Thermal Regulation Techniques for EV Batteries while Charging
Fast charging of electric vehicle batteries generates substantial heat—up to 2.5 kW of thermal energy for a 150 kW charging session. Without adequate thermal management, battery temperatures can rise above 45°C, accelerating degradation and forcing charging systems to throttle power delivery to prevent damage.
The fundamental challenge lies in removing heat quickly enough to enable maximum charging rates while maintaining cell temperatures within optimal bounds and minimizing the energy cost of cooling systems.
This page brings together solutions from recent research—including dual-circuit cooling architectures, external coolant delivery systems, smart temperature control algorithms, and condensation-prevention strategies. These and other approaches help engineers balance the competing demands of charging speed, battery longevity, and system efficiency.
TABLE OF CONTENTS
1. External Coolant Delivery and Off-Board Thermal Conditioning
High-rate EV charging generates substantial heat that conventional onboard thermal systems struggle to manage effectively. This limitation has driven innovation toward external thermal management solutions that shift the cooling burden to charging infrastructure.
The external battery thermal management system integrated into Electric Vehicle Supply Equipment (EVSE) represents a significant advancement in this domain. This system delivers coolant directly to the vehicle through a specialized connector, enabling thermal energy transfer via a liquid-to-liquid heat exchanger without mixing coolants. By eliminating bulky onboard heat exchangers, this approach supports ultra-high charging rates while maintaining a lightweight vehicle design. The multifunctional connector simultaneously delivers power and coolant, incorporating ergonomic features like powered insertion and visual indicators to enhance usability.
Complementing this approach, the connector-based external refrigerant system utilizes an external reservoir tank to supply refrigerant-based cooling. Upon vehicle connection, the system circulates refrigerant through the battery's thermal circuit using a pump controlled by a central controller. The system can incorporate a heat pump loop to precondition the refrigerant based on real-time thermal requirements. This configuration preserves vehicle weight and design flexibility by avoiding oversized onboard air-conditioning systems, while also recovering and recycling refrigerant to minimize environmental impact.
For greater versatility, the actuated arm-based thermal conditioning system offers multiple external cooling or heating modes that adapt to real-time thermal data from the EV. This system selects the optimal thermal exchange method—whether through liquid coolants, conditioned air, or direct contact with thermal pads—based on current conditions. The automated arm mechanism connects both power and thermal conduits without manual intervention, while its modular design supports implementation across diverse vehicle platforms. Unlike single-mode systems, this dual-mode capability ensures optimal battery temperature across varying environmental conditions.
The dual-mode cooling architecture takes a hybrid approach by combining onboard cooling during discharging with off-board cooling during charging. This system leverages onboard heat exchangers optimized for high-altitude, low-temperature discharging conditions, while utilizing external cooling infrastructure during ground-based high-power charging where ambient temperatures and thermal demands are higher. An adaptive controller dynamically balances heat removal between these systems to maintain consistent battery temperature. This approach particularly benefits aviation and weight-sensitive applications by reducing onboard cooling system size while enhancing reliability.
2. Integrated Battery and Cabin HVAC Systems
Lithium-ion battery performance during charging depends heavily on maintaining optimal temperature ranges, typically between 15-35°C. Traditional thermal management approaches using standalone PTC heaters or passive cooling methods create inefficiencies and temperature gradients that compromise charge acceptance, energy efficiency, and battery lifespan.
The integrated thermal management system addresses these limitations by unifying battery and cabin HVAC thermal control. Rather than implementing separate thermal circuits, this system leverages existing vehicle components—including electric heaters, motor waste heat exchangers, and air conditioning units—within a configurable coolant circuit. A network of switching and three-way valves redirects coolant through different thermal paths based on real-time temperature data, enabling the battery pack to utilize the vehicle's broader thermal resources without dedicated components.
