Lithium-Ion Battery Pressure Monitoring for EVs
Electric vehicle battery packs operate under dynamic pressure conditions, with internal cell pressures ranging from 1-3 atmospheres during normal operation to potentially dangerous levels above 10 atmospheres during thermal events. Traditional measurement approaches struggle to capture rapid pressure changes across multiple cells while maintaining the pack's structural and thermal integrity.
The fundamental challenge lies in achieving precise, real-time pressure measurements without compromising the battery pack's sealed environment or introducing new failure points into the system.
This page brings together solutions from recent research—including external pressure sensor configurations, flexible printed circuit implementations, segmented current collector arrays with integrated pressure sensing, and cooling circuit pressure monitoring systems. These and other approaches focus on early detection of thermal events while maintaining the reliability demands of automotive applications.
TABLE OF CONTENTS
1. Embedded Pressure Sensors for Real-Time Cell Monitoring
Lithium-ion battery degradation presents a critical challenge in electric vehicle applications, manifesting through physical expansion caused by internal gas generation and electrode deterioration. While conventional monitoring relies on voltage spread and temperature distribution, these parameters often lack real-time responsiveness and predictive accuracy - particularly in cell-to-pack (CTP) architectures that eliminate module-level monitoring layers.
Direct pressure monitoring offers a fundamentally different approach to battery diagnostics. By integrating pressure sensors between the battery cell stack and housing wall, engineers can detect mechanical stress resulting from cell swelling before electrical or thermal indicators show significant changes. This approach, described in a pressure monitoring integration for CTP designs, employs either piezoelectric or expansion band-based sensors strategically positioned in high-expansion zones within the cell stack.
The effectiveness of embedded pressure monitoring stems from its direct correlation with physical changes in cell structure. Unlike electrical parameters that may remain stable during early degradation stages, pressure changes provide earlier warning signals of aging or functional errors. This is particularly valuable in CTP architectures, where traditional monitoring layers are removed to increase energy density. The system can be configured with either centralized large-area sensors for overall pressure monitoring or distributed smaller sensors that enable spatial pressure mapping across the battery pack.
For high-discharge applications where thermal management becomes critical, pressure monitoring can be extended to cell sidewalls. A pressure sensing and cooling feedback system attaches sensing pads directly to battery cell sides, enabling the detection of pressure-induced swelling during rapid charge and discharge cycles. This approach creates a closed-loop system where pressure data dynamically adjusts cooling water flow rates, preventing the structural deformation that can lead to internal short circuits.
The dual functionality of pressure monitoring - both as a diagnostic tool and as an input for thermal management - represents a significant advancement over traditional monitoring systems. By detecting physical changes before they manifest as thermal or electrical anomalies, these systems provide crucial additional time for preventive measures, potentially averting thermal runaway events that could otherwise cascade through the battery pack.
2. Flexible and Thin-Film Sensor Technologies
The integration of pressure sensors into battery cells presents significant engineering challenges, particularly for pouch-style lithium-ion cells with their sealed, flexible construction. Traditional sensor integration methods risk compromising cell integrity, necessitating innovative approaches that maintain hermetic sealing while providing accurate pressure data.
A notable advancement in this area is the development of flexible printed circuit boards with integrated pressure sensors designed specifically for internal battery monitoring. These FPCBs feature sensing elements mounted on extension arms and encased in metallic sheaths that enable hermetic sealing with the pouch layers during welding. This design allows non-intrusive insertion into internal gas pockets without compromising the structural integrity of the battery. The FPCB approach supports multiple sensing points near electrode leads, enhancing spatial resolution of internal pressure profiles while maintaining compatibility with existing manufacturing processes.
For larger energy storage systems where internal sensor integration may be impractical, external monitoring solutions offer an alternative approach. Thin-film pressure sensor arrays placed directly over battery cell safety valves can detect early signs of thermal runaway by monitoring localized pressure changes. These high-resolution arrays transmit data via wireless communication protocols to the battery management system, enabling real-time anomaly detection with precise spatial resolution. The key advantage of this approach lies in its ability to identify failing cells before catastrophic failure occurs, without requiring modifications to the cells themselves.
Beyond safety monitoring, pressure data also serves as a valuable input for state of charge estimation, particularly in operating regions where voltage-based methods lack precision. A pressure-based SOC estimation method correlates internal pressure behavior with charge levels under varying conditions, identifying inflection points in voltage-pressure curves during cycling. This approach reduces dependency on high-precision voltage sensors and addresses the limitations of coulomb counting in low-current scenarios, creating more robust SOC tracking across the battery's operational life.
