Solid-State Battery Mass Production
Manufacturing solid-state batteries at scale presents significant materials processing and assembly challenges. Current pilot lines achieve yields below 70% when producing cells larger than 5 Ah, with interface defects and non-uniform solid electrolyte layers being primary failure modes. These technical barriers have kept production costs above $400/kWh despite the promised benefits of solid-state technology.
The core challenge lies in maintaining precise interfacial contact between solid components while scaling up from laboratory to industrial production volumes.
This page brings together solutions from recent research—including novel electrode coating methods, quality control systems that analyze formation gases, specialized cell assembly tools, and designs that improve manufacturing yield. These and other approaches focus on practical solutions for achieving consistent, defect-free solid-state cells at commercial scale.
1. Battery Electrode Manufacturing with Vacuum-Assisted Thickness Control
Rivian IP Holdings, LLC, 2024
Controlling thickness variation in battery electrodes during manufacturing using vacuum pressure. The technique involves applying vacuum suction near the slot die coating opening to draw the electrode material onto the current collector as it's being coated. This helps maintain consistent thickness as the material is being applied. The vacuum device is controlled based on sensor feedback measuring the electrode thickness.
2. Continuous Fabrication Process for All-Solid-State Batteries with Zig-Zag Stacked Bendable Electrodes
GM GLOBAL TECHNOLOGY OPERATIONS LLC., 2024
Scalable continuous fabrication process for all-solid-state batteries using zig-zag stacking of bendable electrodes. The process involves stacking alternating continuous anode and cathode electrodes in a zig-zag pattern instead of punched sheets. This allows scalable production of ASSB cells with improved mechanical flexibility. The continuous electrodes have current collectors and active materials on both sides. A sulfide electrolyte layer is applied between adjacent electrodes. The zig-zag stacking provides high speed, accurate positioning, and reduced cost compared to punching individual sheets.
3. Low-Temperature Solution Synthesis of Argyrodite-Type Solid-State Electrolytes for Lithium Batteries
Rivian IP Holdings, LLC, 2024
Process for preparing argyrodite-type solid-state electrolytes for lithium batteries that involves contacting lithium and phosphorus sources with a solvent-reagent at lower temperatures, like 80-120°C, instead of high temperatures like 400-600°C. This allows forming Li7-xPS6-xYx compounds directly in solution, which can then be collected and further processed into solid-state electrolytes. The solvent contains a lithium salt like LiCl and a polymer like PVP. The lower temperature synthesis enables scalable production of argyrodite electrolytes using earth-abundant elements like phosphorus and chlorine.
4. Method for Fabricating Dense Ceramic Electrolytes via Flux-Assisted Low-Temperature Sintering
QuantumScape Battery, Inc., 2024
Process for making high-performance solid-state lithium-ion batteries with improved energy density, cycle life, and safety compared to liquid electrolyte batteries. The process involves mixing ceramic electrolyte powder with flux materials and heating at lower temperatures to form a dense, lithium-conducting electrolyte. This enables depositing thin-film electrolytes with high ionic conductivity suitable for all-solid-state batteries. The lower processing temperatures avoid issues like phase transformation and sintering. The fluxed powder is shaped and heated again at lower temperatures to densify the electrolyte. The lower temperatures and fluxing step allow forming dense electrolytes without sintering issues when directly depositing ceramic powders at high temperatures.
5. Compact Vertical Stacking Configuration for Solid State Battery Pack with Integrated Sensing Circuit and Wedge-Based Busbar Connection
Hyundai Motor Company, Kia Corporation, 2024
Battery pack design and assembly method for maximizing the volume ratio of solid state battery cells in a pack by using a compact vertical stacking configuration. The pack consists of aligned solid state battery cells, a sensing circuit with busbars to connect to the cells, a sensing block with wedges to tight-contact the busbars and cell leads, and a cover. The cells are stacked vertically, leads connect to busbars, and wedges hold them tight. This eliminates side-by-side cell arrangement, pack housing, and interconnects, allowing more cells in the same space.