This integration is enabled by sophisticated temperature monitoring and control strategies that utilize strategically placed sensors throughout the battery module and coolant reservoir. These sensors feed data to a control unit that calculates optimal coolant routing and orchestrates valve and pump operations. Unlike conventional systems that maintain fixed coolant paths, this dynamic approach ensures even thermal distribution across battery cells, significantly reducing cell-to-cell temperature differentials that typically range from 3-8°C in traditional designs.
The energy-efficient integration of vehicle thermal resources represents a fundamental shift from isolated subsystems to a holistic vehicle thermal architecture. By repurposing motor waste heat and utilizing the HVAC system for dual purposes, this approach eliminates redundant thermal components and reduces parasitic energy losses. The simplified system architecture supports modular deployment across different EV platforms while reducing manufacturing complexity. This contrasts with conventional approaches that require separate cooling circuits, pumps, and control systems for each thermal domain within the vehicle.
3. Phase Change Material (PCM)-Based Thermal Regulation
During high-power EV charging, battery temperatures can rise by 10-15°C within minutes, potentially accelerating degradation and increasing thermal runaway risk. Phase change materials (PCMs) offer a passive solution to this challenge by absorbing thermal energy during their solid-to-liquid transition, effectively buffering temperature fluctuations without active cooling.
The PCM-based thermal buffering system integrates PCM modules with a cooling loop and heat pump to create a multi-stage thermal management approach. During initial charging, the PCM absorbs heat and maintains battery temperature near its melting point (typically 30-45°C depending on the formulation). Once the PCM liquefies and thermal loads continue to rise, the system activates a dynamic cooling circuit that redirects coolant through radiators or heat exchangers based on ambient and operational conditions. This staged approach minimizes compressor usage during moderate thermal loads, reducing energy consumption by 15-30% compared to continuous active cooling.
Unlike conventional systems that simply dissipate thermal energy, this design implements a cabin heat reuse mechanism that captures waste heat for cabin warming. This feature is particularly valuable in cold climates where cabin heating can consume 30-40% of available battery energy. The system's ECU integration enables real-time adjustment of flow paths and heat exchange operations based on both battery thermal needs and cabin comfort requirements. This adaptability across environmental conditions represents a significant advancement over fixed-path thermal systems that cannot redistribute thermal energy between vehicle subsystems.
The five-mode thermal control loop further extends PCM capabilities by dynamically adapting to specific operating states. The system selectively activates heating or cooling subsystems based on the vehicle's current mode—charging, discharging, or extreme cold operation—minimizing energy consumption while maintaining battery performance and safety. In low-temperature conditions where discharge power typically decreases by 30-50%, this system can maintain battery temperature without requiring separate heaters, reducing system complexity and cost.
PCM-based solutions fundamentally shift thermal management from reactive to proactive strategies. The thermal integration with HVAC and coolant routing creates a unified thermal architecture that preserves battery longevity while extending driving range through reduced auxiliary power consumption. The passive nature of PCMs provides an inherent safety advantage, as they continue to buffer temperature even during control system failures, offering a fail-safe mechanism not present in purely active cooling systems.
4. Thermoelectric Modules for Localized Cooling or Heating
Thermoelectric modules based on the Peltier effect provide bidirectional thermal control without moving parts, offering compact solutions for targeted battery temperature management. These solid-state devices generate temperature differentials when current flows through them, enabling both heating and cooling functions within a single component.
The active liquid-based thermal management system combines a coolant circulation loop with thermoelectric modules to create a cost-effective solution for EVs lacking integrated HVAC systems. A pump circulates coolant through thermally conductive channels embedded in the battery pack, while thermoelectric modules provide precise thermal regulation. The system employs PWM control for pump speed modulation and PID control algorithms to maintain battery temperature within ±2°C of the target range. This approach offers particular advantages for budget EV segments in developing markets, where dedicated thermal management systems must balance cost constraints with performance requirements.
