Innovations in EV Batteries with Lithium-Metal Anodes
Lithium metal anodes promise theoretical capacities of 3860 mAh/g—ten times that of conventional graphite—but face significant challenges in practical implementation. Current designs struggle with dendrite formation during cycling, volumetric expansion exceeding 100%, and rapid capacity fade due to continuous solid electrolyte interphase (SEI) formation.
The fundamental challenge lies in stabilizing the highly reactive lithium metal surface while maintaining the high ionic conductivity needed for practical charge/discharge rates.
This page brings together solutions from recent research—including three-dimensional architectures with conformal protection layers, composite protective films combining ionic and electronic conductivity, and novel surface modification approaches using carbon-based materials. These and other approaches focus on achieving stable cycling while maintaining the high energy density advantage of lithium metal.
1. Negative Electrode with Micron-Scale Particle Protective Layer for Lithium Metal Batteries
SAMSUNG ELECTRONICS CO., LTD, 2024
Negative electrode for lithium metal batteries with improved cycle life and reduced volumetric change during charging. The negative electrode has a protective layer on the lithium metal surface with particles sizes between 1-100 microns. The protective layer has a Young's modulus of 106 Pa or greater. This provides mechanical strength to prevent dendrite growth and volumetric expansion during charging. The protective layer also improves lithium deposition density compared to bare lithium metal electrodes.
2. Lithium Metal Composite Electrode with In Situ Grown Conductive Layer and 3D Framework Structure
Contemporary Amperex Technology Co., Limited, 2024
Lithium metal composite electrode material for lithium metal batteries with improved cycle stability and reduced dendrite formation compared to conventional lithium metal electrodes. The composite electrode material has a lithium-containing conductive layer grown in situ on the surfaces of lithium metal particles. This layer isolates the lithium metal from the electrolyte to reduce irreversible reactions and dendrite growth. The layer includes an inorganic lithium compound and lithium alloy. The layer serves as a 3D framework structure that coats the lithium metal particles. This framework reduces volume expansion and dendrite formation during cycling. The composite electrode material is prepared by mixing lithium metal, a metal compound, and conductive carbon, then heat treating to grow the in situ layer.
3. Lithium Metal Electrode with Porous Carbon Layer Formed by Gas Desorption for Dendrite and Side Reaction Mitigation
CONTEMPORARY AMPEREX TECHNOLOGY CO., LIMITED, 2023
A lithium metal negative electrode for lithium-ion batteries that addresses the issues of dendrite formation and interface side reactions. The electrode has a porous carbon layer with pores formed by desorbing adsorbed gas during slurry coating. This creates a 3D pore structure in the carbon layer that prevents dendrite growth and reduces side reactions compared to a smooth carbon layer. The pore structure allows lithium metal to deposit inside the pores instead of on the surface, reducing dendrite formation. The pores also provide a pathway for lithium ion transfer, mitigating side reactions.
4. Batteries with Lithiated Carbon-Coated Lithium Anodes, Sulfurized Carbon Cathodes, and Graphene Nanoribbon-Modified Separators
WILLIAM MARSH RICE UNIVERSITY, 2023
Batteries with improved safety, cycling stability, and energy density by using lithiated carbon-coated lithium metal anodes, sulfurized carbon cathodes, and graphene nanoribbon (GNR) modified separators. The lithiated carbon coating on lithium metal prevents dendrite formation during charging, the sulfurized carbon cathodes have high capacity and reduced polysulfide shuttle, and the GNR-modified separators prevent sulfur migration.