6. Solid Electrolyte Composition with Specific Surface Binder Particles for Improved Particle-Collector Interface
FUJIFILM Corporation, 2024
Solid electrolyte composition for all-solid state secondary batteries that improves interfacial resistance between solid particles and collectors. The composition contains an inorganic solid electrolyte, binder particles with specific surface properties, and a dispersion medium. The binder particles have a polymer with an SP value of 10.5 cal/cm^3/2 or more and an average diameter of 10-50,000 nm. This composition provides favorable wettability, bonding, and resistance suppression for all-solid state batteries.
7. Electrode Assembly with Interleaved Folded Plates for Stacked Batteries
CONTEMPORARY AMPEREX TECHNOLOGY CO., LIMITED, JIANGSU CONTEMPORARY AMPEREX TECHNOLOGY LIMITED, 2023
An electrode assembly for stacked batteries that improves production efficiency and safety by folding and interleaving the electrode plates. The assembly involves folding a first electrode plate back and forth to create multiple laminates, then folding a second electrode plate once to create two laminates. These folded plates are inserted with separators to alternately stack and interleave the laminates. This allows efficient, one-by-one assembly of folded plates instead of sequential stacking of separate plates. It also prevents short circuits by having the folded second plate overlap the folded first plate.
8. All Solid-State Lithium Ion Battery with Controlled Particle Size and Shape of Inorganic Solid Electrolyte
FUJIFILM Corporation, 2023
All solid-state lithium ion batteries with improved ionic conductivity by optimizing the particle size and shape of the inorganic solid electrolyte material. The particles are made by milling the electrolyte with specific filling percentages and crushing media to achieve particles with restricted surface unevenness. This prevents grain boundary resistance and improves ionic conductivity compared to conventionally milled particles. The optimized particles can be used in the electrode layers of the battery to provide better ionic conduction.
9. Reinforced Solid Polymer Electrolyte with Fluoropolymer and Ionic Liquid for Lithium-Ion Batteries
HYZON MOTORS INC., 2023
Low cost, reinforced solid polymer electrolytes for lithium-ion batteries that have improved mechanical, electrochemical, and thermal stability compared to conventional polymer electrolytes. The electrolyte is made by dissolving a fluoropolymer in a solvent, mixing it with an ionic liquid, adding lithium salt, and impregnating a porous substrate. This solid electrolyte can be used in lithium-ion batteries to enable solid-state battery technology. The reinforced polymer electrolyte provides mechanical stability, prevents short circuits from dendrite growth, and has higher ionic conductivity compared to conventional polymer electrolytes.
10. Electrode with Sequential Layer Coating for Reduced Interfacial Resistance in All-Solid-State Batteries
LG Chem, Ltd., 2023
Electrode for all-solid-state batteries with reduced interfacial resistance between the electrode and the solid electrolyte layer. The electrode is manufactured by coating a preliminary electrode active material layer on the current collector, followed by a step of coating a solid electrolyte layer on the preliminary electrode active material layer. This results in an electrode with a lower porosity compared to conventional electrodes. The reduced porosity improves the interfacial resistance between the active material and the solid electrolyte, leading to better battery performance.
11. Monolithic Ceramic Electrochemical Cell with Integrated 3D Porous Electrode Structures and Solid Ceramic Separator
Sakuu Corporation, 2023
Monolithic ceramic electrochemical cell for solid-state lithium-ion batteries with integrated electrodes and separator. The cell has a ceramic housing with interconnected electrode spaces. The electrodes have 3D porous structures with conducting networks on sidewalls. The separator is solid ceramic. During charging, lithium forms in the anode space and ions move through the ceramic separator. This eliminates the need for liquid electrolyte and prevents dendrite growth. The 3D porous electrodes improve performance by enhancing lithium ion and electron access. The monolithic design allows hermetic sealing of the anode.
12. Bipolar Battery with Solid-State Ionically Conductive Polymer Electrolyte and Bipolar Electrode Configuration
Ionic Materials, Inc., 2023
Bipolar batteries with solid-state electrolytes that enable high-voltage operation without internal seals. The batteries have multiple bipolar electrodes sandwiched between electrolyte layers, with terminal electrodes on the ends. The electrolyte is a solid ionically conductive polymer that allows ions to diffuse through in the glassy state. This allows the battery to operate at high voltages without needing liquid electrolytes or seals. The polymer electrolyte can be synthesized by mixing a polymer, dopant, and ionic compound, then heating to form the solid ionically conductive material.