The evolution of these flexible and thin-film sensor technologies demonstrates how pressure monitoring has progressed from conceptual research to practical implementation. Each approach represents different trade-offs between integration complexity, measurement accuracy, and manufacturing compatibility - considerations that must be balanced based on specific application requirements and battery designs.
3. External Monitoring Approaches
While internal pressure sensors offer direct measurement capabilities, external monitoring approaches provide alternatives that avoid the complexities of integrating sensors into the battery cells themselves. These methods leverage the mechanical properties of battery housings and supporting structures to infer internal pressure changes without breaching cell integrity.
Traditional battery monitoring systems often integrate pressure sensors directly onto the main control board, creating design constraints and potential safety certification challenges. A distributed pressure sensing architecture addresses these limitations by relocating pressure sensors to external locations such as near switch boxes or on secondary boards. This approach enhances thermal event detection accuracy by positioning sensors closer to battery cells while simplifying compliance with functional safety standards. The distributed architecture also enables correlation between pressure and temperature data, improving diagnostic reliability without compromising system packaging.
Structural strain measurement offers another non-intrusive monitoring method. Rather than placing sensors within batteries or on individual cells, strain sensors can be integrated onto tensioned tie rods that clamp cell arrays between end plates. As cells expand under internal pressure, the resulting strain increases on these rods, providing an indirect yet reliable estimate of pressure buildup. This strain-based pressure monitoring approach eliminates concerns about sensor corrosion or sealing difficulties while providing a cost-effective solution that scales efficiently across different battery formats.
For detecting rapid deformation events indicative of thermal runaway, piezoelectric sensors mounted on inner surfaces of battery housings offer particular sensitivity to mechanical changes. The piezoelectric deformation sensing system captures dimensional changes in real-time, distinguishing between gradual aging-induced swelling and rapid deformation events that signal potential cell failure. This approach provides high sensitivity to transient pressure events while protecting sensors from environmental damage, improving system durability and enabling localization of failing cells.
These external monitoring approaches demonstrate how pressure data can be obtained without compromising the sealed environment of battery cells. Each method presents different advantages in terms of implementation complexity, cost, and diagnostic capability - with strain-based methods offering simplicity and robustness, while piezoelectric approaches provide higher sensitivity to transient events. The selection between these approaches typically depends on specific battery architecture, safety requirements, and manufacturing constraints.
4. Leak Detection and Airtightness Verification
Maintaining airtightness in battery enclosures is essential for preventing moisture ingress and ensuring long-term reliability. Pressure-based methods have emerged as effective techniques for verifying enclosure integrity both during manufacturing and throughout operational life.
Detecting leaks in large-volume battery enclosures presents significant challenges due to environmental factors such as temperature fluctuations and ambient pressure changes. Traditional methods often struggle to distinguish between actual leaks and normal environmental variations. An advanced approach addresses this through temperature-compensated leak analysis that normalizes internal pressure changes against external environmental fluctuations. By integrating pressurizing devices with internal and external pressure sensors, this system isolates pressure variations caused by actual leaks from those resulting from temperature changes, enhancing detection sensitivity even in variable factory environments.
For ongoing monitoring during vehicle operation, battery systems can leverage existing pressure equalization valves to enable non-intrusive airtightness testing. The passive leak detection via vent valve shut-off method temporarily closes the venting device to create a hermetically sealed environment, then monitors internal pressure over time to detect unintended equalization that would indicate a leak. This approach enables periodic assessment without requiring external pressurization equipment, making it suitable for in-field diagnostics throughout the battery's operational life.
Long-term reliability of battery pack seals becomes increasingly important as vehicles age and enclosures experience thermal and mechanical stress cycles. A dedicated real-time airtightness monitoring controller tracks pressure variation rates within battery housings over extended periods, triggering early warnings when detected rates exceed predefined thresholds. This system integrates with the vehicle's electronic control architecture to support predictive maintenance and ensure continued compliance with ingress protection standards throughout the vehicle lifecycle.
The evolution of these leak detection methods reflects growing recognition of enclosure integrity as a critical factor in battery reliability. Each approach offers different advantages in terms of implementation timing and complexity - from production-line verification using temperature compensation to in-service monitoring using existing valve infrastructure. Together, they form a comprehensive strategy for ensuring airtightness from manufacturing through end-of-life.
5. Integration with Battery Management Systems
The integration of pressure monitoring with battery management systems (BMS) represents a critical advancement in battery diagnostics and control. This integration enables not only detection of abnormal conditions but also adaptive responses that enhance safety and performance.
