Lithium-Ion Battery Coatings for Thermal Runaway Prevention
In electric vehicle batteries, thermal events can cascade rapidly between cells, with temperatures exceeding 150°C during thermal runaway. Current data shows that without proper thermal barriers, cell-to-cell propagation can occur in less than 60 seconds, releasing gases and potentially compromising the entire battery pack's integrity.
The fundamental challenge lies in developing coating materials that can both insulate cells from thermal propagation while maintaining effective heat dissipation during normal operation.
This page brings together solutions from recent research—including syntactic foam insulation with hollow glass microspheres, phase change materials (PCMs) for thermal absorption, composite separators with heat-absorbing particles, and cure-in-place thermally conductive interfaces. These and other approaches focus on practical implementation in automotive battery packs while meeting strict safety and performance requirements.
TABLE OF CONTENTS
1. In-cell Reactive Coatings: Stopping Runaway at the Electrode Surface
A logical safety architecture begins at the smallest length scale, the electrochemical interfaces where heat and gas are first generated. Conventional solid-electrolyte interphase (SEI) layers are fragile and irregular, so they can tear apart under high current, exposing fresh active material and accelerating exothermic reactions. The thermally cross-linking SEI film deposits a nitrogen-containing polymer onto the active-material powder before calendaring. During the formation cycle the polymer self-assembles into a nanoporous coating only a few tens of nanometres thick. When cell temperature creeps into the 80 - 280 °C window, pendant groups cross-link, stiffening the film, throttling Li-ion transport, and pinning reactive oxygen in the cathode lattice. Impedance growth at room temperature remains negligible, yet the cell gains an autonomous current-interruption mechanism that requires no external circuitry.
A complementary safeguard is the dendrite-blocking lithium-ion conductor layer. This solid or gel electrolyte, rich in ceramic ion conductors, can be cast onto each electrode prior to winding. Because the layer is both rigid and highly conductive, it lets Li-ions travel freely while arresting sharp metallic dendrites. Heat is spread laterally toward the cell can, lowering hotspot intensity during aggressive charge. Abuse testing shows that the conductor layer sustains over-charge conditions of 1.5C for 30 min without internal short formation, whereas control cells puncture the separator within 8 min. The strategy is attractive for 4680-format cylindrical cells, where long winding paths increase the statistical chance of burrs and dendrites.
Internal metal burrs and weld spatter can still initiate localized shorts after electrode stacking has finished. The in-cavity gas-phase coating process addresses these latent defects in a single vacuum step. Alternating sub-kPa pulses of organometallic precursors and oxidants create conformal films across every interior surface, including foil edges, vent components, and tab welds. An optional on-board laser flash densifies the coating in a few milliseconds, generating graded compositions that both protect against corrosion and preserve electrolyte wettability. By folding the treatment into standard can sealing operations, manufacturers can eliminate a post-assembly rinsing stage and cut particulate contamination by 95 percent.
Taken together, these three reactive coatings intercept thermal events at their earliest inception: they moderate parasitic reactions, block dendrite growth, and passivate stray metal. When packaged inside large-format automotive cells, they cut the likelihood of a catastrophic short to a small fraction of that for unprotected assemblies, yet they require no additional sensors or control logic.
2. Separator Engineering: From Nanoscopic Ceramics to Melt-Free Membranes
Even a perfect electrode interface cannot survive if the polymer separator shrinks or melts. Conventional polyolefin films soften near 140 °C, and once pore closure begins, current concentrates and heat races ahead of any external cooling loop. The conformal ALD alumina coating tackles this weakness by growing an Å-level layer of Al₂O₃ across both faces and, crucially, down each internal pore wall. Atomic layer deposition, preceded by a mild plasma hydroxylation, delivers pin-hole-free coverage without clogging pores. Mechanical puncture strength doubles, dimensional stability extends 70–100 °C beyond the polymer’s own melt point, and ionic resistance climbs by less than 5 percent. Because the film is only a few hundred cycles thick, roll-to-roll web handling equipment requires minimal modification.
Where cost or throughput rule out gas-phase methods, designers can adopt the particle-bonded high-temperature separator. Here, nano- to micro-scale ceramic particles are packed into a self-supporting mat, then tack-welded at contact points with a porous polyimide binder. Unlike a PP-PE laminate, the entire skeleton is melt-free, so the membrane holds dimension beyond 200 °C and maintains porosity above 65 percent. Pilot-line coating trials show that line speeds of 30 m min-¹ are achievable with hot-calendar consolidation, making the approach competitive with current tri-layer separators.
