Separation Processes for Electric Vehicle Battery Recycling
Electric vehicle battery recycling involves processing materials that arrive in complex assembled states. Current recycling operations face yields below 70% for critical materials like lithium, cobalt, and nickel—with primary challenges arising from the intimate lamination of electrodes, separator films, and current collectors within battery cells. The physical and chemical bonding between these components creates separation barriers that conventional mechanical processing struggles to overcome efficiently.
The challenge lies in developing separation processes that maximize material recovery without introducing cross-contamination that diminishes the economic value of recycled streams.
This page brings together solutions from recent research—including multistage ultrasonication techniques for electrode delamination, sequential physical separation systems with dedicated processing zones, and thermal pretreatment methods that enhance subsequent material separation. These and other approaches demonstrate pathways to higher material recovery rates while addressing the practical constraints of industrial-scale processing operations.
1. Method for Delaminating Battery Electrode Active Material Using Multistage Ultrasonication and Spraying
GUANGDONG HAOZHI TECHNOLOGY CO LTD, 2025
Method for recycling battery electrodes that involves washing and rinsing the electrodes multiple times using ultrasonication and spraying to delaminate the active material from the current collectors. The electrodes are first moistened, then washed and rinsed in two stages using ultrasonication at different frequencies. This removes larger particles in the first stage and finer particles in the second stage. The method improves electrode recycling by using optimized washing steps to separate the active material and current collectors.
2. Device for Sequential Separation and Recycling of Lithium Battery Components with Distinct Positioning Oscillation, Shell Separation, and Crushing Areas
HEFEI HAINUOHENG INFORMATION TECHNOLOGY CO LTD, 2024
Waste lithium battery recycling device for new energy vehicles that efficiently separates and recycles battery components without mixing them. The device has three recycling areas: positioning oscillation, shell separation, and shell crushing. The positioning oscillation area holds the battery and vibrates it to loosen connections. The shell separation area removes the outer case. The shell crushing area flattens the remaining battery components. This sequential separation prevents mixing of different materials.
3. Lithium-Ion Battery Recycling System with Multi-Stage Component Separation and Processing
Tianqi Lithium Corporation, TIANQI LITHIUM CO LTD, 2024
Fully automatic lithium-ion battery recycling system that enables efficient separation and processing of battery components through a multi-stage process. The system comprises primary pulverization, air separation, magnetic separation, steel shell collection, and high-energy shearing, followed by a vibration separator. The process achieves separation of battery components through a combination of air separation and magnetic separation, with the collected materials then being processed through a series of mechanical and chemical treatments.
4. Lithium Battery Positive Plate Separation Device with Dual-Step High-Pressure Cleaning and Drying Mechanism
UNIV ANHUI AGRICULTURAL, 2023
A lithium battery positive plate separation device that optimizes the recycling process by removing impurities from the positive plate before processing. The device employs a dual-step approach: first, the positive plate is cleaned through high-pressure water jets to remove attached materials, followed by a drying step to separate the plate from its adherents. This approach significantly enhances the separation efficiency and purity of the positive plate, while also preventing secondary pollution from the attached materials during the subsequent drying process.
5. Sorting Device for Power Battery Diaphragm Pole Pieces with Mechanical, Eddy Current, and Magnetic Separation Mechanisms
JINGMEN POWER BATTERY REGENERATION TECH CO LTD, 2023
A sorting device for decommissioned power battery diaphragm pole pieces that improves recovery purity of positive and negative electrodes through precise separation of pole pieces and diaphragms. The device employs a combination of mechanical separation, eddy current sorting, magnetic separation, and magnetic strengthening mechanisms to separate pole pieces from diaphragms, followed by precise separation of positive and negative electrodes. This enables enhanced recovery of high-value components while minimizing energy consumption and sieve hole blockages.
6. Lithium-Ion Battery Recycling Method with Thermal Pretreatment and Sequential Material Separation
GUANGDONG BRUNP CYCLING TECHNOLOGY CO LTD, 2022
A method for recycling lithium-ion batteries through a novel pretreatment process that enables efficient separation of materials. The process involves heating the battery residue to enhance material separation, followed by crushing and sieving to control particle size. The crushed material is then subjected to magnetic separation to separate steel slag, copper flakes, aluminum foil, and graphite. The graphite is separated through wet leaching, and the remaining materials are processed to recover copper, aluminum, and other valuable components. The method achieves higher purity and recovery rates compared to traditional battery disassembly methods.