13. Battery Module with Integrated High and Low Voltage Connections and Elastic Enclosure
LG ENERGY SOLUTION, LTD., 2023
Battery module design with improved productivity, a battery pack using it, and a manufacturing method. The module has a simplified high voltage (HV) and low voltage (LV) connection scheme. The HV connection is done inside the module by bending and joining electrode leads through slits in sensing blocks covering the cell stack. This eliminates the need for external HV connectors. The LV connection is also simplified by integrating the LV sensing assembly with the lead assembly. An elastic cover encloses both sensing blocks and the cell stack. This allows exposing the lower cell surface for thermal contact. The manufacturing process involves stacking cells, covering with sensing blocks, joining leads, and adding the elastic cover. Simultaneous lead and sensing plate welding improves productivity.
14. Solid-State Battery with Interlayer Comprising Distinct Solid Electrolyte Material and Variable Coverage
GM GLOBAL TECHNOLOGY OPERATIONS LLC, 2023
Solid-state batteries with improved performance by using interlayers between the solid-state electrolyte and electrodes. The interlayer is made of a different solid electrolyte material than the main electrolyte. This improves interfacial compatibility and reduces parasitic currents compared to using only the main electrolyte. The interlayer thickness is 0.1-8 microns. The interlayer can cover 50-100% of the electrode surface. The interlayer can have through-holes.
15. Electrode Layer with Low Cohesion Energy Density Residual Liquid for All-Solid State Batteries
TOYOTA JIDOSHA KABUSHIKI KAISHA, Panasonic Holdings Corporation, 2023
Electrode layer for all-solid state batteries that improves capacity retention. The electrode layer contains an electrode active material, a sulfide solid electrolyte, and a residual liquid. The residual liquid has a low cohesion energy density (delta P < 2.9 MPa½) and a high boiling point (190°C or higher). This reduces cracking and deterioration of the sulfide electrolyte while maintaining ionic conductivity.
16. Compression System with Buffer-Mediated Pressure and Heat Application for Cylindrical Battery Cells
TeraWatt Technology Inc., 2023
A compression system for activating cylindrical battery cells, like jelly-roll style solid-state batteries, by applying pressure and heat to increase surface area contacts. The system uses a compression mechanism that squeezes a buffer material wrapped around the battery cell. This uniformly distributes pressure to the curved cell sidewall. Heating elements surround the buffer to apply heat while compressing. This compresses and activates the cell without liquids or clean-up issues.
17. Planar All-Solid-State Battery with Reduced Area-to-Perimeter Ratio for Uniform Lithium Deposition
Hyundai Motor Company, Kia Corporation, 2023
All-solid-state battery design with improved durability by preventing non-uniform lithium deposition and dendrite growth. The battery has a planar shape with a specific area-to-perimeter ratio of 0.7 or less. This prevents lithium from concentrating at the edges due to higher surface energy, which can cause short circuits and dead lithium. By reducing the perimeter relative to the area, lithium ions are less inclined to migrate to the edges and deposit uniformly.
18. Solid Electrolyte Material with Adjustable Composition and Argyrodite Structure for Lithium Batteries
Solvay SA, 2023
Solid electrolyte material for all-solid-state lithium batteries that provides high ionic conductivity and improved stability. The solid electrolyte has a specific composition of Li6-x-2yCuxP5-yX, where x, y, and X are adjustable parameters. The electrolyte can be produced by milling lithium sulfide, phosphorus sulfide, halogen compound, and copper compound together under inert atmosphere. The resulting solid material has a crystalline phase with the argyrodite structure.
19. All-Solid-State Battery with Glass-Crystalline Exterior for Moisture Suppression and Reflow Compatibility
MURATA MANUFACTURING CO., LTD., 2023
An all-solid-state battery with a protective exterior that suppresses moisture ingress. The battery has an exterior made of a combination of glass and crystalline materials. This allows the battery to be mounted on circuit boards using reflow techniques since the exterior transforms from a moldable state to a solid state during curing. The glass and crystalline materials in the exterior prevent moisture permeation into the battery. This enables all-solid-state batteries to be used in devices like wearables, IoT devices, sensors, and electric vehicles without the need for encapsulation or sealing.