The dual-mode thermal regulation capability represents a key advantage over conventional systems that require separate heating and cooling components. By reversing current flow, thermoelectric modules switch between heating and cooling functions, reducing system complexity and component count. The design incorporates enhanced heat dissipation through aluminum heat sinks and optimized coolant channel geometries using extruded aluminum manifolds. These features ensure uniform temperature distribution across battery cells, maintaining thermal gradients below 3°C even during rapid charging—a significant improvement over the 5-8°C gradients typical in passive cooling systems.
However, thermoelectric modules face efficiency limitations, with coefficients of performance (COP) typically ranging from 0.5-1.5. To address this challenge, the thermoelectric converter for waste heat recovery integrates thermoelectric elements within a hybrid phase-change system. During low-temperature conditions, the system harvests waste heat through the thermoelectric module to preheat the battery, reducing reliance on active electric heating that can consume 20-30% of available energy. This hybrid approach combines the high latent heat capacity of PCMs (typically 200-300 kJ/kg) for passive thermal buffering with active thermoelectric control to maintain optimal battery temperature. The smart control architecture continuously adapts to changing environmental and operational conditions, balancing energy efficiency with thermal performance.
5. Heat Exchanger and Cold Plate-Based Direct Cooling
As battery energy densities increase beyond 250 Wh/kg, the thermal challenges during charging intensify, requiring more efficient heat transfer methods. Direct cooling approaches using heat exchangers and cold plates offer superior thermal performance by minimizing the resistance between heat sources and cooling media.
Traditional cooling systems often rely on thermal interface materials (TIMs) with conductivities of 1-5 W/m·K, creating a thermal bottleneck that limits heat dissipation. The cooling device with a welded heat transfer plate eliminates this limitation by thermally bonding the plate directly to internal cooling channels, removing the need for TIMs entirely. This welded configuration allows direct contact with battery cells, improving thermal conductivity by 300-400% compared to TIM-based solutions. The cooling devices positioned between stacked cells create a compact, modular layout that scales efficiently across different battery configurations while maintaining consistent thermal performance.
Cold plate designs typically suffer from temperature gradients along the coolant flow path, with downstream cells operating 3-5°C hotter than upstream ones. The variable height and contact angle cold plate design addresses this challenge through innovative geometrical features that ensure uniform heat distribution. The cold plates progressively increase in height from 30mm to 60mm and vary their contact angle between 120° and 150° along the coolant flow direction. This graduated geometry compensates for the thermal load accumulated downstream, maintaining cell-to-cell temperature variations below 2°C—a critical factor for preventing capacity imbalances and differential aging across the battery pack.
Conventional bottom-cooled systems create thermal gradients within individual cells due to the distance between the cooling surface and the cell top. The dual-sided liquid cooling configuration overcomes this limitation by integrating liquid-cooled plates on both upper and lower surfaces of battery modules. This arrangement enables bidirectional coolant flow that promotes uniform thermal management throughout the entire cell volume, reducing internal temperature gradients from typical values of 5-7°C to less than 3°C. The system's intelligent control module switches between high-power and energy-efficient cooling modes based on real-time thermal inputs, optimizing energy consumption while supporting fast charging rates of up to 3C without thermal limitations.
6. Battery Preconditioning and Heating for Cold Weather Charging
Lithium-ion batteries experience significant performance degradation at low temperatures, with charging capacity reduced by 20-40% at 0°C and 50-80% at -20°C due to increased internal resistance and lithium plating risk. Effective preconditioning is essential for safe and efficient charging in cold climates.
Traditional preconditioning systems using fluid-based or air-based heaters add complexity, weight, and packaging constraints to vehicle design. The carbon nanotube (CNT) sheet-based heating system offers a lightweight alternative by integrating heating elements directly into the battery module. These CNT sheets, with thermal conductivities exceeding 1000 W/m·K, make direct physical contact with battery cells and function as resistive heaters when activated. The system employs pulse-width modulation to precisely control heating rates between 0.5-2°C per minute, ensuring uniform temperature rise without creating hotspots that could damage cells. This direct-contact approach reduces preconditioning time by 40-60% compared to conventional fluid-based systems while eliminating the weight and complexity of dedicated fluid loops.