5. Si─O Molecular Engineering Enhances Cathode‐Anode Interface Stability for High‐Loading and High‐Voltage Layered Cathode‐Lithium Metal Batteries
shu yang, zhoujie lao, zhuo han - Wiley, 2025
Abstract Nickelrich layered cathodes and lithium metal anode are promising for the next generation highenergydensity batteries. However, unstable electrodeelectrolyte interface induces structural degradation battery failure under highvoltage highloading conditions. Herein, we report a fluorosilanecoupled electrolyte stabilizer with 1H, 2H, 2Hperfluorooctyltrimethoxysilane (PFOTMS), which presents higher adsorption energy LiNi 0.8 Co 0.1 Mn O 2 cathode than solvents through conjugation of SiO bonds therefore is oxidized on its surface to derive an interfacial layer rich in F species. This architecture effectively stabilizes structure, suppresses transition migration, promotes Li + conduction uniform deposition, also side reactions both anode. unique stabilization mechanism enables Li||NCM811 achieve capacity retention rate 80.8% after 600 cycles at 4.7 V. The Li||LiCoO cell high mass loading 20 mg cm 2 achieves remarkably highcapacity 92.79% 500 4.4 work proposes that overcomes limitations practical nickelrich cathode/lithium
6. Ionic Liquid Additive with Symmetrical Cation Structure for Uniform Protective Layer Formation on Lithium Metal
KOREA ADVANCED INSTITUTE OF SCIENCE AND TECHNOLOGY, 2025
Additive for lithium metal batteries that reduces dendrite growth and improves battery life. The additive is an ionic liquid compound that forms a uniform protective layer on lithium metal during charging/discharging. The compound has a cation with a lower reduction potential than lithium, and a symmetrical structure with even numbers of identical aliphatic groups bonded to the central element. This prevents self-aggregation and allows complete coverage of the lithium surface. The additive can be added to the electrolyte to suppress dendrite growth, induce uniform lithium deposition, and improve battery life and safety compared to conventional additives.
7. Lithium Metal Anode with LiF-LiI Protective Layer Formed by Co-Evaporation
BELENOS CLEAN POWER HOLDING AG, 2025
Lithium metal anode for lithium-ion batteries that reduces dendrite growth and improves battery lifetime. The anode has a protective layer containing LiF and LiI. The layer is deposited by simultaneously evaporating LiF and LiI compositions. The LiI leaches out during cycling and replenishes lithium lost from the cathode, mitigating dead lithium accumulation.
8. Electrolyte Composition with Sulfide Compound Additive for Lithium-Sulfur Batteries
LG ENERGY SOLUTION LTD, 2025
Electrolyte for lithium-sulfur batteries that improves capacity and lifetime of the battery by preventing sulfur leaching and lithium metal dendrite formation. The electrolyte contains a sulfide compound additive in addition to the lithium salt and organic solvent. The sulfide compound helps stabilize the lithium metal anode and reduce sulfur dissolution from the cathode during cycling. This improves efficiency, capacity retention, and cycle life of lithium-sulfur batteries compared to conventional electrolytes.
9. Lithium Metal Battery with Interfacial Metal Layer and Dispersed Metal Particles in Negative Electrode
TOYOTA JIDOSHA KABUSHIKI KAISHA, TOHOKU UNIVERSITY, 2025
Lithium metal battery with improved capacity retention and reduced resistance by adding a thin metal layer between the negative electrode and the lithium metal, and dispersing metal particles in the negative electrode active material. The metal layer and dispersed particles homogenize lithium plating to prevent dendrite formation and reduce resistance.
10. Solvent-Free Lithium-Ion Battery Electrode Composition with SEI Formation Inhibition
FORD GLOBAL TECHNOLOGIES LLC, 2025
Lithium-ion battery electrode composition that eliminates the need for solvents in the coating process and prevents solid electrolyte interface (SEI) formation during battery cycling. The electrode composition is made by mixing lithium organic compounds like dilithium terephthalate or dilithium 2-aminoterephthalate with active material powder and binder to form a solvent-free electrode agglomeration. This dry coating technique reduces energy consumption compared to wet coating methods. The lithium organic compounds stabilize the electrode-electrolyte interface, preventing SEI formation and irreversible capacity losses.
11. Composite Polymeric Coating with Lithium Salts and Ceramic Oxides for Dendrite Inhibition in Lithium Metal Batteries
SES HOLDINGS PTE LTD, 2025
Protective layer for preventing dendrite growth and suppressing dead lithium formation in lithium metal batteries. The protective layer is a composite polymeric substance (CPS) coating containing two or more polymers, lithium salts, and ceramic oxide particles. The CPS coating is applied to the lithium metal surface to block dendrite penetration and convert dendrites into desirable compounds like LiF, Li3N, and Li2O. The CPS coating provides mechanical strength to physically block dendrites and chemical conversion of dendrites into stable compounds.