7. Recycling Process for Metal Extraction from Lithium-Ion Batteries Using Crushing, Shaking Screen, and Water Separation System
广东和誉智能科技有限公司, 2022
A recycling process for extracting metals from used lithium-ion batteries without manual separation of lead-acid solution. The process involves crushing the batteries to extract the metals and separate the lead-acid solution. The crushed batteries are fed into a recovery box with a shaking screen to filter out the lead-acid solution. The filtered batteries are then moved to a water storage tank where they sink and metal floats to the surface. A shovel collects the metal and moves it to a separation box with a water surface push plate. The push plate scoops up the plastic and pushes it to the side. The walking roller on the bottom of the push plate follows a sloped guide to lift the push plate. This separates the plastic from the water storage tank. The plastic falls into a collection box. The metal floats in the water and is moved to a metal collection bag.
8. Method for Multi-Stage Electrostatic and Magnetic Separation of Cathode Materials from Lithium-Ion Battery Waste
HUNAN BRUNP EV RECYCLING CO LTD, 2022
A method for precise separation of cathode materials from lithium-ion battery waste using electrostatic and magnetic separation. The process involves crushing the battery waste, followed by magnetic separation to separate iron and other ferromagnetic materials. The magnetic separation is then followed by electrostatic separation to separate the remaining materials, including copper, aluminum, and graphite. This multi-stage separation process enables the precise sorting of cathode materials, achieving higher purity levels compared to traditional single-stage separation methods.
9. Battery Recycling Apparatus with Integrated Crushing and Air-Flow Screening Mechanisms
SHANGHAI XINCHUAN NEW ENERGY TECH CO LTD, 2020
A waste battery recycling device that improves the efficiency of battery material separation from spent electric vehicle batteries. The device comprises a frame with inlet and outlet ports, a power mechanism, crushing mechanism, and air-flow screening mechanism. The power mechanism drives the crushing mechanism, which pulverizes the battery components. The air-flow screening mechanism separates the crushed materials from the battery casings and other contaminants. The crushed materials are then processed through a magnetic force division sieve, which further separates the metal components from the non-metallic materials. The processed materials are then stored in a discharge port for further processing or reuse.
10. Device for Controlled Environment Processing of Lithium Battery Electrolyte Residues with Hazardous Compound Suppression
WUHAN RUIJIETE MATERIAL CO LTD, Wuhan Ruijet Material Co., Ltd., 2020
Device for processing decommissioned lithium battery electrolyte residues to prevent environmental hazards. The device contains a controlled environment where the battery electrolyte is processed in a manner that prevents the formation of hazardous fluoride and phosphorus compounds. The device employs a controlled atmosphere and precise temperature and pressure conditions to safely handle the hazardous electrolyte while maintaining its integrity.
11. Tiered Extraction Process for Metal Recovery from Spent Ternary Lithium-Ion Batteries
CHEN WENQUAN, 2020
A waste ternary lithium battery recycling process that employs a tiered extraction method to recover valuable metals from spent lithium-ion batteries. The process involves heating and evaporating the battery materials, followed by magnetic separation and electrostatic separation. The resulting material is then mixed with an acid solution to extract metals, which are then further processed through multiple stages of extraction and purification to minimize contamination and improve recovery efficiency.
12. Battery Waste Processing Method Utilizing Vibrating Plate for Physical Characteristic-Based Sorting
QIAN CHE-HUA, 2020
A waste battery recycling processing method that enables efficient sorting and transportation of mixed battery waste through controlled separation and collection. The method involves sorting battery types using a vibrating plate and conveying system, where waste batteries are first placed on a vibrating plate and then separated into distinct categories based on their physical characteristics. The sorted batteries are then transported to a sorting facility where they are further processed for recycling.
