Thermal Runaway Prevention in Lithium-Ion Batteries
Electric vehicle battery thermal incidents present a critical engineering challenge, with cell temperatures potentially escalating beyond 150°C during thermal runaway events. When a single cell reaches this threshold, it can trigger a cascade of decomposition reactions, releasing gases at rates exceeding 2L/min per cell and generating heat that threatens adjacent cells in densely packed battery assemblies.
The fundamental challenge lies in detecting and containing thermal events at the individual cell level while maintaining the high energy density demands of modern electric vehicles.
This page brings together solutions from recent research—including multi-layer thermal management sheets with targeted conductivity properties, pressure-based early warning systems, active coolant discharge mechanisms, and graphite-based heat dissipation designs. These and other approaches focus on practical implementation in production vehicles while addressing both prevention and containment of thermal events.
TABLE OF CONTENTS
1. Cell Chemistry, Separator, and Electrolyte Improvements for Heat Stability
Thermal runaway is most easily stopped when a cell’s own materials refuse to feed the reaction, so intrinsic choices become the first line of defence. Nickel-rich layered oxides deliver range yet release lattice oxygen at high state of charge. The newly disclosed oxygen-buffered LiTMO cathode embeds an electro-chemically inactive oxygen-storage phase in the positive electrode. While charging or during abuse heating, this phase captures liberated oxygen before it reaches the organic solvent; during discharge it hands the oxygen back and restores the layered structure. The reversible mechanism cuts exothermic heat release, extends cycle life and lets high-Ni chemistries operate without their usual safety penalties.
Electrolyte modification reinforces this inherent stability. A flowable precursor that cures inside the assembled cell forms an in-situ hybrid polymer–inorganic electrolyte. Only a few volume percent of fast-ion ceramic particles are dispersed, yet conductivity remains 10⁻⁴–10⁻² S cm⁻¹ while the flash point rises above 200 °C. A complementary acid-scavenging bifunctional additive neutralises PF₅ and HF with Lewis-basic sites and builds thin, resilient SEI and CEI films with redox-active groups. Together the two ingredients suppress gas evolution, metal dissolution and impedance growth during high-temperature storage or fast charging.
Attention then turns to the separator, which has to halt ion transport before temperature runs away. A roll-to-roll coating of high-surface-area zeolite creates a zeolite-integrated separator coating that is electronically insulating and highly wettable; its pores adsorb water, dissolved metals and even pre-loaded flame retardants. To shorten shutdown time, a ceramic-backed polyolefin film can be dusted with phase-change particles, yielding a phase-change assisted shutdown separator. Around 130 °C the particles melt, soak up heat and flow into the pores, blocking ion transport before the base polymer shrinks. Where ultra-thin cells demand extra robustness, a stacked alumina sheet plus an amphiphilic nanofibre mesh provides a multi-layer ceramic–nanofiber separator that resists puncture, holds electrolyte and stays stable well past 200 °C.
A final safeguard is placed directly on the electrode surface. A micron-scale layer of polyolefin latex and a trace cross-linker forms a self-crosslinking safety coating. During normal cycling it is inert; once the surface reaches about 80 °C the latex melts, the cross-linker activates and the layer fuses into an impermeable film that arrests ion flow in milliseconds. Because the formulation is water-based and slot-die printable, it offers a low-cost path to adding one more intrinsic barrier against thermal runaway.
These material-level measures prevent or delay the first exothermic reactions. A pack still must keep every cell inside its operating window so that those reactions never begin.
2. Continuous Cooling and Heating Loops for Operating-Window Control
With stable chemistry in place, the next priority is temperature moderation during daily use. Rapid duty-cycle swings, harsh climates and pack ageing make that difficult, so several inventions reroute a single coolant loop or adjust operating points in real time.
A representative approach is the five-mode coolant orchestration system, which polls cell temperatures and selects Cooling, Heating, Equalisation, Preservation or Safety mode. By varying pump speed, coolant temperature and circulation time, it tightens cell-to-cell gradients without adding stack height. Looking beyond temperature alone, predictive power-balance cooling estimates instant heat generation and ramps the compressor or pump before a spike arrives, removing the lag that plagues reactive control.
When a single medium cannot handle peak loads, multi-loop architectures step in. The cascade liquid-PCM-air loop stages phase-change buffering, air convection and liquid flow so coolant enters the pack at a stepped-down temperature, preventing thermal shock. A similar idea, the multi-stage inlet-temperature staircase, coordinates three valves to drop coolant temperature in controlled increments and achieve smoother heat removal.