A third route chemically reinforces existing fibrous membranes. The phosphate-grafted fibrous separator esterifies surface –OH groups of cellulose or glass fibers using phosphate or phosphite treatments. Shrinkage in a 180 °C hold test drops from 22 percent to below 4 percent, and electrolyte oxidation currents fall by roughly one-half, thanks to scavenging of residual water. Capacity retention over 1,000 cycles at 1C improves by 8–10 percent relative to an untreated control.
In situations that require both a thermal fuse and post-shutdown stability, multilayers excel. The dual-layer composite separator positions a single-side ceramic coat on a PP core and caps the opposite face with a polyimide. Once the PP melts, the ceramic/alumina network prevents puncture, while the high-temperature polymer keeps shrinkage below 3 percent. For packs where hotspot equalisation is as important as tear strength, designers can laminate a thin graphite or metal-oxide film using the thermally conductive multilayer coating. Through-plane conductivity remains low, preserving electrical isolation, but in-plane k exceeds 30 W m-¹ K-¹, sufficient to drag a 5 mm hotspot over several centimetres in less than a minute.
Collectively, these separator technologies provide graduated responses: pore shutdown at 140 °C, melt-free mechanical integrity beyond 200 °C, and lateral heat spreading to prevent cell-wide fusion. They form the second defensive shell, right outside the electrode coatings discussed earlier.
3. Latent-Heat Media at the Cell Casing: PCM Sleeves, Inserts, and Internal Capsules
Once chemical triggers are moderated, the next hurdle is transient thermal spikes generated by fast charging, high-power pulses, or mild abuse. Instead of relying solely on bulky cold plates, engineers increasingly embed phase-change materials (PCMs) directly at the cell casing. Early sleeves, however, left air gaps that paradoxically insulated the hottest regions. The gap-filling PCM-elastomer composite sleeve disperses micron-scale paraffin reservoirs (latent heat ≥5 J g-¹, melt 40–70 °C) in a compliant silicone matrix. At assembly the elastomer wets every ridge and weld bead, eliminating voids; during operation it soaks up 60–80 kJ per litre before temperature climbs more than 10 °C. For prismatic pouch cells, cycle-life tests over 1,500 fast-charge events show capacity fade suppressed by 15 percent versus airflow-cooled references.
Where sleeves add unacceptable radial thickness, designers can place PCM even closer to the electrodes. The double-bent seal PCM insert exploits the unused fold in a pouch perimeter, inserting a slim PCM ribbon that sits millimetres from the jelly-roll. Thermal FEA indicates peak temperature suppression of 12–16 °C during a 3C discharge, yet external pack volume stays unchanged. Cylindrical and prismatic formats replicate the idea with a micro-encapsulated PCM coating sprayed onto the can wall. A silica shell encapsulates each PCM droplet, so there is no free liquid at any state-of-charge. Subsequent winding or stacking of electrodes proceeds without contamination, and the latent-heat layer survives to 2,000 operational cycles without delamination.
An ambitious concept unites these approaches: the internal PCM microcapsule and tube network. Micro-tubes, co-extruded from aluminium and polyimide, snake through the capsule layer, creating a bidirectional heat highway toward an external coolant plate. During a runaway event, the PCM must first melt, absorbing 200-250 kJ m-², before heat reaches the tube. Only then does the liquid coolant carry energy away, ensuring that average cell core temperature never exceeds 120 °C in a worst-case simulation.
Latent-heat materials can also function as strategic firewalls at module or sub-pack interfaces. The PCM heat-sink interface between battery arrays deposits a 2-mm meltable layer on the coolant plate that separates two strings. If one string runs away, the PCM must absorb and dissipate a large fraction of the heat flux before the opposite array can ignite. Accelerated abuse tests (over-charge to 8.4 V per cell at 3C) demonstrate that the second string remains 60 °C cooler and avoids venting altogether.
Where duty cycles saturate a PCM, hybrid regeneration is needed. The fin-assisted PCM regeneration loop embeds aluminium fins inside the PCM block and connects them to a cold plate running glycol at 25 °C. Infrared thermography during a 10-minute 4C discharge shows that cell wall temperature peaks 18 °C lower, while regeneration between pulses empties 80 percent of stored heat within 4 minutes. This compromise preserves energy density yet authenticates the PCM for repeated fast-charge services.