Conventional BMS architectures rely heavily on individual cell temperature sensors, creating complex and cost-intensive monitoring networks. An innovative alternative leverages pressure-based thermal anomaly detection within the cooling circuit to identify early signs of thermal runaway. By momentarily halting coolant flow and observing pressure changes in the cooling circuit, the system can detect localized cell heating and coolant evaporation before significant temperature increases occur. This approach offers greater sensitivity to early thermal events while reducing per-cell instrumentation requirements, simplifying the overall sensor architecture.
More comprehensive integration approaches combine multiple sensor types within a unified BMS framework. An multi-parameter pressure control system incorporates pressure sensors, temperature monitors, gas concentration detectors, and electrolyte management systems to provide holistic battery monitoring. This architecture actively regulates internal battery pressure using solenoid valves and electrolyte transfer mechanisms while continuously updating the BMS on voltage, degradation, and environmental conditions. The system's ability to factor in ambient conditions and respond dynamically through the vehicle management system enables both enhanced safety and extended battery life.
For applications where direct pressure sensing is impractical, mechanical methods using strain-based pressure detection offer an alternative integration pathway. By embedding strain sensors on tie rods within battery modules, the BMS can process strain data using pre-calibrated pressure-strain relationships to detect abnormal swelling before thermal thresholds are breached. This non-invasive approach reduces system complexity while providing reliable early warnings of potential cell failures.
The evolution of these integration approaches demonstrates how pressure data has become increasingly central to battery management strategies. Rather than treating pressure as an isolated parameter, modern BMS architectures incorporate it within multi-factor analysis frameworks that enable more sophisticated diagnostic and control capabilities. This trend toward integrated monitoring reflects growing recognition that battery safety and performance depend on correlating multiple parameters rather than analyzing them in isolation.
6. Thermal Runaway Detection Strategies
Thermal runaway represents one of the most significant safety risks in lithium-ion battery systems, making early detection critical for preventing catastrophic failures. Pressure-based monitoring offers distinct advantages over traditional temperature-based approaches, particularly in detecting precursor events before thermal propagation begins.
Temperature sensors alone often detect thermal runaway too late for effective intervention, as significant heat generation occurs only after the runaway process has initiated. A more proactive approach employs a dual-sensor thermal chain determination method that simultaneously monitors internal pressure and cell voltage to identify thermal chain reactions in their earliest stages. This dual-parameter approach mitigates false positives by requiring both pressure and voltage thresholds to be breached before triggering alerts, while still enabling earlier intervention by capturing pressure spikes before measurable temperature increases occur.
Cell-to-cell pressure variations often indicate degradation or uneven aging before thermal events develop. A multi-tiered early warning system leverages these pressure differentials by establishing intermediate thresholds between initial warnings and fault conditions. By dynamically adjusting thresholds using state-of-charge mapping and data analytics, this approach enables precise identification of abnormal pressure behavior without triggering unnecessary fault states. The ability to detect and escalate warnings based on pressure-derived SOC differences supports more effective predictive maintenance strategies.
Physical deformation tracking using piezoelectric sensors offers yet another detection pathway. When mounted on battery pack housings, these sensors can identify internal pressure build-up caused by cell degassing - a known precursor to thermal runaway. The piezoelectric sensor-based pressure monitoring system performs time-based analysis to differentiate between gradual swelling and rapid deformation events, enabling localized detection of hazardous cells and targeted intervention measures.
For comprehensive protection, multi-sensor integration provides the most robust detection capability. By combining pressure sensors with strain, gas, and temperature monitors within a multi-sensor thermal runaway detection system, battery management systems can implement tiered sensing strategies where low-power sensors continuously monitor for anomalies and high-power sensors activate only for confirmation. This approach optimizes energy usage and sensor longevity while enabling early and accurate detection through heterogeneous data fusion.
These diverse detection strategies illustrate how pressure monitoring has evolved from a supplementary measurement to a primary indicator for thermal event prediction. Each approach offers different advantages in terms of detection speed, false positive rates, and implementation complexity - considerations that must be balanced based on specific battery designs and safety requirements.
7. Pressure-Driven Control Systems
The integration of pressure monitoring into battery control systems enables adaptive management strategies that respond dynamically to changing cell conditions. These pressure-driven control systems extend beyond passive monitoring to actively regulate charging, cooling, and operational parameters based on real-time pressure data.