Flow management provides the last increment of uniformity. With module-level valve isolation each module owns a solenoid valve; under normal conditions all remain open, but if a hot spot appears the controller throttles neighbouring branches and floods the affected module. In long serial paths, the reversible flow loop flips pump direction whenever axial temperature rise crosses a threshold, bathing the previous outlet cells in the coldest liquid. Finally, fuzzy PID branch balancing drives stepper-actuated valves in a tree of pipes, learning the optimal opening so every cell receives just enough coolant.
Active temperature control delays abnormal heating and creates time for sensing and control systems to respond.
3. Sensor-Driven Early Detection and Diagnostic Technologies
Even with good cooling, internal faults still develop, so the third layer is rapid detection. In pouch and cylindrical formats, exothermic reactions cause the can or laminate to swell well before temperature probes notice. A cell-integrated deformation sensor embeds a strain gauge in at least one cell per module and streams data to the BMS. When expansion exceeds a threshold the controller warns the cabin and triggers mitigation. Blending thermal management and diagnostics, the multifunction heat-spread/heater/sensor layer dissipates heat, warms cells in winter and records surface temperature and thickness growth.
Chemical clues emerge even earlier. Every cell vents electrolyte gases milliseconds after its internal pressure spikes. A chemistry-agnostic vent-gas detector samples the first pressure impulse, temperature change and gas composition inside the enclosure. A single micro-sensor that tracks thermal conductivity serves a sub-second first-venting monitor; a sharp drop betrays light solvent vapors. For localisation, palladium nanogap elements act as a ppm-level hydrogen sentinel with dual thresholds so the BMS isolates only the offending cell.
Fusing multiple cues cuts false positives. A module that correlates temperature, pressure and gas concentration, the T–P–G correlation logic, declares danger only when temperature rise coincides with either a pressure collapse or a gas spike.
Pack-level guards add redundancy. Because runaway often ruptures coolant passages first, a coolant-parameter anomaly detector watches level, pressure and flow. Electrical cues include a temperature-differential current limiter that suppresses charge in cold climates and a switch-modulated impedance probe that injects AC and reads the imaginary component so hot cells are revealed without extra thermistors. Passive acoustics supplies a non-contact layer: an infrasound precursor detector listens for gas-bubble resonance inside the jelly-roll.
These sensors can warn minutes or hours before temperature reaches critical thresholds, giving the BMS time to pull energy out of danger.
4. Electrical Isolation, Charge Control and Energy Redistribution Strategies
Active energy removal is often the fastest intervention. The multi-mode energy-transfer architecture monitors every cell; if a risk flag appears, solid-state switches connect the endangered cell to a large electrical or thermal sink. Charge can be dumped into coolant-loop heaters, spread across side walls or pushed back into the pack. Because the rest of the battery has orders-of-magnitude greater thermal mass, extracted energy raises overall temperature only slightly.
Current can also be steered without leaving the pack. The virtual-cell current shunting scheme places bidirectional converters in parallel with physical cells; once a temperature excursion is spotted, converters source or sink current so the hottest cell contributes less I²R heat. Scaling up, the temperature-equalisation current allocator computes a reference for every parallel string and redistributes flow until all stacks share a common thermal set-point.
If a fault is too severe, rapid isolation is vital. The auxiliary isolation-and-dissipation module opens dedicated contactors, diverts trapped energy into an external resistor bank and activates its cooling loop, buying minutes before neighbours ignite. At cell level, the bi-material disconnect bracket flips from conductive to open circuit once local temperature crosses a preset limit and severs the cell from the string while leaving a low-current path for controlled discharge.
Charge control itself can be made preventive. Fast chargers with full bidirectional capability implement the pulsed charge-and-discharge protocol. They alternate high-rate charging bursts with brief discharges back to the grid or an auxiliary store, stripping plated lithium, relaxing local hot spots and resetting over-voltage.
With electrical threats curtailed, the pack must still contain any heat that does appear.
5. Inter-cell Thermal Propagation Barriers and Insulative Materials
Cells are often packed with millimetres of clearance, so a runaway cell can ignite its neighbour by radiation, conduction and flame. Early work introduced a high-melting-point ceramic spacer assembly that locks cylindrical or prismatic cells in place. Because the spacer stays intact above 500 °C it prevents polymer brackets from collapsing, preserves air gaps and keeps coolant passages open.