12. Li Heteroepitaxial Deposition on Single Crystalline Ni Substrates with Enhanced Cycling Stability
zhiqiang zheng, tian qiu, zhanghua fu - Wiley, 2025
Lithium (Li) metal is recognized as a highly promising anode material for nextgeneration highenergydensity batteries. Nonetheless, dendrite growth and low coulombic efficiency significantly impede the practical application of Li anodes. The deposition morphology chemical stability are intricately linked to its crystallographic orientation. This study presents substrate engineering approach that employs singlecrystalline Nickel (Ni) facilitate epitaxial due their excellent lattice matching. findings reveal Ni(110) exhibits more pronounced heteroepitaxial effect than Ni(111). A robust {110}textured was prepared on with uniform planar lower selfdiffusion barrier Li(110) plane. improves cycling in NiLi cells full cells. Notably, Li||LiFePO4 cell utilizing high capacity retention 109.6 mAh cm2 over 350 cycles at 1 C under negativetopositive ratio 1.26. investigation highlights crucial role substrateinduced heteroepitaxy improving plating/stripping dynamics provides insights development stable anodes by orientation modification.
13. Lithium Metal Battery with Composite Electrolyte for Anodeless Configuration and Dendrite Suppression
SAMSUNG SDI CO LTD, SAMSUNG ELECTRONICS CO LTD, 2025
An anodeless lithium metal battery with improved energy density and reduced dendrite formation compared to conventional lithium metal batteries. The battery uses a composite electrolyte containing lithium metal or lithium alloy instead of a separate anode. During discharge, the composite electrolyte releases lithium ions that electrodeposit onto the lithium metal/alloy surface, forming an interconnected structure bound to the anode current collector. This prevents dendrite growth and swelling issues of a planar lithium anode. The composite electrolyte is prepared by combining lithium particles with the liquid electrolyte and coating it on the anode.
14. 3D Porous Single‐Ion Conductive Polymer Electrolyte Integrated with Ether Polymer Networks for High‐Performance Lithium‐Metal Batteries
tapabrata dam, asif javid, eunsan jo - Wiley, 2025
The integration of polymerbased electrolytes into nextgeneration lithiummetal batteries (LMBs) offers significant potential for enhancing energy density and safety. However, their development is impeded by challenges such as low ionic conductivity at room temperature, anion polarization effects, a lithiumion transference number. This investigation aims to address the limitations combining singleion conductive polymer (SICP) ether network (EPN) electrolytes. interwoven structure SICP EPN ensures uniform distribution, facilitating efficient delocalized transport. Utilizing sulfonated poly(vinylidene fluoridecohexafluoropropylene)based with enhances conductivity, electrochemical stability, mechanical strength. optimized SICPEPN membrane exhibits an 10 4 S cm 1 , stability window exceeding 4.9 V, transport number 0.58 30 C. Li/SICPEPN/NCM811 cell demonstrates initial discharge capacity 189 mAh g Coulombic efficiency 99.7% 0.1 C C, maintaining minimal fading after 250 chargedischarge cycles 0.5 C. These findings highlight present viable econom... Read More
15. Bonded <b> <i>β</i> </b>12-borophene/hybrid honeycomb–kagome silicene heterostructure: A high-capacity anode with robust structural stability for Na-ion batteries
junming fan, xiaobin niu, haiyuan chen - American Institute of Physics, 2025
The development of next-generation energy storage systems critically demands anode materials with exceptional ion capacity and structural robustness. Bonded heterostructures offer distinct advantages over conventional two-dimensional (2D) monolayers by synergistically stabilizing lattice frameworks through interfacial interactions. 2D hybrid lattices composed honeycomb kagome structures have garnered significant attention due to their unique geometries tailored electronic states. Herein, via first-principles calculations, we propose a strongly bonded 12-borophene (12-B)/hybrid honeycombkagome silicene (hhk-Si) heterostructure as high-performance for lithium/sodium-ion batteries (LIBs/SIBs). This configuration exhibits superior stability compared van der Waals counterparts, evidenced machine learning-accelerated ab initio molecular dynamics simulations spanning an extended 100 ps timeframe. demonstrates intrinsic robustness during multi-ion intercalation, coupled stable adsorption sites featuring ultralow diffusion barriers (Li: 0.35 eV; Na: 0.20 eV). Notably, the predicted max... Read More
