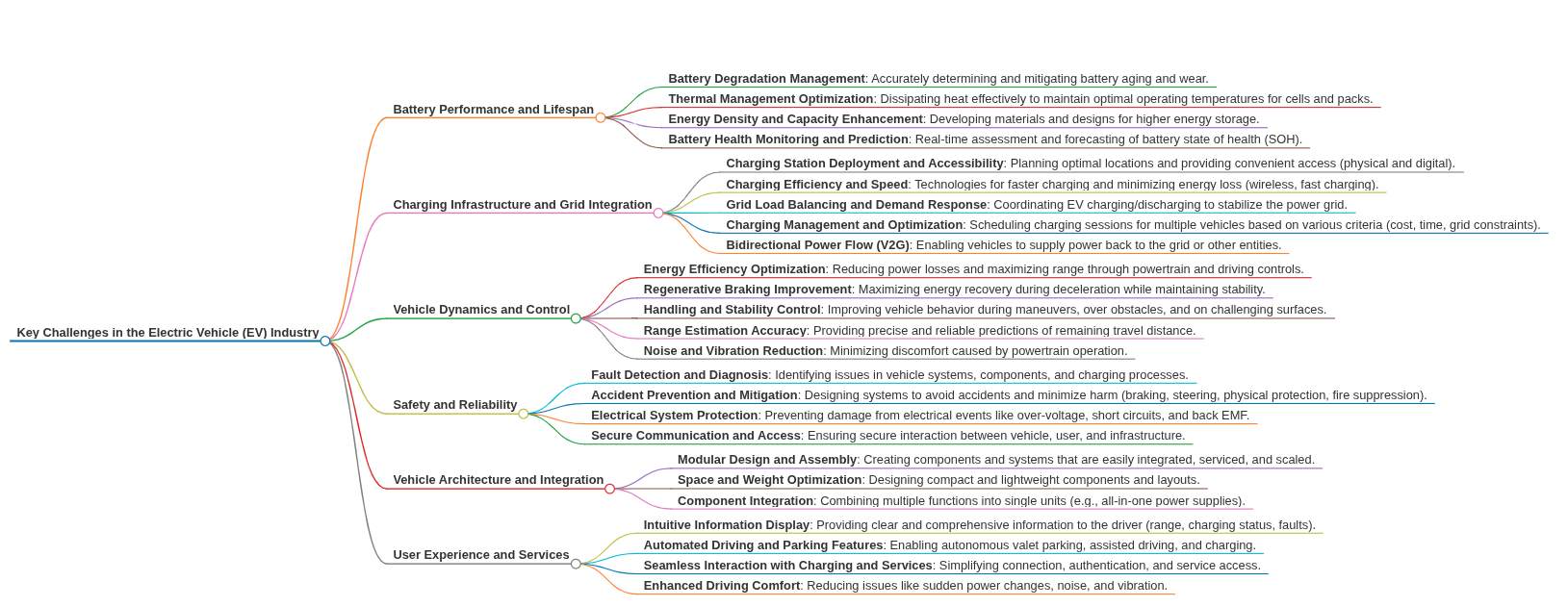