For larger modules, groups must be quarantined. The low-conductivity thermal barrier element partitions the enclosure into discrete cell sets. Made from ceramics, aramid composites or metal-ceramic sandwiches, these barriers span at least 90 % of the gap and can include coolant channels. By combining sub-W m⁻¹ K⁻¹ cores with melting points above 1000 °C they delay heat flow long enough for active subsystems or first responders to step in.
Recently the spotlight moved to ultra-thin inserts that slide between pouch or prismatic cells. The compressible tri-laminate sheet bonds aluminium or copper heat-spreading foils to a silicone-foam core; the foils homogenise temperature, yet through-thickness conductivity remains low. A complementary idea, the rigid-core / dual heat-resistant layer barrier, uses ceramic-filled skins to arrest flame while a structural middle layer resists blast pressure. Both laminates are roll-to-roll manufacturable and deliver everyday thermal uniformity plus emergency isolation.
These barriers immobilise cells and slow propagation, but the module lid and side walls must still absorb pressure and flame jets.
6. Battery Housing and Module Architectures Enhancing Thermal Containment
At module scale the cell tops are the hottest regions because vent jets originate there. The multilayer structural-insulated cover plate replaces plastics with a rigid-metal and high-temperature insulation sandwich that bridges cross-beams locking each cell. Even after adhesives liquefy, the stack cannot shift. When a cell vents, the insulation shields neighbouring terminals from 700 °C gases.
Where hot gas threatens the pack lid, a double-layer vent-shield lid adds an air-gap buffer. A sacrificial inner plate aligned with each vent absorbs the blast; stamped protrusions split and spread flow and the air gap behind it keeps the outer lid cool enough to preserve its coating.
A pack-level solution couples strength with pressure relief. The sacrificial upper surface with calibrated release mounts a frame above modules then holds the cover with weakened fasteners or scored sections. During crash loads the cover is rigid; if runaway occurs, pressure exceeds the holding force and the panel detaches cleanly, carving a wide exhaust aperture.
Some architectures segment the stack into self-contained bunkers. The dynamic three-sided enclosure with pivoting canopy seats each group in a U-shaped mini-bunker. Under normal pressure the canopy stays closed and isolates neighbours; during runaway, over-pressure lifts it and vents flames away from adjacent cells.
Safe routing of gas and debris then becomes the next concern.
7. Venting, Pressure Relief and Gas Flow Management Systems
Runaway releases high-temperature, high-pressure gas mixed with sparks and metal debris. Conventional vents handle only one hazard at a time, so integrated devices now tackle the chain. The integrated explosion-proof valve merges a melt-out membrane, staged particle filters, a flame-arresting disk and external heat sinks in one housing. As pressure ruptures the membrane, meshes strip solids, the arrestor quenches flames and fins absorb heat. A removable cover lets technicians replace the membrane and restore service.
Routing the plume outside the vehicle needs dilution. The high-flow thermal vent management system pairs a spring-loaded valve with a Venturi nozzle that entrains ambient air into a chamber, lowering gas temperature before directing it through a tailpipe under the bumper. For stronger extraction, a multi-ring cooled vent forces gas through concentric metal rings with liquid-coolant passages; offset apertures make flow turn and impinge on chilled surfaces, cutting exhaust temperature.
Some designs steer gas within the pack. A top plate with a serpentine vent passageway ruptures only above the failing cell and channels gas away from electronics. Side-wall gravity-assisted debris separation channels slow the plume so fragments settle before cooler gas exits upper ports. A thin-layer vent gas manifold and runner captures effluent at each cell, shields neighbours with mica and forces the plume through a cooling path.
Vents become adaptive actuators. An automatic re-closing vent opens early yet shuts once gases exceed roughly 350 °C, cutting off oxygen. Cell housings with dual local weakenings yield in stages to guide the plume away from adjacent cells. A dual-mode safety valve melts thermoplastic bonds for low-pressure venting during heat but ruptures classically during over-charge.
These paths remove energy and debris, yet if temperature stays too high active suppression must follow.
8. Emergency Coolant Discharge and Fire Suppression Mechanisms
Passive hardware remains the most fail-safe way to arrest a thermal event. The pressure-balanced double-valve circuit equips every cell with two resealable valves: the first dumps coolant into an overheated core, the second vents combustible gases. Fusible materials offer an alternative. Fusible-alloy coolant blocks melt around 120 °C and flood the cell, a rupturable coolant tube lattice is embroidered across the pack and an elastic-nozzle fire layer injects suppressant into cylindrical modules. Each design triggers without sensors and either reseals or permits simple replacement.