For vehicles with existing thermal management infrastructure, the multi-loop thermal management system separates battery and radiator thermal circuits using dual heat exchangers and intelligent valve control. This architecture thermally isolates the battery from the radiator during charging in cold environments, preventing heat loss to ambient air and enabling more efficient warming. The system transitions between heating and cooling modes based on real-time operational data, maintaining battery temperature within the optimal 15-35°C range for both charging and discharging. This adaptability across ambient conditions from -30°C to +45°C ensures consistent performance regardless of climate, addressing a key limitation of single-mode thermal systems.
System reliability in extreme conditions is enhanced through redundant heating mechanisms that ensure continued battery preconditioning even during component failures. If the primary heater malfunctions, the control logic detects the failure and reroutes a secondary heater—originally designated for a different thermal load—to warm the battery. This fail-safe approach prevents vehicle inoperability due to single-point failures in the thermal system, significantly improving cold-weather reliability without requiring duplicate components for each thermal function.
The multi-mode thermal management system further optimizes energy usage by coordinating thermal control across both battery and passenger cabin systems. Rather than treating these as separate domains, the system implements five operational modes tailored to different temperature scenarios, including a dedicated mode for cold-temperature charging. This integrated approach reduces the load on auxiliary heaters by sharing thermal resources between subsystems, extending driving range by 5-15% in cold conditions by minimizing parasitic energy consumption.
7. Smart Control Algorithms for Dynamic Thermal Regulation
Thermal management during EV charging requires balancing multiple objectives: maintaining optimal battery temperature, minimizing energy consumption, and ensuring system longevity. Advanced control algorithms enable these goals by adapting thermal strategies to changing conditions in real time.
Conventional thermal systems often implement fixed setpoints that fail to account for varying charging rates, ambient conditions, and battery states. The smart control integration approach addresses this limitation through a centralized controller that dynamically manages both HVAC and battery cooling subsystems. This system continuously monitors critical parameters including state of charge (SOC), ambient temperature, cabin temperature, and battery thermal state. Based on this data, it modulates electronic expansion valves, bypass conduits, and heat exchangers to match battery temperature to the optimal target—typically 25°C for normal charging and 15-20°C for fast charging. This real-time adaptability reduces energy consumption by 15-25% compared to fixed-setpoint systems while maintaining cell-to-cell temperature variations below 3°C.
For fast charging scenarios, the dynamic cooling control logic implements preemptive thermal management based on anticipated heat generation. Unlike reactive systems that activate only after temperature rises, this approach initiates cooling before thermal loads peak, preventing temperature spikes that could trigger charging power reductions. The system uses electric water pumps and chillers with variable capacity control, activating cooling only when the battery temperature exceeds optimal thresholds. This selective approach avoids unnecessary cooling when the battery is already at favorable temperatures (15-25°C), conserving energy and reducing system wear. Vehicle-specific battery charging maps further customize the control strategy, optimizing the balance between charging speed and battery longevity based on the particular cell chemistry and pack configuration.
Traditional thermal control systems react to temperature changes after they occur, creating lag times that allow thermal excursions beyond optimal ranges. The feedforward thermal control algorithm overcomes this limitation by estimating heat generation from electrochemical models before temperature increases manifest. This predictive approach calculates thermal loads based on current, voltage, and internal resistance data, enabling the system to set coolant temperatures proactively. The algorithm implements incremental cooling adjustments that maintain battery temperature within ±2°C of target values, avoiding the large thermal oscillations common in reactive systems. This stability not only improves charging efficiency but also reduces thermal stress on battery components, extending cycle life by reducing degradation mechanisms triggered by temperature fluctuations.