13. Automated Battery Disassembly System with Intelligent Sorting and Sensor-Based Type Identification
TIANJIN HONGJIAN RUIHE TECHNOLOGY CO LTD, 2019
A method for non-hazardous battery recycling and dismantling that automates the disassembly process through intelligent sorting, classification, and recycling. The system employs advanced gas detection and sensor technology to identify battery types and integrity before disassembly, enabling precise control over the recycling process. The system integrates vacuum, gas, and liquid processing, with automated cutting and thruster systems to efficiently dismantle batteries. This approach eliminates manual labor and hazardous conditions associated with traditional recycling methods.
14. Lithium-Ion Battery Recycling Pretreatment via Dual-Activation with Ball Milling and Additive System
HIGHPOWER TECH GANZHOU CO LTD, 2019
A lithium-ion battery recycling pretreatment method that enhances the recovery of valuable metals through a dual-activation process after initial thermal treatment. The method combines ball milling with an advanced additive system to activate the electrode material, followed by selective dissolution and leaching of the resulting active material. This approach addresses the limitations of conventional pretreatment methods by providing both mechanical activation and chemical activation pathways for metal recovery.
15. Vacuum Chamber with Automated Mechanical Disassembly for Lithium-Ion Battery Component Separation
UNIV XIANGTAN, 2019
Vacuum-based method and device for safely and efficiently dismantling lithium-ion batteries in a controlled environment. The method utilizes a specially designed vacuum chamber with automated disassembly capabilities, where the battery is first removed from the cell and then broken down into its constituent components through precise mechanical disassembly. The process is performed in a sealed environment with controlled atmosphere conditions, allowing for the safe handling of hazardous materials and preventing fire hazards. The dismantling process is further supported by a vacuum system that captures and recovers the generated gases, ensuring a controlled and environmentally responsible disposal process.
16. Lithium Battery Recycling Process with Magnetic Separation and High-Pressure Leaching Stages
TAISHUN YONGQING ELECTRIC POWER TECHNOLOGY CO LTD, 2019
A novel lithium battery recycling process that enhances material recovery through a multi-stage approach. The method involves a magnetic separation stage followed by a high-pressure leaching process, and then a purification step. The process utilizes a unique combination of magnetic separation and high-pressure leaching to separate lithium-ion battery components, while the high-pressure leaching process enables the extraction of valuable lithium and other metals. This multi-stage approach addresses the challenges of traditional lithium-ion battery recycling by providing a more comprehensive and efficient recovery process.
17. Sequential Mechanical and Chemical Processing Method for Component Recovery from Waste Lithium-Ion Batteries
CENTRAL SOUTH UNIVERSITY, 2019
Method for processing waste power lithium-ion batteries to recover valuable components while minimizing environmental impact. The process involves a multi-step sequence of mechanical separation, chemical treatment, and purification to extract valuable materials such as aluminum, copper, and graphite. The treatment includes crushing, volatilization, decomposition, alkaline washing, and pyrolysis steps to ensure the recovery of hazardous materials while maintaining their chemical integrity. The method enables the efficient recovery of valuable components from spent lithium-ion batteries while protecting the environment through controlled chemical processing.
18. Hierarchical Lithium-Ion Battery Recycling Process with Multi-Stage Mechanical and Chemical Separation
HUIZHOU EVE ENERGY CO LTD, 2019
A novel recycling method for lithium-ion batteries that enables selective extraction of valuable metals while minimizing chemical reagent consumption. The process employs a hierarchical approach involving multiple stages of separation, including mechanical sieving, chemical treatment, and selective precipitation. The first stage of mechanical separation removes the battery components, followed by chemical treatment with sodium persulfate to dissolve the battery materials. The resulting slurry is then subjected to selective precipitation using sodium hydroxide, which selectively precipitates the desired metal ions while leaving the battery components behind. This multi-stage approach enables the efficient recovery of valuable metals from lithium-ion battery waste without requiring the use of harsh chemicals.