20. Solid State Battery with Melt-Infiltrated High Volume Fraction Electrode Active Material
Sila Nanotechnologies, Inc., 2023
Solid state batteries with improved energy density, flexibility, and safety compared to conventional solid state batteries. The batteries use a melt-infiltration process to incorporate a high volume fraction of active material into the electrodes, rather than mixing powders. A liquid electrolyte composition is infiltrated into the electrodes or separator at elevated temperatures when molten. This allows higher active material loading and thinner electrolyte layers. It also enables using thermally stable polymer separators instead of porous ceramics. The process improves rate performance, energy density, and flexibility compared to conventional solid state batteries.
Get Full Report
Access our comprehensive collection of 95 documents related to this technology
Identify Key Areas of Innovation in 2025
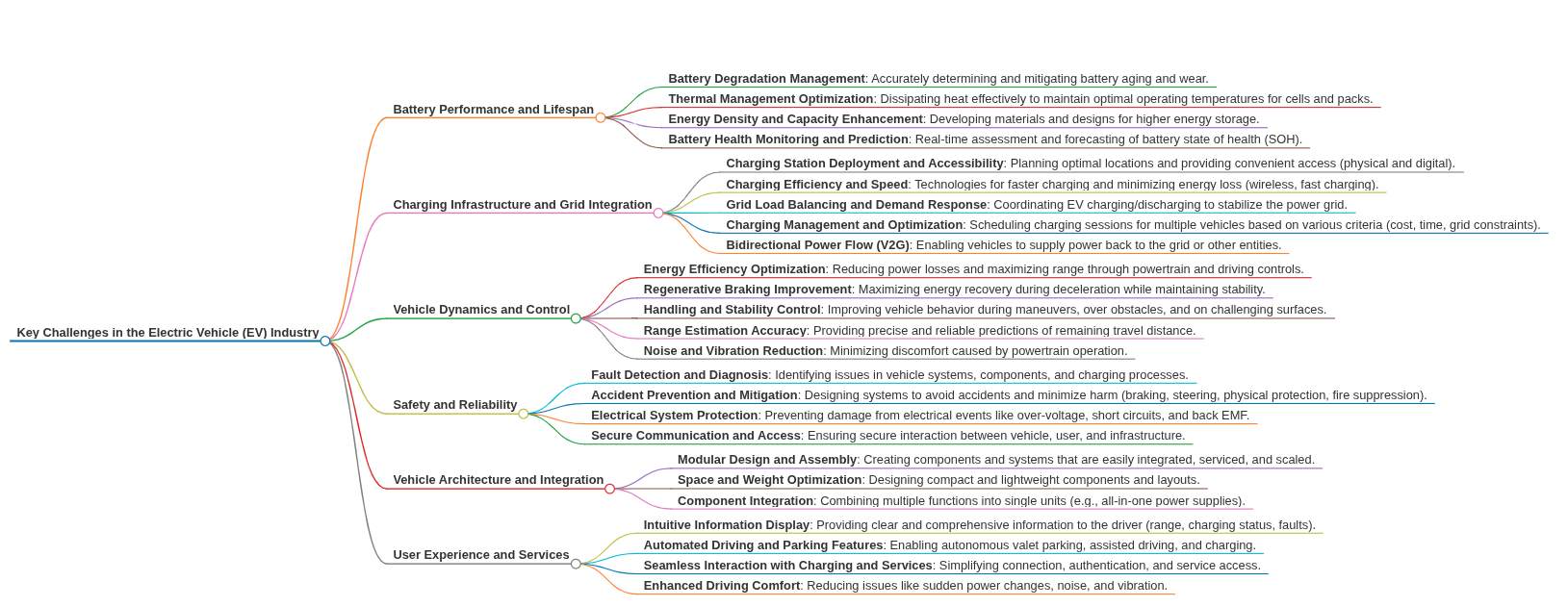