Environmental adaptability is further enhanced through multi-mode thermal regulation that selects cooling pathways based on ambient and component-specific temperatures. The controller evaluates thermal conditions and switches between active cooling (compressor-based), passive cooling (radiator-based), and cold storage cooling paths to maximize efficiency. For instance, at ambient temperatures below 15°C, the system bypasses energy-intensive compressor cooling in favor of radiator-based heat rejection, reducing energy consumption by 30-50%. This context-aware approach ensures thermal safety across diverse scenarios while minimizing the energy penalties associated with thermal management.
8. Battery Cooling via Air Conditioning System Integration
Integrating battery cooling with the vehicle's air conditioning system offers significant advantages in packaging efficiency and thermal performance, particularly during high-power charging when heat generation can exceed 3-5 kW in a typical EV battery pack.
Conventional front-mounted radiator systems rely heavily on ambient air for heat rejection, limiting their effectiveness when ambient temperatures exceed 30-35°C. The closed-loop refrigerant cycle with heat recovery and regeneration addresses this limitation by connecting the battery's thermal management unit directly to the vehicle's refrigerant loop. This dual-medium system circulates coolant through the battery while exchanging thermal energy with the refrigerant cycle via a chiller unit. Unlike radiator-based systems limited by ambient conditions, this refrigerant-based approach can maintain battery temperatures 10-15°C below ambient, enabling consistent fast-charging performance even in hot climates. The shared architecture between battery cooling and cabin air conditioning reduces component count and system complexity while improving thermal response times by 30-50% compared to separate systems.
A distinctive feature of this integrated approach is its ability to recover waste heat generated during cooling operations. The heat recovery-enabled heating unit captures thermal energy that would otherwise be rejected to the environment and redirects it for battery heating when needed. This bidirectional capability enables the system to transition between cooling and heating modes without requiring separate thermal circuits, reducing system mass by 15-25% compared to conventional designs with dedicated heating elements. The control system intelligently switches between operating modes based on battery state and ambient conditions, optimizing energy utilization across the thermal management system.
For charging infrastructure, the integrated heat pump thermal management system for charging piles applies similar principles to auxiliary batteries within charging stations. This system addresses thermal challenges in extreme environments through a heat pump architecture with multiple solenoid valves, water pumps, and a centralized controller. Unlike conventional charging station designs that treat thermal management as an afterthought, this approach incorporates waste heat recovery from power electronics to assist in battery heating during cold conditions. This integration improves overall energy efficiency by 20-30% while ensuring optimal battery temperature during both active charging and standby states.
The multi-mode operational framework enables dynamic switching between heat pump cooling, radiator cooling, and heater-assisted heating based on real-time sensor data. This adaptability ensures effective thermal management across ambient temperatures ranging from -30°C to +50°C without requiring oversized components designed for worst-case scenarios. The modular design supports scalability across charging stations with power ratings from 50 kW to 350+ kW, maintaining consistent thermal performance despite varying heat loads. By stabilizing battery temperature during high-power charging sessions, this solution improves both safety and longevity while enhancing the reliability of the charging infrastructure network.
9. Refrigerant-Based Battery Cooling Systems
As EV charging powers increase beyond 150 kW, the thermal management requirements exceed the capabilities of traditional cooling methods. Refrigerant-based systems offer superior cooling capacity and temperature control, enabling sustained high-power charging without thermal limitations.
Conventional single-loop air conditioning systems struggle to simultaneously manage cabin and battery cooling during fast charging, often requiring compressor operation at 80-100% capacity with associated noise and efficiency penalties. The dual refrigerant circulation architecture addresses this challenge by separating thermal duties into two independent loops: a primary loop for cabin conditioning and a secondary loop dedicated to battery cooling. This configuration allows the battery cooling loop to operate aggressively during charging while maintaining moderate loads on the primary compressor. Thermal testing shows this approach can maintain battery temperatures below 30°C even during 250 kW charging sessions, while reducing compressor energy consumption by 20-35% compared to single-loop systems operating at maximum capacity.