19. Device for Lithium-Ion Battery Electrolyte Recovery with Controlled Evaporation and Multi-Stage Separation
GUIZHOU LIGHT IND TECHNICAL COLLEGE, 2018
A device for recovering lithium-ion battery electrolyte from spent batteries through a controlled evaporation process. The device comprises a furnace, vapor cooler, and collection system to manage the electrolyte vapor stream. The furnace uses electric or microwave heating to vaporize the electrolyte, while the vapor is cooled to prevent dust formation. The vapor is then collected and processed through a series of separation steps, including evaporation, condensation, and separation of the liquid and gas phases. The liquid phase is then processed through a fluoride removal step, followed by liquefaction using a pressurized or refrigerated process. The resulting liquid electrolyte is then treated with activated carbon to remove trace organic compounds.
20. Method for Multi-Step Recovery of Unformed Sheet Waste in Lithium-Ion Battery Production
GUIZHOU GUIHANG NEW ENERGY TECHNOLOGY CO LTD, 2018
A method for recovering unformed sheet waste from lithium-ion battery production through a multi-step process that addresses the conventional separation challenges. The process involves crushing, roasting, washing, sieving, settling, and drying of the unformed material, followed by separation of the current collector from the electrode material. The current collector is then further processed to produce a high-purity material suitable for recycling.
Get Full Report
Access our comprehensive collection of 43 documents related to this technology
Identify Key Areas of Innovation in 2025
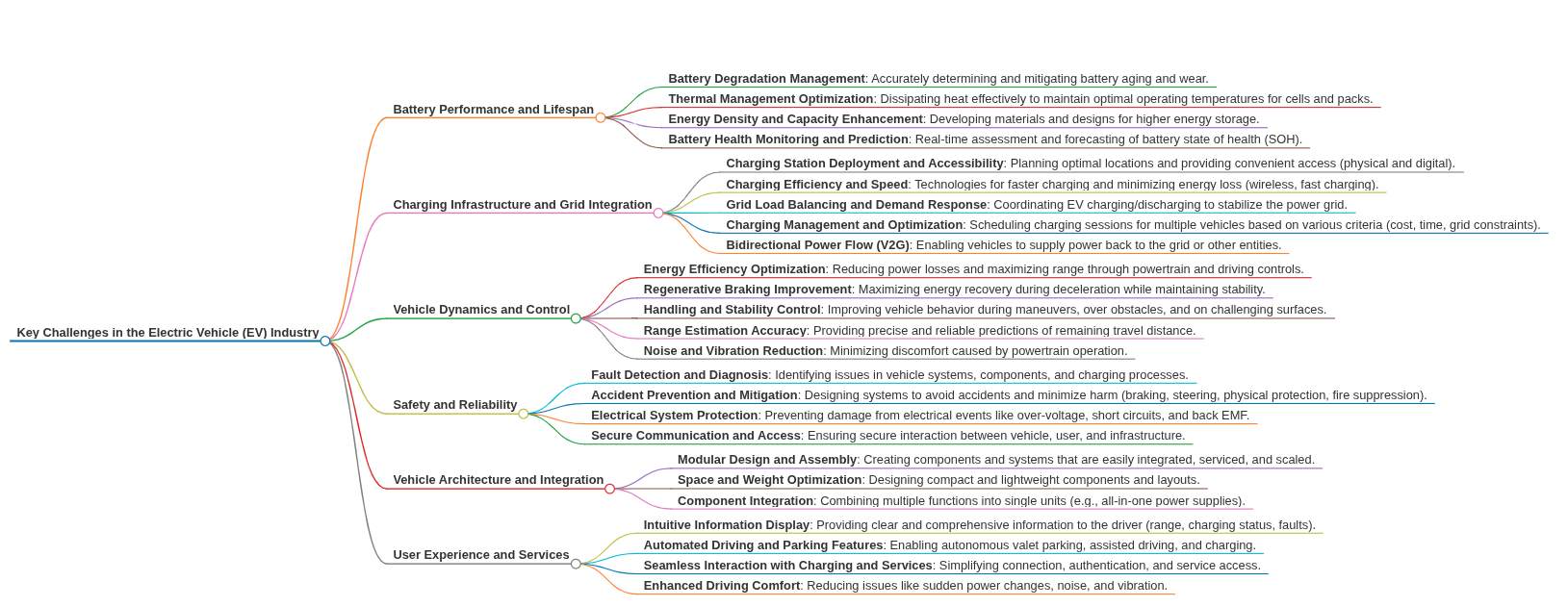