During high-rate charging and discharging, battery cells can experience internal gas generation that leads to swelling and increased mechanical pressure between adjacent cells. An integrated sensing system addresses this challenge by mounting pressure-sensitive pads on cell sidewalls to provide real-time data to the battery management system. The BMS classifies pressure readings into operational zones and dynamically adjusts cooling water flow rates accordingly. This pressure-driven cooling regulation enables early detection of abnormal thermal events while optimizing thermal management efficiency, preventing unnecessary energy expenditure on cooling when pressure remains within normal ranges.
At the battery pack level, pressure sensors embedded within the enclosure can be calibrated post-assembly to establish baselines for structural monitoring. The pressure sensor initialization and calibration process ensures that pressure increases due to cell swelling or mechanical damage trigger automatic adjustments to charging or discharging operations. This approach enhances transport and installation safety by detecting latent defects while providing diagnostic feedback through real-time communication of abnormal states. By integrating pressure monitoring directly into operational control logic, the system significantly reduces the risk of overpressure-induced failures.
The key advantage of these pressure-responsive systems lies in their ability to provide adaptive, real-time control without relying solely on thermal indicators that may lag behind actual cell conditions. In cooling-integrated systems, pressure readings directly influence thermal management strategies, while pack-level monitoring approaches leverage calibrated pressure thresholds to safeguard against both overpressure and underpressure scenarios that might indicate internal damage.
These control architectures represent a significant advancement over traditional battery management approaches that rely primarily on voltage and temperature. By incorporating pressure as a control parameter, these systems enable more nuanced and responsive management strategies that can adapt to variations in cell behavior due to aging, manufacturing tolerances, or external stressors. This adaptive capability becomes increasingly important as battery systems face more demanding operational profiles in automotive applications.
8. Structural Monitoring Approaches
Structural monitoring of battery systems provides critical insights into mechanical integrity and internal pressure changes without requiring direct access to cell internals. These approaches leverage various sensor technologies to detect deformation, strain, and pressure distribution across battery modules.
Traditional internal pressure sensing faces significant implementation challenges including limited space, potential sensor corrosion, and sealing complexities. An alternative approach employs strain sensors on tie rods that compress battery cell stacks between end plates. As cells expand due to internal pressure increases, the resulting strain on these pre-tensioned rods provides an indirect measurement of pressure build-up. This centralized sensing strategy reduces system complexity by eliminating the need for distributed gauges while improving maintainability and safety. The system compares strain readings against pre-calibrated data tables that account for variables like temperature and state of charge, enabling real-time detection of anomalies such as thermal runaway or cell failure.
To enhance detection reliability and reduce false alarms, multi-parameter analysis approaches integrate pressure data with other environmental and electrical parameters. When pressure thresholds are corroborated by abnormal readings in metrics such as voltage, temperature, and humidity, the system can distinguish between normal operational variations and potentially hazardous conditions. This multi-factor approach enables more accurate and timely detection of hazardous events while ensuring that alarms are both meaningful and actionable in real-world operating environments.
For lithium iron phosphate (LFP) batteries, which often exhibit minimal variation in voltage and temperature during early-stage degradation, structural monitoring becomes particularly valuable. Placing pressure sensors between battery modules and mechanical enclosures allows structural deformation to serve as a proxy for internal pressure changes. By tracking pressure changes over successive charge-discharge cycles at identical state-of-charge levels, the system can detect subtle signs of aging or failure before they manifest as electrical or thermal anomalies. This approach is especially effective for chemistries where traditional indicators provide limited early warning capabilities.
These structural monitoring approaches demonstrate how mechanical measurements can complement electrical and thermal monitoring to create more comprehensive battery management systems. Each method presents different trade-offs between implementation complexity, measurement accuracy, and integration requirements - considerations that must be evaluated based on specific battery designs, safety requirements, and operational profiles.
9. Multi-Parameter Integrated Monitoring
As battery technologies advance toward higher energy densities and enhanced safety requirements, integrated multi-parameter monitoring systems have emerged that combine pressure data with other critical measurements. These comprehensive approaches enable more nuanced diagnostics and improved failure prediction compared to single-parameter monitoring.
Conventional battery monitoring approaches that rely on external sensors often create blind spots that hinder accurate, real-time diagnostics of cell-level anomalies. An internal multi-parameter monitoring system addresses this limitation by embedding temperature, pressure, and air pressure sensors directly within battery cells. This integration enables direct sensing of internal expansion forces and casing air pressure, providing unprecedented visibility into cell-level conditions. The inclusion of heat sinks between cell packages improves thermal management while serving as conduits for thermal data collection, creating a compact design that supports both safety and energy density.