16. Regulating Li+ Solvation, Transport, and Interfacial Robustness via Voltage Resistant Cationic Copolymer Design for Safe Lithium Metal Batteries
zhiheng zou, guang yang, haolan li - Wiley, 2025
Abstract The application of polymer electrolytes in highperformance lithium metal batteries (LMBs) is usually restricted by their sluggish ion conduction, and inferior electrochemical stability compatibility with electrodes. Here, a cationic copolymerbased electrolyte PMC developed. copolymer acryloyloxyethyl trimethylammonium bis(trifluoromethanesulfonyl)imide (AETTFSI), hexafluorobutyl acrylate (HFBA), N, Nmethylenebisacrylamide (MBA) synthesized photopolymerization carbonate electrolytes. facilitates the salt dissociation, adjusts Li + interaction chain, regulates solvation environment, thus promotes fast transport (ionic conductivity 7.19 10 4 S cm 1 , transference number 0.84) uniform deposition. electrochemically stable up 4.43 V versus /Li forms solid interphase (SEI) anode, supporting longterm (1500 h) plating/stripping test at 0.2 mA 2 mAh . Li/PMC/LiFePO 4 cell shows excellent 1C high specific capacity 134.2 g even 5C. voltageresisting, LiFrich cathode interface (CEI) LiCoO 2 Li/PMC/LiCoO over 100 cycles retention 96%. Nonflammability ... Read More
17. X-Ray Fluorescence Mapping System for In-Line Inspection of Lithium Metal Anodes via Copper Current Collector Analysis
GM GLOBAL TECHNOLOGY OPERATIONS LLC, 2025
Non-destructive, in-line quality inspection of thin lithium metal anodes in battery cells using X-ray fluorescence (XRF) mapping of the copper current collectors. By measuring the intensity of characteristic copper radiation through the lithium anode and into the current collector, the lithium thickness and defects can be inferred without analyzing the lithium itself. This allows non-contact, non-destructive, in-line characterization of thin lithium anodes during manufacturing to improve quality control and reduce scrap.
18. Electrochemical Cell with Graded Thickness Interlayer for Dendrite Detection and Control
24M TECHNOLOGIES INC, 2025
Electrochemical cells with interlayers between the anode and cathode to prevent dendrite growth and mitigate safety issues like short circuiting and thermal runaway. The interlayer has a thickness that increases towards the cathode end. If a dendrite grows into the interlayer, it can be detected by monitoring the voltage potential. A battery management system can then discharge the cell and use the remaining energy to power other devices, removing cell energy to create a safe condition. The interlayer voltage can also be actively changed to stop dendrite growth or dissolve it.
19. Electronic Cigarette Cartridge with Replaceable Absorbent Element and Membrane-Puncturing Mechanism
JOYETECH EUROPE HOLDING GMBH, 2025
Electronic cigarette cartridge design that allows replacing just the absorbent element when the tobacco liquid runs out, instead of the entire cartridge. The cartridge has a liquid container with a sealing membrane at the bottom. Below the membrane is a puncturing unit with an elastic element. The heater is attached to the puncturing element. When the cartridge is assembled, the puncturing element punctures the membrane and seals the liquid in the container. The elastic element compresses to hold the puncturing element and membrane. When the liquid runs out, the elastic element extends to lift the puncturing element and membrane, allowing new liquid to be added. This prevents leakage when the cartridge is inserted into the battery assembly. The cartridge can be disassembled and just the absorbent element replaced.