Other inventors merge daily cooling with an emergency dump mode. The shared motor–battery fluid loop with dump valve merges motor coolant with the battery circuit only when runaway is detected. Plate-cooled packs can morph into immersion systems when a wax-sealed port opens, as in the temperature-triggered plate-to-immersion switch. Dual-loop solutions keep firefighting liquid separate so it is full-strength when a higher emergency threshold is crossed, as in the dual-reservoir cooling / firefighting architecture and the selective pack-level immersion strategy.
High heat-flux removal with modest pump power is met by misting concepts. A fine-spray fusible channel diverts the normal coolant stream into atomising nozzles once its fusible plug melts. For pre-runaway hot spots, a targeted water-injection manifold opens coded valves only above threatened modules.
Finally, staged capabilities support first responders and self-recovery. The extendable external-agent launcher provides a pop-out port for injecting suppressants, while rupturable flame-retarding vents neutralise hot ejection gases inside the module. Sequential melt-valved spray jets open one after another to deliver multiple cooling pulses, buying time for occupants and rescuers.
With this final layer the battery becomes an active firefighting system that can rapidly, locally and repeatedly suppress thermal runaway.
Get Full Report
Access our comprehensive collection of 337 documents related to this technology
Identify Key Areas of Innovation in 2025
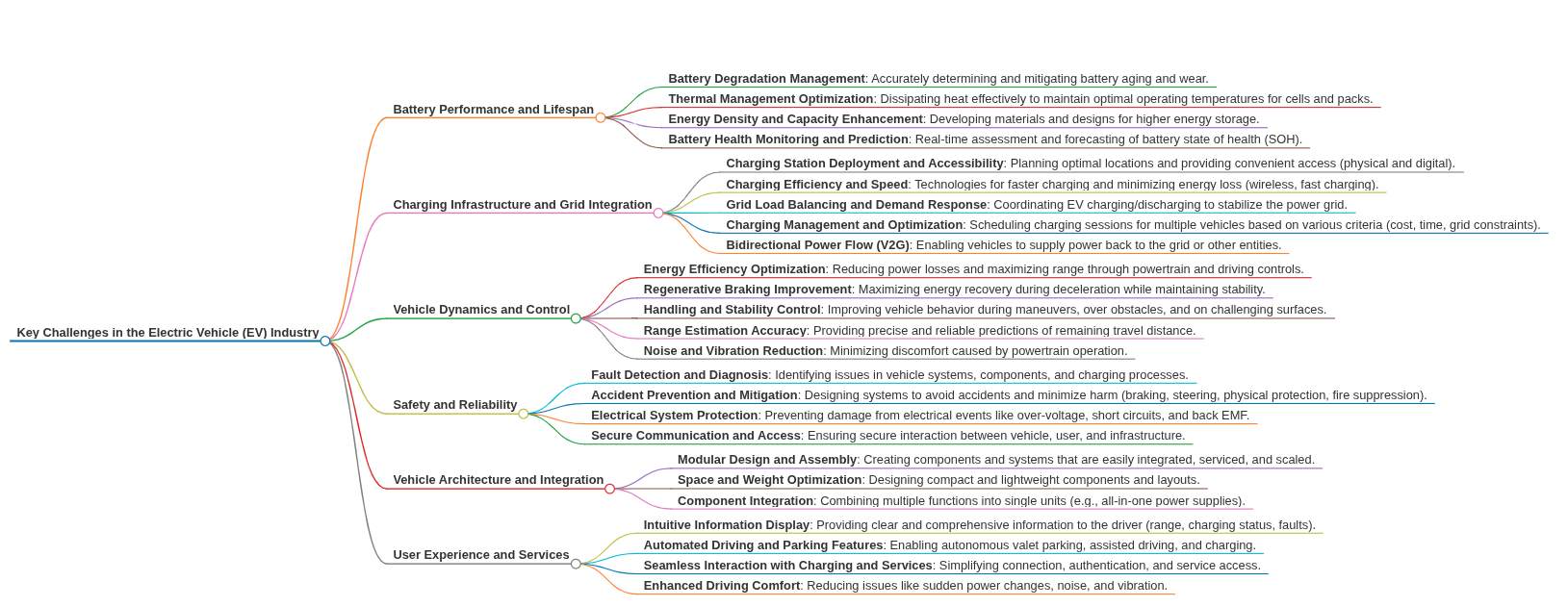