The most significant advantage of this approach lies in its seamless integration with vehicle-level battery management systems. Battery modules constructed with these enhanced cells can wirelessly communicate with external BMS components, enabling real-time, cell-level diagnostics without extensive wiring or external instrumentation. This architecture enhances monitoring granularity and allows for early fault detection, significantly reducing the risk of undetected cell degradation or failure.
For early detection of thermal runaway events, a two-tier sensing approach combines continuous low-level monitoring with targeted high-resolution analysis. The multi-sensor early detection system continuously monitors parameters including strain, pressure, hydrogen gas, carbon monoxide/dioxide levels, and acceleration. Upon detecting potential abnormalities, high-power sensors such as hydrogen detectors activate to confirm threats, enabling rapid and energy-efficient responses to emerging safety risks.
This two-step approach improves detection accuracy through multi-sensor data fusion while introducing robust remediation mechanisms that can automatically disable affected modules to prevent fault propagation. The selective sensor activation architecture conserves energy and extends sensor lifespan while maintaining comprehensive monitoring coverage, representing a significant advancement in battery safety systems.
The evolution toward integrated multi-parameter monitoring reflects growing recognition that battery health and safety depend on complex interactions between mechanical, electrical, thermal, and chemical processes. By capturing these diverse parameters within unified monitoring frameworks, these systems enable more sophisticated diagnostic capabilities and predictive maintenance strategies that enhance both safety and performance throughout battery operational life.
Get Full Report
Access our comprehensive collection of 102 documents related to this technology
Identify Key Areas of Innovation in 2025
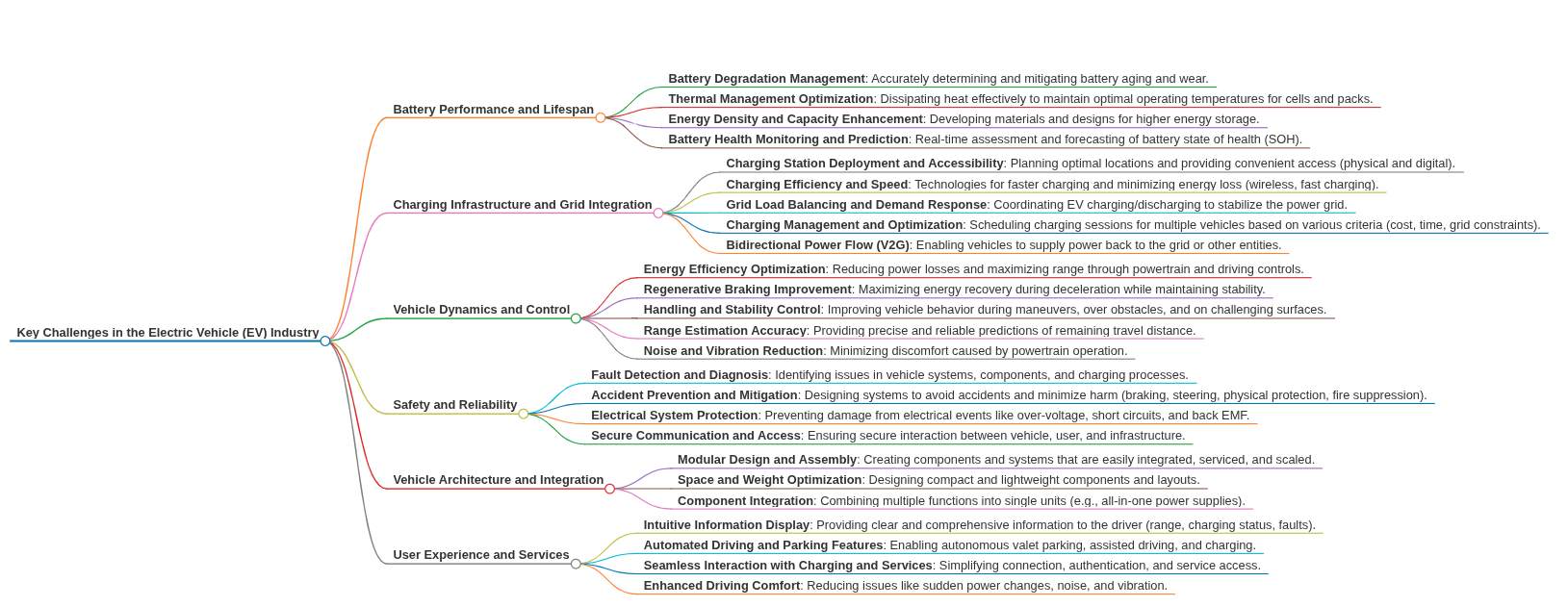