The compressor operation strategy represents a significant advancement over conventional approaches. The battery-focused secondary compressor operates at higher speeds (3000-6000 RPM) during fast charging while the primary compressor maintains minimal load (1000-2000 RPM) for cabin comfort. This targeted operation improves not only thermal efficiency but also acoustic performance, reducing interior noise levels by 3-5 dB compared to single high-capacity compressor systems. The separate cooling circuits further enable precise temperature control for each domain, allowing battery temperature to be optimized for charging efficiency (15-25°C) while maintaining cabin comfort at different setpoints (20-24°C) without compromise.
An alternative approach shifts cooling infrastructure entirely off the vehicle through an external thermal management system that incorporates a refrigerant reservoir and circulation loop within the charging station. This configuration eliminates the need for oversized onboard cooling components, reducing vehicle weight by 5-10 kg and simplifying internal packaging. The system utilizes a specialized connector that integrates both electrical charging terminals and refrigerant lines, creating a unified interface that activates automatically upon connection. Once engaged, a refrigerant pump circulates coolant from the external reservoir through the vehicle's battery chiller at rates of 0.5-2 L/min, providing cooling capacities of 5-15 kW without burdening the vehicle's internal systems.
The integrated connector design represents a particularly innovative element, as it automates refrigerant flow through mechanical valve actuation when coupled. After charging completes, the system recovers refrigerant back into the external reservoir, preventing residual weight from remaining in the vehicle. This approach not only enhances charging station efficiency but also supports compatibility across various EV architectures without requiring standardized onboard cooling systems. The external cooling solution proves especially valuable for vehicles with space constraints or weight sensitivity, offering flexibility without compromising thermal performance during high-power charging sessions.
10. Battery Temperature Equalization and Cell-Level Thermal Balancing
Temperature uniformity across battery cells is critical for performance, longevity, and safety during charging. Even modest temperature variations of 5°C between cells can create 20-30% differences in internal resistance, leading to imbalanced current distribution, accelerated aging, and reduced charging efficiency.
Conventional cooling systems often create temperature gradients due to uneven coolant distribution among parallel battery modules. The real-time flow equalization system addresses this challenge by implementing separate heat exchangers, flow sensors, and control valves for each battery box. A centralized controller continuously monitors temperature data and dynamically adjusts individual valve positions to balance coolant flow rates, typically between 0.5-2 L/min per module. This active distribution eliminates the inconsistencies caused by unequal pipe lengths and varying flow resistances, reducing module-to-module temperature differences from typical values of 4-7°C to less than 2°C. The system's adaptive regulation ensures uniform heat exchange across all modules regardless of their position within the pack, improving both charging performance and cycle life.
Within individual battery modules, thermal gradients commonly develop along the coolant flow path as heat is absorbed progressively. The variable thermal coupling mechanism offers an innovative solution by actively modulating heat transfer rates between cells and coolant. This is achieved using adjustable heat transfer members whose contact surface area changes based on cell position and temperature. For downstream cells that typically run hotter, the system increases thermal coupling to enhance cooling, while upstream cells receive reduced coupling to prevent overcooling. This position-specific thermal management maintains cell-to-cell temperature variations below 1.5°C even during 3C charging rates, significantly improving safety margins and enabling higher sustained charging powers without thermal limitations.
For large-scale battery systems with multiple parallel modules, direct cooling methods provide another pathway to achieving thermal uniformity. The direct contact cooling architecture employs dedicated heat exchangers and pump systems connected directly to battery modules, with temperature sensors at critical locations including coolant inlet, outlet, and within cell groups. This configuration allows precise regulation of coolant flow to maintain the battery pack within an optimal operating range of 25 ± 3°C. Unlike air or fan-based systems that create significant thermal gradients due to uneven airflow, this direct approach ensures consistent cooling across the entire battery volume. The system's ability to provide rapid thermal response during fault conditions adds a critical safety layer, particularly during high-rate charging when thermal runaway risks are elevated.