Through careful composition and placement, PCM sleeves, inserts, and coatings delay or even avert thermal runaway without pumps, fans, or active controls. They represent the first macro-scale thermal layer outside the separator.
4. Module-Level Fillers: Syntactic Foams and Hybrid Heat-Extraction Matrices
Moving outward again, the empty spaces between cells become both a blessing and a curse. They moderate expansion and ease assembly, but they also allow flames, electrolyte vapors, or acoustic noise to propagate. The mould-in-place silicone syntactic foam fills these cavities with a low-viscosity, two-part vinyl-PDMS mixed with hollow borosilicate microspheres. Cure occurs at room temperature within 10 minutes, so automated filling lines can dispense the material immediately before cell insertion. Density can be tuned from 0.3 to 0.5 g cm-³, and compression-set resistance exceeds 85 percent retention after 1,000 cycles of 2 percent strain. Thermocouple array tests show that a 6-mm foam barrier blocks 850 °C flame for 4 minutes, granting BMS logic time to isolate the failing string.
Passive insulation is only half the job. The silicone-rubber syntactic foam with integrated heat-exchange members co-moulds aluminium plates or serpentine tubes alongside the glass-bubble matrix. During benign operation, glycol or water-ethylene coolant pulls continuous Joule heat away, while the foam dampens vibration and cushions cell swell. If one cell heats rapidly, the low-k foam buys time until the coolant loop evacuates energy through the embedded plate, limiting propagation to adjacent cells. Drop-weight and side-impact testing reveals that the composite maintains cell spacing within ±0.3 mm, critical for modules that rely on pressure-sensitive contactors.
A newer variant integrates aerogel particles into the syntactic mix, shaving thermal conductivity to below 80 mW m-¹ K-¹ without hurting pot-life. The result is a three-function gap filler: vibration damping, fire barrier, and continuous heat spreader. Such multifunctionality is vital for skateboard chassis packs where vertical height is limited and every millimetre of clearance must contribute to safety or stiffness.
5. Intumescent, Aerogel, and Endothermic Barriers for Cell-to-Cell Containment
If a module gap filler fails to halt a runaway event, the next line of defence is a dynamic barrier that adsorbs heat, releases inert gas, or expands to choke flame. The multifunctional ceramic-endothermic blanket mixes aluminium trihydrate or hydromagnesite with silica fibres in a flexible mat. Upon hitting 200 - 250 °C the fillers decompose, absorbing up to 1,200 J g-¹ and releasing water vapour or CO₂ that dilute combustible electrolytes. Meanwhile the silica backbone remains intact to 900 °C. Flammability tests per UL-2596 show that a 5-mm blanket delays flame penetration by 11 minutes, three times better than a similar-thickness basalt felt.
Where module spacing is tight, the sublimating heat-sink coating offers a 0.3 - 2 mm film deposited directly on cell cans or steel housings. The proprietary salt-hydrate sublimes at 180 °C, drawing off hundreds of joules in the process and leaving behind a porous, thermally insulating residue. Because the coating adds under 7 kg to a 70 kWh pack, it is well suited for premium EVs that prize range.
Aerogels provide an alternative route, combining record-low conductivity with adaptable structure. The thermo-adaptive aerogel/CNT skin lines inner and outer prismatic walls. Carbon nanotubes contract below 10 °C, trapping aerogel in closed cells that retain heat during winter. At 40 °C they expand, opening conductive pathways that help evacuate heat. Cycling between −30 and +60 °C for 200 hours shows volumetric changes below 2 percent, and the skin maintains 90 percent of its super-insulating performance after thermal shock.
For second-life modules that inherit inconsistent state of health, external add-ons are attractive. The modular aerogel-SSPCM plate sandwiches an aerogel board, a solid-solid PCM, and a liquid cooling channel. Clamped onto existing prismatic packs, it grants 60 Wh kg-¹ of latent capacity and merges passive absorption with active removal. In field trials on repurposed bus batteries, thermal gradients drop from 17 °C to 6 °C during 2C fast charge.
Intumescent chemistries bring yet another function: mechanical expansion that seals gaps as temperature climbs. The silicone-to-ceramic wrap lives in the inter-cell gap. During gentle aging it remains flexible, accommodating cell swelling. Once its onset temperature of 350 °C is reached, it sinters into a rigid ceramic wall, quenching flame spread. In coin-stack calorimetry, the wrap cuts heat transfer rate by 75 percent within 90 seconds of activation.