20. Construction of Ionic Conductive Electrode/ Electrolyte Interphases via Li<sup>+</sup> Coordination Regulator for 4.7 V Li/ LiNi<sub>0.9</sub>Co<sub>0.05</sub>Mn<sub>0.05</sub>O<sub>2</sub> Batteries
wei wang, yx chen, z y wang - Wiley, 2025
Abstract Lithium metal batteries (LMBs) using highvoltage nickelrich layered cathode (LiNi x Co y Mn 1xy O 2 , NCM, x 0.9), though delivering high energy density, suffer from critical instability of electrode/electrolyte interphases and structural degradation NCM cathodes, causing rapid capacity fading. Here, trimethoxyboroxine (TMOBX) is used as a lithiumion coordination regulator in the commercial carbonate electrolyte to improve cycling stability LMBs at voltage. Owing strong polarized BO bonds, TMOBX not only prefers interact with Li + because electron density O, but also attracts more PF 6 solvation structure due positively charged B, resulting robust ionic conductive electrode/ rich PF compounds, BF species. Moreover, effectively eliminates HF electrolyte, all which can avoid lithium dendrites, suppress corrosion LiNi 0.9 0.05 (NCM90) dissolution transition ions. Consequently, Li/Li symmetrical cells exhibit highly enhanced 500 h 1 mA cm 2 retention Li/NCM90 increases 45.7% 80.5% after 100 cycles an ultrahigh cutoff voltage 4.7 V.
Get Full Report
Access our comprehensive collection of 113 documents related to this technology
Identify Key Areas of Innovation in 2025
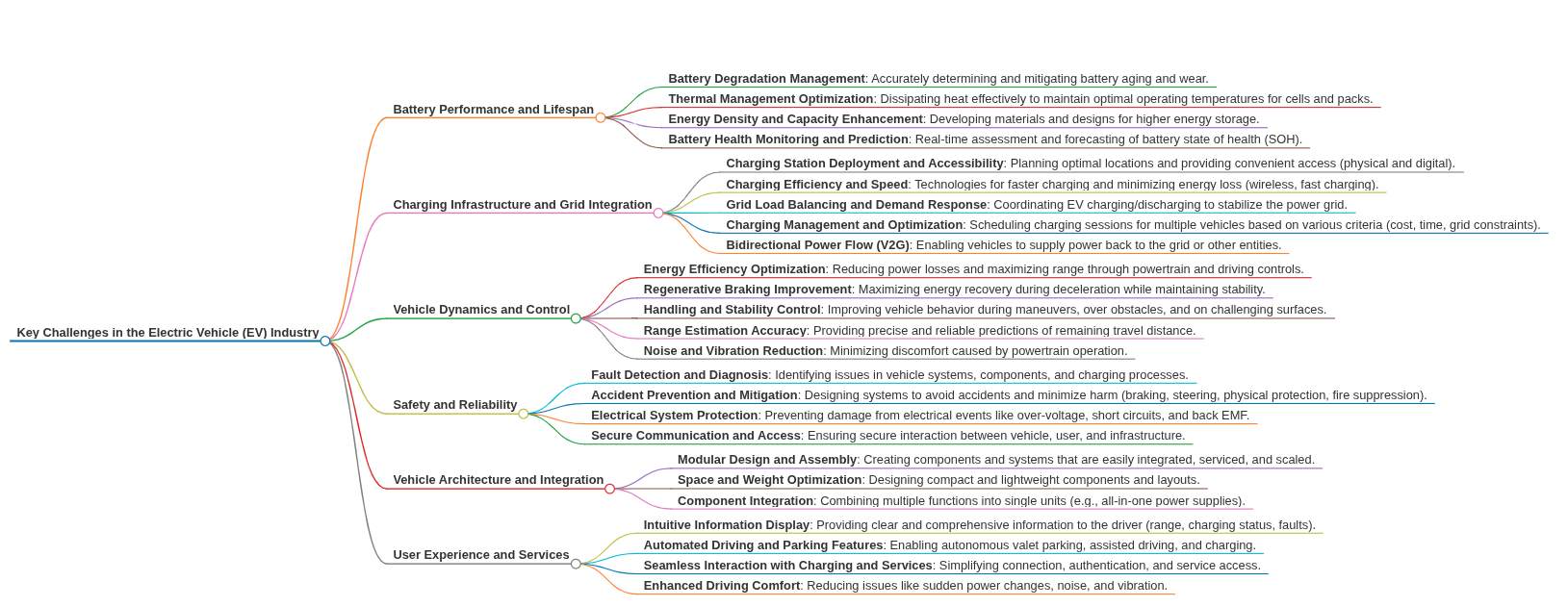