11. Heat Pipes and Thermally Conductive Materials
As EV battery energy densities increase beyond 250 Wh/kg, conventional thermal management approaches face limitations in heat transfer efficiency. Advanced thermal materials and heat pipe technologies offer enhanced conductivity and more uniform temperature distribution during high-power charging.
Traditional cooling systems often rely on thermal interface materials (TIMs) with conductivities of 1-5 W/m·K, creating a significant thermal resistance between cells and cooling systems. The welded heat pipe structure eliminates this bottleneck by directly bonding the heat transfer plate to the coolant channel without intermediate materials. This configuration enables direct thermal contact between battery cells and the cooling surface, improving effective thermal conductivity by 300-400% compared to TIM-based solutions. The heat pipe surrounds the coolant channel and interleaves between stacked cells, creating a compact cooling architecture that maintains consistent performance across the battery pack. This direct thermal pathway supports charging rates up to 4C without exceeding temperature limits, while reducing manufacturing costs by eliminating expensive high-performance TIMs.
Low-temperature charging presents distinct challenges, as lithium plating occurs rapidly below 10°C, permanently degrading battery capacity. The carbon nanotube (CNT) sheet heating system addresses this through ultra-conductive materials with thermal conductivities exceeding 1000 W/m·K. These CNT sheets make direct contact with battery cells and generate localized heat through resistive heating when current is applied. Unlike conventional fluid heaters that warm cells indirectly, this direct contact approach reduces preheating time from 20-30 minutes to 5-10 minutes before fast charging can begin. The system's PWM controller and temperature sensors ensure precise heating rates between 0.5-2°C per minute, preventing thermal shock while quickly bringing cells to optimal charging temperature.
Single-sided cooling systems create temperature gradients within individual cells, as heat must conduct through the entire cell thickness. The upper and lower liquid cold plates address this limitation by cooling both surfaces of the battery module simultaneously. This dual-sided approach reduces the maximum thermal path length by 50%, decreasing internal temperature gradients from 5-7°C to less than 3°C during fast charging. The bidirectional coolant flow further enhances thermal uniformity by creating balanced heat extraction across the module. An intelligent thermal controller dynamically switches between high-power cooling mode (pump speeds of 2500-3500 RPM) during charging and energy-efficient mode (1000-1500 RPM) during normal operation, optimizing energy consumption while ensuring effective thermal management across all operating conditions.
12. Safety Mechanisms for Overheating and Thermal Runaway Prevention
Thermal runaway represents the most severe safety risk in lithium-ion batteries, with propagation temperatures typically between 130-150°C depending on cell chemistry. Effective safety mechanisms must not only prevent initial cell overheating but also contain thermal events if they occur.
Conventional thermal management systems often lack the capacity to address localized heating in individual cells, allowing thermal runaway to propagate across the battery module. The dual-circuit thermal management system introduces tiered and localized cooling within battery modules to address this vulnerability. The internal circuit handles standard cooling through a dedicated heat exchanger, while the external circuit, connected to the vehicle's HVAC system, activates during thermal emergencies. This architecture enables targeted intervention when a single cell approaches critical temperatures (typically 80-90°C), preventing propagation to adjacent cells. Temperature sensors with 0.5°C accuracy monitor individual cell groups, triggering escalated cooling responses when thresholds are exceeded. This multi-level approach ensures both energy efficiency during normal operation and rapid response during thermal events.
Fast-charging scenarios create particularly challenging thermal conditions, with heat generation rates of 3-5 kW in typical EV battery packs. The hybrid heat exchange apparatus combines internal and external coolant loops managed by a temperature-aware controller that continuously monitors cell temperatures with ±1°C precision. This controller dynamically adjusts both charging power and cooling circuit activation based on real-time thermal conditions, reducing charging current by 20-40% if temperatures approach upper limits (typically 40-45°C). The system incorporates a thermal interface within the charging station itself, allowing external coolant to supplement the vehicle's internal cooling during high-power charging. This hybrid approach maintains safe operating temperatures without requiring oversized onboard cooling systems, optimizing both cost and energy efficiency.