Densely packed modules may rely on the bifunctional SiO₂ foam filler. Below 130 °C the silica matrix conducts heat to the cold plate, yet above this threshold embedded foaming agents inflate the filler to five times its original volume, isolating the failing cell. A final safeguard appears at enclosure scale in the self-gapping hybrid housing. A bonded metal skin delaminates under extreme heat, creating an air gap that throttles heat penetration while the composite frame carries crash loads.
By combining latent-heat absorption, gas dilution, expansion, and structural adaptation, these barrier layers provide graded responses that buy minutes of suppression time, letting BMS algorithms shut down or firefighters intervene.
6. High-Conductivity Interfaces: Wrappers, Directional Coatings, and Energy-Harvesting Skins
While the layers above focus on blocking or absorbing heat, other applications demand the opposite: move heat quickly to the cooling loop so that average cell temperature stays low and uniform. Traditional plastic spacers hinder that goal. The thin, thermally conductive-dielectric wrapper replaces multi-millimetre separators with a micrometre-scale film loaded with boron nitride platelets. Volume resistivity exceeds 10¹¹ Ω cm, yet through-plane thermal conductivity surpasses 2 W m-¹ K-¹. Because the film hugs the cell faces, modules gain 8–10 percent volumetric energy density and operate 5–7 °C cooler at 1C through-discharge.
Sometimes the design calls for anisotropic heat steering: remove heat downward to a cold plate while insulating flanks against neighbor interaction. The directional base-conductive/side-insulating architecture meets that need by screen-printing a ceramic-filled epoxy on the cell bottom and shrink-wrapping the sides with low-k PET. During a runaway event, radial heat flow falls by 60 percent while vertical heat flow to the plate doubles, in effect creating a one-way thermal diode.
To smear hotspots laterally without promoting cross-talk, engineers can deploy the anisotropic graphene film. Aligned graphene sheets laminated on a polyimide substrate offer in-plane k near 1000 W m-¹ K-¹, but through-plane k below 0.7 W m-¹ K-¹. A 25 µm film brings cell-to-cell temperature delta under 3 °C during 3C discharge, while adding just 12 g per cell.
Some coatings double as radiative fins. The dual-function thermal radiation coating mixes endothermic pigments with infrared-emissive fillers. Mid-IR emissivity jumps to 0.91, enabling natural convection plus radiation to dump 15 percent additional heat from the can wall when pack temperature rises above 50 °C. A cheaper counterpart, the far-infrared emissive shell, integrates FIR-active ceramics in the housing paint, allowing retrofits without disturbing internal architecture.
Heat-transfer coatings can even recover a slice of wasted energy. The nano-wettability coolant channels coat flow passages with hydrophilic nanoparticles, driving contact angles below 5 degrees and tripling the convective coefficient. Another inventive twist is the thermoelectric Bi₂Te₃ mid-section coating applied to a cylindrical cell’s equator. With a 20 °C radial gradient, the coating generates a few dozen milliwatts that feed back into the BMS, offsetting sensor power draw and slightly reducing resistive heating.
High-conductivity interfaces function best when paired with the insulating or latent-heat layers already described. Together, they shape temperature profiles, limit peak values, and extend calendar life without heavy or complex plumbing.
7. Pack-Level Structures: Passive Disconnects, Vent Reinforcement, and Targeted Suppression
Even with every inner layer performing flawlessly, a single cell can still fail catastrophically. The pack therefore needs hardware that confines that failure geographically and electrically. Continuous aluminium or copper busbars, for instance, are perfect highways for both current and heat. The fail-safe differential-CTE busbar embeds an expansive yet insulating polymer core inside a metal shell. Under runaway heat the core swells, breaking tab-to-tab connectivity within milliseconds without arcing. Testing at 400 A shows that the break induces a transient voltage spike of less than 5 V, well inside inverter tolerance.
Gas management is another critical path. Pouch stacks venting through a weak edge can spray molten lithium or conductive debris onto neighbours. The resin-reinforced pouch edge realigns the strongest machine direction of the separator with the lead tab and overlays a high-softening-point resin film. Peel strength exceeds 25 N cm-¹ at 200 °C, and abuse tests confirm that hot gasses exit through the intended relief area, not laterally into adjacent cells.