Environmental adaptability presents another critical safety dimension, as thermal management requirements vary dramatically across climate conditions. The multi-mode circulation control system enables simultaneous heating and cooling of different battery regions through configurable fluid routing and multiple heat exchangers. In cold environments (-20°C to 0°C), the system prioritizes battery heating to prevent lithium plating, while in hot conditions (35°C+), it maximizes cooling capacity to prevent thermal runaway. This flexibility ensures thermal stability across ambient temperatures from -30°C to +50°C without compromising safety or charging performance. By intelligently leveraging ambient air for passive cooling and redirecting waste heat during cabin conditioning, the system maintains optimal battery temperatures with minimal energy expenditure, indirectly supporting thermal safety while extending vehicle range.
Get Full Report
Access our comprehensive collection of 165 documents related to this technology
Identify Key Areas of Innovation in 2025
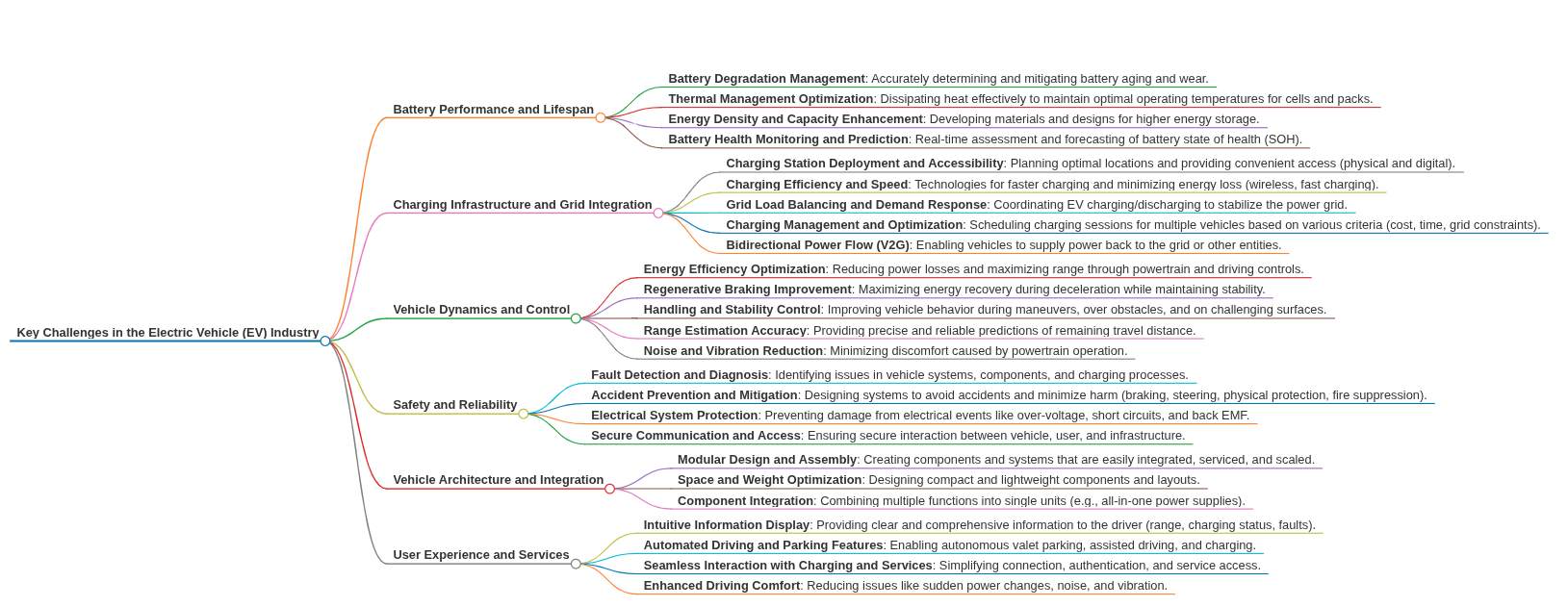