Liquid cooling resolves steady-state heat but introduces electrocution risks if coolant leaks after a crash. The two-zone coolant barrier retainer divides the enclosure into a wet volume surrounding the coated mid-sections of the cells and a dry plenum housing terminals. Pressure cycling to 2 bar shows zero leakage across the elastomeric seal for 500 hours, and dielectric strength remains above 5 kV mm-¹ even when the wet zone is flooded.
The ultimate backstop is active suppression. Thin insulation redirects heat towards a network of embedded heat pipes, while thermistors monitor for outliers. Upon a temperature excursion the sensor-triggered suppressant nozzles discharge extinguishant precisely onto the endangered area. Because activation is localised, only a few millilitres of agent are needed, avoiding the mass penalty of full-pack sprinklers. Demonstration packs pass UNECE R100.03 propagation limits with a 63 percent mass reduction compared to legacy blanket systems.
By stacking passive disconnects, reinforced vents, coolant isolation, and micro-suppression, the enclosure itself evolves into the final thermal firewall, ensuring that even a worst-case cell failure is contained within a strictly bounded zone.
Get Full Report
Access our comprehensive collection of 82 documents related to this technology
Identify Key Areas of Innovation in 2025
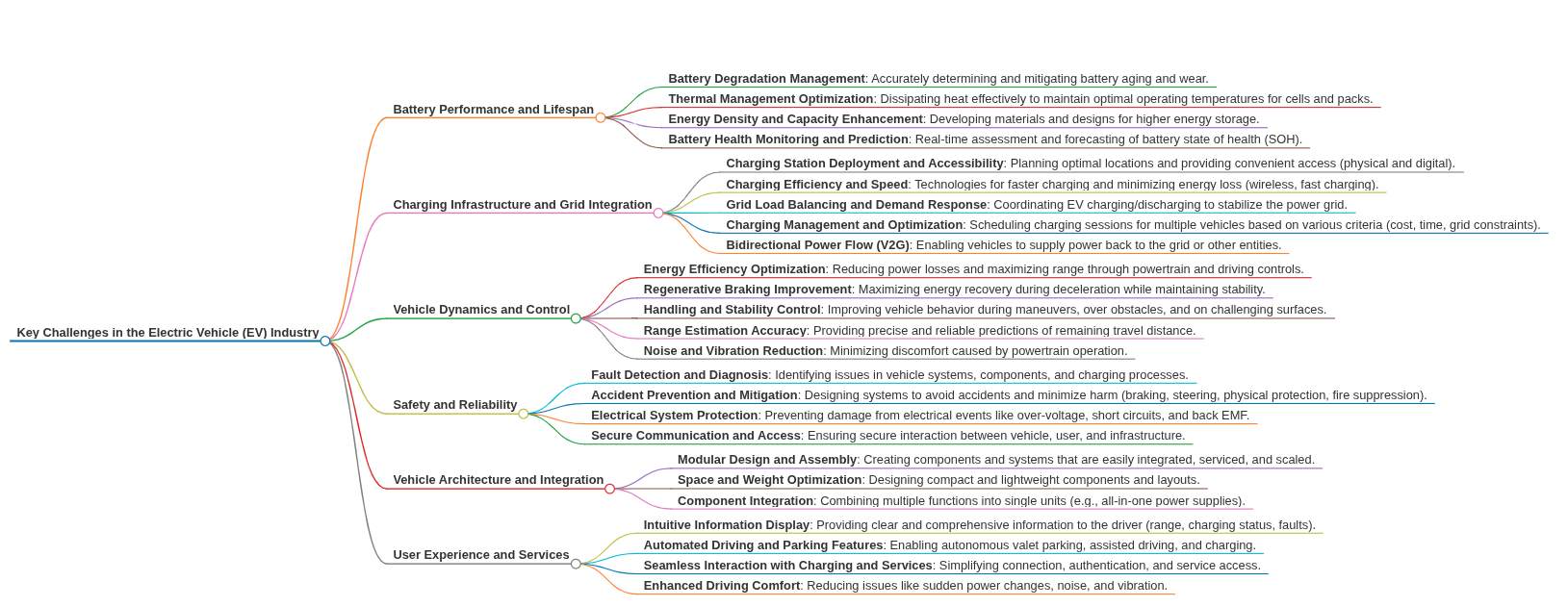